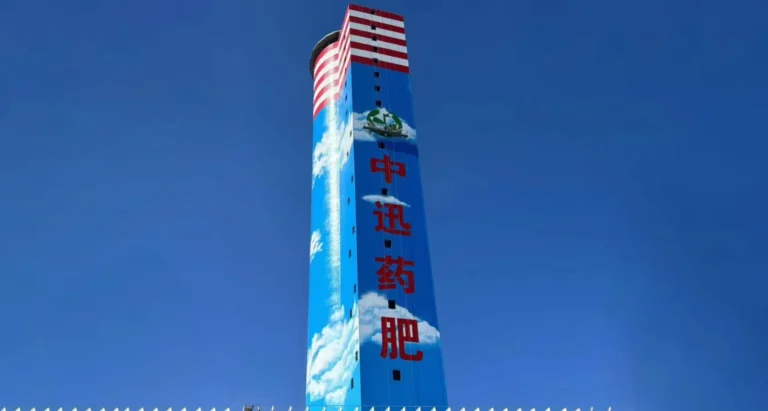
This 300,000-ton-per-year high-tower compound fertilizer production line was put into operation in 2017. It mainly produces high-nitrogen fertilizers such as 28-6-6, 30-0-5, 26-11-11 and other formulas. Sichuan is located in central China and is also a major rice-growing area. This production line adds medicated fertilizer to the formula based on high-nitrogen fertilizer to further enhance the nutritional value of the fertilizer.
What are the design considerations in this high tower fertilizer plant?
- Equipment layout and space planning: Tongli first ensures that the layout of the production line is reasonable, ensures that all links are closely connected, and reduces the distance and time of material transportation. For example, the distance from the raw material mixing equipment to the granulator and then to the drying equipment should be the shortest to improve efficiency. Tongli will reserve at least 20% of the space for equipment maintenance and expansion.
- Civil construction: The equipment in the production line, such as the drum granulator and dryer, is heavy and generates vibrations during operation. Therefore, the equipment needs to be installed on a solid foundation, usually with a concrete foundation with a thickness of ≥300mm, to ensure long-term operation stability.
- Pipeline and electrical system design: The material conveying pipeline and electrical control system are reasonably designed to ensure easy operation and stability of automatic control. The pipeline layout should ensure smooth air flow and reduce resistance; the response time of the electrical control system should generally be ≤200 milliseconds to ensure accurate temperature and pressure control.
- Dedusting: Exhaust gas and dust will be generated during the production of compound fertilizers, so Tongli has designed efficient dust removal and tail gas treatment equipment, and the emission concentration can reach ≤50mg/Nm³.
Equipment | Parameters | Capacity |
Raw Material Batching Belt | (800+1200)x 5 sets | 41.66t/h |
Urea Melting Tank | Heating source: Steam boiler, Fuel type: Natural gas/coal/oil | 50-200 tons/day |
Prilling Tower | Tower height: 128 meters, Operating temperature: 120-150°C, Granule size: 2-4mm | 1000-3000 tons/day |
Rotary Cooler | Power: 200-500 kW | 200,000-500,000 Nm³/h |
Screening Unit | Multi-deck vibrating screens, Screening efficiency: ≥90%, Granule size distribution: 2-4mm | Screening capacity: 1000-3000 tons/day |
Dust Removal System | Dust collector type: Baghouse or cyclone, , Dust concentration: ≤50mg/Nm³ | Airflow capacity: 200,000-300,000 Nm³/h |
Automatic Packaging Line | Packaging capacity: 25-50 kg/bag, Weighing accuracy: ±0.1%, Sealing method: Heat sealing | 500-1000 bags/hour |
Control System | PLC/DCS system, Full automation, Safety interlocks, SCADA for process monitoring | Controls entire production process |