
What is High Tower Ammonia Nitrate Fertilizer Plant?
The high-tower urea compound fertilizer production line is a modern NPK fertilizer production system with high technological content. It uses urea, ammonium nitrate, potash fertilizer and other materials as the main raw materials. It uses the characteristics of rapid crystallization of urea after melting to accurately measure the heated ammonium phosphate, urine and potassium slurry, and sprays them into the tower through the nozzle at the top of the tower. During the falling process, the material is fully in contact with the cold air, naturally cooled and solidified, and granulation is completed. The production line covers a series of closely connected processes from raw material pretreatment, precise batching, mixed pulping, high-tower granulation, to subsequent particle cooling, screening, coating and finished product packaging. It is equipped with core equipment such as mixing tank, high-efficiency emulsification pulping machine, high-tower melt granulator, etc. Some advanced production lines also use tubular reactor technology, molten urine granulation technology, DCS control technology, and coating wrapping technology to realize the automation and precision control of the production process, ensuring that the product particles are uniform and smooth, have melting holes, low moisture content, no agglomeration, high water solubility and balanced nutrients, which can meet the nutritional needs of different crops at various growth stages.
Understanding High Tower Granulation Technology
What is High Tower Granulation?
High tower granulation is a key process in the production of high tower compound fertilizer. It is a process of converting fertilizer raw materials in a molten state into granular compound fertilizer. The granulation part can be divided into the following three steps:
Step1: Heating and melting:
The measured raw materials are put into a special heating equipment and heated to a certain temperature to make the raw materials reach a molten state. In this process, the temperature and stirring speed need to be strictly controlled to ensure that the raw materials are fully mixed and evenly mixed to form a slurry with good fluidity. Generally speaking, the melting temperature of urea is around 130-140℃, and ammonium phosphate and potash fertilizers also need to be heated to the corresponding suitable temperature to ensure that they can fully blend with urea.
Step2: Spraying of slurry:
High tower granulation: The molten slurry is transported to the nozzle at the top of the tower through a pipeline. The nozzle usually has a special structure that can evenly disperse and spray the molten slurry transported from the pipeline into fine droplets. The parameters such as the aperture, shape and spraying angle of the nozzle have been carefully designed and optimized by Tongli to ensure uniform droplet size and reasonable distribution. Tongli nozzle adopts a rotary design. Through high-speed rotation, the molten slurry is thrown into fine droplets under the action of centrifugal force and can be evenly distributed in the horizontal direction.
Step3: Falling and cooling and solidification:
The sprayed droplets fall from the top of the tower under the action of gravity, and are fully in contact with the cold air introduced from the bottom of the tower during the falling process. There is a strong heat exchange between the cold air and the droplets. Due to the low temperature of the cold air, the droplets quickly cool and solidify. The height of the tower is generally designed to be high, usually around 80-120 meters, in order to provide enough falling time for the droplets to fully cool and solidify. During the falling process, the surface of the droplets first solidifies to form a hard shell, and as the cooling proceeds, the inside gradually solidifies, and finally forms granular compound fertilizer.
Evolution of Fertilizer Production Techniques
- The high-tower compound fertilizer technology is a compound fertilizer production process with special functions such as energy saving, high efficiency and environmental protection that was successfully developed by American fertilizer experts in the 1970s after many years of research and development. It represents the highest technical level of compound fertilizer production in the world. This technology uses the principle of rapid crystallization after urea melting. After heating ammonium phosphate and accurately measuring it with urine and potassium slurry, it is sprayed into the high tower through a nozzle. During the falling process, it is fully exposed to cold air and cooled and solidified to form compound fertilizer particles. Due to its advantages such as uniform and smooth particles, melting holes, no agglomeration, and high water solubility,
- Before 2004, only a few developed countries in the world such as the United States could produce high-tower compound fertilizers. Afterwards, with the continuous development and dissemination of technology, some other countries such as China, Germany, Norway, Denmark, etc. have gradually mastered the high-tower compound fertilizer production technology and applied it in actual production.
- At the beginning of the 21st century, although China's fertilizer production technology has improved, the products have problems such as unstable quality, easy moisture absorption and agglomeration, and separation of nitrogen, phosphorus and potassium fertilizer elements. Imported fertilizers occupy a large share of the Chinese market. In this context, Tongli Heavy Machinery joined hands with CNCEC to independently develop high-tower granulation compound fertilizer technology. In 2002, Tongli Heavy Machinery used two experimental middle towers to produce air-cooled compound fertilizers with transitional significance.
- In December 2003, Tongli Heavy Machinery successfully built the first domestic production unit for high-tower granulation to produce granular compound fertilizers with an annual output of 200,000 tons, and launched the first domestic "high-tower nitrate-sulfur-based" compound fertilizer products, organically combining high-tower granulation and compound fertilizer production process technologies, and realizing the production of multi-component compound fertilizers by high towers (over 80 meters).
- In 2005, Tongli Heavy Machinery and Stanley Compound Fertilizer successfully built the world's first annual production line of 200,000 tons of urea-based high-tower compound fertilizers, and produced qualified products. Since then, Tongli has continued to extend and improve the high-tower granulation technology, and built a double-tower compound fertilizer production line with an annual output of 800,000 tons in 2006. It also integrated the two technologies of high-tower granulation and slow-release efficiency enhancement, and added biological enzyme inhibitors to enable fertilizers to release nutrients in a timely manner according to the needs of crops at different growth stages. As Stanley and Kingenta made breakthroughs in the field of high-tower compound fertilizer technology, many domestic manufacturers followed suit, and high-tower compound fertilizer technology was rapidly promoted in China.
Advantages of the high tower granulation compare to steam drum and roller extrusion granulation:
Aspect | High Tower Granulation Line | Roller Press (Extrusion) Granulation Line | Rotary Drum Granulation Line |
Production Process | Directly uses molten urea or ammonium nitrate, eliminating the need for urea melting spray granulation, packaging, transport, and crushing of solid urea. The process is simplified. | Requires mixing and crushing of raw materials, then extrusion molding. The process is relatively complex. | After mixing raw materials, water and binders are added. Granules form while tumbling in the drum, followed by drying, etc. The process is relatively long. |
Energy Consumption | Uses heat from molten urea or ammonium nitrate; low moisture content; no drying needed; low energy consumption. | Requires significant mechanical energy for extrusion, and materials may need preheating; relatively high energy usage. | Requires water addition during granulation; high energy use in the drying stage. |
Product Quality | Uniform granules with smooth, round surfaces; high compressive strength; anti-caking; uniform nutrient distribution; long-lasting effect; enhanced trace element effectiveness through chelation; micro-pores for anti-counterfeiting. | Regular granule shape but rougher surface than high tower granules; moderate strength; nutrient distribution may be uneven or layered. | Uneven granule size; rough surface; lower strength; prone to caking; poor nutrient uniformity. |
Production Efficiency | High percentage of qualified granules; minimal recycling of unqualified material; high production efficiency. | Lower output; equipment wears easily; high maintenance cost affects efficiency. | Relatively high output, but recycling and reprocessing steps reduce overall efficiency. |
Environmental Impact | Clean production; no waste emissions; good working conditions. | Dust generation requires dust collectors; high operational noise. | Dust and exhaust gas produced during drying and granulation. |
Investment Cost | High initial cost for granulation tower, but low long-term operational costs; more advantageous with larger scale. | Lower equipment investment, but high maintenance costs in the long run. | High initial equipment investment and long construction time, higher long-term operational costs. |
Formula Flexibility | Allows production of various fertilizer formulas based on market demand; N, P, K can fully mix in molten state. | Less flexible in formula adjustment; requires strict control over material particle size and moisture. | Moderate flexibility in formulation, but less than high tower; not suitable for high-concentration fertilizers. |
What are the Key components of High Tower urea Fertilizer prilling production line?
1. Granulation Tower Structure and Design
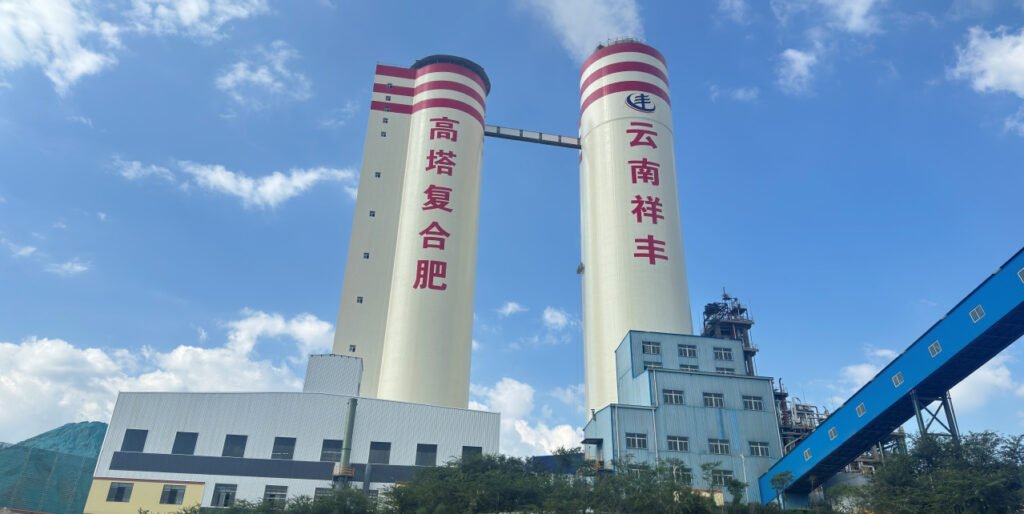
1.1 Foundation structure
Take the 300,000-ton annual high-tower compound fertilizer production line of Anyang Zhongsheng, which was built by Tongli Heavy Machinery, as an example. The foundation adopts a plate-type raft foundation, covering an area of about 414.84㎡. The plate-type raft foundation is a common foundation form. It is like a huge flat plate, which evenly transfers the weight of the high tower to the foundation. This foundation has a large bearing capacity and can adapt to various loads generated by the high tower during the production process, including the weight of the tower body, the weight of the equipment, and wind loads. Its large bottom area can effectively reduce the pressure of the foundation and reduce the settlement of the foundation.
1.2 Tower structure
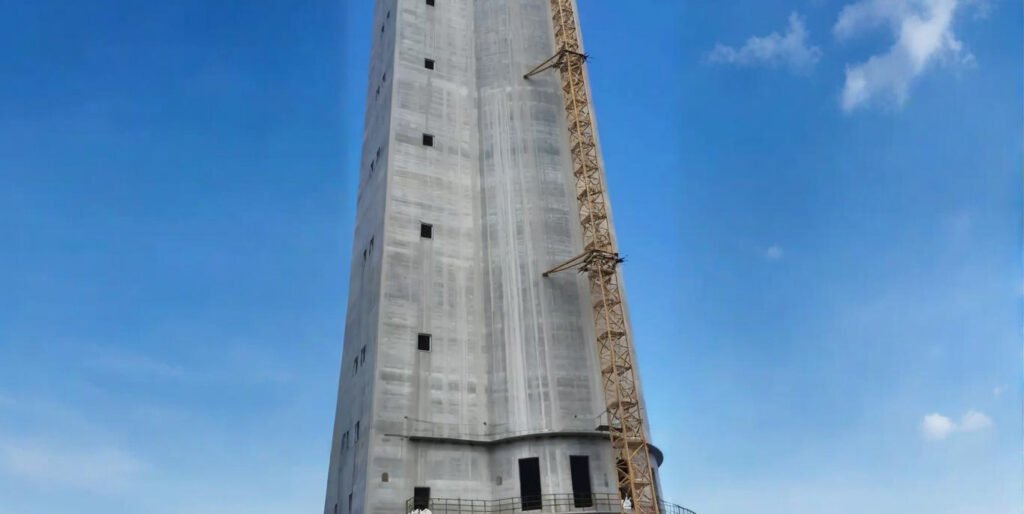
Tower Height:
The height of the tower usually ranges from 100 to more than 130 meters. Sufficient height is to ensure that the compound fertilizer has enough time to crystallize, cool and exchange heat in the tower. For example, the material falls from the top of the tower and fully contacts the cold wind rising from the bottom of the tower after a long distance, which can make the slurry particles gradually cool and solidify during the descent to form high-quality compound fertilizer particles. If the height is not enough, the particles may not be fully cooled, resulting in unstable product quality, such as insufficient strength of the particles, excessive water content and other problems.
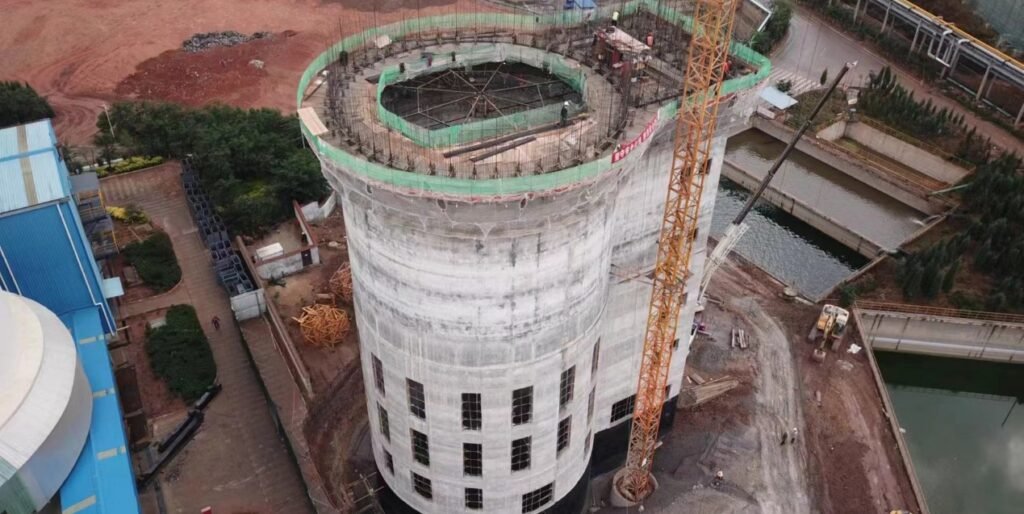
Tower Diameter:
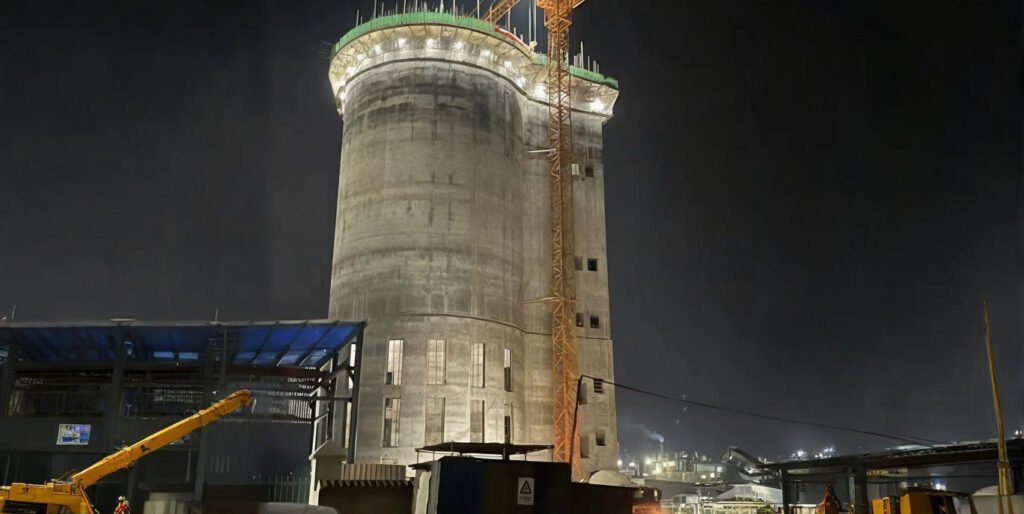
Influence of diameter: The diameter of the tower is also closely related to production capacity and product quality. A larger diameter can increase the space in the tower and make the material more evenly distributed in the tower, which is conducive to improving production efficiency and product consistency. For example, the inner diameter of the tower of Guangdong Zhongxun, which was built by Tongli, is 20 meters, and the designed diameter of the tower of Anyang Zhongsheng is 21 meters. Such a diameter can meet the needs of large-scale production and make the granulation process more stable and efficient.
1.3 Graunlation Tower steel structure and concrete material
1.3.1 High tower structural design:

Advantages of reinforced concrete cylinder plus shear wall structure: High towers mostly use reinforced concrete cylinder plus shear wall structure. Reinforced concrete has good compressive strength and durability, and can bear the huge weight of the tower. The cylinder structure can provide good integrity and torsion resistance, so that the tower remains stable when subjected to wind loads or other horizontal forces. The shear wall further enhances the structure's ability to resist lateral forces and improves the tower's seismic performance.
1.3.2 Structural Adventages:
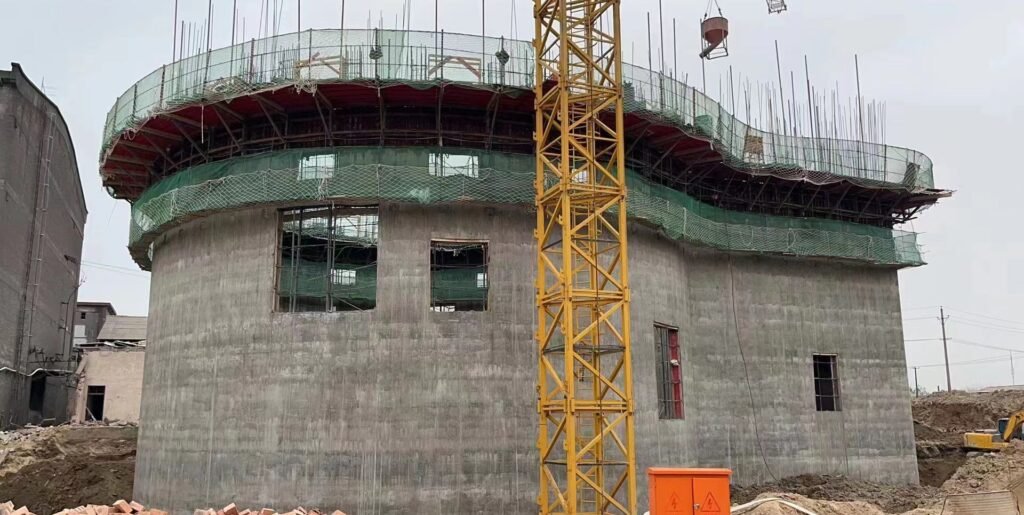
Take Yuntianhua Petrochemical as an example: its tower adopts this structure, which can meet the requirements of building structure safety level 2, seismic category C, and fire resistance level 1. This means that the tower can ensure the safety of the structure during normal use, avoid serious damage when encountering an earthquake of a certain intensity, and has good fire resistance. It can maintain the stability of the structure in emergency situations such as fires, providing enough time for personnel evacuation and fire rescue.
1.4 Granulation high tower Internal space layout from top to bottom

1.4.1 Top of the granulation tower level(+128m):
- Dust collector: installed on the top of the tower, mainly used to collect dust generated during the granulation process to prevent it from escaping into the atmosphere and causing environmental pollution. Its working principle is to capture dust particles through filtering, adsorption, etc. The most commonly used is the bag dust collector.
- Electric control room: This is the control center of the high tower compound fertilizer production line, which is equipped with various electrical control cabinets, automatic control systems and monitoring equipment. Through these devices, the staff can centrally control and monitor the entire high tower production process, and adjust the operating parameters of the equipment in real time, such as the speed of the granulator, the temperature of the heating device, etc., to ensure stable and efficient operation of the production process.
1.4.2 Top of the granulation tower level(+120m):

- Mixing reactor: The main function is to fully stir and mix various raw materials such as urea, ammonium phosphate, potash fertilizer, etc. in the equipment to achieve the purpose of preparing a mixed slurry with good flow properties. Some will also add additives or perform chelation reactions in the reactor to avoid the loss of certain nutrients or adverse side reactions during the production process and improve fertilizer efficiency.
- Heating device: Use steam heating or electric heating to heat the urea raw material, heat and melt the solid urea or ammonium nitrate into a molten liquid, so that the subsequent melting and mixing process can proceed smoothly. For example.
- High tower granulator: Installed on the top of the high tower, the tower granulator rotating nozzle uses the centrifugal force generated by rotation to evenly spray the 140-degree (urea) or 170-degree (ammonium nitrate) molten material from above into the entire tower, forming spray lines, so that the material quickly cools and solidifies in the air and falls to the bottom of the tower, eventually forming granular fertilizers of the required specifications and strength.
1.4.3 Cooling zone of the tower level(20~100m):
Air circulation system: It consists of fans and other equipment. Cold air is sent in from the bottom of the tower to exchange heat with the hot fertilizer particles falling from the top of the tower to cool the particles. The cold air rises in the tower and fully contacts the falling particles to achieve efficient cooling.
1.4.4 Bottom granule collection level(+10m)
Disc collecting device: It is located at the bottom of the tower and consists of a rotatable disc and a matching scraper. The cooled and solidified fertilizer particles fall onto the disc, which rotates slowly. The scraper scrapes the particles off and transports them to the subsequent screening and conveying links. The device can efficiently collect the granulated fertilizer particles to ensure the continuity of the production process, and the collection speed can be flexibly controlled by adjusting parameters such as the disc speed.
1.4.4 Bottom conveyor system level(+2m)
The belt conveyor at the bottom of the high-tower compound fertilizer tower drives the roller through the motor, so that the conveyor belt circulates around the roller. When the disc collecting device conveys the cooled fertilizer particles to the feeding end of the belt conveyor, the materials fall onto the conveyor belt under the action of gravity and the guide trough. The conveyor belt relies on the friction between the roller and its own tension to drive the materials forward and transport the fertilizer particles to the subsequent screening, packaging and other processes. During the conveying process, the roller supports the materials and the conveyor belt, ensuring the smooth operation of the conveyor belt and reducing the bumps and spills of the materials during the conveying process.
2. Raw Materail Handling: 3 types of commonly used crusher in high tower plant
2.1 Urea bulk roller crusher:
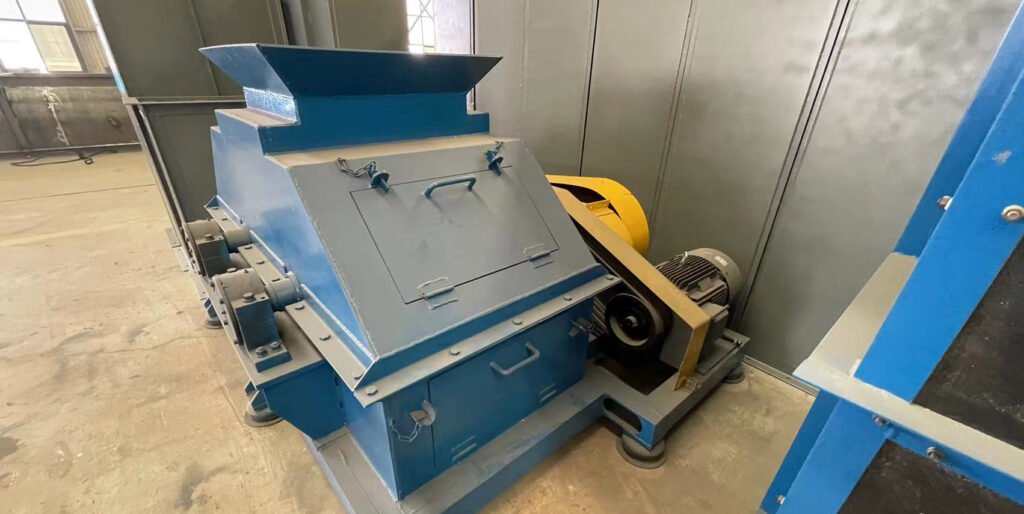
Urea crushing machine: In the production process of high-tower compound fertilizer, roller urea crusher is often used. It crushes the urea raw material through the extrusion effect generated by the high-speed rotation of the rollers. The grille equipped at the feed port can effectively block the entry of large pieces of material, and the lower block-breaking tooth roller can handle slightly larger pieces of material. It has the characteristics of fast crushing speed, precise and uniform particle size adjustment according to the production needs of high-tower compound fertilizer, non-stick roller, no wearing parts, no dust, and no material heating, which effectively guarantees the continuous and stable operation of the urea crushing link in the production of high-tower compound fertilizer and optimizes the working environment.
2.2 DAP/MAP Cage crusher:
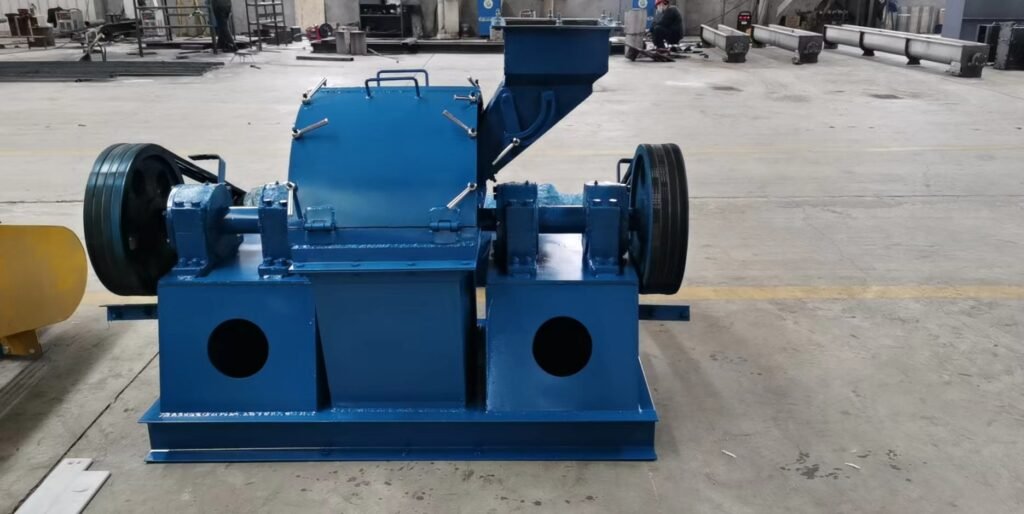
As an important crushing equipment on the high tower compound fertilizer production line, the cage crusher is designed based on the impact crushing principle and consists of a frame, a casing, a large rat wheel group, a small rat wheel group and two motors. When working, the two motors drive the large and small rat wheels to rotate in reverse, so that the materials entering the inner rat wheel frame are repeatedly impacted and crushed by steel bars. The crusher has a simple structure, high crushing efficiency, good sealing performance, stable operation, and easy cleaning and maintenance. It is particularly suitable for the crushing process of granular materials such as phosphate ammonium and urea in the production of high tower compound fertilizer.
2.3 KCL+Urea+MAP+DAP Chain Crusher

Chain crusher: In the production of high tower compound fertilizer, the chain crusher has two structures: vertical single rotor and horizontal double rotor. It mainly relies on the rotor with a steel chain to crush the material blocks through the high-speed rotating chain. It consists of a feed port, a body, a discharge port, a rotor, a transmission device and a shock absorber. The body is lined with rubber plates and has inspection doors on both sides. The chain crusher has a scientific and reasonable design of inlet and outlet, and the crushed materials are evenly distributed, not easy to stick to the wall, and easy to clean. It is widely used in the production of high-tower compound fertilizers and the crushing of block materials in the chemical, building materials, mining and other industries.
2.4 What are the difference between cage crusher/chain crusher/bulk crusher in high tower fertilizer production line?
Feature | Chain Crusher | Cage Crusher | Bulk Crusher |
Application in High-Tower Plant | Commonly used before granulation or after drying | Often used after granulation for fine crushing | Less common; used for coarse crushing (e.g., raw material prep) |
Installation Position | Inline (between drying and screening) | Inline (between granulation and screening) | Generally used at ground level or in raw material system |
Vertical Flow Adaptability | ✅ Compact, good for tower flow | ✅ Compact and closed system | ❌ Often bulky or horizontal layout |
Particle Size Control | Good (1–5 mm adjustable) | Excellent (<1 mm, uniform) | Varies—may need screening after |
Crushing Method | Impact via chains | Impact via high-speed cage bars | Varies: impact, pressure, shear |
Handling of Moisture | Tolerates moderate moisture (not sticky) | Needs dry or low-moisture material | Depends on type; roller crushers better with moist |
Dust Control | Moderate (enclosed but needs suction) | High (fully enclosed structure) | Varies; often needs extra enclosure |
Space Occupation | Small, vertical-friendly | Small-medium footprint | Large (unless customized for vertical use) |
Maintenance in Tower Setup | Easy to access & replace chains | Cages may be harder to replace in-place | Depends heavily on type and layout |
Energy Efficiency | Medium; efficient for size | Medium to high; precision crushing | Varies |
Feeding Size Range | Usually <60 mm | <60 mm | Roller: <50 mm, Jaw: up to 150 mm |
Output Uniformity | Moderate | Very High | Low to medium (unless screened) |
Best Use Case in Tower | After dryer or before screener | After granulator to crush oversized granules | Initial crushing of bulk raw materials |
3. DEL Automatic-Batching System Using Germany Schenck Technology Developed to high tower fertilizer raw material proportion
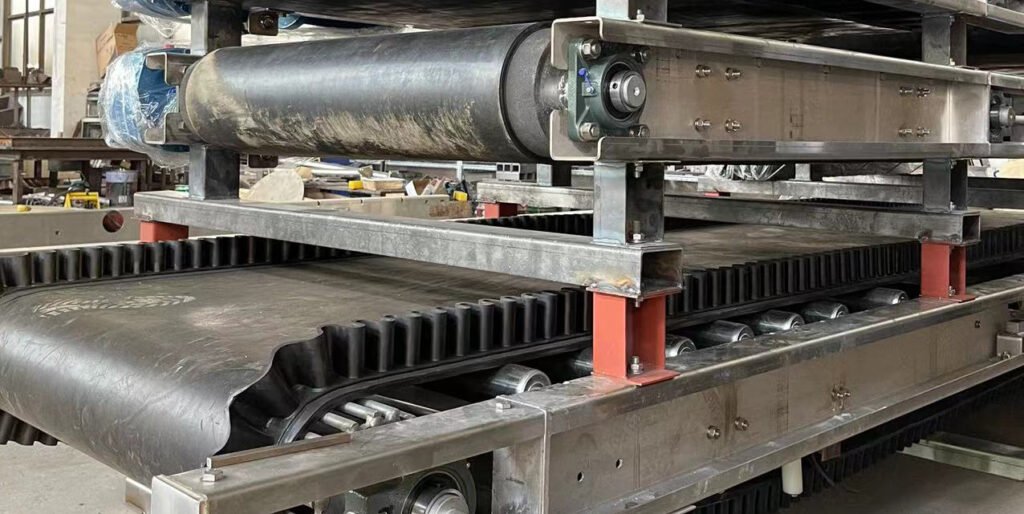
The high tower compound fertilizer DEL Germany Schenck technology metering and batching system is a combination of equipment and control system used to accurately measure and mix various raw materials in the production process of high tower compound fertilizer. Its main function is to ensure that different raw materials are accurately delivered to the production process according to a specific formula ratio to ensure the stability and consistency of product quality. The metering scale in the high tower compound fertilizer metering and batching system is one of the core equipment, usually an electronic metering scale. Its working principle is to use a weighing sensor to convert the gravity acting on the scale body into an electrical signal, which is amplified, processed and displayed by an electronic circuit to accurately measure the weight of the material.
3.1 Schenck DEL batching system Features:
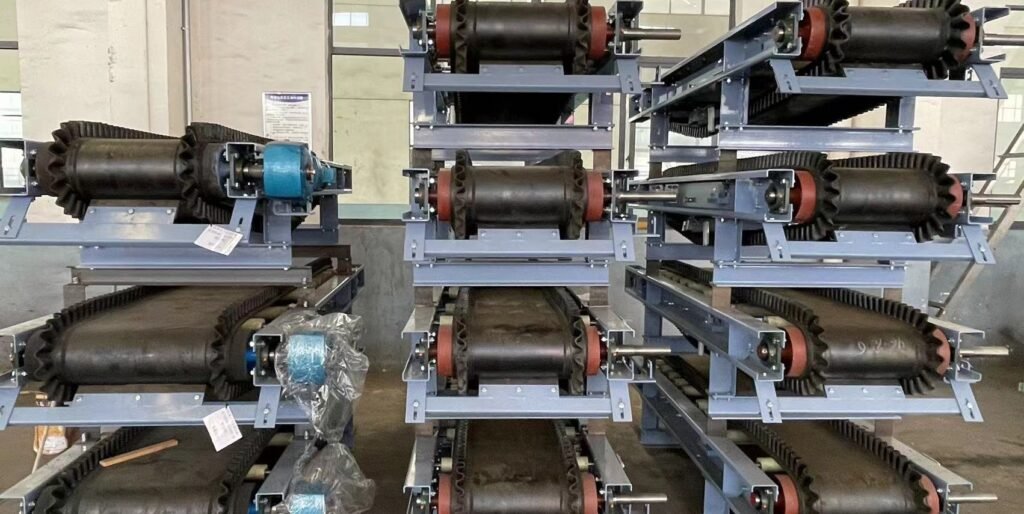
The schenck metering scale has the following characteristics and functions:
- High-precision metering: It can accurately measure the weight of various raw materials, and the error is controlled within a very small range to meet the strict requirements of high-tower compound fertilizer production on batching accuracy. Generally speaking, the metering accuracy can reach about ±0.1% to ±0.5%.
- Multiple material metering: It can measure a variety of different raw materials at the same time, such as urea, ammonium phosphate, potash fertilizer, additives, etc. Each material has an independent metering channel and scale body to ensure the accuracy of the batching of each raw material.
- Automatic batching control: Combined with the automatic control system, it automatically controls the feeding and stopping of materials according to the preset formula parameters to realize the automation of the batching process. When the metering scale detects that the material weight reaches the set value, it will automatically stop the corresponding feeding device to ensure the accuracy and stability of the batching.
- Data recording and management: It has data recording and storage functions, and can record the material name, weight, time and other information of each batching, which is convenient for traceability and quality control of the production process. At the same time, the data can also be transmitted to the host computer or production management system for further analysis and management.
- Fast response and stable performance: With a fast response speed, it can accurately measure the change of material weight in a short time and provide timely feedback to the control system. In addition, the weighing scale also has good stability, can maintain accurate weighing performance during long-term operation, and is not affected by external environmental factors (such as vibration, temperature, humidity, etc.).
3.2 Detailed specification of TONGLI DEL Schenck batching scale:
Category | Specification / Description |
Belt Width | B500 ~ B1000 |
Feeding Capacity | 0.1 ~ 500 t/h |
Feeding Accuracy | ±0.5% |
Weighing Sensors | Three-sensor / Four-sensor system |
Adjustment Range | 1:05 |
Speed Control | Upper belt: Pre-feeding + Variable Frequency Drive (VFD) |
Lower belt: VFD (optional) | |
Operating Mode | Continuous operation |
Drive Mode | Upper belt: Cycloidal chain drive |
Lower belt: High-efficiency shaft-mounted gearbox | |
Custom Option 1 | Rubber-coated driving roller |
Custom Option 2 | Hollow tail roller |
Custom Option 3 | Plastic idlers |
Custom Option 4 | Anti-corrosion paint |
Custom Option 5 | Optional dust cover and sealing enclosure |
Custom Option 6 | Guided feed bin design |
Custom Option 7 | Internal & external belt cleaners, automatic belt tracking device |
3.3 Model Selection of TONGLI DEL Schenck batching scale:
Model | I.width | O.width | U.length | B.length | total.length | 1Gearbox | 2Gearbox |
DEL-500/0812S | 500 | 860 | 800 | 1200 | 2320 | BWY-11-71-0.75KW | SBD50-φ40-0.75KW |
DEL-500/0815S | 500 | 860 | 800 | 1500 | 2620 | BWY-11-71-0.75KW | SBD50-φ40-0.75KW |
DEL-500/1015S | 500 | 860 | 1000 | 1500 | 2820 | BWY-11-71-0.75KW | SBD50-φ40-0.75KW |
DEL-500/1020S | 500 | 860 | 1000 | 2000 | 3320 | BWY-11-71-0.75KW | SBD50-φ40-0.75KW |
DEL-500/1215S | 500 | 860 | 1200 | 1500 | 3020 | BWY-11-71-0.75KW | SBD50-φ40-0.75KW |
DEL-500/1220S | 500 | 860 | 1200 | 2000 | 3520 | BWY-11-71-0.75KW | SBD50-φ40-0.75KW |
DEL-650/0812S | 650 | 1010 | 800 | 1200 | 2320 | BWY-11-71-0.75KW | SBD50-φ40-0.75KW |
DEL-650/0815S | 650 | 1010 | 800 | 1500 | 2620 | BWY-11-71-0.75KW | SBD50-φ40-0.75KW |
DEL-650/1015S | 650 | 1010 | 1000 | 1500 | 2820 | BWY-11-71-0.75KW | SBD50-φ40-0.75KW |
DEL-650/1020S | 650 | 1010 | 1000 | 2000 | 3320 | BWY-11-71-0.75KW | SBD50-φ40-0.75KW |
DEL-650/1215S | 650 | 1010 | 1200 | 1500 | 3020 | BWY-11-71-0.75KW | SBD50-φ40-0.75KW |
DEL-650/1220S | 650 | 1010 | 1200 | 2000 | 3520 | BWY-11-71-0.75KW | SBD50-φ40-0.75KW |
DEL-800/0812S | 800 | 1160 | 800 | 1200 | 2320 | BWY-11-71-1.1KW | SBD50-φ40-1.1KW |
DEL-800/0815S | 800 | 1160 | 800 | 1500 | 2620 | BWY-11-71-1.1KW | SBD50-φ40-1.1KW |
DEL-800/1015S | 800 | 1160 | 1000 | 1500 | 2820 | BWY-11-71-1.1KW | SBD50-φ40-1.1KW |
DEL-800/1020S | 800 | 1160 | 1000 | 2000 | 3320 | BWY-11-71-1.1KW | SBD50-φ40-1.1KW |
DEL-800/1215S | 800 | 1160 | 1200 | 1500 | 3020 | BWY-11-71-1.1KW | SBD50-φ40-1.1KW |
DEL-800/1220S | 800 | 1160 | 1200 | 2000 | 3520 | BWY-11-71-1.1KW | SBD50-φ40-1.1KW |
DEL-1000/0812S | 1000 | 1360 | 800 | 1200 | 2320 | BWY-11-71-1.1KW | SBD50-φ40-1.1KW |
DEL-1000/0815S | 1000 | 1360 | 800 | 1500 | 2620 | BWY-11-71-1.1KW | SBD50-φ40-1.1KW |
DEL-1000/1015S | 1000 | 1360 | 1000 | 1500 | 2820 | BWY-11-71-1.1KW | SBD50-φ40-1.1KW |
DEL-1000/1020S | 1000 | 1360 | 1000 | 2000 | 3320 | BWY-11-71-1.1KW | SBD50-φ40-1.1KW |
DEL-1000/1215S | 1000 | 1360 | 1200 | 1500 | 3020 | BWY-11-71-1.1KW | SBD50-φ40-1.1KW |
DEL-1000/1220S | 1000 | 1360 | 1200 | 2000 | 3520 | BWY-11-71-1.1KW | SBD50-φ40-1.1KW |
4. 128 meters of raw material lifting: Heavy-duty stainless steel bucket elevator

4.1 What is high tower fertilizer raw material bucket elevator?
The bucket elevator for transporting and lifting compound fertilizer in high tower is a key conveying equipment specially serving the production line of compound fertilizer in high tower. It uses a series of buckets evenly fixed on the endless traction components (commonly chain, plate chain or belt) to lift materials vertically. The driving device transmits power to the head spindle through the motor, reducer, etc., drives the traction components and buckets to run at a constant speed in a specific direction, scoops up compound fertilizer production materials such as powdered phosphorus and potassium raw materials, granular nitrogen fertilizers, etc. from the lower position of the production line, and continuously lifts them to the top of the high tower, and then dumps the materials into the batching tank or reactor at the top of the high tower through the chute. Tongli's high tower bucket elevator is specially designed in terms of high temperature resistance and corrosion resistance in response to the production environment of high tower compound fertilizer, and can work in coordination with the automatic control system of the production line. It has the characteristics of relatively simple structure, small lateral size, small footprint, large lifting height, good conveying capacity, and strong sealing to reduce environmental pollution.
4.1.1 Working principle:
The high-tower bucket elevator is a continuous conveying machine that uses a series of buckets evenly fixed on the endless traction member to lift materials vertically. The drive device outputs power to the head spindle through the motor, reducer, coupling, and large and small sprockets. The head wheel rotates to drive the chain or belt to run at a constant speed in a certain direction. The bucket moves with the chain or belt, scoops up the material from the low place, lifts it to the top of the tower and pours it into the receiving tank.
4.1.2 Structural composition:
The whole machine consists of five parts: head, drive device, middle box, tail, and lifting components. The head contains head wheel, spindle and other components; the drive device provides power; the middle box is the channel for material lifting; the tail has tail wheel and other components, which play the role of tensioning the chain or belt; the lifting components include buckets and traction components.
4.1.3 Features and advantages:
Compared with other lifting equipment, the high-tower bucket elevator has a more complex and reliable structure, small lateral size, small footprint, and can effectively save space. It is suitable for use in places with limited space such as high-tower compound fertilizer production workshops. The lifting height can reach 128 meters, which can meet the height requirements of material lifting in high-tower compound fertilizer production. It works in a fully enclosed body and has little pollution to the workshop environment. In addition, the bucket elevator consumes less power and has a lower operating cost.
4.2 What are the special design of high tower fertilizer lifting bucket elevator?
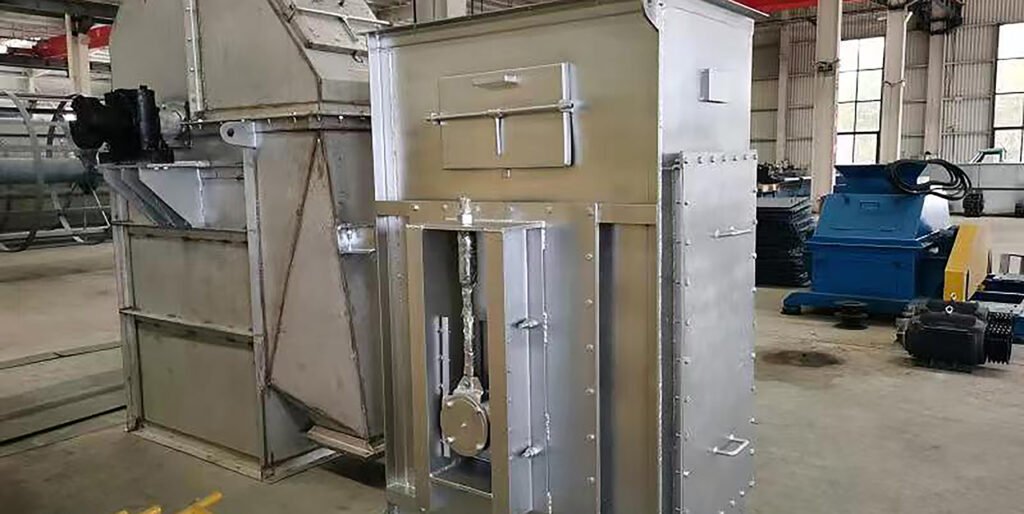
4.2.1. Material Features:
- Corrosion resistance: Since compound fertilizer raw materials such as urea, DAP, and MAP contain corrosive components such as acid and alkali, Tongli elevator hoppers, chains, sprockets, and housings are made of corrosion-resistant stainless steel, such as 304 stainless steel or 316 stainless steel or acid- and alkali-resistant rubber. Stanley Fertilizer High Tower Compound Fertilizer Production Line, built by Tongli, uses 316 stainless steel for some key parts of its elevators. In the case of long-term contact with corrosive raw materials, the key parts of the equipment can still operate normally after 5 years of use, effectively reducing the frequency of equipment replacement. For some less corrosive environments, the service life of the equipment is also extended by spraying anti-corrosion coatings on the surface of carbon steel. This method can extend the service life of the equipment by 2-3 years in a mildly corrosive environment.
- High temperature resistance: In the production process of high-tower compound fertilizers, the raw materials may have a higher temperature. For example, the material temperature in some process links can reach 120℃-150℃. Therefore, the traction parts and hoppers of the elevator need to have high temperature resistance. For example, a high-temperature resistant rubber belt is used as a traction belt, or a special alloy steel chain that can withstand high temperatures is used. The hopper can be made of high-temperature resistant or metal materials, and a heat-insulating coating or heat-insulating treatment is added. The hopper uses a metal hopper with a heat-insulating coating. Under the condition of a material temperature of 130°C, after continuous operation for 8,000 hours, the hopper has no obvious deformation or damage.
- Wear resistance: Compound fertilizer raw materials are mostly granular or powdery, which will cause wear to the hopper and conveying parts during the lifting process. Therefore, parts such as hoppers and chains usually use materials with good wear resistance. Tongli hoppers can be made of high-strength and wear-resistant cast steel or manganese steel, and the chain uses a surface-hardened alloy steel chain to improve its wear resistance and reduce maintenance and replacement frequency. Related tests show that the wear rate of hoppers made of wear-resistant cast steel is reduced by 60% - 70% compared with ordinary carbon steel hoppers under the same working conditions, greatly reducing maintenance costs and downtime.
4.2.2 Structural features:
- Large-capacity hopper design: In order to improve the lifting efficiency and meet the continuous production needs of the high-tower compound fertilizer production line, Tongli bucket elevators usually use large-capacity hoppers. The shape and size of the hopper are optimized and designed, generally with a deep bucket or shallow bucket structure. The appropriate bucket type is selected according to the characteristics of the raw materials. For powdery raw materials with good fluidity, a deep bucket can be used to increase the loading capacity of the hopper; for raw materials with greater viscosity, a shallow bucket is used to facilitate the unloading of materials. Tongli's TH-type bucket elevator has a hopper capacity ranging from 3.75 liters to 60 liters. For example, when the TH500 model bucket elevator uses a deep bucket structure, the single lifting volume can be increased by 30% to 40% compared to the same specification shallow bucket lifting volume, which effectively improves the overall conveying efficiency.
- Reinforced frame structure: Considering that the elevator needs to operate stably for a long time in a high-tower environment and has to withstand a large material weight and lifting force, the Tongli elevator frame structure usually adopts a reinforced design. It is welded with high-strength steel, with additional support points and reinforcement ribs to improve the stability and rigidity of the overall structure and prevent shaking or deformation during operation. In the compound fertilizer production project with a tower height of more than 80 meters, the hoist frame can stably carry the material lifting through optimized design and strengthened structure. Even in harsh environments such as strong winds, the vibration amplitude of the equipment can be controlled within a very small range, ensuring the safe operation of the equipment.
- Special unloading device: In order to ensure that the material can be accurately and smoothly unloaded into the mixing tank at the top of the tower, the unloading device of the hoist is specially designed. There are two ways of unloading: centrifugal unloading and gravity unloading, which are selected according to the characteristics and unloading requirements of the material. For granular materials with good fluidity, centrifugal unloading is used to achieve rapid unloading by using the centrifugal force of the material in the hopper; for materials with high viscosity or poor fluidity, gravity unloading is used. Through the inclination angle of the hopper and the design of the unloading port, the material is unloaded slowly and evenly under the action of gravity. Practical data shows that for materials with good fluidity, centrifugal unloading can increase the unloading speed by 50% - 80% compared with gravity unloading, and the unloading is more thorough.
4.2.3 Design features:
- Optimization of lifting speed: Tongli rationally designs the lifting speed of the elevator according to the output and material characteristics of the high-tower compound fertilizer production line. It is necessary to ensure that the material supply demand on the production line can be met, and to avoid excessive speed causing the material to spill during the lifting process or causing excessive impact and wear on the equipment. The lifting speed will be adjusted within a certain range according to different raw materials and production scales, between 1-3m/s. Taking Stanley's medium-sized compound fertilizer production line as an example, when lifting powdery materials, the lifting speed is controlled at 1.2m/s, which can not only ensure a conveying capacity of 20-30 tons per hour, but also effectively reduce the spilling of materials; when lifting granular materials, the speed is increased to 2m/s, and the conveying capacity can reach 40-50 tons per hour.
- Feed and discharge port design: The design of the feed port should facilitate the smooth entry of materials into the hopper, while avoiding accumulation or blockage of materials at the feed port. The discharge port must be precisely connected to the batching trough or reactor at the top of the tower to ensure that the material can be accurately discharged into the designated position. The size, shape and position of the feed port and the discharge port need to be optimized according to the specific layout of the production line and the flow characteristics of the material. Tongli has improved the smoothness of material feeding by 40% - 50% by optimizing the shape of the feed port, changing the square shape to a trumpet shape, and effectively reducing the feed blockage.
- Safety protection design: Tongli bucket elevator is equipped with a variety of safety protection devices. Limit switches are set at the head and tail of the elevator to prevent the traction components from exceeding the limit position; an overload protection device is installed. When the material weight exceeds the set value, the equipment will automatically stop running to avoid damage to the equipment due to overload; guardrails and safety doors are also set to prevent operators from contacting moving parts and causing accidents. Bucket elevators equipped with complete safety protection devices have a safety accident rate that is 80% - 90% lower than those without them.
4.2.4 Assembly features:
- High-precision assembly requirements: Since the elevator operates in a 128-meter-high tower environment, the assembly accuracy requirements are particularly high. The installation of each component needs to be carried out strictly in accordance with the design requirements to ensure the coaxiality and verticality of rotating components such as the head wheel, tail wheel, sprocket, and the installation position of the hopper is accurate. The coaxiality error of the head wheel and tail wheel should be controlled within 0.1mm to ensure the smooth operation of the traction component and avoid problems such as deviation and tooth skipping. In the actual assembly process, by using high-precision measuring instruments and professional assembly processes, Tongli can control the assembly error of key components within the standard range and effectively improve the operation stability of the equipment.
- On-site assembly and commissioning: When assembling the elevator at the high-tower compound fertilizer production site, professional technicians and equipment are required for hoisting, installation and commissioning. During the assembly process, each component must be carefully inspected and calibrated to ensure a firm connection and good sealing. After the equipment is installed, no-load and load debugging are carried out to check the operating conditions of the equipment, such as the lifting speed, the unloading conditions of the hopper, the temperature and vibration of each component, etc., to promptly discover and solve problems in the assembly process. For example, during the on-site assembly and debugging of the Tongli Guangxi project, through the test of 5 hours of no-load operation and 8 hours of loaded operation, the problems of poor hopper unloading and excessive vibration of some components were discovered and solved in a timely manner, ensuring the stable operation of the equipment after it was officially put into use.
4.2.5 Auxiliary drive feature
- Auxiliary drive drive system: In order to prevent the main drive system from failing and causing the production line to stop, the high tower compound fertilizer raw material bucket elevator will be equipped with a backup drive system. The backup drive system can be a manual drive device, or an electric or hydraulic drive device. When the main drive system fails, it can be put into use in time to safely transport the materials in the elevator to the designated location to avoid the accumulation of materials in the elevator causing blockage or other problems. The backup drive system of the elevator of a large compound fertilizer enterprise can start and operate normally within 5-10 minutes after the main drive fails, effectively ensuring the continuity of production.
- Lubrication and cooling system: The auxiliary drive system also includes a lubrication and cooling system. The transmission parts of the elevator will generate friction and heat during operation, and the lubrication system needs to be used to regularly lubricate the rotating parts to reduce the friction coefficient. The cooling system is used to cool some parts that are prone to heat, such as motors, reducers, etc., to prevent them from being damaged due to overheating. The automatic lubrication system can automatically lubricate the equipment according to the running time or number of times. Compared with manual periodic lubrication, the lubrication effect is improved by 30% - 40%, effectively extending the service life of the equipment.
4.3 High tower bucket elevator technical data table and model selection table:
Model | Hopper Capacity (L) | Capacity (m3/h) | Hopper Distance (mm) | Movement Speed (m/s) | Drive Sprocket Revolution (r/min) | Max Bulk Material Size (mm) |
TH315 | 3.75 / 6 | 35 / 59 | 512 | 1.4 | 42.5 / 37.6 | 35 |
TH400 | 5.9 / 9.5 | 58 / 94 | 688 | 1.5 | 35.8 / 31.8 | 40 |
TH500 | 9.3 / 15 | 75 / 118 | 920 | 1.6 | 30.5 | 50 |
TH630 | 14.6 / 23.6 | 114 / 185 | 920 | 1.6 | 24.4 | 60 |
TH800 | 24 / 38 | 150 / 240 | 1001 | 1.6 | 28 | 75 |
TH1000 | 38 / 60 | 240 / 360 | 1100 | 1.6 | 26 | 85 |
TH1250 | 60 / 95 | 360 / 540 | 1250 | 1.6 | 24 | 100 |
5. Raw material emulsification: Urea DAP MAP KCL

The high tower compound fertilizer emulsification tank is a closed container with a stirring device. It is composed of a tank body, agitator, motor, reducer, thermometer, level gauge, feed port, discharge port, etc. It is a key equipment for preparing emulsified slurry in the production process of high tower compound fertilizer. Tongli high tower fertilizer emulsification shear tank is made of stainless steel, which has good corrosion resistance and heat preservation performance to ensure that the slurry is emulsified at a suitable temperature and environment. The agitator is the core component of the emulsification tank. It uses specially designed stirring blades to produce strong shearing and mixing effects to fully emulsify and mix various materials.
5.1 Emulsification tank working principle:
The working principle of the high tower compound fertilizer emulsification tank is to fully mix and emulsify the various raw materials put into the tank, such as nitrogen fertilizer, phosphate fertilizer, potash fertilizer, additives and water, under certain temperature and pressure conditions through the high-speed rotation of the agitator. During the stirring process, the shear force and impact force generated by the stirring blades break the large particles into fine particles, and make the materials of different components evenly dispersed in the liquid phase to form a stable emulsified slurry. At the same time, by controlling the parameters such as the temperature and stirring time in the tank, it is ensured that sufficient chemical reactions and physical changes occur between the materials to achieve the expected emulsification effect, laying the foundation for subsequent granulation in the high tower.
5.2 What is the function of emulsification in high tower urea ammonia nitrate-based fertilizer production?

- Material mixing: Mix a variety of different fertilizer raw materials evenly to ensure the uniform distribution of various nutrients in the compound fertilizer, thereby improving the quality and use effect of the fertilizer. It can make the main nutrients such as nitrogen, phosphorus, potassium and trace elements fully mixed according to specific formula requirements.
- Promote reaction: During the emulsification process, a series of chemical reactions occur between the materials, such as acid-base neutralization and double decomposition reaction. The emulsification tank provides a suitable reaction environment to accelerate these reactions, convert the raw materials into a compound form that is easier for crops to absorb, and improve the fertilizer efficiency.
- Preheating materials: During the emulsification process, the materials can be preheated. Because in the production of high-tower compound fertilizers, the materials need to reach a certain temperature before entering the high-tower granulation to ensure the granulation effect and product quality. The heating device in the emulsification tank can heat the materials to a suitable temperature, reduce the burden of subsequent heating processes, and improve production efficiency. Moreover, uniform preheating helps to avoid problems such as agglomeration or precipitation of materials in the pipeline due to uneven temperature.
5.3 Why emusification is necessary in high tower urea fertilizer granulation process?
5.3.1 Forming a stable slurry:
The mixed materials form an emulsified slurry with good fluidity and stability. This slurry can be smoothly transported to the top of the tower through the pipeline during the high tower granulation process, and evenly sprayed out from the granulation nozzle to form compound fertilizer particles of uniform size and regular shape. If the stability of the slurry is not good, it may cause problems such as nozzle blockage and uneven particle size, affecting production efficiency and product quality.
5.3.2 Remove impurities and gases:
The stirring and mixing action of the emulsification tank can make impurities in the material easier to precipitate or float, which is convenient for removal by filtration or other means. At the same time, it also helps to release the gas dissolved in the material to avoid the formation of bubbles in the slurry, affecting the stability of the slurry and the quality of granulation. If there is too much gas in the slurry, it may cause defects such as hollowness and rupture of the particles during the granulation process, reducing the qualified rate of the product.
5.3.3 Adjust the slurry performance:
By emulsifying the material in the emulsification tank, the performance parameters such as viscosity and surface tension of the slurry can be adjusted. Appropriate viscosity and surface tension help the slurry to form good droplets at the granulation nozzle, which in turn affects the formation and quality of compound fertilizer particles. For example, by adjusting the emulsification conditions, the viscosity of the slurry can be reduced, making it easier to transport and spray granulate. At the same time, the droplets can shrink and shape better in the air to obtain round and smooth particles.
6. The role of three-stage mixing of urea/ Kcl/Ammonia Nitrate

The three-stage mixing tank on the top of the high-tower compound fertilizer tower is a key mixing equipment located on the top of the tower in the production process of high-tower compound fertilizer. It is mainly used to fully mix various fertilizer raw materials. The materials enter the primary mixing tank from the feed port in a certain order and proportion, and are initially mixed under the action of the stirring device. The materials after initial mixing then enter the secondary mixing tank for further mixing and refinement. Finally, the materials enter the tertiary mixing tank for final fine mixing to ensure that the various fertilizer raw materials reach a highly uniform mixing state. After meeting the production process requirements, they are discharged from the discharge port and enter the subsequent granulation process.
6.1 What is the size of the three-stage mixing tank?
Made of corrosion-resistant materials such as 304 stainless steel. The shape of the tank is mostly cylindrical to accommodate enough materials and provide sufficient mixing space. The tank size will be different for mixing tanks with different production scales and process requirements. For a large-scale high-tower compound fertilizer production line with an annual output of 300,000 tons, the volume of the first-stage mixing tank may be around 10-20 cubic meters, the volume of the second-stage mixing tank is slightly smaller, at 8-15 cubic meters, and the volume of the third-stage mixing tank is around 5-10 cubic meters. There is usually an observation window on the tank body to facilitate the operator to observe the mixing of the internal materials; there is also a liquid level gauge to monitor the liquid level of the material in real time to control the feeding and discharging.
6.2 what is the structure of a three-stage mixing tank?
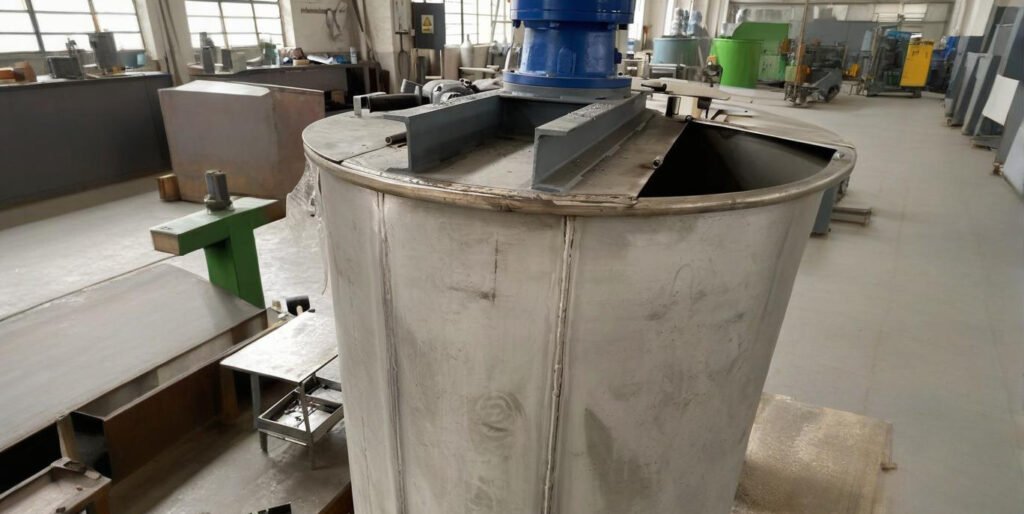
6.2.1 Stirring device:
It consists of a motor, a reducer, a stirring shaft and a stirring blade. The motor drives the stirring shaft to rotate through the reducer. The stirring blade is installed on the stirring shaft and rotates with the rotation of the stirring shaft. The shape and size of the stirring blade are designed according to the size of the mixing tank and the characteristics of the material. There are pusher type, turbine type, anchor type, etc. The pusher blade is suitable for mixing large-capacity, low-viscosity materials, which can produce strong axial flow and improve the overall mixing effect of the material; the turbine blade can produce strong shear force and radial flow, which is more suitable for occasions where the material needs to be fully dispersed and refined; the anchor blade is suitable for high-viscosity materials and can prevent the material from accumulating near the tank wall. The speed of the stirring device can also be adjusted according to needs. Generally, the stirring speed of the first-stage mixing tank is 30-60 rpm, the second-stage mixing tank is 40-80 rpm, and the third-stage mixing tank is 50-100 rpm to meet the mixing needs of different stages.
6.2.2 Feed port and discharge port:
The feed port is located on the upper part or side of the tank body, and is used to add the raw materials of the high tower fertilizer to the mixing tank in a certain order and proportion. Each feed port is equipped with a valve and a metering device to accurately control the feed amount of the raw materials. The discharge port is located at the bottom or side of the tank body, and is used to transport the mixed materials to the next process. A valve is usually also provided at the discharge port to stop the discharge or control the discharge speed when necessary. In order to prevent the material from being blocked at the discharge port, the diameter of the discharge port is generally large, and an auxiliary stirring device or a vibration device may be provided near the discharge port.
6.2.3 Heating or cooling device:
According to the requirements of the high tower production process, the mixing tank needs to heat or cool the material. The heating device generally adopts a steam jacket, an electric heating element or a heat transfer oil circulation, etc., and heats the tank body to make the material reach a suitable temperature to promote the chemical reaction and mixing uniformity between the raw materials. The cooling device usually adopts a cooling water pipe or a cooling coil, and passes cooling water to reduce the temperature of the material to prevent the material from deteriorating or other adverse reactions due to excessive temperature during the mixing process. For example, when producing certain temperature-sensitive compound fertilizers, the material temperature in the mixing tank needs to be controlled between 50 and 80°C. At this time, precise heating and cooling devices are required to maintain temperature stability.
6.2.4 Pipeline and valve system:
Pipes connecting various mixing tanks and other production equipment form a complete material conveying system. Various valves, such as stop valves, ball valves, regulating valves, etc., are installed on the pipeline to control the flow direction, flow rate and pressure of materials. By reasonably setting the opening and closing state of the valve, the orderly flow of materials between different mixing tanks and precise control in the entire production process can be achieved. For example, when feeding the primary mixing tank, by opening the corresponding feed valve and closing other unnecessary valves, ensure that the raw materials enter the primary mixing tank accurately; after the mixing is completed, open the connecting valve between the primary mixing tank and the secondary mixing tank to transport the materials to the secondary mixing tank for further mixing.
6.3 what is the function of a three-stage mixing tank?
- Precise batching and mixing: The production of high-tower compound fertilizers requires precise mixing of raw materials such as nitrogen, phosphorus, potassium, and trace elements in strict accordance with the formula. The three-stage mixing tank can achieve precise batching and uniform mixing of various raw materials through multi-stage mixing, ensuring that the content of each nutrient in the compound fertilizer is accurate and evenly distributed, thereby improving the stability and consistency of product quality.
- Promote chemical reactions: During the mixing process, the stirring action allows the materials to fully contact, which helps to promote chemical reactions between the raw materials, such as acid-base neutralization and double decomposition reactions. This is conducive to converting the raw materials into a compound form that is easier for crops to absorb and improve the fertilizer efficiency.
- Adjust material properties: Through the stirring and mixing of the three-stage mixing tank, the performance parameters of the material such as humidity, temperature and viscosity can be adjusted. Appropriate material properties are crucial for the subsequent granulation process, which can ensure that the slurry forms good droplets at the granulation nozzle, and then produce compound fertilizer products with uniform particles and regular shapes.
6.4 what is the technical parameter of the three stage mixing tank:
Parameter | Primary Mixing Tank | Secondary Mixing Tank |
Volume (m³) | 10~20 | 8~15 |
Tank Material | Stainless steel | Stainless steel |
Agitator Type | Propeller or turbine type | Turbine or anchor type |
Mixing Speed (rpm) | 30 - 60 | 40 - 80 |
Motor Power (kW) | Depends on volume and mixing requirements, typically 15 - 30 | Depends on volume and mixing requirements, typically 20 - 40 |
Number of Inlets | 3 - 5, depending on types of raw materials | 2 - 4, depending on discharge from the primary tank and additional materials |
Outlet Diameter (mm) | 200 - 300 | 200 - 300 |
Level Meter Type | Radar or ultrasonic level meter | Radar or ultrasonic level meter |
Heating / Cooling Method | Steam jacket or thermal oil circulation heating; cooling with water pipes | Steam jacket or thermal oil circulation heating; cooling with water pipes |
Operating Temperature (℃) | Based on process requirements, generally 50 - 100 | Based on process requirements, generally 50 - 100 |
Operating Pressure (MPa) | Atmospheric or slight positive pressure, generally 0 - 0.1 | Atmospheric or slight positive pressure, generally 0 - 0.1 |
7. Role of High pressure Spray Nozzles in high tower Granulation
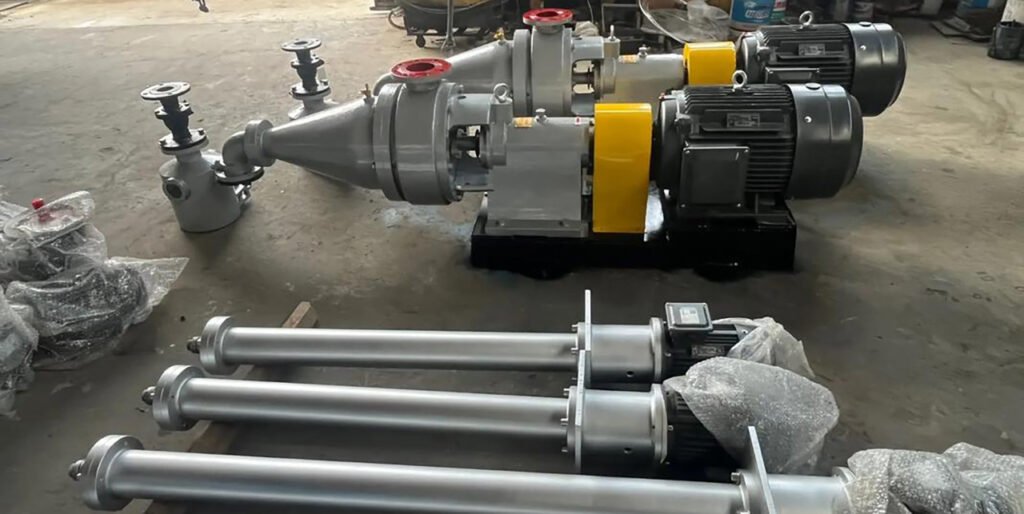
The high pressure tower granulator nozzle is the core component in the high tower compound fertilizer production process. It plays a key role in converting the fully mixed and reacted fertilizer slurry into small droplets of specific specifications in the entire production process. In the production of high tower compound fertilizer, solid urea or ammonium nitrate is first heated and melted to form a molten liquid, and then the corresponding phosphate fertilizer, potash fertilizer, filler and active substance are added to make a mixed slurry. The granulator nozzle is installed on the top of the tower, and these high-temperature, corrosive slurries are transported to the nozzle through pipes.
7.1 What is the working principle of the high tower granulator?

The working principle of the high tower granulator nozzle is based on the gravity and centrifugal force of the slurry. The slurry is transported into the nozzle body under pressure and evenly distributed to each nozzle hole through the distributor. When the slurry is sprayed out from the nozzle hole, due to the high-speed rotation of the nozzle or other driving methods, the slurry obtains a certain centrifugal force, and is thrown into small droplets. These small droplets fall freely in the gravity field of the high tower, and at the same time exchange heat with the cold air in the tower, quickly cool and solidify to form granular compound fertilizer. During the falling process, the size and shape of the particles mainly depend on factors such as the size of the nozzle hole, the flow rate of the slurry, and the rotation speed of the nozzle. By precisely controlling these parameters, high tower compound fertilizer particles of different specifications and quality requirements can be produced.
7.2 What is the structure of the high tower granulation spray nozzle?

7.2.1 Granulator Spray hole:
The spray hole is one of the most critical parts of the nozzle. Its size, shape and number have a decisive influence on the characteristics of the finished compound fertilizer particles. The diameter of the spray hole usually ranges from 1 to 5 mm. Common shapes include round and elliptical. Different designs are suitable for different production needs. Circular spray holes are more commonly used in most conventional production, which can make the slurry spray out evenly to form more regular spherical particles; elliptical spray holes can adjust the shape of the particles according to specific process requirements. The number of spray holes in the nozzle is large, ranging from dozens to thousands depending on the specifications of the nozzle. Numerous spray holes can make a large amount of slurry be sprayed into small droplets at the same time, thus meeting the needs of large-scale production. In order to flexibly adjust the size, shape and distribution of the particles, the nozzle is also equipped with an adjustment device. The operator can use this device to accurately control the key parameters such as the spray speed and angle of the slurry according to the specific requirements of the production process, and then produce high-tower compound fertilizer particles that meet different quality standards.
7.2.2 Granulator Spray cup:
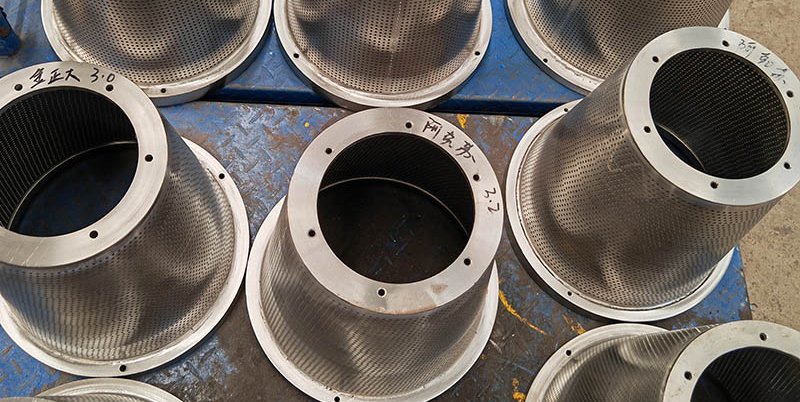
The spray cup is also an important part of the nozzle of the high-tower granulator, generally in the shape of a cone. There are many through holes on its surface. The aperture of the through holes is usually about 1.8-2.5 mm, and the spacing between adjacent through holes is also roughly within this range. The inner diameter of the upper opening of the spray cup and the inner diameter of the bottom are in a certain proportional relationship. The taper is generally between (53:160)-(53:130). The height is larger than that of the traditional spray cup, usually around 650-800 cm. This design can effectively improve production efficiency. In order to further improve the spraying condition of the slurry, the through holes will form several rows of inclined through hole rows on the plane. The angle formed by the inclined through hole rows and the horizontal line is about 30°. During operation, the molten fertilizer is introduced into the spray cup, and the spray cup rotates at high speed under the action of a motor or other driving device. The liquid fertilizer in the spray cup is sprayed out from the through holes on the spray cup under the action of centrifugal force to form small droplets. The small droplets are thrown into the high tower. During the falling process of the high tower, they gradually cool and solidify to form solid particles, thereby completing the fertilizer granulation production. Some spray cups are also equipped with scraper assemblies. The scraper is usually an arc-shaped plate. Its function is to generate pressure from top to bottom on the slurry, forcing the slurry to spray out from the middle and lower sections of the spray cup, so that the particle size of the fertilizer particles can be smaller and more uniform.
7.2.3 Outside spray cup:
In the high-tower compound fertilizer granulator, there is also an external spray cup. It has structures such as side metal mesh and metal ring. The cross-section of the side metal mesh is a trapezoidal structure. The barrel is covered with 7000-8000 tapered holes with small inside and large outside, with a diameter of 2.4-3.2 mm. When rotating, the material can be thrown out of the tapered hole to form a granular free fall. The metal ring is located above the side metal mesh and is connected to the side metal mesh through a clamping mechanism, which is convenient for the removal, cleaning and replacement of the side metal mesh.
7.3 Technical data table and model selection of high tower spray granulator:
Parameter | Model 25.5 | Model 30.5 | Model 40.5 | Model 45.4 |
Granulation Tower Height | 80 m | 100 m | 110 m | 128 m |
Granulation Tower Diameter | 20m | 20 m | 20 m | 22 m |
Nozzle Top Inner Diameter | 250 mm | 300 mm | 350 mm | 400 mm |
Nozzle Bottom Inner Diameter | 100 mm | 120 mm | 150 mm | 180 mm |
Nozzle Taper | 53:150 | 53:140 | 53:135 | 53:130 |
Nozzle Height | 700 cm | 750 cm | 800 cm | 850 cm |
Spray Orifice Diameter | 2.0 mm | 2.5 mm | 3.0 mm | 3.2 mm |
Number of Spray Orifices | 3,000 | 4,000 | 5,000 | 6,000 |
Orifice Inclination Angle | 30° from horizontal | 30° from horizontal | 30° from horizontal | 30° from horizontal |
Feed Pressure | 5 MPa | 7 MPa | 9 MPa | 10 MPa |
Feed Temperature | 120°C | 130°C | 140°C | 145°C |
Spray Head Rotation Speed | 300 rpm | 320 rpm | 350 rpm | 380 rpm |
Hourly Output | 8 tons | 12 tons | 20 tons | 25 tons |
Product Particle Size | 1.5 – 3.0 mm | 2.0 – 4.0 mm | 2.5 – 5.0 mm | 3.0 – 5.5 mm |
Product Particle Strength | 4 N | 5 N | 6 N | 7 N |
8. High tower compound fertilizer disc collecting scraper machine

The high-tower disc collector is usually located at the bottom of the granulation tower and is a key equipment used in the high-tower granulation process. It is mainly composed of a disc, a scraper, a transmission device and other parts. The disc diameter is generally 10~15 meters, and it rotates smoothly at a lower speed (such as 5-10 revolutions per minute) through the transmission device. Its function is to collect the granular materials falling from the high tower, use the scraper to scrape the materials from the edge of the disc, and transport them to the subsequent packaging or storage links. It can adapt to high-tower granulation systems of different outputs, with a maximum processing capacity of 40 tons per hour. It has the characteristics of high collection efficiency, stable material transportation, and effective avoidance of particle breakage.
8.1 What is the working principle of this high tower rotary scraper machine?

8.1.1 Material receiving and initial distribution
During the high tower granulation process, the slurry sprayed from the granulation nozzle is cooled and solidified in the high tower to form granular materials, which fall freely from the top of the high tower. The disc of the high tower disc receiver is located in a suitable position at the bottom of the high tower to receive the falling granular materials. Since the granular materials have a certain speed and dispersion during the falling process, when they fall on the disc, an initial material accumulation will be formed in the central area of the disc.
8.1.2 Disc rotation and centrifugal action
The disc is driven by a motor through a transmission device and performs circular motion at a relatively stable and low speed (usually 5-10 revolutions per minute). As the disc rotates, the granular materials falling on the disc will be affected by centrifugal force. According to the centrifugal force formula (F = mω²r) (where F is the centrifugal force, m is the mass of the material particles, (ω) is the angular velocity of the disc, and r is the distance from the material particles to the center of the disc), the material particles will diffuse from the center of the disc to the edge under the action of centrifugal force. This process allows the material to gradually form a material layer on the disc that becomes thinner from the center to the edge, thus achieving the initial distribution of the material on the disc.
8.1.3 Scraper scraping and conveying
A scraper is installed on the edge of the disc, and an appropriate gap is maintained between the scraper and the disc (generally a few millimeters to more than ten millimeters, depending on the material characteristics and production requirements). When the rotating disc conveys the material to the edge of the disc, the scraper will scrape the material off. The shape and angle of the scraper are carefully designed, usually tangent to the edge of the disc or at a certain angle of inclination, so that the material can be effectively scraped off the disc and guided to move in the direction of the scraper. The scraped material will slide along the scraper and then enter the conveying device connected to the bottom of the scraper, such as a conveyor belt or chute. The conveying device will transport the material to the subsequent packaging equipment or storage bin, thereby completing the material collection and conveying process.
8.1.4 The role of auxiliary devices
In order to better realize the collection and conveying of materials, some high-tower disc collectors are also equipped with auxiliary devices. For example, a material dispersion device such as a rotating material plate or an air jet device may be installed above the disc. These devices can disperse the materials initially when they fall, so that the materials are more evenly distributed on the disc, avoiding local accumulation and affecting the collection effect. In addition, buffer devices such as buffer pads or buffer chutes may be set under the disc or in the conveying device to reduce the impact force of the materials during the falling and conveying process, prevent particle breakage, and ensure product quality.
8.2 Technical parameter table of double spiral collecting turntable for compound fertilizer high tower granulation
Parameter Category | Parameter Details | Description |
Disc | Diameter: 9.5 - 10.5 m | Matches the capacity of high tower granulation, provides sufficient material area |
Rotation Speed: 3 - 8 rpm | Balances centrifugal distribution and scraping efficiency, avoids scattering/accumulation | |
Gear Ring Spec: Module 8 - 12, ~300–400 teeth (adjusted by diameter) | Works with drive gear to transmit motor power for disc rotation | |
Number of Support Rollers: 8 - 12 | Evenly supports the disc, ensures smooth rotation and reduces wear | |
Roller Diameter: 200 - 300 mm | Strong enough to support disc weight and material load | |
Screw Assembly | Left/Right Shaft Diameter: 150 - 200 mm | Ensures shaft strength and stability for screw blade rotation |
Screw Blade Outer Diameter: 800 - 1000 mm | Fits above the material collection pan, effectively pushes material | |
Screw Pitch: 300 - 500 mm | Controls pushing speed for uniform material transport | |
Shaft Rotation Speed: 15 - 30 rpm | Coordinates with disc speed to direct material toward the discharge hole | |
Gear Motor Power (each): 11 - 15 kW | Provides stable torque to drive the screw blades | |
Scraper | Quantity: 4 - 8 | Evenly distributed on the disc edge for complete scraping |
Length: 0.8 - 1.2 m | Matches disc diameter for effective scraping coverage | |
Width: 0.2 - 0.3 m | Ensures scraping force and material guidance | |
Angle with Disc: 45° - 60° | Promotes efficient material scraping and transport | |
Motor | Number of Disc Drive Motors: 3 - 5 | Provide power jointly for stable disc rotation |
Disc Drive Motor Power (each): 7.5 - 11 kW | Selected based on disc load and speed requirements | |
Screw Shaft Gear Motor Power (each): 11 - 15 kW | Meets material transport power demand of screw blades | |
Discharge Port | Outlet Diameter: 600 - 800 mm | Ensures smooth material discharge and links to next stage |
Discharge Hopper Size (L × W × H): approx. 1500×1500×2000 mm | Guides material to the collection pan, fits layout | |
Overall | Equipment Height (with support): approx. 3 - 4 m | Considers installation space and connection to lower conveyors |
Equipment Weight: approx. 20 - 30 tons | Includes all components: disc, screw, scraper, motors, etc. | |
Processing Capacity: 20 - 50 tons/hour | Depends on material characteristics and operating parameters |
9. How to cool down high tower fertilizer granule temperature efficiently?
The high tower compound fertilizer production line uses two types of cooling equipment, namely drum cooler and solex plate-coil bulk flow heat exchanger.
- Drum cooler is a kind of equipment commonly used in compound fertilizer production. It allows the drum wrapped with compound fertilizer particles to fully contact the particles with cold air during the rotation process, and uses the heat exchange principle to take away the heat of the particles to achieve the cooling of the high tower compound fertilizer. This cooling method can effectively reduce the temperature of compound fertilizer particles and prevent them from agglomerating and discoloring due to high temperature. At the same time, under the action of the drum, the particles can also be tumbled and screened to a certain extent, making the product quality more uniform and stable.
- The solex bulk flow heat exchanger powder flow cooler uses powder fluidization technology to put the high-temperature compound fertilizer powder in a fluidized state, which is evenly surrounded by low-temperature gas and heat exchanged. Its unique design can make the cooling process more efficient and uniform, avoiding the local overheating or uneven cooling that may occur in traditional cooling methods, greatly improving the cooling effect and product quality. In addition, the powder flow cooler also has the advantages of small footprint and low energy consumption, and has gradually been widely used in modern compound fertilizer production.
9.1 What is rotary drum cooling machine in high tower fertilizer plant?

Tongli high tower compound fertilizer drum cooler is a cooling device used in the production process of high tower compound fertilizer to cool it down from 90 degrees to 40 degree. It is mainly composed of a drum, a driving device, a feeding and discharging device, a ventilation device and other parts. The drum is an inclined cylindrical cylinder made of rolled steel plates, with spiral blades or lifting plates inside.
What is the working principle of the rotary drum high tower cooling machine?
During operation, the high-temperature compound fertilizer particles enter from the high end of the drum. Under the rotation of the drum, the particles fall along the spiral blades or are lifted by the lifting plates, and continue to roll forward. At the same time, the cooling air enters from the other end of the drum, fully exchanges heat with the compound fertilizer particles, takes away the heat of the particles, cools the compound fertilizer particles, and finally discharges them from the low end of the drum. By adjusting the parameters such as the speed of the drum, the tilt angle, and the flow rate of the cooling air, the cooling effect and residence time of the compound fertilizer particles can be controlled to meet the requirements of different production processes.
9.2 What is plate-coil solex bulk flow heat exchanger cooler in high tower fertilizer plant?

Solex plate-coil powder flow cooler is an energy-saving, green and low-carbon cooling equipment, which was innovatively developed by Solex Company of Canada in the 1980s. It combines the dense phase conveying principle with the traditional plate heat exchanger design concept. The dense phase conveying principle is used to ensure that the material is freely discharged at a uniform speed in the same cross section of the box and silo, so as to achieve a uniform cooling effect of the material, while avoiding the generation of dead zones and bridging blockages. The cooling water flows from bottom to top through the channel inside the heat transfer plate, and the powder materials such as compound fertilizer particles pass slowly and evenly from top to bottom between the heat transfer plates by gravity, and the liquid phase and the solid phase exchange heat in countercurrent to achieve the cooling purpose.
9.2.1 What is the stucture of the canada solex water-cooled powder heat exchanger?

9.2.1.1 Feeding Part
Inlet Hopper: Located at the top of the heat exchanger, it is used to receive hot products. Hot materials enter the equipment from here, which is the starting point for materials to enter the heat exchange process. Its design helps the materials to be evenly dispersed into the subsequent areas.
9.2.1.2 Heat Transfer Part
Cooling Plates: It is the core component of the heat exchanger and consists of a series of metal plates. Cooling water flows through the cooling plates (through the Closed-Loop Cooling Water circulation loop, driven by the Circulating Pump, and cooled by Water Cooling), and the high-temperature materials pass through the cooling plates, and heat is transferred through the metal plates to achieve material cooling. The structure and layout of the cooling plates determine the efficiency and effect of heat exchange.
9.2.1.3 Connection and Sealing Part
Flexible Connections: Used to connect cooling plates and other components, allowing a certain degree of displacement and deformation, compensating for dimensional changes caused by factors such as thermal expansion and contraction, while ensuring the sealing of the system to prevent material leakage and loss of cooling medium.
9.2.1.4 Detection and control part
- Temperature sensor (TI): installed in the feed hopper and other key positions of the equipment, used to monitor the material temperature in real time, and provide temperature data for the control system to adjust the operating parameters according to the temperature conditions.
- Level sensor (LE, LT): used to detect the material level height in the feed hopper and feed back to the control system, so that the system can control the feeding speed, unloading speed, etc. according to the material level conditions to maintain stable operation of the system.
- Control system (Control System): Receives signals from temperature sensors, material level sensors, etc., and controls the entire heat exchange process according to preset parameters and logic, such as adjusting the opening and closing degree of the unloading device (controlled by Pneumatic Actuator) to control the material flow rate, coordinate the cooling water flow rate, etc., to ensure that the material cooling effect meets production requirements.

9.2.1.5 Auxiliary part:
- Plant ventilation (Plant Ventilation): used to discharge the heat and moisture generated during the heat exchange process, maintain the air circulation and quality inside and around the equipment, and prevent the accumulation of hot and humid gases from affecting the operation of the equipment and the surrounding working environment.
- Dry Air Purge (Optional): Optional, introduce dry air to purge the inside of the equipment to prevent the material from getting damp and agglomerated inside the equipment. It is especially suitable for materials that are sensitive to humidity to ensure the dryness inside the equipment and good fluidity of the material.
- Feeding device (with Pneumatic Actuator at the bottom): Located at the bottom of the heat exchanger, it is used to discharge the cooled product (Cooled Product to Coating and Storage) and send it to the subsequent coating processing and storage links. The pneumatic actuator is used to control its opening and closing degree, adjust the feeding speed, and cooperate with the control system to maintain the stable material level and flow state of the material in the equipment.
9.2.2 Why use solex plate-coil water cooled cooling machine in high tower fertilizer production line?
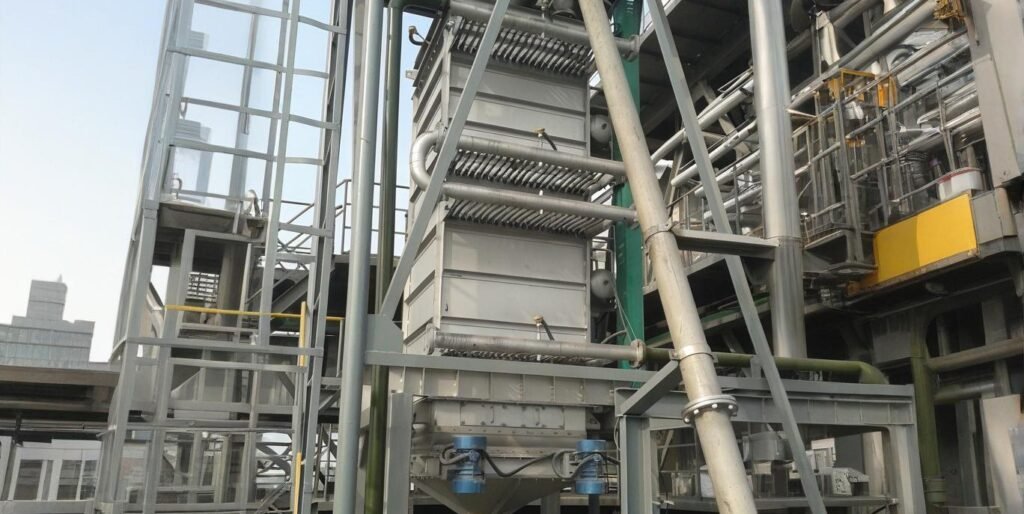
- Efficient cooling: The powder flow cooler uses Canada Solex's unique powder fluidization technology to evenly surround the high-temperature compound fertilizer with water cooling plates and exchange heat. This cooling method can achieve efficient and uniform cooling, avoiding local overheating or uneven cooling that may occur in traditional cooling methods. It can quickly cool the high-tower compound fertilizer particles to the required temperature, improving production efficiency and product quality.
- Protect product quality: During the cooling process, the powder flow cooler can effectively prevent the agglomeration, discoloration and pulverization of compound fertilizer particles. Due to uniform cooling, the temperature gradient on the surface and inside of the particles is small, which reduces the particle breakage and deformation caused by thermal stress, maintains the integrity and appearance quality of the compound fertilizer particles, and also helps to maintain the nutrient content and chemical stability of the compound fertilizer.
- Energy saving and consumption reduction: The equipment adopts the principle of countercurrent heat exchange, fully utilizes the characteristics of the large specific heat capacity of cooling medium water, improves heat exchange efficiency, and reduces the amount and energy consumption of cooling medium. Compared with other cooling equipment, the powder flow cooler can achieve better cooling effect at lower energy consumption, which helps to reduce production costs and achieve the goal of energy saving and emission reduction.
- Environmental advantages: The powder flow cooler generates less dust and noise during operation, and has less pollution to the environment. At the same time, since the cooling medium can usually be recycled, the discharge of wastewater and exhaust gas is reduced, which meets environmental protection requirements and is conducive to the sustainable development of the enterprise.
- High degree of automation: The powder flow cooler is equipped with an advanced automatic control system, which can accurately control parameters such as cooling temperature, material flow and cooling medium flow according to the requirements of the production process. This not only improves the stability and reliability of the production process, but also reduces manual intervention, reduces labor intensity, and improves the level of automation in production.
9.2.3 What are the adventages of solex water-cooled pate coil heat exchanger?
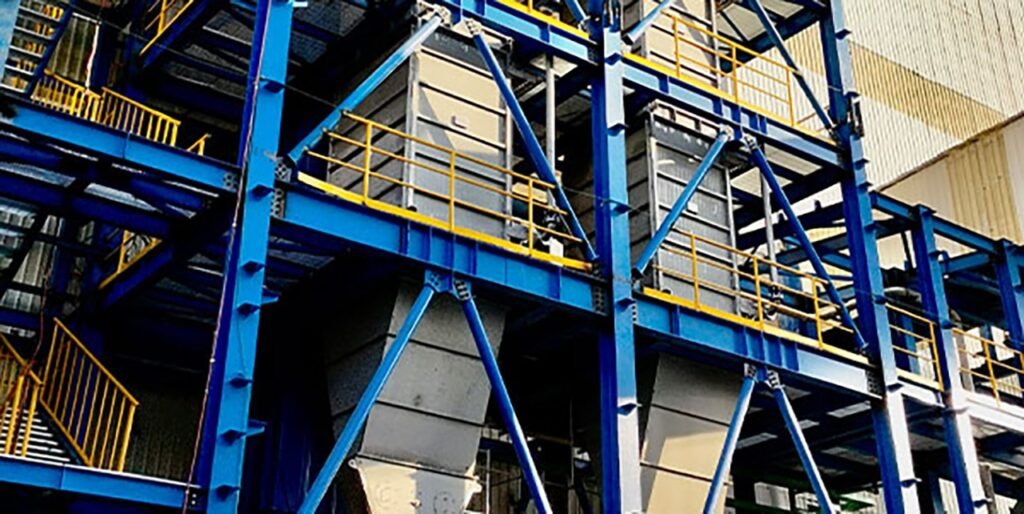
- Significant reduction in energy consumption: Use up to 90% less energy, energy consumption can be reduced by up to 90%, through efficient heat exchange technology, reduce energy consumption and reduce production costs.
- Uniform Final Product Temperatures: The mass flow design means the product moves slowly and with uniform velocity through the cooler. This enables even temperature distribution producing stable and uniform final product temperatures.
- Recover and reuse waste energy: Recover and reuse waste energy, can recycle and reuse waste heat, improve energy utilization, achieve efficient energy utilization and sustainable development.
- Guaranteed thermal performance: Guaranteed thermal performance, ensure stable and good heat exchange performance, can reliably achieve cooling of high-tower compound fertilizer, and meet the production process temperature requirements.
- Mass Flow Technology: The mass flow discharge feeder creates uniform product velocity through the cooler and regulates the product flow rate.
- Prevent product damage: Prevent abrasion or degradation, can effectively prevent compound fertilizer particles from being worn or degraded during the cooling process, and ensure the integrity and stability of product particles.
- Accurate and uniform temperature: Receive precise & uniform final temperatures, can enable compound fertilizer to obtain precise and uniform final cooling temperature, ensure product quality uniformity, and improve product quality.
- Compact and Modular Design: The compact installation footprint makes this design easy to integrate into existing plants, and is ideal for debottlenecking or revamps. The modular design means additional Platecoil heat exchange banks can be stacked if increased cooling capacity is required in the future.
- Reduce pollutant emissions: Reduce emissions dust, fines or odors, can reduce pollutant emissions such as dust, fines and odors, improve the production environment, and meet environmental protection requirements.
- Compact and modular design: The equipment is compact in design, occupies little space, and adopts modular design, which is easy to install, expand and maintain, and can flexibly adapt to different production scale requirements.
- Reduced installation costs: Reduced installation costs, with its compact design and reasonable structure, it can reduce the cost of manpower, material resources, etc. during the installation process.
- Produces a Superior Final Product: The slow and controlled movement of the product through the cooler prevents product abrasion and degradation so that there is no change in particle characteristics or crystal shape.
9.2.4 Technical data table of solex pate-coil heat exchanger:
Parameter | Typical Range / Value | Notes |
Heat Transfer Method | Indirect | Uses vertical hollow plates |
Heat Transfer Surface Area | 10 – 500 m² | Depends on model and capacity |
Thermal Duty | Up to 50,000 kW | Varies by application and unit size |
Material Flow Rate | 1 – 1000+ tons/hour | Depends on product density and flow properties |
Operating Temperature | Up to 700°C (for solids) | Heating/cooling depending on process |
Heating Media | Steam, Thermal Oil, Hot Water | Flow inside the plates |
Cooling Media | Water, Glycol, Chilled Water | For cooling applications |
Solids Handled | Fertilizers, Sugar, Sand, Minerals | Free-flowing granular or crystalline solids |
Plate Material | SS304, SS316, Duplex, etc. | Based on product corrosiveness and thermal requirement |
Solids Residence Time | 5 – 60 minutes | Can be designed per process requirement |
Energy Consumption | Up to 90% lower than rotary drums | No moving parts inside product zone |
Footprint | Compact (varies by capacity) | Vertical design saves floor space |
Maintenance | Low | No moving parts in contact with material |
10. The importance of screening in high tower fertilizer production

Tongli high tower compound fertilizer line rotary drum screen uses a unique structural design to use the rotation of the screen drum to fully roll and screen the materials in it, accurately classify the compound fertilizer particles according to the particle size, and effectively ensure that the finished product particles are uniform in size. In the production process of high tower compound fertilizer, the particle size of compound fertilizer will vary due to various factors. Through screening, large or small particles that do not meet the particle size requirements can be returned to the production process for reprocessing, so that the materials in the production process can be recycled. At the same time, timely screening out materials that do not meet the requirements can reduce the energy loss of subsequent cooling and coating, and reduce the load of equipment.
10.1 What is the structure of the high tower fertilizer screener?

10.1.1 Shell:
The drum screen shell mostly adopts a fully enclosed welded structure, made of Q235B steel plate with a thickness of 4-8mm, which can effectively resist the impact and wear of materials during the screening process. Its appearance is based on the screen cylinder and the internal structure layout, usually designed as a cuboid. In order to avoid dust spilling during the screening process, the shell connection parts adopt a special sealing design. At the shell joints, a continuous welding process is used, and sealant is applied to further enhance the sealing effect; rubber sealing pads are installed at the connection with the feed port, discharge port and inspection door. According to GB/T 14683 standard, the compression rate of the sealing pad is controlled at 15%-25%, which can make the dust leakage rate less than 0.1%, meeting environmental protection and safe production requirements.
10.1.2 Screen mesh:

Screen mesh material: 304 stainless steel wire is commonly used for metal wire mesh, with a wire diameter of 0.1-0.5mm and an opening rate of 40%-60%; steel plate punching screen is mostly made of Q345, with a hole diameter of 1-20mm, which can be customized according to demand. The hole types are round, square, etc., and the processing accuracy of round holes can reach ±0.1mm. The number of screen layers depends on the screening process. When the double-layer screen is used, the inner screen has a larger hole diameter than the outer layer, such as 8mm for the inner layer and 4mm for the outer layer, to achieve graded screening of materials and improve screening accuracy and efficiency.
10.1.3 Support device:
When the roller is supported, the diameter of the roller is 100-200mm, the material is 45 steel, the surface hardening hardness is HRC40-45, the spacing between each group of rollers is 0.8-1.2m, and the bearing capacity can reach 1-3t according to the weight and length of the screen drum. The bearing support mostly uses spherical roller bearings, such as 22208, with a rated dynamic load of 140kN, which can adapt to the radial and axial loads of the screen drum, reduce operating vibration and noise, and ensure the smooth rotation of the screen drum.
10.1.4 Feed port and discharge port:
The feed port size is designed according to the material conveying volume and flow rate, and is calculated using the Bernoulli equation combined with actual working conditions. For example, if the conveying volume is 5t/h and the material flow rate is 0.5m/s, the cross-sectional area of the feed port is about 0.003m², mostly rectangular, with a size of 200mm×150mm. The discharge port is set according to the screening specifications, and the size and position of the qualified fine material, coarse material and large miscellaneous discharge ports are arranged according to the production process to ensure smooth discharge of materials and prevent blockage and mixing.
10.1.5 Drive device:
The screen motor is selected according to the power calculation formula P = Tn/9550 (T is torque, n is speed) based on the screen drum load and speed requirements. For example, if the screen drum load torque is 1000N・m and the speed is 10RPM, the motor power is about 1.05kW, and the YE3 series high-efficiency and energy-saving motor is often selected. The reducer mostly uses a helical gear reducer with a transmission efficiency of 92% - 96% and a speed ratio range of 5 - 50. It is matched according to the motor and screen drum speed, such as a motor of 1450RPM, a screen drum of 10RPM, and a speed ratio of 145. The motor and reducer are connected by an elastic pin coupling to compensate for the relative displacement of the two shafts by ±0.5mm and buffer the start-up impact.
10.1.6 Screen self cleaning mechanism:
The comb teeth of the comb cleaning mechanism are made of 65Mn spring steel, with a tooth spacing of 5-10mm and a gap of 1-2mm with the screen. The screen drum rotates at a frequency of 2-3Hz, effectively clearing the blocked screen holes. The bouncing ball screen cleaning uses polyurethane bouncing balls with a diameter of 20-30mm and a density of 0.9-1.1g/cm³. 8-12 balls are arranged per square meter of screen. The elasticity of the ball is used to impact the screen to remove the adhered materials. The brush cleaning uses nylon bristles with a hardness of 80-90HA, a bristle length of 20-30mm, and an installation spacing of 10-15mm. It continuously cleans the screen, maintains the transparency of the screen, and ensures stable screening efficiency.
10.1.7 Drive shaft:
The drive shaft is generally made of medium carbon alloy steel such as 40Cr. After quenching and tempering treatment to improve the comprehensive mechanical properties, its allowable torsional shear stress can reach 50-80MPa. According to the torque calculation formula T = 9550P/n (P is the motor power, n is the screen drum speed), the selection is combined with the screen drum load and speed requirements. For example, a 5.5kW motor drives a screen drum with a speed of 15RPM, and the drive shaft torque is about 3500N・m. The shaft diameter design must meet the strength and stiffness conditions, and is determined according to the empirical formula d≥A³√(T/[τ]) (A is the coefficient, [τ] is the allowable shear stress) to ensure stable power transmission.
10.1.8 Upper dust cover and dust removal port:
The sealing performance of the upper dust cover is designed according to GB/T 17626.3 standard, which can effectively reduce the dust leakage rate by more than 90%. The dust removal port is connected to the cyclone dust collector or bag dust collector. The inlet wind speed of the cyclone dust collector is 18-23m/s. The processing air volume is determined by the specifications of the screen drum and the amount of dust generated. For example, the diameter of the screen drum is 1.5m, and the air volume is about 3000-5000m³/h. The bag dust collector has a filtration wind speed of 0.8-1.2m/min, and the filtration efficiency is more than 99%. It can control the emission dust concentration below 30mg/m³, which meets the environmental emission standards.
10.1.9 Maintenance platform:
As a key facility for equipment maintenance, the maintenance platform's load-bearing capacity must comply with relevant mechanical design standards. It is usually designed to withstand 3-5 people and 50-100kg of maintenance tools. Its surface anti-slip coefficient is in accordance with GB 4053.3 standard, not less than 0.6, to prevent personnel from slipping during operation. The platform material is mostly Q235B hot-dip galvanized steel, which has good anti-corrosion properties, ensuring long-term safety in complex working conditions such as dust and high humidity, and facilitating personnel to conduct regular inspection and maintenance of screens, drive components, etc.
10.2 Why does high tower compound fertilizer need screening?
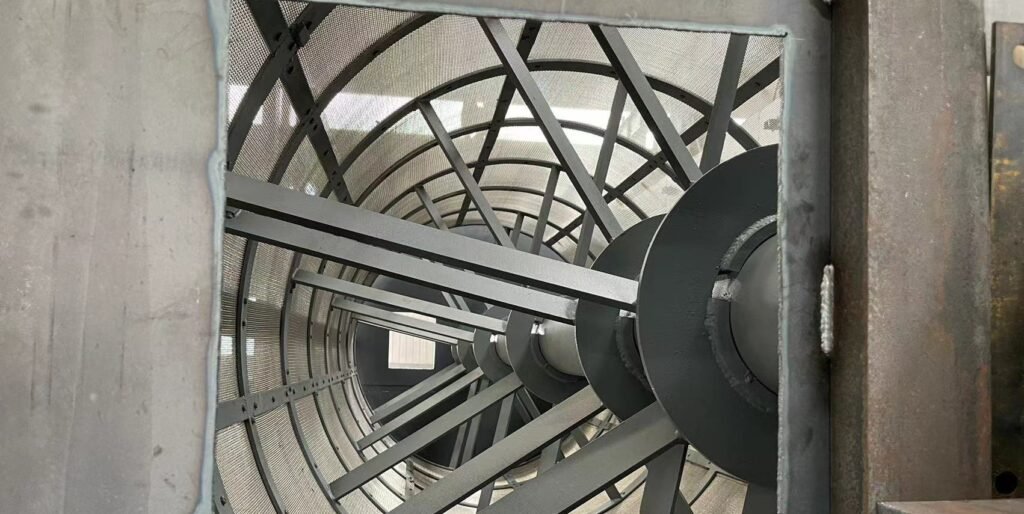
10.2.1 Improve product market competitiveness:
Product appearance and quality consistency are important factors affecting sales. High-tower compound fertilizer particles with uniform particle size give people a visually neat and high-quality intuitive feeling. When farmers use it, uniform particles are easier to control the amount of fertilizer, avoiding excessive or low local fertilizer concentration due to uneven particle size, which affects crop growth.
10.2.2 Improve cooling efficiency:
Compound fertilizer particles with uniform particle size are more evenly distributed in the cooler, and cold air can pass through the particle layer more evenly and fully exchange heat with the particles. In contrast, particles with different particle sizes will cause uneven airflow distribution in the cooler, the gaps between large particles are larger, and the airflow is easy to short-circuit, while small particles may be too densely stacked, hindering the airflow, resulting in poor cooling effect. Screening to make the particle size uniform can make the heat exchange process in the cooler more efficient. In the same cooling time, the compound fertilizer particles can be cooled to the required temperature more quickly, thereby reducing the operating time of the cooler and reducing energy consumption.
10.2.3 Reduce production energy consumption and equipment loss:
If screening is not performed, particles of different sizes will enter the subsequent processing links, such as packaging and transportation, which will cause many problems. Small particles are prone to dust, which not only causes material waste, but also may affect the air quality of the production workshop, increase the load of ventilation and dust removal equipment, and increase energy consumption. Large particles or agglomerated particles may cause packaging equipment to stagnate and wear containers during transportation. Screening and removing unqualified particles in advance can make the properties of materials entering subsequent equipment more uniform, the equipment run more smoothly, reduce the frequency of equipment failure maintenance, reduce the degree of equipment wear, extend the service life of the equipment, and significantly reduce the cost of equipment maintenance and replacement, so as to achieve energy saving and efficiency improvement in the production link.
10.2.4 Improve product stability and storage performance:
Compound fertilizer particles with consistent particle size have better stability during storage and transportation. Particles of uniform size are tightly packed, and it is not easy for particles to squeeze and break each other, which reduces the generation of dust and the possibility of fertilizer agglomeration. For example, during long-term storage, compound fertilizers with uneven particle sizes are prone to uneven moisture absorption due to differences in the gaps between particles, which in turn causes agglomeration, while compound fertilizers with uniform particle sizes that have been screened can better maintain a loose state, which is convenient for storage and subsequent use.
10.2.5 Reduce the load on the cooler:
When the particle size of the compound fertilizer particles is uniform, their movement state in the cooler is relatively stable, and there will be no excessive collision, friction and accumulation due to differences in particle size. This means that the conveying device, stirring device and other components of the cooler are subject to less resistance during operation, and the driving equipment such as the motor does not need to consume too much energy to maintain the normal operation of the equipment. For example, for a spiral conveyor cooler, particles with uniform particle size can make the process of the spiral blade pushing the material more stable, reduce local blockage and jamming caused by uneven particle size, thereby reducing the overall load of the cooler and achieving the purpose of energy saving.
10.2.6 Comply with industrial production and quality standards:
In the process of compound fertilizer production, screening is an important link to ensure that product quality meets standards. Industry standards and enterprise production specifications usually have clear requirements for the particle size range of compound fertilizers. Screening can remove particles that are too large or too small that do not meet the particle size requirements, making the product quality stable and consistent and improving the market competitiveness of the product. For example, the national standard stipulates that the particle size of a certain type of compound fertilizer should be between 2 and 4 mm. Screening can ensure that the product meets this standard and meets the actual needs of agricultural production.
10.2.7 Ensure uniformity of fertilization:
Compound fertilizers with uniform particle sizes can be more evenly distributed in the field during fertilization. If the fertilizer particles are of different sizes, when spreading or mechanically applying fertilizers, large particles may be concentrated in certain areas, while small particles are distributed in other areas, resulting in uneven fertilization and affecting the consistency of crop growth.
10.2.8 Meet the needs of different crops and soils:
Different crops have different requirements for fertilizer particle size at different growth stages. Some vegetable crops have shallow roots distributed on the soil surface, and require compound fertilizer particles with smaller particle sizes so that they can dissolve quickly and be absorbed by the roots. However, deep-rooted crops such as fruit trees have deep root distributions, and compound fertilizer particles with larger particle sizes are more conducive to slowly releasing nutrients to meet their long-term growth needs. At the same time, soils of different textures have different adaptability to fertilizer particles. Sandy soils have poor fertilizer retention, so it is appropriate to use compound fertilizers with smaller particle sizes, which can quickly exert fertilizer effects; clay soils have good fertilizer retention, and compound fertilizers with larger particle sizes can be selected to extend the fertilizer effect period. Through screening, compound fertilizers with suitable particle sizes can be provided according to different crops and soil conditions to improve fertilizer utilization.
10.3 Why rotary drum screener is suprior than vibrate screener?
- Good dedusting: The rotary drum screener has a outer shell and an upper cover plate, and is equipped with a dust removal port, which can be easily connected to a bag dust collector. During the screening process, the generated dust can be effectively collected through the dust removal port, reducing the flying of dust in the workshop, improving the working environment, and reducing pollution to the environment. In contrast, the vibrating screen has certain difficulties in dust removal. Due to its large vibration amplitude, dust easily escapes from various gaps. Even if equipped with dust removal equipment, it is difficult to achieve the same good dust removal effect as the drum screen.
- Small damage to fertilizer granule: During the screening process, the material slowly rolls in the drum as the drum rotates, and the impact and friction are relatively small. For granular products such as high-tower compound fertilizer, it can effectively reduce the particle breakage and dust generation caused by the screening process, and ensure the quality and appearance of the product.
- Large processing capacity: The structural design of the drum screen enables it to accommodate a larger volume of material, and the movement of the material in the drum is relatively smooth, which can achieve continuous feeding and discharging, so it can handle a larger material flow rate to meet the needs of large-scale production.
- Smooth operation: The drum screen adopts a drum structure, with less vibration during operation and good equipment stability. This not only helps to extend the service life of the equipment and reduce maintenance costs, but also generates relatively low noise during operation, which is conducive to improving the working environment.
- Re-processing: Compared with vibrating screens, drum screens have a significant advantage in screening convenience. Its unique structure makes it easy to add return material equipment. In actual production, you only need to cleverly place the cone bucket to allow the screened large particles to fall smoothly and directly into the chain crusher with the help of gravity, starting the secondary crushing process. In contrast, vibrating screens are limited by their structure and operating principles, and it is difficult to connect to return material equipment so efficiently and conveniently. This feature makes the drum screen better at optimizing production processes and improving material recycling efficiency, ensuring close coordination of all links in the production of high-tower compound fertilizers and reducing manpower and time costs.
10.4 High tower screening machine technical parameter data table:
Parameter | Details |
Product Name | Fertilizer Sieve Machine/screener |
Model | ZJTL2290 |
Power | 37 KW, 45 KW |
Voltage | 380V |
Motor Power | 3–37 KW |
Rotary Speed | 13–20 r/min |
Capacity | 10–60 Ton/Hour |
Mesh Size | 10–65 m² |
Weight | 16,500 kg |
Machine Material | Carbon Steel / SS304 |
Application | Classification and Screening of Compound Fertilizer |
Place of Origin | Zhejiang, China |
Brand Name | ZJTL Series Sieving Machine |
Warranty | 12 month or 18 months after delivery |
After Warranty Service | 1–3 years |
After-sales Service Provided | Online Support |
Video Outgoing-Inspection | Provided |
Machinery Test Report | Provided |
Core Components | PLC, Engine, Bearing, Gearbox, Motor |
11. How does coating enhance the durability of high tower fertilizer?

The high-tower compound fertilizer coating can form a protective film on the surface of the fertilizer particles, effectively reducing the direct contact between the fertilizer and the external environment, reducing the volatilization and loss of nutrients, and improving the utilization rate of the fertilizer; at the same time, the coating can control the release rate of nutrients in the fertilizer, so that it can slowly release nutrients according to the different stages of crop growth, achieve synchronization between nutrient supply and crop demand, and extend the fertilizer effect period; in addition, the coating can also improve the physical properties of the fertilizer particles, such as increasing the hardness and wear resistance of the particles, reducing breakage and dust generation during transportation and storage, improving the appearance quality and commercial value of the fertilizer, and to a certain extent preventing the fertilizer from absorbing moisture and agglomerating, making it easier to store and apply.
11.1 What is high tower fertilizer plant coating machine?
The high tower compound fertilizer coating machine usually adopts the rotary coating method. When the equipment is running, the compound fertilizer particles enter the rotating drum of the coating machine from the feed port, and at the same time, the coating liquid is evenly sprayed on the surface of the particles through the nozzle. As the drum rotates, the particles continue to roll in the drum, so that the coating liquid can be evenly wrapped on the surface of each particle, forming a uniform coating.
11.2 What equipment is used in high tower fertilizer coating process?
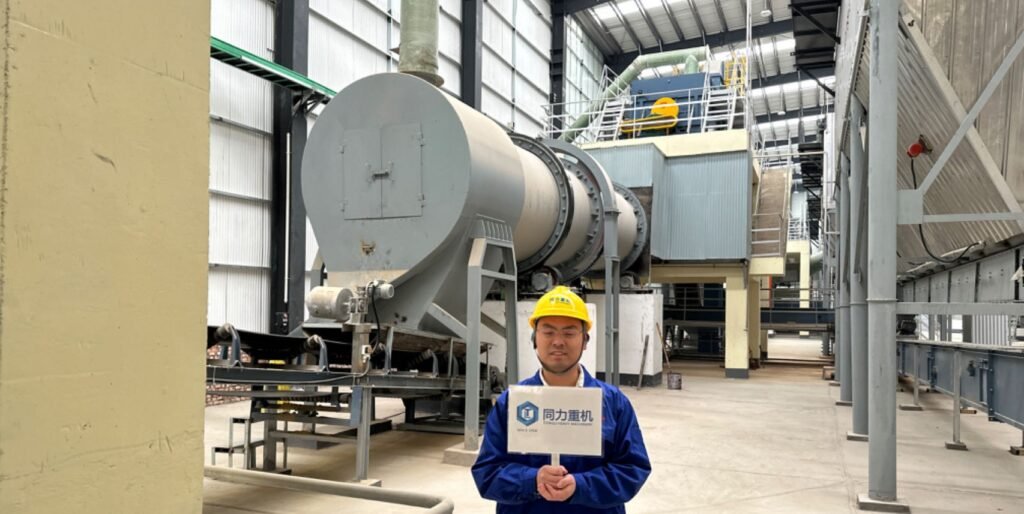
11.2.1 Feeding system:
The bucket elevator is responsible for evenly conveying the high tower compound fertilizer particles into the coating machine. It usually includes a feeding hopper and a feeding conveying device. The feeding speed of the hopper can be adjusted according to production needs.
11.2.2 Rotating drum:
It is the core component of the coating machine and is driven to rotate by a motor. The drum is usually equipped with a 304 liner because the coating oil and anti-caking agent are highly corrosive. It is used to push the particles to roll and move in the drum to ensure that the particles are fully in contact with the coating liquid and are evenly coated.
11.2.3 Coating liquid supply system:
It includes components such as coating oil tank, metering pump and nozzle. The coating oil tank is used to store the coating liquid. The metering pump extracts the coating liquid from the storage tank and conveys it to the nozzle. The nozzle sprays the coating liquid evenly on the particles in the form of mist.
11.2.4 Discharging system:
Located at the other end of the drum, it is used to discharge the coated compound fertilizer particles. The discharge port is usually connected to a conveying device to transport the coated products to the finished product packaging workshop for packaging.
11.4 What is coating oil and anti-caking agent used in high tower fertilizer coating machine?
11.4.1 What is Coating oil? Composition and type:
- Mineral oil-based coating oil: obtained by refining and modifying petroleum fractions as raw materials. For example, paraffin-based mineral oil has good chemical stability and low volatility, and can form a dense protective film on the surface of fertilizer particles. Its carbon chain length is generally between 16 and 30, and its molecular weight is relatively high, usually between 200 and 500.
- Plant oil-based coating oil: Common products include soybean oil, rapeseed oil, etc., which are modified by esterification or polymerization. This type of coating oil has good biodegradability and environmental protection. Taking soybean oil as an example, its main component is fatty acid glyceride, in which the content of unsaturated fatty acids such as oleic acid and linoleic acid is relatively high. After modification, its average molecular weight can reach about 300-600, with suitable viscosity and surface tension, and can be evenly coated on the surface of fertilizer particles.
- Synthetic oil-based coating oil: prepared by chemical synthesis, such as poly α-olefin (PAO). PAO has excellent low temperature performance, oxidation stability and thermal stability. It has a regular molecular structure and a high viscosity index. It can maintain a relatively stable viscosity at different temperatures. The general viscosity is between 2 - 100mm²/s at 40°C. Products with different viscosities can be selected for compound fertilizer coating according to needs.
11.4.2 What is Coating oil's function? How does it work?
- Physical isolation: Coating oil forms a continuous oil film on the surface of fertilizer particles, isolating the fertilizer from external moisture, oxygen, etc. The thickness of this oil film is usually between 0.01-0.1mm, which can effectively prevent moisture in the air from entering the fertilizer particles and slow down the deliquescence and loss of nutrients in the fertilizer. For example, for hygroscopic fertilizer components such as ammonium nitrate, coating oil can isolate them from external moisture to prevent agglomeration and nutrient loss.
- Reducing surface energy: Coating oil can reduce the surface energy of fertilizer particles, weaken the interaction between particles, and reduce the agglomeration and agglomeration between particles. At the same time, it can also reduce the adhesion between particles and packaging materials, which is convenient for the storage and transportation of fertilizers.
- Improving appearance: Coating oil can give fertilizer particles a good gloss, making the fertilizer more beautiful and improving the commodity value of the product. High-quality coating oil can make the gloss of fertilizer particles reach 60-80GU (gloss unit) or more, enhancing the competitiveness of the product in the market.
11.4.3 What is the Composition and type of anti-caking agent:
- Inorganic salt anti-caking agent: Magnesium carbonate has a large specific surface area and adsorption performance, and can be adsorbed on the surface of fertilizer particles to prevent direct contact between particles. Its particle size is generally between 1-10μm, and the addition amount is usually 0.5%-2% of the fertilizer mass. Calcium silicate is a white powder that is insoluble in water and has stable chemical properties. It can form a physical barrier on the surface of fertilizer particles to prevent particles from sticking together due to moisture absorption. The average particle size of calcium silicate is about 5-20μm, and the addition amount in compound fertilizer is generally 0.3%-1.5%.
- Surfactant anti-caking agent: Anionic surfactants such as sodium alkylbenzene sulfonate (LAS) contain hydrophilic and hydrophobic groups in their molecular structure. On the surface of fertilizer particles, the hydrophobic group faces the particle surface and the hydrophilic group faces outward, forming a layer of directional molecular film, which reduces the surface tension of the particle surface and makes it difficult for water to adhere to and penetrate the particle surface. The critical micelle concentration (CMC) of LAS is generally between 0.01% and 0.1%, and the amount added to compound fertilizer is usually 0.1% to 0.5%. Nonionic surfactants such as polyoxyethylene sorbitan fatty acid esters (Tween series) have good emulsification, dispersion and wetting properties. It can form a uniform protective film on the surface of fertilizer particles to prevent mutual attraction and agglomeration between particles. The hydrophilic-lipophilic balance (HLB) value of the Tween series is between 8 and 18. According to different fertilizer formulations and needs, products with appropriate HLB values are selected, and the addition amount is generally 0.2% to 0.8%.
- Polymer anti-caking agents: Sodium polyacrylate is a water-soluble polymer with strong water absorption and water retention. It can form an elastic polymer film on the surface of fertilizer particles. When there is water on the surface of the particles, sodium polyacrylate absorbs water to form a gel-like substance to prevent adhesion between particles. Its molecular weight is usually between 1000 and 10000, and the amount added is usually 0.1% - 0.3%. Polyvinyl alcohol has good film-forming and adhesive properties. The film formed on the surface of fertilizer particles has a certain degree of flexibility and strength, which can effectively isolate the contact between particles. The degree of polymerization of polyvinyl alcohol is generally between 500 and 2000, and the amount added to compound fertilizer is usually 0.2% - 0.6%.
11.4.4 How does anti-caking agent work? what is the working principle?
- Isolation effect: Anti-caking agents are adsorbed or wrapped on the surface of fertilizer particles to form an isolation layer, which separates the particles from each other and prevents the particles from agglomerating due to direct contact. For example, inorganic salt anti-caking agents are physically adsorbed on the surface of particles to form a structure similar to "microcapsules" to prevent adhesion between particles.
- Moisture absorption and regulation: Some anti-caking agents are hygroscopic and can preferentially absorb moisture in the air to form a humidity buffer layer on the surface of fertilizer particles to prevent fertilizer particles from directly absorbing a large amount of moisture and causing agglomeration. At the same time, when the ambient humidity decreases, they can slowly release the absorbed moisture. For example, high molecular weight polymer anti-caking agents such as sodium polyacrylate can adjust their own water absorption according to changes in ambient humidity and keep the surface of fertilizer particles relatively dry.
- Changes in surface properties: Surfactant anti-caking agents reduce the surface tension and polarity of the fertilizer particles, making the particle surface hydrophobic or weakly hydrophilic, reducing the attachment and penetration of moisture on the particle surface, thereby preventing the agglomeration and agglomeration of particles caused by moisture.
11.5 Technical parameter table of high tower fertilizer coating machine:
Component | Parameter |
Roller Ring | Diameter 2-3m |
Width: 0.3–0.5m | |
Weight (each): 2–5 tons | |
Material: ZG310–570 Cast Steel | |
Girth Gear | Module |
Number of Teeth: 90–120 | |
Width: 0.2–0.3m | |
Weight: 3–8 tons | |
Material: ZG310–570 Cast Steel | |
Pinion Gear | Number of Teeth |
Width: 0.2–0.3 meters | |
Weight: 0.5–1.5 tons | |
Material: ZG310–570 Cast Steel | |
Drum (Cylinder) | Diameter |
Length: 8–12 meters | |
Material: Medium Carbon Steel Plate | |
Internal Lining: Stainless Steel / Acid-Resistant Polypropylene | |
Production Capacity: 25t/h | |
Installed Power: 55–75 kW |
What are the Advantages of High Tower Fertilizer Plants?

Enhanced Nutrient Distribution and Uniformity
- The high tower compound fertilizer adopts melt granulation process. Various raw materials are heated to a molten state at the top of the high tower, and then the molten liquid is evenly sprayed down through the nozzle. It is fully in contact with cold air during the falling process, and quickly cooled and solidified into particles. This process makes the nutrient distribution inside the fertilizer particles more uniform, because in the molten state, various nutrients can be fully mixed to form a uniform liquid phase, and then this uniformity is maintained during the solidification process.
- Compared with the traditional granulation method, the granulation method is to agglomerate the raw material powder into particles by adding binders, etc., which is prone to uneven nutrient distribution inside the particles, especially for the addition of some trace elements, it is difficult to achieve uniform distribution. The melt granulation process of the high tower compound fertilizer can accurately control the proportion and distribution of nutrients to ensure that each fertilizer contains balanced nutrients.
Advantages of particle shape and structure:
The particles of high-tower compound fertilizer are nearly perfect spherical, with a smooth surface and uniform particle size. This particle shape makes the fertilizer more evenly distributed in the soil, can better contact with soil particles, and reduce the local enrichment or deficiency of nutrients. In contrast, some fertilizer particles produced by other processes are irregular in shape and of different sizes, which are prone to accumulation or uneven distribution in the soil, resulting in uneven nutrient release and affecting the absorption of nutrients by plants. The spherical particles of high-tower compound fertilizer also have good fluidity, which can be spread or applied more accurately during fertilization, further ensuring the uniform distribution of nutrients in the field.
Advantages of nutrient release characteristics:
The particle structure of high-tower compound fertilizer is relatively dense, and the nutrient release has certain slow-release characteristics. Due to the formation of a relatively stable crystal structure during the granulation process, the dissolution and release of nutrients in the soil are relatively slow and stable, which can continuously supply nutrients at different stages of plant growth and meet.
long-term demand of plants for nutrients:
Compared with some instant fertilizers, although instant fertilizers can quickly provide nutrients to plants, they are prone to nutrient loss and waste, and may cause plants to absorb too much nutrients in a short period of time, resulting in insufficient nutrients in the later period. The slow-release characteristics of high-tower compound fertilizers allow nutrients to be released evenly in the soil, improving nutrient utilization, reducing the number of fertilizations and fertilizer usage, and also reducing the risk of environmental pollution.
Improved Physical Properties of Fertilizer Granules
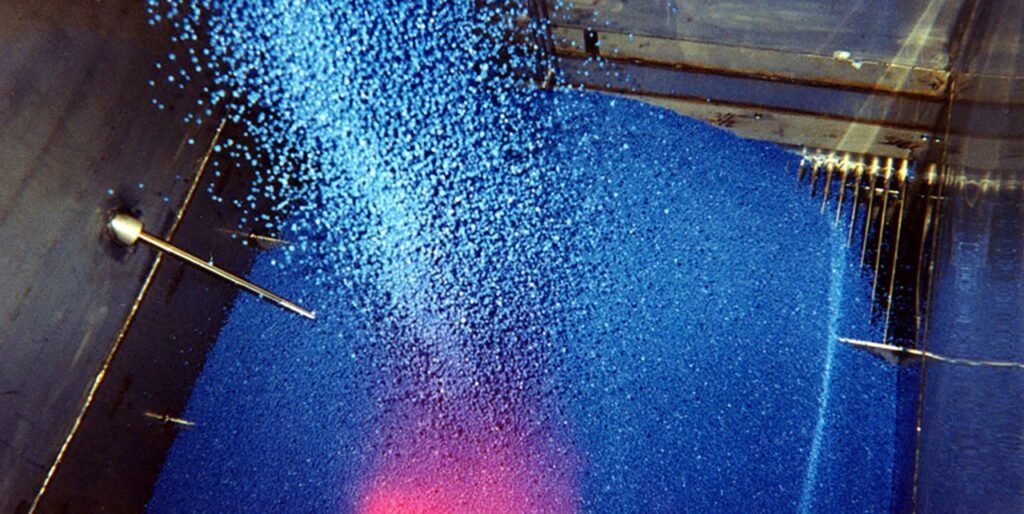
Regular particle shape:
The high tower compound fertilizer adopts the melt granulation process. The molten material is sprayed down from the top of the high tower and naturally cooled into particles during the falling process. This process makes the fertilizer particles almost perfect spherical, with uniform particle size and smooth surface. In contrast, the fertilizer particles produced by other processes such as disc granulation and drum granulation are irregular in shape and have high surface roughness.
Concentrated particle size distribution:
In the production process of high tower compound fertilizer, the particle size of fertilizer particles can be precisely controlled by accurately controlling the process parameters such as nozzle aperture, spray pressure, and cooling wind speed, so that the particle size distribution of the product is relatively concentrated. For example, the particle size of most particles may be concentrated between 2 and 4 mm, which is conducive to meeting the requirements of fertilizer particle size for different crops and different fertilization methods. It is relatively difficult for fertilizers produced by other processes to achieve such high precision in particle size control, and the particle size distribution range may be wide.
High strength:
The internal structure of high tower compound fertilizer particles is dense and has high mechanical strength. This is because during the melt granulation process, the materials are fully melted and mixed at high temperature, and a relatively strong crystal structure is formed after cooling. The higher particle strength makes the fertilizer not easy to break and pulverize during storage, transportation and application, and can maintain good particle integrity and reduce nutrient loss. In contrast, some fertilizer particles produced by simple mixing or low-temperature granulation process have low strength and are prone to breakage.
Good fluidity:
Due to the regular shape, smooth surface and concentrated particle size distribution of high-tower compound fertilizer particles, the friction between particles is small, thus having good fluidity. During the fertilization process, it can pass through fertilization equipment such as seeders and fertilizer spreaders more smoothly to ensure the uniformity and accuracy of fertilization. Fertilizers produced by other processes may have poor fluidity due to irregular particle shape or high surface viscosity, affecting the fertilization effect.
Good slow-release performance:
The production process of high-tower compound fertilizer can form a relatively dense coating on the surface of the particles. This coating can slow down the release rate of fertilizer nutrients to a certain extent and achieve a slow-release effect of nutrients. Compared with some common compound fertilizers, it can prolong the effective period of fertilizer, reduce the number of fertilization times, and improve fertilizer utilization rate. It also helps to reduce the pollution to the environment caused by nutrient loss.
Environmental and Economic Benefits
Energy Efficiency in Production
The high-tower compound fertilizer production process integrates multiple processes such as granulation, drying, and cooling in one high-tower equipment, reducing the transmission of materials between different equipment and the energy loss in the intermediate links. Compared with the traditional compound fertilizer production process, it can save 30% of energy consumption.
Lower Emissions and Environmental Impact
- Dust emission control: In the production process of high-tower compound fertilizer, advanced tail gas treatment systems, such as cyclone dust collectors, bag dust collectors and other multi-stage dust removal equipment, are used to efficiently collect and treat the dust generated during the production process. The dust emission concentration can be controlled below 30mg/m³, which is far below the national environmental protection emission standards, effectively reducing the dust pollution to the atmospheric environment.
- Wastewater recycling: Cooling water and process wastewater in the production process can be recycled after treatment. By building sewage treatment facilities, the wastewater is precipitated, filtered, purified and other treatments, so that the reuse rate of wastewater reaches more than 90%, reducing the waste of water resources and the pollution of wastewater discharge to the environment.
- Reduction of greenhouse gas emissions: In the production process of high-tower compound fertilizer, due to the improvement of energy efficiency, the consumption of fossil fuels is reduced, thereby indirectly reducing the emission of greenhouse gases such as carbon dioxide. At the same time, some companies also use advanced denitrification technology to treat nitrogen oxides generated in the production process, further reducing the emission of greenhouse gases and atmospheric pollutants.
Cost-Effectiveness and Scalability
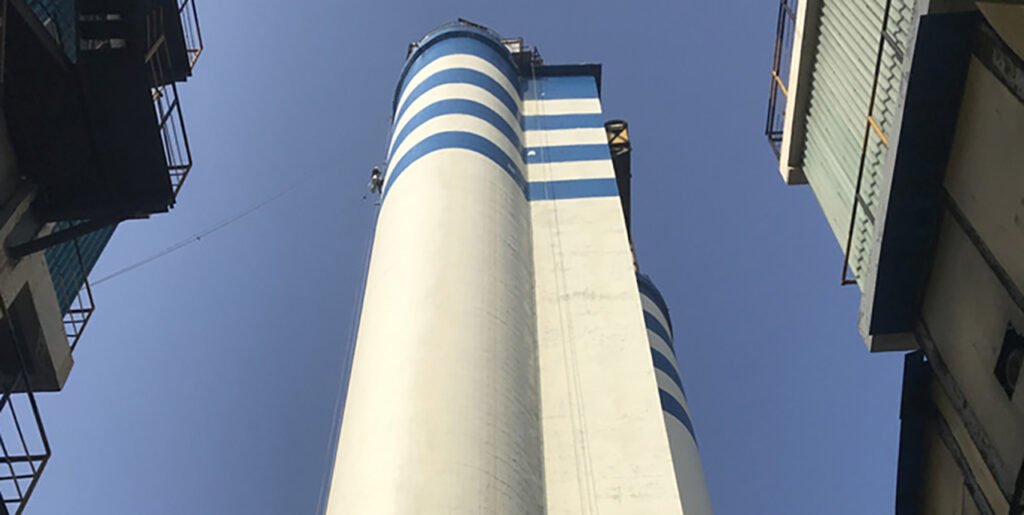
Economies of scale:
The high-tower compound fertilizer production unit has a large production scale, and the production capacity of a single unit can generally reach 100,000-500,000 tons/year. As the production scale expands, the production cost per unit product gradually decreases. For example, in terms of raw material procurement, large-scale procurement can obtain more favorable prices; in terms of equipment investment, the equipment investment cost per unit capacity decreases with the increase in scale, thereby improving cost-effectiveness.
Stable product quality:
The high-tower compound fertilizer production process can produce high-quality compound fertilizer products with uniform particles, stable nutrient content and good water solubility by accurately controlling the material ratio, temperature, humidity and other parameters. The stability of product quality helps to improve the market competitiveness of the product, reduce the after-sales cost and market loss caused by product quality problems, and has good cost-effectiveness in the long run.
Strong scalability:
The high-tower compound fertilizer production unit is usually designed with a certain degree of scalability in mind. Enterprises can relatively easily achieve capacity increases by increasing the height of the tower, expanding the production scale, optimizing the production process, etc. according to the growth of market demand. Moreover, during the expansion process, due to the foundation and experience accumulation of the original production equipment, the technical risks and costs of expansion can be reduced, and it has strong scalability.
Applications and Case Studies

Global Adoption of High Tower Granulation Technology
- Asia: As a gathering place for major agricultural countries, Asia has a huge demand for fertilizers. China is a major country in the application of high-tower compound fertilizer production technology. As of 2023, the production capacity of high-tower compound fertilizer accounts for about 30% of the total domestic compound fertilizer production capacity. China has a vast territory, and the soil conditions and crop types in different regions vary greatly. The high-tower process can produce a variety of formula compound fertilizers to meet the needs of various regions. For example, the northern corn-producing areas have a large demand for high-nitrogen compound fertilizers, while the southern fruit-growing areas rely on products with high potassium sulfate content.
- According to market data, the global high-tower granulated NPK compound fertilizer market size will reach US$6.675 billion in 2023, and is expected to grow to US$9.33743 billion by 2032, with an annual compound growth rate of 3.80%. Many international fertilizer giants, such as Yara, Nutrien, Eurochem, etc., have deployed high-tower compound fertilizer production, reflecting the global market's favor for this technology product.
Case Study: Successful Implementation in Henan, Anyang
- Anyang Zhongsheng Fertilizer Technology Co., Ltd. is located in the Neihuang County Venous Industrial Park, Anyang City, Henan Province. As a large agricultural and vegetable county, Neihuang County has a huge use of compound fertilizers, which undoubtedly opens up a broad market space for the development of Zhongsheng Fertilizer Industry and becomes an important opportunity for it to invest in the construction of high-tower fertilizer production lines.
- AYZS Zhongsheng Fertilizer Industry's high-tower fertilizer production line construction project was awarded the key construction project of Anyang City. It is quite large in scale and covers a total area of 152 acres. Before deciding to build a high-tower fertilizer production line, the company conducted a lot of market research and technical evaluation. At that time, the homogeneity of compound fertilizer products on the market was serious. Zhongsheng Fertilizer Industry was keenly aware that if it wanted to stand out in the fierce market competition, it was urgent to improve product quality and production efficiency. The compound fertilizer produced by high-tower granulation technology has the advantages of uniform particles, balanced nutrients, and good water solubility, which can greatly meet the market's demand for high-quality fertilizers, so the company decisively decided to introduce this advanced technology.
- It is worth mentioning that the project was contracted and constructed by Tongli Heavy Machinery EPC. With its rich industry experience and excellent technical strength, Tongli Heavy Machinery is fully responsible for the design, procurement, construction and other aspects of the project. The total investment of the first phase of the project is 31,469,773USD, and the construction content includes a series of key equipment and facilities. Tongli Heavy Machinery carefully planned and installed a natural gas boiler to continuously provide stable heat energy support for the production process, effectively ensuring the smooth progress of material melting and other links. The installation of the elevator was also done by Tongli Heavy Machinery, which accurately transported the raw materials to various heights of the tower to ensure the continuity of the production process. As the core facility, the tower has a height and diameter that has been carefully designed by the professional team of Tongli Heavy Machinery to perfectly meet the space and process requirements required for tower granulation. The materials complete the key steps of granulation in the tower in an orderly manner. The screening machine provided by Tongli Heavy Machinery efficiently screens and grades the fertilizer after granulation, separates the particles that do not meet the specifications for reprocessing, and ensures that the finished particles are uniform in size. The coating machine was also introduced and installed by Tongli Heavy Machinery. It wraps a protective film for qualified fertilizer particles, which not only improves the appearance quality of the particles, making them more round and shiny, but also effectively prevents the fertilizer from absorbing moisture and agglomerating, extending the shelf life.
- During the project construction process, difficulties came one after another. On the technical level, the high-tower granulation technology has extremely strict control over process parameters. Any deviation in any parameter such as temperature, pressure, and material flow rate may affect product quality. The technical team of Tongli Heavy Machinery worked closely with the technical staff of Zhongsheng Fertilizer Industry, and maintained high-frequency communication with the equipment supplier. After countless debugging and optimization, it finally achieved precise control of various parameters. At the same time, financial pressure also followed during the construction process. In order to ensure the smooth progress of the project, the Neihuang County Government actively coordinated and not only set up a project service team to provide "nanny-style" services for project construction, but also simplified the approval process and implemented a tolerance process for qualified key projects to ensure the smooth start of the project. In addition, the government actively resolved the financing difficulties of enterprises and provided a large amount of financial support for Zhongsheng Fertilizer's high-tower fertilizer production line project, alleviating the company's financial pressure.
- After more than a year of hard work, Zhongsheng Fertilizer's high-tower fertilizer production line was successfully put into production and achieved results in the first half of this year. After the production, the high-tower production line showed strong production capacity, with a daily output of up to 1,500 tons. Later, the company completed and put into production the drum line in October 2023, and the two packaging lines were running at the same time, with daily output increasing to more than 2,300 tons. With its excellent quality, the products are sold well in Guangdong, Guangxi, Hebei, Shandong and other provinces and cities across the country.
- Today, Zhongsheng Fertilizer has emerged in the field of high-tower fertilizer production, but the company has not stopped its pace. At present, it has actively planned the construction of the second phase of the project, and plans to further improve and build the compound fertilizer industry chain, moving towards a comprehensive compound fertilizer production enterprise integrating R&D, production and sales, and continuing to contribute to the development of agricultural industrialization and rural revitalization.
Challenges and Considerations
What are the technical Challenges in High Tower Construction 2025?
High tower structure design and stability:
- Mechanical considerations: The tower height of the high tower compound fertilizer production line is usually between 30-120 meters. Such a tall building structure needs to withstand a variety of complex external forces. On the one hand, to resist the horizontal thrust generated by strong winds, the design wind speed values vary according to the meteorological conditions in different regions. For example, coastal areas may face typhoons, and the design wind speed must reach 50-60 meters/second or even higher, which requires the high tower structure to have sufficient lateral stiffness in the horizontal direction. On the other hand, seismic force is also a key factor. In areas where earthquakes occur frequently, seismic design must be carried out according to the local seismic fortification intensity to ensure that the tower does not collapse under the action of an earthquake. For example, in areas with a 7-degree seismic fortification, the ductility and energy dissipation capacity of the tower must be ensured through reasonable structural layout and component selection.
- Foundation design: The foundation of the tower bears the weight of the entire tower body and internal equipment and materials, and its importance is self-evident. Due to the high center of gravity and large load of the tower, the foundation design requires accurate calculation of the foundation bearing capacity. For soft soil foundations, pile foundations are often used to transfer the load to the deep solid soil layer through piles. There are various types of piles, such as concrete cast-in-place piles, precast piles, etc., which need to be selected comprehensively based on geological conditions, construction conditions and other factors. The pile length, pile diameter and pile arrangement must be calculated in detail to ensure the stability and uniform settlement of the foundation.
Material conveying and distribution system
- Vertical conveying: It is a big challenge to convey a large amount of raw materials to the top of the tower. The commonly used bucket elevator must ensure that the conveying volume meets the production needs during the conveying process, while avoiding the spilling and clogging of materials. Taking a high-tower compound fertilizer production line with a daily output of 1,000 tons as an example, the conveying volume of the bucket elevator may need to reach 50-80 tons per hour. The chain, hopper and other components of the elevator must have high strength and wear resistance to prevent damage during frequent operation. In addition, the power of the driving motor of the elevator must be reasonably matched to ensure smooth operation when starting at full load to avoid overload tripping and other situations.
- Tower top distribution: After the material reaches the top of the tower, it must be evenly distributed to each granulation nozzle or reaction area. The distribution system must have high precision to ensure that the discharge of each nozzle is uniform, otherwise it will cause the compound fertilizer particles to be of different sizes and unstable quality. Common distribution methods include rotary distributors, tubular distributors, etc. The rotary distributor is driven by a motor to rotate and throw the material to the surrounding area, but the rotation speed and throwing angle must be precisely controlled. The tubular distributor relies on pipeline layout and valve adjustment to achieve material distribution, and has extremely high requirements on pipeline processing accuracy and valve sealing.
Granulation and reaction process control
- Temperature control: In the production of high-tower compound fertilizers, the granulation process is often accompanied by chemical reactions, and the temperature control requirements are extremely strict. For example, when urea reacts with monoammonium phosphate to produce urea-based compound fertilizers, the reaction temperature needs to be controlled between 130-150°C. Too high a temperature may cause material decomposition and product quality to decline, while too low a temperature will result in incomplete reaction. In a high tower, the temperature at different locations is affected by multiple factors such as material flow and ventilation conditions. It is necessary to install multiple temperature sensors to monitor temperature changes in real time and accurately control the temperature by adjusting the heating or cooling device. Cooling devices such as the air volume of the air cooler and the flow of the cooling water pipeline must be adjusted in time according to temperature feedback.
- Pressure control: In some high-tower reaction processes, pressure is also a key parameter. For example, during the high-tower ammonium nitrate granulation process, the pressure in the reaction tower needs to be maintained within a certain range to ensure the atomization effect and granulation quality of the ammonium nitrate solution. Too high a pressure may cause equipment leakage and increase safety risks, while too low a pressure will affect the granulation efficiency. The pressure control system needs to be equipped with high-precision pressure sensors and regulating valves. When the pressure exceeds the set range, the regulating valve will automatically operate to adjust the pressure inside the tower. At the same time, it is necessary to ensure that the system has good sealing properties to prevent pressure leakage.
Environmental protection and energy-saving and emission reduction technology
- Dust treatment: A large amount of dust will be generated during the production of high-tower compound fertilizers. If not properly handled, it will not only pollute the environment, but also cause material waste. Commonly used dust removal equipment includes cyclone dust collectors, bag dust collectors, and electrostatic dust collectors. Cyclone dust collectors use centrifugal force to separate large particles of dust, but the removal efficiency of fine dust is limited. Bag dust collectors capture fine dust through filter media, and the filtration efficiency can reach more than 99%, but the bags need to be cleaned or replaced regularly to prevent the bags from clogging and affecting the dust removal effect. Electrostatic dust collectors use high-voltage electric fields to charge dust and adsorb it to the dust collecting electrode. They are suitable for handling large air volumes and high-concentration dust, but the equipment investment is large and the maintenance requirements are high.
- Waste heat recovery: A large amount of waste heat will be generated during the production of high-towers, such as the heat carried by high-temperature particles after granulation and the heat in the exhaust gas. Realizing waste heat recovery can not only save energy and reduce emissions, but also reduce production costs. A heat exchanger can be used to transfer waste heat to cold air or cold water entering the system for preheating raw materials or producing hot water. For example, by using a heat exchanger to recover the heat from the pelletizing cooling exhaust, the cold air can be preheated to 80-100°C for drying raw materials or other processes, effectively reducing energy consumption. However, the design of the waste heat recovery system needs to consider multiple factors such as heat exchange efficiency, equipment investment and operating costs to achieve a balance between economic and environmental benefits.
Maintenance and Operational Considerations
How to maintain the high tower fertilizer line?

Granulation nozzle:
Granulation nozzle determines the shape and quality of fertilizer particles. After each shift, clean the residual material on the nozzle surface to prevent the material from drying and clogging the nozzle. Check the wear of the nozzle regularly. The wear of the nozzle will change the material spraying speed and angle, resulting in uneven particle size. Once the wear of the nozzle exceeds the tolerance range, the nozzle needs to be replaced in time to ensure the stability of the granulation effect.
Conveying equipment:
For conveying equipment such as belt conveyors and bucket elevators, check whether the belt is torn or deviated, and adjust the belt tension in time. If the bucket of the bucket elevator is deformed or detached, it will not only affect the conveying efficiency, but also may cause equipment failure. The hopper connection needs to be tightened regularly. At the same time, pay attention to the drive motor and reducer of the conveying equipment, check its temperature, noise and vibration, and replace the lubricating oil according to the prescribed period to ensure the smooth operation of the equipment.
Equipment lubrication system:
There are many lubrication points of each equipment on the production line. The lubrication system should be fully checked every certain production cycle (such as 3-6 months). Clean the lubrication pipeline to prevent impurities from clogging and ensure that the lubricating oil can reach each lubrication part smoothly. According to the equipment operation status and seasonal changes, choose the lubricant grade reasonably, such as high viscosity lubricant in summer high temperature, low viscosity and good fluidity lubricant in winter low temperature, to extend the service life of the equipment.
Electrical control system:
The electrical control system is related to the automated operation of the production line. Arrange professional electricians to conduct a comprehensive inspection of the electrical cabinet every quarter, clean the internal dust, and prevent short circuit failures caused by dust accumulation. Check whether the wiring of electrical components is loose, and replace aging and damaged electrical components in time. Regularly calibrate various sensors, such as temperature sensors, pressure sensors, etc., to ensure that the data obtained by the control system is accurate and to ensure that the equipment operates stably according to the set parameters.
Reactor:
Open the reactor for internal inspection at regular intervals, clean the scale and material accumulation on the reactor wall and the stirring paddle. Check the wear of the stirring paddle, and replace it in time if it is severely worn. Check and maintain the sealing device of the reactor to ensure that it is well sealed to prevent material leakage.
Operational considerations to prolong the life time of a high tower prilling urea line
- Temperature control: Many links in the production process have strict temperature requirements. For example, in the material melting stage, the temperature needs to be precisely controlled within a certain range. If the temperature is too low, the material cannot be fully melted, affecting the granulation effect; if the temperature is too high, the material may decompose and deteriorate. By installing high-precision temperature sensors, real-time monitoring of temperature changes and feeding back data to the control system, the power of the heating equipment is automatically adjusted to ensure temperature stability. The suitable production temperature of compound fertilizers with different formulas is slightly different, and operators need to flexibly adjust according to actual conditions.
- Material flow and ratio: Ensuring the stable flow of each raw material and accurate ratio is the key to producing qualified products. Use feeding equipment with high metering accuracy, such as loss-in-weight feeders, to accurately control the amount of material added. Regularly calibrate the metering device of the feeding equipment to prevent material ratio imbalance due to equipment errors. According to the production plan and product formula, timely adjust the flow of each raw material to ensure that the fertilizer nutrient content meets the standard under different production requirements.
- Granulation speed and air volume: The speed of the granulator determines the size and shape of the fertilizer particles. If the speed is too fast, the particle size will be small; if the speed is too slow, the particle size will be large and easy to stick together. Combined with the material characteristics and product requirements, the granulator speed should be reasonably set, and fine-tuned according to the actual situation of the particles during the production process. At the same time, control the air volume during the drying and cooling stages. Too much air volume may cause the moisture on the particle surface to evaporate too quickly and cracks to appear; too little air volume will result in insufficient drying and cooling. By adjusting the fan frequency, the air volume can be accurately controlled to ensure product quality.
Market Dynamics and Economic Viability
Assessing the investment and return in adopting high tower technology.
Initial investment:
Assuming that the price of investing in a high-tower line is 30 million US dollars, this includes the purchase and installation costs of key equipment such as the main equipment of the high tower, granulation nozzles, conveying equipment, electrical control systems, and waste heat recovery systems. In addition, it also includes the costs of land acquisition, plant construction, early technical research and development, and personnel training. As a core asset, the main equipment of the high tower accounts for a large proportion of the price, about 10-15 million US dollars, depending on the height, diameter, and material requirements of the tower. The purchase and commissioning costs of precision equipment such as granulation nozzles are about 3-5 million US dollars. The quality of these equipment directly affects product quality and production efficiency.
Operating costs:
Raw material costs account for the largest proportion of operating costs, mainly including the purchase costs of basic raw materials such as urea, monoammonium phosphate, and potassium chloride. With market fluctuations, raw material prices vary greatly, which has a significant impact on production costs. Energy costs are also an important component, used for material melting, drying, equipment operation, etc., such as natural gas and electricity consumption. Taking a medium-sized high-tower compound fertilizer production line as an example, the annual energy cost may be around 5-8 million US dollars. The labor cost involves the salaries of personnel in various positions such as production, management, and technical maintenance. It varies according to the regional labor market situation. Generally, the annual labor cost is between 3-5 million US dollars. In addition, there are equipment maintenance and depreciation costs, regular equipment maintenance and depreciation due to use, which is about 2-3 million US dollars per year to ensure the long-term stable operation of the equipment and maintain production capacity.
Product sales revenue:
Based on the current market price, the price of ordinary high-tower compound fertilizer is between 300 and 500 US dollars per ton, and the price of high-end and special formula products can reach 600 to 800 US dollars per ton. Assuming that the annual production capacity of a high-tower production line is 200,000 to 300,000 tons (the specific capacity depends on the scale of the production line and the operating efficiency), if the average selling price is 400 US dollars per ton, the annual sales can reach 40 million to 80 million US dollars. With the expansion of market share, the improvement of brand awareness and the optimization of product structure, the sales price is expected to increase further, thereby increasing sales revenue.
By-product and comprehensive utilization revenue:
In the production process of high-tower compound fertilizer, some by-products with certain value may be produced to create additional revenue. Some companies carry out comprehensive treatment and utilization of waste gas and waste residue in the production process, such as recovering valuable chemicals from waste gas and processing waste residue into building materials, which not only reduces environmental pollution but also increases the source of revenue for enterprises. Although this part of revenue is relatively small compared to the product sales revenue, it is considerable when accumulated over the long term, and can increase revenue by US$500,000 each year.
Payback period:
Based on the above cost-benefit analysis, the payback period can be estimated in the following way. Assuming that the annual net profit (annual sales - annual operating costs - equipment depreciation, etc.) is 10-20 million US dollars (this value will fluctuate according to the actual operating conditions) and the initial investment is 30 million US dollars, the payback period is approximately between 1.5 and 3 years. In actual operation, if costs can be effectively controlled, such as reducing raw material costs by optimizing procurement channels, improving energy efficiency and reducing energy consumption, or increasing product prices, such as launching high value-added products and strengthening brand building, the payback period is expected to be further shortened.
People also ask: Frequently asked question about high tower fertilizer production line.
The high-tower fertilizer granulation production line has significant advantages. It can simplify the process, directly use urea or ammonium nitrate melt, skip the urea melt spray granulation and solid urea packaging, transportation, crushing and other links. It has excellent performance in energy consumption. With the help of the heat energy of the molten raw materials, the material moisture is low, no drying is required, and energy consumption is greatly reduced. The product quality is high, the particles are uniform and smooth, strong in pressure resistance, not easy to agglomerate, each particle has consistent nutrients, the effectiveness of trace elements is improved after chelation, the fertilizer effect is long and the utilization rate is high, and it also has unique pinholes for anti-counterfeiting. The production efficiency is high, the proportion of qualified product particles is high, and the return material is very small. Moreover, the production line belongs to the clean production process, no three wastes are discharged, and the operating environment is good; the formula is flexible, and a variety of formula compound fertilizers can be produced according to market demand.
The raw materials commonly used in high-tower fertilizer granulation are rich and varied. Urea is mostly used as the raw material for nitrogen fertilizer. It is synthesized by ammonia and carbon dioxide under high temperature, high pressure and catalyst, and is an important nitrogen source in high-tower granulation. Monoammonium phosphate is the main raw material for phosphate fertilizer, which provides phosphorus for crop growth. In terms of potash fertilizer, potassium chloride and potassium sulfate are more commonly used, which can enhance the ability of crops to resist lodging. In addition, some additives and auxiliary materials are also used in production, such as conditioners to improve the physicochemical properties of fertilizers, and anti-caking agents to prevent fertilizers from caking during storage. For example, some high-tower compound fertilizer manufacturers in Shandong will use urea, monoammonium phosphate, and potassium chloride as the basis according to the needs of different crops, and then add appropriate amounts of additives to produce special compound fertilizers suitable for crops such as wheat and corn.
In the production of fertilizers, the solid urea and ammonium nitrate (or ammonium nitrate phosphorus, etc.) are first heated and melted, and the melt after evaporation and concentration can also be used directly. Then, phosphate fertilizer, potash fertilizer, filler and additives are added to the melt, and after sufficient stirring and mixing, a mixed slurry with good fluidity is made. Subsequently, the slurry is sent to the high tower granulator and sprayed evenly into the granulation tower through the nozzle. The material falling from the top of the high tower interacts with the cold air rising from the bottom of the tower during the descent process to exchange heat. The cold air quickly takes away the heat and moisture of the droplets, cools and dries them, and turns them into solid particles that settle at the bottom of the tower. Finally, the particles gathered in the aggregate box fall into the belt conveyor and leave the high tower. After screening and surface treatment, granular compound fertilizer is obtained. The whole process can make the fertilizer particles uniform, and the nutrients are fully mixed in the molten liquid, thereby improving the quality of the fertilizer.
The annual production capacity of small-scale high-tower granulation production lines is usually between 100,000 and 200,000 tons. Such production lines occupy relatively less land and equipment investment. The production capacity of medium-sized high-tower granulation production lines is larger, generally between 200,000 and 500,000 tons. Large-scale high-tower granulation production lines have outstanding production capacity, some of which can reach 500,000 to 1 million tons or even higher. Their tower height, equipment configuration and production process have all been optimized and upgraded.
The essential equipment of a high-tower fertilizer granulation plant is first the tower body. As the core, the diameter and height of the granulation tower are directly related to the production capacity and product quality. Its main function is to provide space for crystallization, cooling and heat exchange for compound fertilizer. Secondly, the granulation equipment. The high-tower melt granulator can meet the granulation needs of different slurries and has excellent granulation performance for medium and low nitrogen compound fertilizers. The mixing reactor is also indispensable, which can fully stir the raw materials and prepare mixed slurry with good fluidity. In addition, raw material pretreatment equipment is also required, such as crushers for crushing raw materials, electronic belt scales, spiral batching machines, etc. for accurately measuring the proportion of nitrogen, phosphorus, potassium and trace elements. In the production process, screening equipment (such as vibrating screens) are used to separate qualified and unqualified particles, cooling equipment (such as rotary coolers) quickly cool particles to prevent agglomeration, and packaging equipment (such as fully automatic packaging machines) realize automatic weighing, sealing and coding. In terms of environmental protection equipment, bag dust collectors, cyclone dust collectors, etc. are used to collect dust and reduce pollution. Conveying equipment such as belt conveyors and bucket elevators connect various processes to achieve automatic material transmission.
In the production of NPK fertilizers, high-tower granulation and rotary drum granulation have their own characteristics. High-tower granulation can directly use urea or ammonium nitrate melt, eliminating the process of spraying granulation of urea melt and the subsequent packaging, transportation, and crushing of solid urea, greatly simplifying the production process. It has obvious advantages in energy consumption because it fully utilizes the thermal energy of molten raw materials, has low moisture content in the materials, and does not require drying, which saves a lot of energy compared to rotary drum granulation. In terms of product characteristics, the fertilizer particles produced by high-tower granulation are uniform and smooth, have high compressive strength, are not easy to agglomerate, and each particle has good nutrient consistency, long fertilizer effect and high utilization rate. High-tower granulation can also be controlled by fully automatic computer batching to flexibly produce a variety of compound fertilizers with different formulas; although rotary drum granulation can also adjust the formula, its flexibility is inferior to high-tower granulation, and it is difficult to produce high-concentration products.
From the perspective of energy consumption, the process directly uses urea or ammonium nitrate melt without the need for additional drying of materials, which greatly reduces energy consumption and carbon emissions caused by energy production. For example, the traditional granulation process requires a large amount of heat energy for drying, while high-tower granulation avoids this high-energy consumption link by virtue of its own characteristics. In terms of pollutant emissions, its operating environment is good, and there is no discharge of three wastes throughout the process. It is a clean production process that will not pollute the soil, water and air, and effectively maintains the ecological environment. In terms of resource utilization, the percentage of qualified product particles in high-tower granulation production is high, and the amount of returned materials is almost zero, which improves the utilization rate of raw materials and reduces resource waste. At the same time, the compound fertilizer particles produced by high-tower granulation are uniform, have high compressive strength, and are not easy to agglomerate. They can release nutrients slowly and evenly, improve fertilizer utilization, and reduce the negative impact of excessive fertilizer application on the environment.
From the production process, it directly uses urea or ammonium nitrate melt, eliminating the energy-consuming links of urea melt spray granulation and subsequent solid urea packaging, transportation, crushing, etc. Because the material has low moisture content, no additional drying is required, which greatly reduces energy consumption. Compared with conventional granulation processes, its energy consumption can be saved by more than 50%. For example, the high-tower urea-based compound fertilizer production line of Zhanjiang Ladom Technology Co., Ltd. has been reviewed by the Guangdong Provincial Energy Bureau. The comprehensive energy consumption per unit product of its high-tower compound fertilizer is not higher than 19.84 kg of standard coal/ton. Batan Co., Ltd.'s high-tower granulation production technology, with its own process advantages, has achieved a significant reduction in energy consumption, and has outstanding performance in energy saving compared to traditional processes. In general, the high-tower fertilizer granulation production line effectively reduces energy loss in the production process with its unique process, and is superior to many other types of fertilizer granulation production lines in energy consumption control. It is an energy-saving and efficient production method.
In terms of particle appearance, this technology makes the particles uniform, transparent, bright in color, and with clearly visible pinholes in the middle, which is difficult to achieve with traditional granulation methods. In terms of compressive strength, the moisture content of compound fertilizer particles produced by high-tower granulation can be controlled below 1% or even 0.5%, and the compressive strength is more than doubled that of traditional process products, which is suitable for various fertilization methods. In terms of nutrient uniformity, the molten raw materials are fully mixed during the falling process, so that the nutrients in each particle are basically the same, and the crop growth is more uniform. The high-tower granulation technology can also process trace elements through chelation technology to improve nutrient effectiveness and promote crop absorption. At the same time, the nutrient release of the compound fertilizer particles produced by it is more uniform, the fertilizer effect lasts longer, and the fertilizer utilization rate is improved.
First of all, there is the initial investment, which includes the construction of the main tower, the purchase and installation costs of advanced nozzles and other equipment. The investment scale is large. For example, the total investment of the nitro high-tower compound fertilizer renovation project of Fengxi Compound Fertilizer Company is estimated to be 13.75 million yuan. Secondly, the cost of raw materials. The prices of basic raw materials such as urea, ammonium phosphate, and potash fertilizer fluctuate greatly. For example, the scale of raw material procurement of compound fertilizer company B is about 200,000 tons, and the procurement cost is significantly affected by market conditions. The third is the labor cost, which depends on the scale and complexity of the production line. For example, the production line of the high-tower compound fertilizer device of China Salt Meifu Ecological Fertilizer Industry plans to have two shifts, with no less than 26 people in each shift. In terms of energy consumption costs, material melting and equipment operation require a lot of energy. There are also equipment maintenance and depreciation costs, which require regular maintenance to ensure stable operation, and equipment depreciates as the service life increases. In addition, storage costs such as the storage fee of compound fertilizer company B of 3 yuan/ton/day and loading and unloading of 12 yuan/ton cannot be ignored.
From the perspective of process principle, ordinary granulation covers a variety of methods, such as extrusion granulation, which is to extrude materials into shape through mechanical pressure, and drum granulation, which is to roll and agglomerate materials in a drum; while high-tower granulation is to heat raw materials such as urea, ammonium phosphate, and potash fertilizer to a molten state, spray them from the nozzle at the top of the high tower, and contact with cold air to cool and solidify into granules during the falling process. In terms of product appearance, ordinary granulation products have various shapes, extrusion granulation particles are relatively regular but the surface may not be smooth enough, and drum granulation particles are uneven in size and rough in surface; high-tower granulation particles are almost perfect spherical, with a smooth and round surface, and there are unique small holes on the particles formed by rapid cooling. In terms of product performance, the nutrient uniformity of ordinary granulation products is general, and fertilizers produced by some granulation methods may have nutrient stratification, and the particle strength and anti-caking properties are unstable; the fertilizer particles produced by high-tower granulation have uniform nutrient distribution, high compressive strength, are not easy to agglomerate, and due to rapid cooling, pores are formed inside, water solubility and nutrient release properties are excellent, and the fertilizer effect is long-lasting and efficient. In terms of energy consumption, ordinary granulation such as extrusion granulation requires a lot of mechanical energy, and drum granulation consumes a lot of energy for subsequent drying; high tower granulation utilizes the melting heat of raw materials, the moisture content of the material is low, and no additional drying is required, which significantly reduces energy consumption.
This technology makes the internal structure of fertilizer particles relatively uniform, and can achieve relatively stable and continuous nutrient release in the soil. This is because during the granulation process, the nutrients are fully mixed, and the formed particles have similar physical and chemical properties. Unlike traditional processes, nutrient stratification is prone to occur, so crops can stably obtain nitrogen, phosphorus, potassium and other nutrients at different growth stages, and the fertilizer effect is more lasting. In terms of solubility, fertilizer particles produced by high-tower granulation usually have good water solubility. On the one hand, the material is in a molten state during granulation, the components are fully integrated, and the crystalline structure of the particles is conducive to water penetration. After encountering water, it can quickly disintegrate and accelerate the dissolution of nutrients; on the other hand, the tiny pores that may exist on the surface of the particles increase the contact area with water, further increasing the dissolution rate. For example, Kailin high-tower nitro-sulfur-based compound fertilizer, due to the high-tower granulation process, has a water-soluble phosphorus content of more than 90%, which dissolves quickly and takes effect quickly.
In terms of daily cleaning, dust and dirt on the surface of the equipment should be cleaned up in time after work, especially the feed port, discharge port and other parts that are prone to blockage. The residual materials inside should also be cleaned regularly with compressed air or special tools. Lubrication maintenance cannot be ignored. Regularly check the lubricating oil in bearings, gears and other parts to ensure that they are sufficient and clean. According to the use of the equipment, a reasonable oil change plan should be formulated and the lubricating oil of the appropriate type should be selected. Tightening inspection is also very important. It is necessary to regularly check whether the bolts and nuts at the various connection parts of the equipment are loose and tighten them in time; at the same time, check the transmission parts, such as the tension of belts and chains, to avoid problems such as slipping and breaking. Electrical system maintenance is also critical. Regularly check the motors, controllers, sensors and other components to check whether the wires and cables are firmly connected, whether they are damaged or aged, keep the electrical system clean, and prevent dust and moisture from entering. In addition, according to the use of the equipment and the manufacturer's recommendations, the equipment should be regularly overhauled and severely worn parts should be replaced in time.
From the initial investment point of view, the high tower granulation plant needs to build a high tower and be equipped with large equipment such as special granulation nozzles, so the initial investment is relatively large, usually 30 million US dollars or even higher. Among them, the cost of high tower construction, core equipment procurement and installation accounts for a large proportion. In contrast, the equipment investment of the extrusion granulation production line is relatively small, and the main equipment is extruders, etc. The overall investment may be around 1 million to 5 million US dollars. The investment in the rotary drum granulation production line is also relatively low, mainly rotary drum equipment and supporting facilities, and the construction cost is about 2 million to 6 million US dollars.
. In terms of space, a larger site is required, not only to accommodate the high tower, but also to reserve space for raw material storage areas, production workshops, finished product warehouses, office areas, etc. Taking a project with a designed annual output of 60,000 tons as an example, the high tower granulation workshop has a construction area of 2,400 square meters, equipped with a 100-meter high tower and a variety of systems. If large-scale production is planned, the land area may exceed 100 acres. For example, in a project in Zhejiang, a 200,000-ton/year high tower granulation production line and its workshop and other facilities are equipped with a 19-meter × 128-meter high tower structure, with a total construction scale of 220 acres.
In terms of infrastructure, the high tower is the core, and its height is mostly 80-120 meters. For example, the high tower upgraded by Lu Tianhua has an inner diameter of 24 meters and a total height of about 120 meters, which requires a stable foundation to bear. Equipment such as mixing reactors should be equipped to fully mix the materials. A complete water and electricity supply system is also required to meet the needs of equipment operation and material handling, and good ventilation and temperature control facilities are required to ensure a suitable production environment. At the same time, due to the involvement of chemical raw materials and production processes, environmental protection facilities are indispensable, such as waste gas treatment and wastewater purification devices.
During the high-tower granulation process, after the molten material is ejected from the nozzle at the top of the high tower, it falls, cools and solidifies. Due to its own surface tension and uniform cooling, the formed particles are approximately spherical and have a smooth and round surface. According to Baidu Encyclopedia, this not only improves the appearance quality of the product, but also reduces the contact points between particles, reducing the risk of agglomeration during storage and transportation. In terms of particle strength, due to the rapid cooling of the material in the high tower, the internal structure is tight, and the compressive strength of the particles is greatly improved, which can be more than doubled compared with the products produced by traditional processes. As shown in the information of high-tower granulated compound fertilizer, this makes the fertilizer not easy to break during transportation and fertilization, ensuring the integrity of nutrients. In terms of particle size uniformity, by precisely controlling the nozzle parameters and production process, the ejected molten droplets can be made of similar size, thereby forming fertilizer particles of uniform particle size, ensuring that the nutrients of each fertilizer particle are consistent, which is conducive to the balanced absorption of nutrients by crops. In addition, the high-tower granulation process can effectively control the moisture content of the fertilizer particles, generally controlling the moisture content below 1%. The low moisture content reduces the agglomeration and pulverization of the fertilizer due to moisture absorption.
Regularly check the integrity of the tower structure to prevent collapse caused by structural damage due to material impact, corrosion, etc. Check key components such as granulation nozzles and conveying pipelines for wear and blockage to avoid affecting production or causing material leakage. High-temperature molten materials can easily scald operators, so employees must be equipped with professional heat-insulating clothing, protective gloves and other equipment, and strictly require them to dress according to regulations. In the workshop, good ventilation must be ensured, and harmful gases such as ammonia that may be produced must be discharged in time to reduce the risk of poisoning. Hazardous gas warning signs should also be posted in prominent locations. The electrical system is related to production safety. Professional electricians should be arranged to regularly check for hidden dangers of line aging and short circuits. The grounding of motors and other equipment must be good to prevent leakage accidents. At the same time, formulate rigorous operating procedures and strengthen employee training. It is strictly forbidden to operate in violation of regulations, such as putting materials into the equipment without preheating it, and performing equipment maintenance without shutting down the machine.
In terms of equipment and process design, high-efficiency granulation nozzles are selected to accurately control the particle size and distribution of the melt spray, so that the material can more efficiently exchange heat with the cold air during the falling cooling process, reducing cooling time and energy consumption. Optimize the thermal insulation design of the high tower to reduce heat loss, such as using new insulation materials to wrap the tower body. In the energy utilization link, recycle waste heat and use the waste heat of high-temperature exhaust gas generated during the granulation process to generate electricity or preheat raw materials. For example, a heat exchanger is set up to transfer the heat of the exhaust gas to the raw materials to be melted, reducing the energy consumption required to heat the raw materials. During operation, stabilize the production load and avoid frequent start and stop of equipment, as the energy consumption is high during the equipment startup phase. Reasonably regulate production parameters, such as accurately controlling the melt temperature, cold air flow and temperature, to ensure that the granulation process is carried out under optimal conditions and improve energy utilization efficiency. In terms of raw material processing, pre-treat the raw materials to ensure that their particle size, humidity, etc. are uniform and stable, which is conducive to subsequent efficient granulation.
If the material temperature out of the tower is too high, it cannot be fully cooled and solidified, and it is easy to adhere to the bottom of the tower. It is also easy to be ground into powder during subsequent cooling, which is not conducive to screening; if the temperature is too low, the product is easy to absorb moisture in high humidity seasons. The solution is to accurately determine the tower height and tower diameter by calculation or reference charts based on local climatic conditions, and equip with a precise temperature control system to monitor and control the material temperature in real time. Sticking to the wall and particle agglomeration are also common problems, which will affect the particle quality and equipment operation. By optimizing the nozzle design, the material can be sprayed evenly and local material aggregation can be reduced; regular cleaning of the tower wall can alleviate the sticking phenomenon. In addition, dust pollution is more prominent. Dust will be generated in the spraying of molten materials and particle cooling, which will not only pollute the environment, but also cause material loss. Installing efficient dust removal equipment, such as bag dust collectors, cyclone dust collectors, etc., and strengthening workshop ventilation can effectively reduce dust concentration. Fluctuations in raw material quality will also interfere with granulation. Differences in the composition and particle size of raw materials in different batches may lead to unstable product quality. Therefore, it is necessary to strengthen raw material inspection, strictly control the procurement source, and conduct detailed inspections on each batch of raw materials to ensure that they meet production standards.
Conclusion: High tower fertilizer plant it is the Future!
The global population continues to grow, and the demand for food continues to rise, which has prompted agricultural production to pursue higher yields and quality. High-tower compound fertilizers are favored by farmers because of their uniform particles, balanced nutrients, and good water solubility, which can significantly improve crop yields and quality. In densely populated areas such as Asia and Africa where agriculture is developing rapidly, the demand for high-tower compound fertilizers is particularly strong. At the same time, international giants such as Yara and Nutrien not only continue to expand the production scale of high-tower compound fertilizers, but also continue to invest in research and development resources to launch new formulas and high-end products. Therefore, as a representative of new fertilizer production technology, high-tower compound fertilizers will usher in a blowout development in the next 10 years.