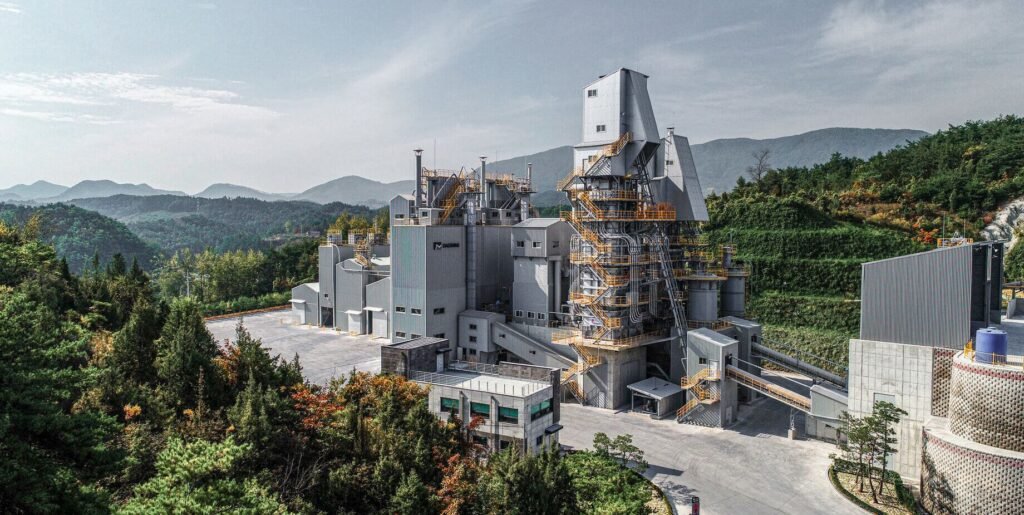
The double vertical lime kiln, double chamber heat storage vertical kiln, commonly known as the Maerz kiln, is an efficient, reliable and environmentally friendly lime production equipment. Compared with other lime kilns, it has the lowest heat consumption, high activity of burned lime and low residual carbon dioxide. It is widely used in steel, chemical, building materials and other industries. This working principle is called the parallel flow heat storage principle. It uses the two kiln chambers to alternately calcine and store heat to achieve heat transfer and storage between the two kiln chambers, ensuring the continuity and stability of lime production. This kiln is an innovative equipment that uses the latest technology. Each lime kiln is designed to optimize the entire process of converting calcium carbonate into calcium oxide without affecting the quality. This machine consists of several components, each of which plays an important role in the entire process. In addition, the product is optimized to reduce pollution to the ecological environment, which is a focus of many industries. The equipment is designed to reduce the emission of substances harmful to the air and ensure the protection of the environment
Maerz kiln process flow
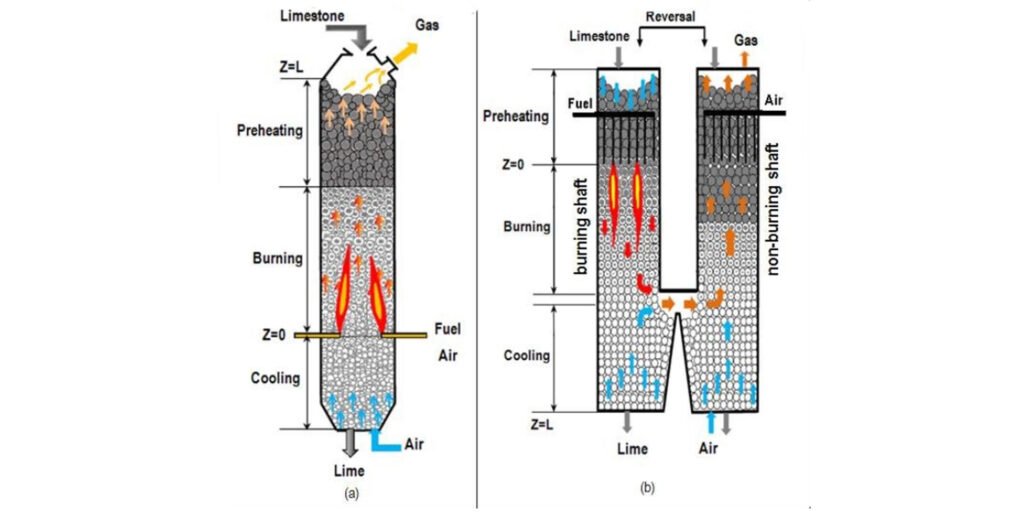
Raw material preparation: Raw materials are sent to the silo in front of the kiln to ensure uniformity and stability of raw materials.
Raw materials entering the kiln: The two chambers are alternately loaded with ore, and the fuel is sent in from the upper part of the two kilns.
Calcination process: In the calcination chamber, the fuel is evenly distributed on each section of the kiln body through multiple spray guns located at the bottom of the preheater. The hot gas flows in the same direction as the raw materials, transferring heat to the raw materials for heating and calcining.
Heat storage: The raw materials store the heat from the calcination chamber in the heat storage chamber to prepare for the next calcination.
Reversing process: Every once in a while (10-15 minutes), the calcination chamber and the heat storage chamber are reversed. During the reversing process, the circulation channel will cut off the connection with the calcination chamber and open the connection with the heat storage chamber, so that the heat can be smoothly transferred from the calcination chamber to the heat storage chamber.
Discharging process: After various calcinations and heat storage, the raw materials are finally sent to the calcination chamber for subsequent processes.
Process characteristics
- Parallel calcination: This is the technical feature of the double-chamber vertical kiln. Since the high-temperature flame contacts the lower-temperature material, the heat exchange rate is very high, and the relatively low-temperature hot gas contacts the material to burn, avoiding over-burning and under-burning, making the roasting product better quality and more active, which can reach more than 360ml, and the residual CO2 is less, generally not higher than 2.5%;
- High heat utilization rate: Due to the use of a heat storage and heat exchange system, the high-temperature exhaust gas is discharged through the preheating kiln, and after a long period of heat exchange, the heat is transferred to the material, making full use of the waste heat and achieving the purpose of energy saving. The unit product heat consumption can reach 850kcal/kg, which is relatively low among all existing kiln types;
- Low exhaust gas temperature and dust content: Due to the sufficient heat exchange between the exhaust gas and the material, the exhaust gas temperature is very low. Under normal circumstances, the exhaust gas temperature is 90-130℃, and the dust concentration in the exhaust gas is generally 5-8g/m³. It is easy to take exhaust gas purification measures, which is conducive to reducing environmental pollution;
- Uniform heat supply: 2×33 burners are evenly distributed in the kiln, and each burner provides heat to the same range of the kiln space, so that the heat supply on the kiln section is uniform, which is conducive to uniform and stable roasting of products;
- Convenient quality inspection: There are 2×8 quality inspection doors under the kiln, which can adjust the fuel supply of the corresponding burner by checking the quality of the products in each part to ensure quality;
Advantages of double vertical lime kiln
Parallel calcination | Low dust content | High heat utilization rate |
The double-chamber lime kiln adopts a double-chamber structure, with the upper chamber being the limestone heating zone and the lower chamber being the limestone calcining zone. The limestone enters the heating zone through the upper chamber and gradually heats up under the action of high temperature to reach the decomposition temperature. During the decomposition process, the carbon dioxide produced by the decomposition of the limestone is sprayed into the fuel for complete combustion, and the residual carbon dioxide is relatively small, generally not higher than 2.5%. | Shuangli lime kiln flue gas treatment is easy, because the flue gas volume is small, the combustion is complete, the pollutants are relatively few, easy to treat, and the degree of purification is pure. | Due to the long simultaneous calcination process, the excellent quality of lime, and the alternating operation of the two chambers, the exhaust gas preheats the ore and the heat is fully utilized, so the unit heat consumption is the lowest among all kiln types, thus achieving the purpose of energy saving. |
Difference from ordinary lime kiln
Comparison Item | Conventional Lime Kiln | Twin-Shaft Lime Kiln |
Single Kiln Daily Capacity | 100–2000 tons/day | 50–1000 tons/day |
Fuel Type | Solid, Liquid, Gas | Solid, Liquid, Gas |
Air Pressure Requirement | ~17 kPa | ~50 kPa |
Minimum Raw Material Size | 30 mm | 15 mm |
Granularity Ratio | 1:2 | 1:2 |
Calcination Principle | Partial co-current, partial counter-current | Full co-current calcination |
Lime Reactivity | ≥350 ml | ≥350 ml |
Combustion Loss Rate | ≤5% | ≤4% |
Residual CO₂ Content in Lime | ≤1.5% | ≤1.5% |
Shuangli lime kiln is obviously superior to ordinary lime kiln in terms of efficiency, quality and environmental performance. It is suitable for enterprises with high requirements for lime quality, large production scale and strict environmental protection requirements, while ordinary kiln is more suitable for small-scale and low-budget production requirements. The choice of kiln type needs to be determined according to the specific needs and long-term development plan of the enterprise.
Technical Parameters
Compare Items | Sleeve Kiln | Double Chamber Kiln | Double Beam Kiln |
VSK Type | BASK | MAERZ | FERCALX |
Daily Production Capacity | 150–600 T/D | 300–600 T/D | 150–500 T/D |
Fuel Calorific Value (Gas) | ≥1500 Kcal/Nm³ | ≥800 Kcal/Nm³ | ≥1500 Kcal/Nm³ |
Fuel Calorific Value (Solid) | ≥2400 Kcal/Nm³ | ≥2400 Kcal/Nm³ | ≥2400 Kcal/Nm³ |
Fuel Type | Solid, Liquid, Gas | Solid, Liquid, Gas | Solid, Liquid, Gas |
Gas Pressure Requirements | ~17 KPa | ~50 KPa | ~17 KPa |
Minimum Particle Size | 30 mm | 15 mm | 15 mm |
Particle Size Ratio | 1:2 | 1:2 | 1:2 |
Calcination Principle | Partly cocurrent, partly countercurrent | Full-process parallel calcination | Full countercurrent calcination |
Lime Activity | ≥350 mL | ≥350 mL | ≥300 mL |
Light and Overburnt Rate | ≤5% | ≤4% | 6–8% |
Residual CO₂ Content in Lime | ≤1.5% | ≤1.5% | ~2% |
Energy Consumption Index (Kcal/kg lime) | 900–950 × 4.18 | 850–900 × 4.18 | 1050–1250 × 4.18 |
Power Consumption Index (KWh/t lime) | 30–35 | 22–28 | 34–40 |
Annual Operating Rate | ~96% | 92–96% | ~96% |
Total Weight | ~2800 tons/set | ~3200 tons/set | ~2600 tons/set |
Single Kiln Investment | ~55,000,000 RMB | ~50,000,000 RMB | ~30,000,000 RMB |
Exhaust CO₂ Concentration | ≥32% | ≥28% | ≥32% |
Cost of double-lime kiln
Small kiln (50-200 t/d): $5-10 million.
Medium kiln (200-500 t/d): $10-20 million.
Large kiln (500-1000 t/d): $20-30 million.
Production capacity: The larger the kiln's production capacity, the higher the cost.
Fuel selection: Fuel selection affects cost. Kilns designed to use multiple fuels or equipped with advanced combustion systems have higher initial costs but lower long-term operating costs.
Automation: Advanced automation systems (designed to control temperature, monitor, and optimize) may increase costs, but can improve efficiency and reduce operating costs.
Customization needs: Special raw materials, production goals, and location conditions may increase costs.
Mixed fuel double beam design lime kiln for lime production line
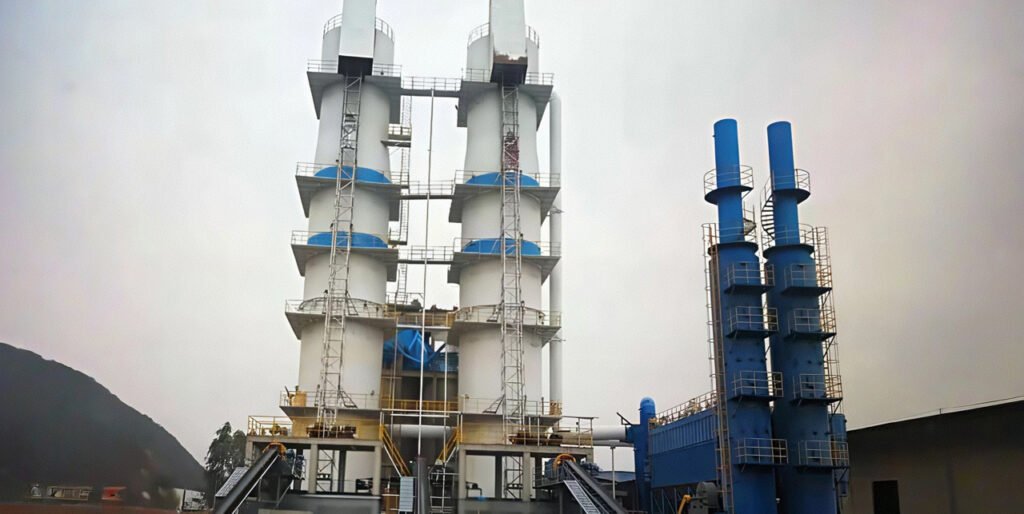
Capacity | 100-600 tons/day (adjustable) |
Limestone particle size | 30-60 mm; 40-80 mm |
Fuel | natural gas, oil, coal powder, etc. |
Activity | >320 ml |
Features | Mixed fuels (gas-oil, gas-coal, etc.) can be used, low investment cost, medium output, high degree of automation, high activity value. |
Structural features
- The kiln is a quasi-rectangular structure with upper and lower burner beams. The upper kiln gas extraction pipe is located above the limestone storage area and can be preheated between the extraction pipe and the upper burner beam. The high-temperature kiln gas preheats the limestone before entering the calcination area to ensure uniform calcination into active lime and adjust according to quality and output requirements.
- The limestone is added through the kiln top distribution device and is evenly distributed. The sealed door prevents air from entering during feeding. The system includes storage, preheating, calcination, post-calcination and cooling belts. The double-layer burner beam is a key technical element, cooled by thermal oil and contains adjustable burners for cross-sectional heating. Uniform negative pressure is maintained through the upper suction pipe to ensure optimal combustion efficiency, low permeability and high lime activity.
- The upper kiln gas extraction pipe and the evenly distributed openings in the lower layer maintain uniform negative pressure for optimal combustion efficiency. The lower suction beam in the cooling belt draws in cold air to cool the finished ash. The kiln body consists of only 2 layers of suction beams, 2 layers of burner beams and a flight mechanism, with a simple structure, low maintenance cost and low energy consumption.
- The PLC control system realizes the operation control, ensuring simple operation and easy to master. Our kiln design adopts innovative design to ensure the efficiency, uniformity and cost-effectiveness of lime production.
Competitive Advantages
- After many improvements, the three-way pressurization system effectively prevents too much air from entering the calcining zone, avoids interference with the calcining temperature, ensures that the heat carried by the lime from the calcining zone to the post-calcining zone is evenly distributed, greatly reduces power consumption and heat consumption, thereby improving the quality of lime, and the generation rate and overburning rate are about 5%-6%.
- Low investment, 500t/d steel structure is about 370 tons, refractory materials are about 480 tons, material specifications are standardized, no special-shaped bricks are required, and the system equipment is relatively less than other kiln types.
- Simple operation, high operating efficiency, low production cost.
- High production flexibility, can produce lime products that meet the diverse needs of various industries.
Double beam double combustion chamber lime kiln for industrial lime production
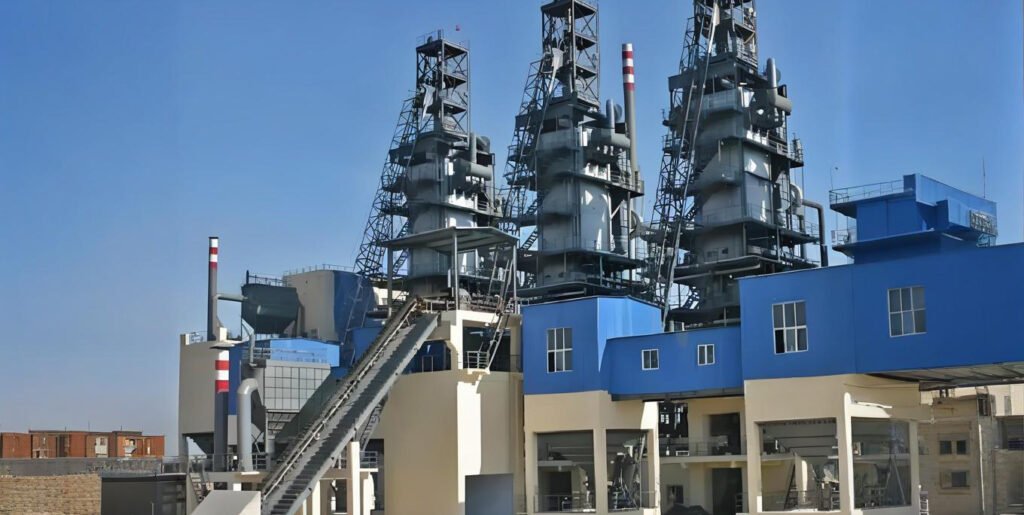
Capacity | 100-600 tons/day (adjustable) |
Limestone particle size | 30-60 mm; 40-80 mm |
Fuel | natural gas, oil, coal powder, etc. |
Activity | >320 ml |
Features | Mixed fuels (gas-oil, gas-coal, etc.) can be used, low investment cost, medium output, high degree of automation, high activity value. |
Structural features
- The kiln body is a quasi-rectangular structure with upper and lower burner beams arranged side by side. The upper kiln gas exhaust pipe is located above the limestone storage area to facilitate preheating between the exhaust pipe and the upper burner beam. The high-temperature kiln gas preheats the limestone before entering the calcination area, where the limestone is uniformly calcined into active lime and adjusted according to quality and output requirements.
- The limestone is fed by the kiln top distribution device and is evenly distributed. The sealed door prevents air from entering during feeding. The system includes storage, preheating, calcination, post-calcination and cooling belts. The double-layer burner beam is a key technical element, cooled by thermal oil and has adjustable burners inside to ensure cross-sectional heating. Uniform negative pressure is maintained through the upper suction pipe to ensure optimal combustion efficiency, low permeability and high lime activity.
- The upper kiln gas exhaust pipe and the evenly distributed openings in the lower layer maintain uniform negative pressure for optimal combustion efficiency. The lower suction beam in the cooling belt draws in cold air to cool the finished ash. The kiln body consists of only 2 layers of suction beams, 2 layers of burner beams and a flight mechanism, with a simple structure, low maintenance cost and low energy consumption.
- The PLC control system realizes the operation control, ensuring simple operation and easy to master. Our kiln design adopts innovative design to ensure the efficiency, uniformity and cost-effectiveness of lime production.
Competitive Advantages
- The three-way pressurization system is adopted and has been improved many times, which effectively prevents excessive air from entering the calcination zone to interfere with the calcination temperature, so that the heat carried by the lime from the calcination zone to the post-calcination zone is averaged, thereby effectively reducing power consumption and heat consumption, improving the quality of lime, and the generation and overburning rate is about 5%-6%.
- Low investment, 500td uses about 370 tons of steel structure and 480 tons of refractory materials. The material requirements are general, there are no special-shaped bricks, and the system equipment is less than other kiln types.
- Simple operation, high operation rate, low production cost.
- High production flexibility, can produce lime products required by all walks of life.
Energy-saving double vertical lime kiln for lime production
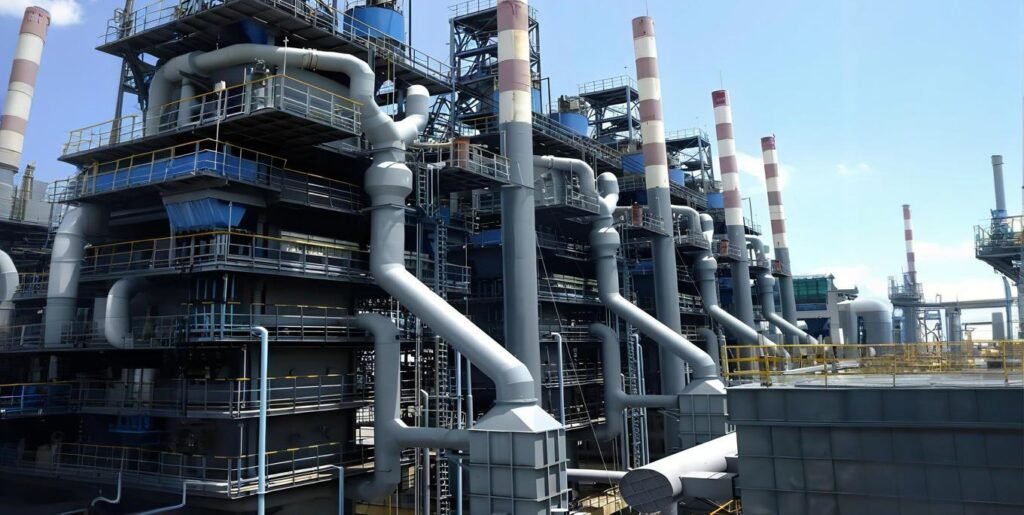
Capacity | 300-800 tons/day (adjustable) |
Limestone particle size | 30-60 mm; 40-80 mm |
Fuel | natural gas, oil, coal powder, etc. |
Activity | 360-400 ml |
Features | China Maerz kiln, large feed particle size, high price, most energy-saving, suitable for a variety of fuel types, and the highest activity value. |
Structural features
- Combustion in a twin-vertical lime kiln always occurs as the combustion air and fuel flow downward. In each kiln, the limestone also moves downward, a process called "co-flow", which is the first of the two characteristics of the kiln. And the very hot flame flows in contact with the limestone and the cooler gases to complete the calcination process. The limestone raw material at the initial end of the combustion zone cannot be over-burned, and the heat exchange rate can be very high. Near the end of the cooler combustion zone, the calcination of the limestone is completed and uniform light calcination conditions are obtained.
- The second characteristic of the twin-vertical lime kiln is the "regenerative" heat storage process, which occurs in the preheating zone. In this area, the limestone becomes a huge heat exchanger, absorbing heat from the exhaust gas and reducing the gas to a very low temperature. In the next cycle, part of the heat is released to the inhaled combustion air, bringing the combustion air to combustion temperature before it comes into contact with the fuel. This process is very efficient and the heat of the exhaust gas is fully utilized, which is largely the reason why the twin-vertical lime kiln has a very high thermal efficiency.
Competitive Advantage
- High efficiency; the double-lime kiln process can make full use of the thermal energy of the fuel and increase the output of lime. Compared with the traditional lime kiln, the lime output of the double-lime kiln can be increased by 20%~30%.
- Excellent quality: In the double-hole lime kiln process, the limestone is calcined at high temperature, which can better decompose to generate lime and remove impurities in the limestone. Therefore, the calcareous limestone produced by the double-hole lime kiln is of higher quality and more suitable for industrial and construction applications.
- Energy saving: In the double-lime kiln process, the limestone in the preheating chamber and the high-temperature flue gas in the combustion chamber are indirectly heat-exchanged to heat the limestone and reduce fuel consumption. Compared with the traditional lime kiln, the double-lime kiln can save 20%~30% of fuel.
- Environmental protection: In the double-lime kiln process, the high-temperature flue gas in the combustion chamber can take away impurities in the limestone and reduce pollution to the environment. At the same time, the double-lime kiln can also be used in conjunction with environmental protection facilities such as dust removal equipment to reduce emissions during lime production.
High activity value circular shaft kiln (CASK) based on Chinese technology
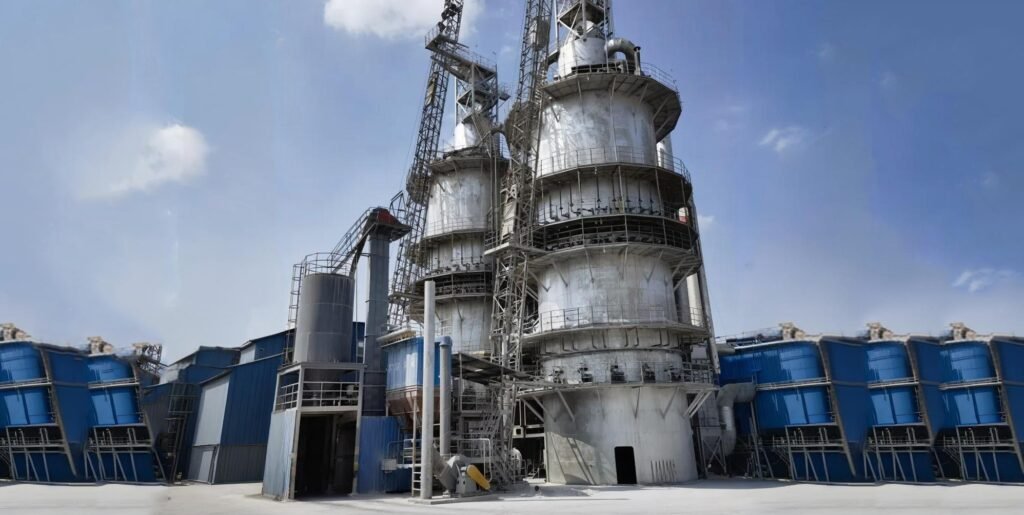
Capacity | 100-300 tons/day (adjustable) |
Limestone particle size | 30-60 mm; 40-80 mm |
Fuel | natural gas, coal powder, etc. |
Activity | >320 ml |
Features | Based on Chinese technology, large feed particle size, low price, small output, high automation, high activity value. |
The parameters of the China Ring Shaft Kiln are finely tuned for unrivalled performance. From temperature control to rotation speed, every aspect is precisely calibrated to enable multiple applications in different industries. Available in a variety of models to meet specific needs and expansion requirements, the kiln is a versatile asset for companies. In addition to its technical strength, the China Ring Shaft Kiln also has a lot to offer in terms of practicality. It has a wide range of uses - from cement production to mineral calcination and more.
Process
The 500 ton annular shaft kiln is a typical example with a clear process flow. It consists of upper and lower burners, each with six evenly distributed burners, 3.9 meters apart and 30 degrees apart. The lower burner divides the countercurrent and cocurrent calcination zones, and the combustion chamber has an arch bridge made of refractory material, which allows the hot gas to be evenly distributed throughout the material bed.
The annular sleeve active lime kiln consists of an inner and outer cylinder, forming an annular space for calcining limestone. This space is divided into preheating zone, countercurrent calcination zone, cocurrent calcination zone and cooling zone, maintaining optimal conditions for continuous calcination of limestone. The upper inner sleeve is suspended from the top, and the lower inner sleeve is located in the middle, made of boiler steel plate and lined with refractory material for efficient cooling.
Careful design ensures uniform distribution of pressure, airflow and temperature, improves the uniformity of limestone calcination, improves product quality and reduces unit consumption. The kiln is divided into three zones: a 9-meter preheating zone (90-140°C to 850-900°C), an 11-meter calcining zone (850-900°C to 900-950°C) and a 7-meter cooling zone (900-950°C to 80-130°C).
In the preheating zone, waste heat is minimized by using low calorific value gases or high CaCO3 limestone through the upper inner casing and heat exchanger design. The calcining zone accounts for 70-80% of the process flow, mainly operating in the countercurrent calcining zone, while the downstream calcining zone handles the remaining 20-30%. The cooling zone effectively exchanges heat with cold air to reduce the temperature of the lime before discharge (80-130°C). This innovative circular vertical lime kiln not only optimizes production efficiency, but also has adaptability to a variety of raw materials, which distinguishes it from traditional lime kilns.
Competitive Advantage
- The ring-shaped vertical lime kiln has been changed from the original positive pressure operation mode to negative pressure operation, which prevents the overflow of flue gas and dust and is more in line with environmental protection requirements.
- Multiple combustion chambers are cleverly arranged in a staggered manner on the upper and lower floors. Each combustion chamber is connected to the inner tube through an arch bridge made of refractory bricks. This design ensures that the high-temperature flue gas generated during combustion is evenly distributed, so that the stone is heated evenly.
- The combination of multiple calcination stages such as the preheating zone, the upper countercurrent calcination zone, the middle countercurrent calcination zone, and the lower downstream calcination zone achieves the best lime calcination quality and activity.
- The inner tube is used to preheat the primary combustion air, and part of the flue gas is recovered through the heat exchanger for further preheating, reducing the overall energy consumption.
- The ring-shaped vertical kiln has a high degree of automation, simple operation, and convenient adjustment. It is a technologically advanced and user-friendly solution.
Large vertical main lime kiln with high production capacity
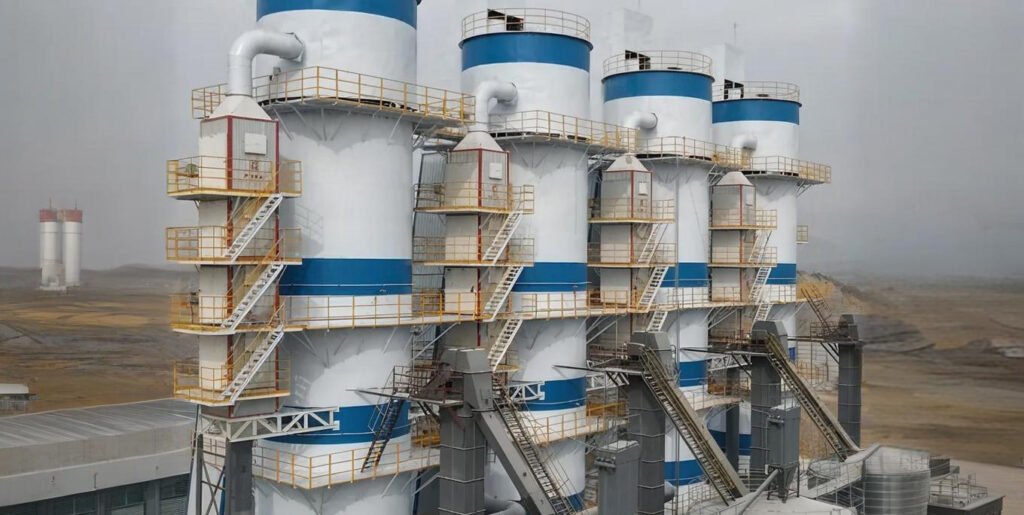
Capacity | 600-1200 tons/day (adjustable) |
Limestone particle size | 30-60 mm; 40-80 mm |
Fuel | natural gas, oil, coal powder, etc. |
Activity | 320 ml |
Features | Applicable to many types of fuels, large feed particle size, moderate investment cost, large output, high degree of automation, energy saving. |
Describe
A vertical lime kiln is a device that heats limestone and fuel together to produce a high-temperature reaction and burns to produce lime. Its main working principle is to feed limestone and fuel (such as wood, coal, etc.) into the vertical lime kiln in layers. Under the combustion of fuel, the limestone enters the furnace layer by layer, is continuously pyrolyzed at high temperatures, and releases carbon dioxide (CO2) to generate the lime (CaO) required for production.
Process
- The loader delivers the raw fuel to the limestone silo and coal silo, and transports it to the mixing silo to wait.
- Accurately weigh the raw fuel.
- The vibrating mixer feeds and mixes the materials evenly.
- The mixed fuel is poured into the furnace top hopper and distributed in the furnace through the furnace top volute distributor.
- When the charge moves slowly downward, it passes through the hot zone, forging zone, and cooling zone. In this process, it exchanges heat with the hot rising air flow, producing the process of limestone grain development and limestone decomposition.
- After the above steps are completed, the combustion air is cooled to 40-60℃, and the fuel can be unloaded onto the belt.
Competitive Advantage
- Automatic batching:The limestone and coal in the furnace can be accurately weighed and reasonably proportioned to achieve the effect of energy saving and consumption reduction.
- Good air tightness:The kiln masonry is built with high temperature resistant and low thermal conductivity insulation materials.
- Uniform feeding:The top feeding equipment consists of a receiving hopper, a rotary distributor, and a transmission device. The rotary distributor performs uniform quantitative feeding, so that the limestone and coal are distributed in a point-like and mesh-like manner, the air volume is evenly distributed, and the calcination zone is stable.
- Automatic control:The lime vertical kiln adopts a new automatic control technology to ensure the safe operation of key equipment such as distribution, stirring, air supply, and ash unloading.
- Quantitative air supply:The wind cap controls the air supply speed, which is designed by our factory to ensure uniform air supply in the furnace and avoid partial burning and overburning in the vertical furnace.
Low investment cost vertical lime kiln for limestone calcination

Capacity | 80-400 tons/day (adjustable) |
Limestone particle size | 20-40 mm; 60-90 mm |
Fuel | natural gas, oil, coal powder, etc. |
Activity | 320 ml |
Features | mixed feed lime kiln, Japanese technology, low investment cost, small output, high degree of automation, energy saving. |
Description
The single vertical lime kiln is also called the lime shaft furnace, which consists of a furnace wall and a burner installed on the furnace wall. A cylindrical furnace core is arranged at the center of the shaft furnace, and an annular gap is surrounded between the furnace core and the furnace wall.
The mechanized shaft kiln is the main calcining equipment in the production of cement and alumina. It has a reasonable structure, advanced technology, a sturdy transmission device, strong bearing capacity, long service life, stable output, and produces high-quality lime. It is an indispensable and valuable resource in industrial production.
Specification
Item | Details |
Effective Volume (m³) | 100–500 |
Production Capacity (T/D) | 80–400 |
Energy Consumption (KJ/kg lime) | 910 × 4.1868 |
Coal Consumption (kg/T lime) | <130 |
Utilization Factor (T/D·m³) | ≥0.85 |
Lime Reactivity (mL) | ≥300 |
Calcium Content in Quicklime (%) | ≥90 |
Overburning Rate (%) | <5–7 |
Lime Consumption (T/T) | 1.8 |
CO₂ Concentration in Flue Gas (%) | 42 |
Dust Emission Standard (mg/Nm³) | <10 |
Competitive Advantage
- Uniform feeding, rotating distribution:The upper feeding mechanism includes a hopper, a transmission device and a rotary distributor. The materials on the truck are evenly and quantitatively delivered to the rotary distributor for thorough mixing before entering the furnace. The circular fixed-point distribution of the rotary distributor, whether automatic or manual, distributes limestone and coal in the furnace in a "point and net" manner. This arrangement forms an "M"-shaped surface, ensuring uniform airflow throughout the furnace, which is essential for a stable calcination process.
- Optimize air supply, sealing, ash discharge:This section includes centrifugal fans, hoods and ash dischargers. The fan delivers air precisely as required, while the hood we design ensures uniform air supply to prevent partial or over-burning of the shaft furnace. The ash discharger allows the material to be evenly discharged along the circumference of the furnace, ensuring that the material column descends consistently and smoothly. This not only maintains the stability of the furnace airflow and prevents gas leakage, but also improves the on-site environmental conditions.
- Automatic weighing and consistent batching:Accurate weighing and maintaining the appropriate ratio of limestone to coal are essential to achieve high-quality calcination and energy efficiency in the lime shaft kiln.
- Efficient automatic control to ensure safety:The lime kiln system adopts advanced automatic control technology to optimize key processes such as material distribution, mixing, air supply, and ash discharge, ensure the safe operation of key equipment, and improve the safety and reliability of the entire lime production process.
Parallel flow heat storage double vertical lime kiln
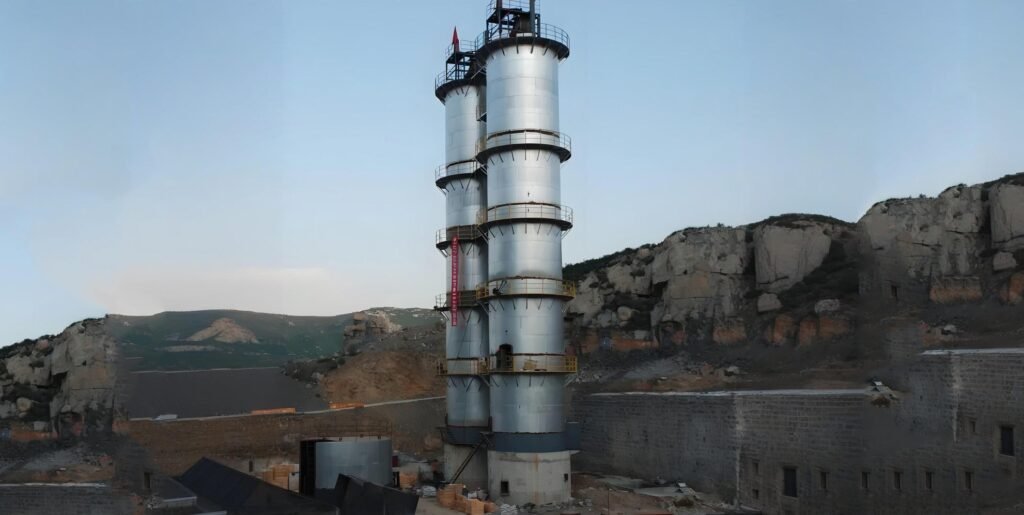
Capacity | 300-800 tons/day (adjustable) |
Limestone particle size | 30-60 mm; 40-80 mm |
Fuel | natural gas, oil, coal powder, etc. |
Activity | 360-400 ml |
Features | China Maerz kiln, large feed particle size, high price, most energy-saving, suitable for a variety of fuel types, and the highest activity value. |
Describe
The Twin Drive Lime Kiln represents the pinnacle of innovation in lime production, incorporating state-of-the-art technology and efficiency. This robust kiln is engineered to transform limestone into premium lime with unrivalled precision. Its twin-shaft configuration ensures optimal heat treatment, resulting in a more consistent product quality.
The kiln is made of resilient materials to ensure long life and durability, capable of meeting the demands of continuous operation. Precision in dimensions and parameters is the focus, achieving a delicate balance between compactness and high-capacity lime production. Its versatility to meet the needs of different types of limestone makes it a flexible solution for a range of industrial applications.
Structural features
In a twin shaft lime kiln, combustion occurs continuously as the combustion air and fuel move downward. The limestone in each kiln moves downward simultaneously, called “co-flow”, which is the first distinguishing feature of the kiln. The high intensity flame interacts with the limestone and the cooling gases to promote the calcination process. At the initial end of the combustion zone, the limestone raw material is prevented from over-combustion, thus ensuring a potentially high heat exchange rate. At the end of the cooling combustion zone, the limestone calcination is completed, achieving a uniform and lightly calcined state.
The second distinguishing feature of the twin shaft lime kiln is the “regenerative” heat storage process in the preheating zone. Here, the limestone acts as an important heat exchanger, absorbing heat from the exhaust gases and significantly reducing the gas temperature. In the subsequent cycle, part of the stored heat is released to preheat the incoming combustion air, raising it to combustion temperature before reaching the fuel. This process is very efficient, making full use of the heat in the exhaust gases and making a significant contribution to the excellent thermal efficiency of the twin shaft lime kiln.
Competitive Advantage
- Improved efficiency: The twin-shaft lime kiln process maximizes the use of fuel heat energy and significantly increases lime production. Compared with traditional lime kilns, the twin-shaft lime kiln has a 20% to 30% increase in lime production.
- Excellent quality: In the twin-shaft lime kiln process, limestone is calcined at high temperature, which has the best decomposition effect, high lime production, and effective removal of impurities. The produced lime is of high quality and more suitable for industrial and construction purposes.
- Energy saving: In the twin-shaft kiln process, limestone undergoes indirect heat exchange with high-temperature flue gas in the preheating chamber, which reduces fuel consumption. This energy-saving method enables the twin-shaft kiln to save 20%-30% fuel compared to traditional lime kilns.
- Environmental protection: The twin-shaft kiln process uses high-temperature flue gas in the combustion chamber to remove impurities from limestone and minimize environmental pollution. In addition, the twin-shaft kiln is used in conjunction with environmental protection tools such as dust removal equipment to further reduce emissions during lime production.
TTHN Automatic Vertical Lime Kiln
Kiln thickness | 1000 mm |
Customizable configuration | Supported |
Single kiln footprint | Approximately 0.33 acres (40x40 meters) |
Raw materials and fuels | Limestone and coke (anthracite) |
Applications | Small and medium-sized lime production lines |
Specification
Item | Details |
Effective Volume (m³) | 100–500 |
Output (Tons/Day) | 80–400 |
Energy Consumption (KJ/kg·lime) | 910 × 4.1868 |
Coal Consumption (kg/t·lime) | <130 |
Utilization Coefficient (t/d·m³) | ≥0.85 |
Lime Activity (mL) | ≥300 |
Calcium Content in Quicklime (%) | ≥90 |
Overburning Rate of Quicklime (%) | <5–7 |
Quicklime Consumption (t/t) | 1.8 |
CO₂ Concentration in Flue Gas (%) | 42 |
Smoke Emission Index (mg/Nm³) | <10 |
Competitive Advantage
- Unique Design & Energy Efficiency: The kiln body adopts a fully sealed design, significantly reducing heat loss. The fuel calorific value utilization exceeds 80%. A dual-slot distributor (TTS type) ensures uniform distribution of limestone and coal, promoting even combustion and preventing fuel waste. This innovative design saves more than 15 kg of coal per ton of lime produced.
- Five-Layer Kiln Structure: The kiln body consists of high-alumina bricks, lightweight insulating bricks, thermal insulation fillers, insulation fibers, and a steel shell. The lightweight outer shell extends the refractory insulation layer's service life to over five years.
- Compliance with Emission Standards: A new pulse bag dust collector and fiberglass desulfurization tower effectively filter dust, SO₂, and NOₓ from flue gas, ensuring that dust concentration remains below 10 mg/Nm³.
- Compact & Rational Process Layout: The vertical lime kiln system comprises feeding, mixing, batching, kiln body, discharge, finished product storage, and dust removal systems. A single kiln system occupies approximately 0.33 acres (40×40m).
- Scientific Approach to Raw Materials: Emphasizing the quality of fuel and raw materials, advanced technology ensures high-quality lime production. Maintaining uniform limestone particle size and minimizing impurities is crucial for stable calcination and preventing severe scaling. Proper coal particle size is also essential to avoid insufficient heat during CaCO₃ decomposition or combustion in the cooling zone.
- Innovative & Adjustable Weighing & Mixing System: The weighing and mixing system features a fully automated weighing device with high precision (error below 3%). The limestone weighing error is within 3 kg, while the coke (coal) weighing error is within 0.21 kg. The system automatically compensates for the final weighing error. The entire process is PLC-controlled and equipped with a monitoring system.
Maerz PFR kiln
Maerz C Series
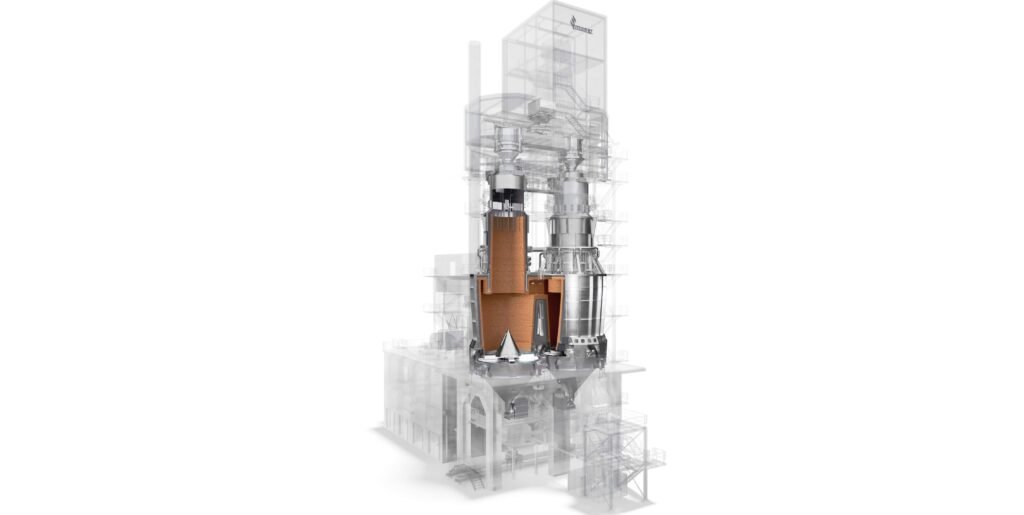
The Maerz C series is a further development of our classic round kilns with production capacities of 300 to 800 t/day: The annular channel ensures that even with larger kiln cross-sections, the fuel gas flows into it and is evenly distributed over the circumference of the inner cylinder. This ensures an even heat distribution over the kiln cross-section and guarantees a high quality of the quicklime. The charging system of the kiln has been further optimized and, thanks to an intelligent distribution system, several particle sizes can be used simultaneously for optimized utilization of the quarry. The layout of the new kilns in this series is modular, so that more fuel can be easily added without major adjustments to the existing equipment.
Maerz E Series
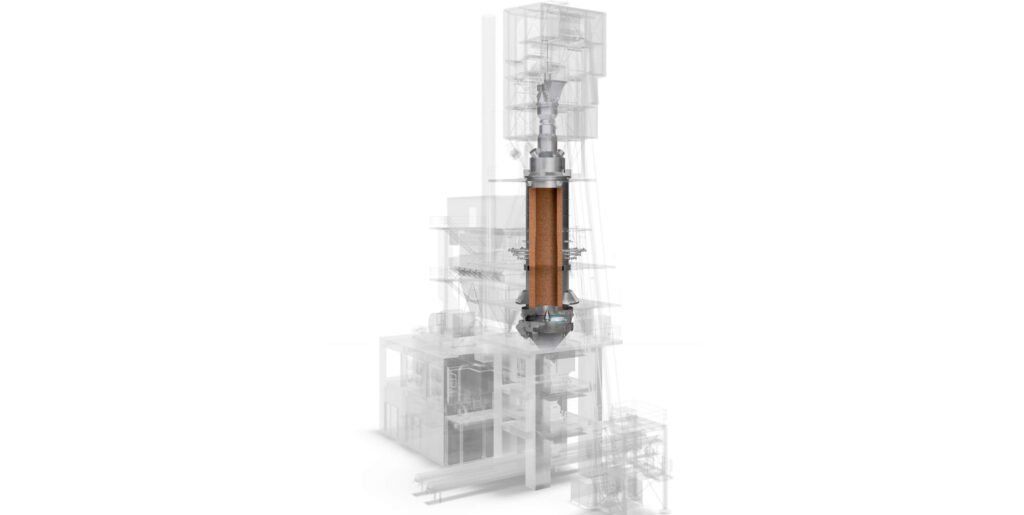
The Maerz E series is designed for production rates from 100 to 400 t/day. Its geometry with a direct cross-pass between two shafts requires less steel and refractory material than circular kilns and is optimized in terms of investment costs.
In these kilns, not only can the quality of the quicklime be optimized by special charging processes, but - just like in circular kilns - there is the option of using several particle sizes simultaneously.
In the E kiln, it is also possible to burn the lime more completely by installing additional side burners below the cross-pass, thus significantly reducing its reactivity. We call this type of kiln a "hybrid kiln" - it gives you the flexibility to use one kiln to produce different types of quicklime.
Maerz Ecological Kiln
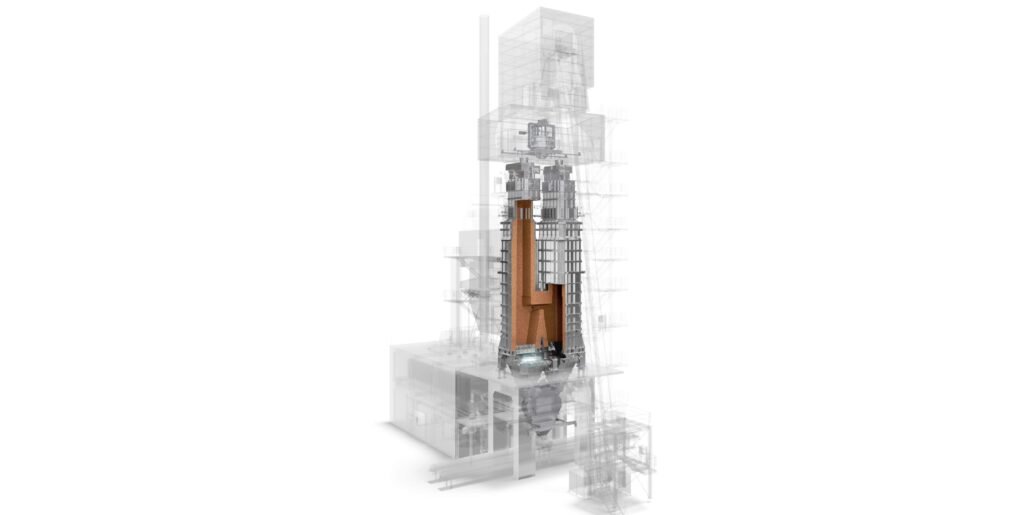
Until now, when dealing with lime kilns, people have always thought about optimizing the production process of quicklime, without taking into account the CO2 emissions of the lime kiln.
As the climate debate unfolds, this situation has changed radically: Maerz has worked step by step with innovation and great enthusiasm to increase the CO2 content in the kiln exhaust gases as much as possible. In the process, Maerz has patented several inventions and finally developed the Maerz EcoKiln series. As a result, the highly concentrated CO2 can be easily liquefied and used for further use or storage.
The Maerz EcoKiln series can be expanded in several stages: The simplest solution is to replace the combustion air only with oxygen-enriched kiln gas (oxy-combustion operation). In this way, CO2 contents of 40-45% in the kiln exhaust gases can be achieved. This configuration is ideally suited for use in the soda and sugar industries, where in many cases replacement investments for old co-fired kilns will be required in the coming years.
Maerz Mixing Kiln
Flexibility in lime plants with regard to product quality and fuel usage is very important today. In addition to large quantities of highly reactive lime, small quantities of medium-reactive lime are also required for special applications. This is not a problem for the Maerz hybrid kiln, which can be operated like a normal PFR kiln and, if required, the desired reactivity can be set by thermally post-treating the lime by opening the side burners in the lower area of the kiln.
Maerz fine lime kiln
Maerz PFR kilns can also be designed in a special way that allows small stones to be fired in the shaft kiln, thus improving the utilization of the quarry. The geometry of the cooling and preheating zones is optimized for the use of small stones, so that this design of the Maerz fine lime kiln can only be used in new kiln construction.
Another improvement is that the kiln can use several grain belts at the same time, each of which is fed into the kiln according to an optimized pattern. This significantly increases the total grain belt width and thus optimizes the utilization of the quarry. Existing plants can also be upgraded with this, as long as there is enough space in front of the hopper for several stone silos.
Maerz External Cooler
Maerz has developed a patented process to further optimize the cooling process in the kiln by means of a direct overflow channel. This makes it possible to produce quicklime of the highest quality, e.g. for use in the food industry. At the same time, the residual CO2 content can be kept very low, while the reactivity is very high.
The quicklime is cooled in two steps: The cooling air supply into the kiln shaft is reduced so that the quicklime temperature in the upper cooling zone is always kept high. In this process, the lime is discharged at a higher temperature than in conventional lime kilns. Further cooling of the quicklime takes place in a second step in an external cooler, which is installed below the discharge damper in the kiln shaft. Depending on the available space, the external cooler can also be installed in existing plants.
Author: Chumin
Date: 2025/3/8