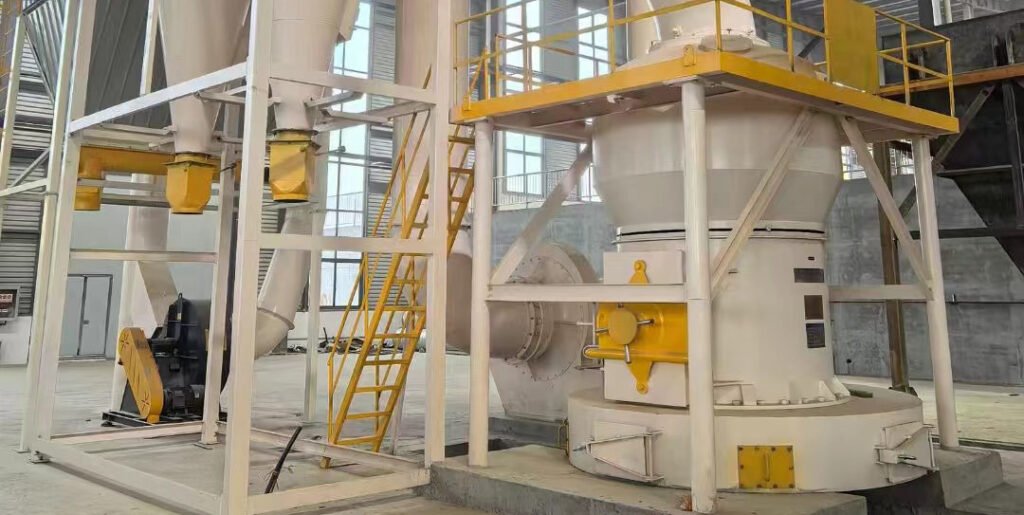
What is a Raymond Mill?
Raymond mill is also called pendulum mill, or Raymond mill for short. It is a commonly used grinding machine in industrial production. Raymond mill is an efficient closed-circuit fine powder grinding machine for non-metallic minerals. The finished product has a relatively fine and uniform particle size, which can well meet the material requirements of various fields. It is suitable for processing various non-flammable and explosive minerals with a Mohs hardness below 7 and a humidity below 6%. It is mainly used in mining, metallurgy, chemical industry, building materials, petrochemical, coal, smelting, fertilizer, medicine, infrastructure, roads, engineering, abrasives, food, feed, plastics and other industries. The finished product fineness can be adjusted between 613 microns and 44 microns (0.613 mm-0.044 mm) by the analyzer and fan to meet different requirements.
It can process cement clinker, quartz sand, feldspar, calcite, lime, limestone, dolomite, barite, graphite, gold and silver mines, rutile, titanium dioxide, kaolin, bentonite, aluminum ore, coke gemstone, fluorite, wollastonite, phosphate rock, rare earth, iron red, metallic silicon, electrolysis, niobium alloy, silicon carbide, diamond steel sand, smelting metal, calcium magnesium ore, coal, activated carbon, humic acid, carbon black, grass ash, coal gangue, slag, zircon sand, iron ore, iron fine powder, talc, granite, potassium feldspar, marble, barite, wax feldspar, clay, glass, coke, petroleum coke, water slag, slag, fly ash, cement. Pigments, clay, ceramsite sand, brine, mud sand grinding materials, such as additives, fire extinguishing agents, curing agents, waste ceramics, waste bricks, refractory materials, aluminum ore, bauxite, etc.
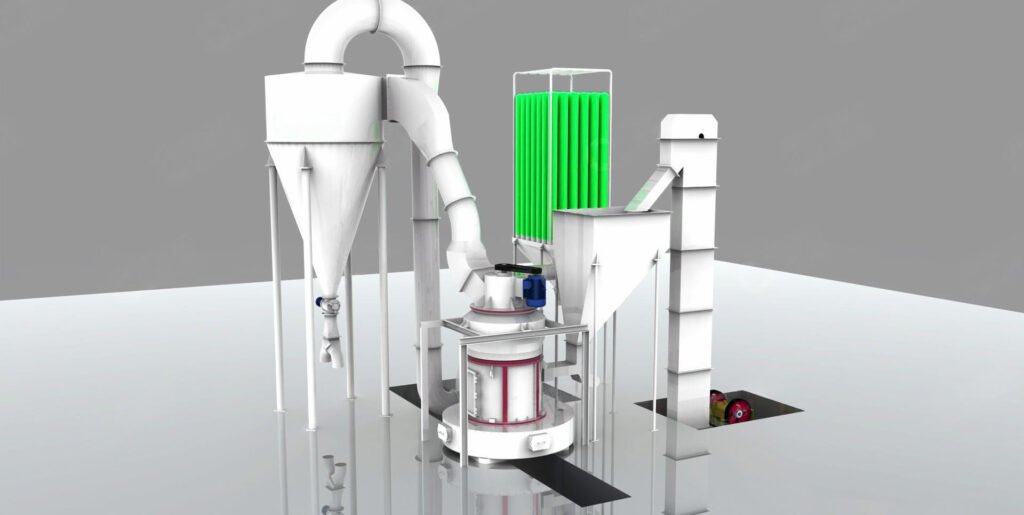
Feed size | Motor power | Processing power |
0-25mm | 7.5-300kw | 0.5-60t/h |
Why choose Tongli Heavy Machinery?
TONGLI is one of the major grinding equipment suppliers in China. We can provide any size and model of Raymond mill and other grinding equipment.
- Price: Our equipment is sold directly by the manufacturer, so the price will be lower.
- Experience: Rich production experience enables our equipment to have advanced process technology, guaranteed quality, and reduced material consumption and energy consumption.
- Export: Our equipment is exported to all over the world. We have rich export experience, so we can ensure timely and safe delivery and reduce customers' time costs.
- Customization: Customization services are provided. We can customize equipment according to customer requirements, such as capacity, color, size, etc.
- Wide application: Widely used in fine grinding of materials such as limestone, desalination enzyme, calcium carbonate, barite, calcite, potassium feldspar, talc, marble, dolomite, etc. Raymond mill can adjust the particle size 80-325, and some materials can reach 600.
- Cost-effectiveness: Compared with ball mill, Raymond mill has the advantages of high cost-effectiveness, low cost and small footprint.
- Technological innovation: In order to increase profits, according to the accumulation and analysis of field operation data over the years, Raymond mill needs to separate ultrafine powder and expand production. So we have updated and renovated it. ZJTL adopts the advanced structure of similar products at home and abroad, and designs and updates the traditional Raymond mill.
- Long service life: The service life of the upper and lower grinding rings is more than 8000 hours, the service life of the grinding balls is 4000 hours to 6000 hours, and the service life of the whole machine is more than 30 years. Raymond mills also have a long replacement cycle for easily damaged parts.
- Customized service: In order to meet the individual requirements of customers, TONGLI provides customized solutions for each processing production.
- Environmental protection: Fully consider environmental protection, the machine is scientifically designed, and the machine body without dust leakage and ash leakage is installed, and the dust removal and silencer device is installed, which has low noise and eliminates the production stop caused by dust and noise.
Raymond mill structure
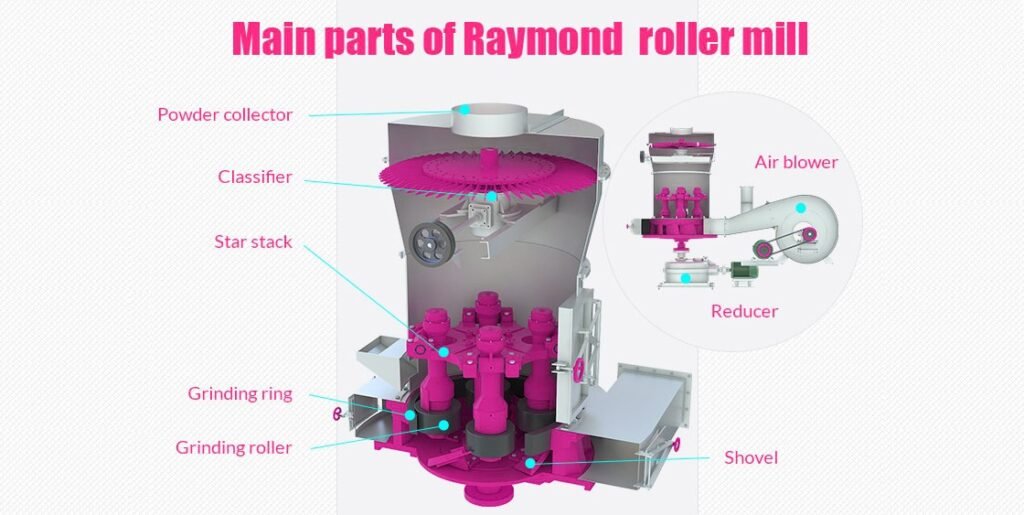
Working Principle of Raymond Mill
When the material enters the mill continuously and evenly, it will be transported by the scraper to the middle of the grinding roller and the grinding ring. During the grinding process, the material will be repeatedly stirred. The grinding roller is tightly pressed against the grinding ring under the action of centrifugal force, so that the material is crushed into powder under the action of grinding pressure, and then enters the powder classifier through the circulating air of the blower. After that, the qualified material will pass through the powder classifier and enter the dust collector for separation and collection. The unqualified material will be sent back to the grinding disc for re-grinding.
Advantages
- The force generated by the grinding roller connected by the tie rod and high-pressure spring can avoid damage to the equipment caused by bulk materials;
- The elastic coupling between the main machine and the separator can reduce vibration and noise and increase the service life of the equipment. Since crushing, drying, grinding, grading and conveying are connected together, the system is simple and compact in layout, occupying about 50% of the area of the ball mill system, and can be arranged outdoors, which can greatly reduce the investment cost;
- The milling roller device adopts superimposed multi-stage sealing with excellent sealing performance. The unique air circulation system is equipped with advanced dust collectors to implement the environmental protection concept to the end;
- The high-density and high-precision impeller device can increase the yield of more than 50% at the same power. The efficient and energy-saving centrifugal induced draft fan greatly improves the efficiency of the induced draft fan. The convenient impeller adjustment device improves the precision of the finished product.
Raymond mill production line
Raymond mill usually includes cyclone dust collector, pipe fittings, dust collector, storage hopper, elevator, crusher, electric control cabinet, feeder, main plant, blower, separator, etc.
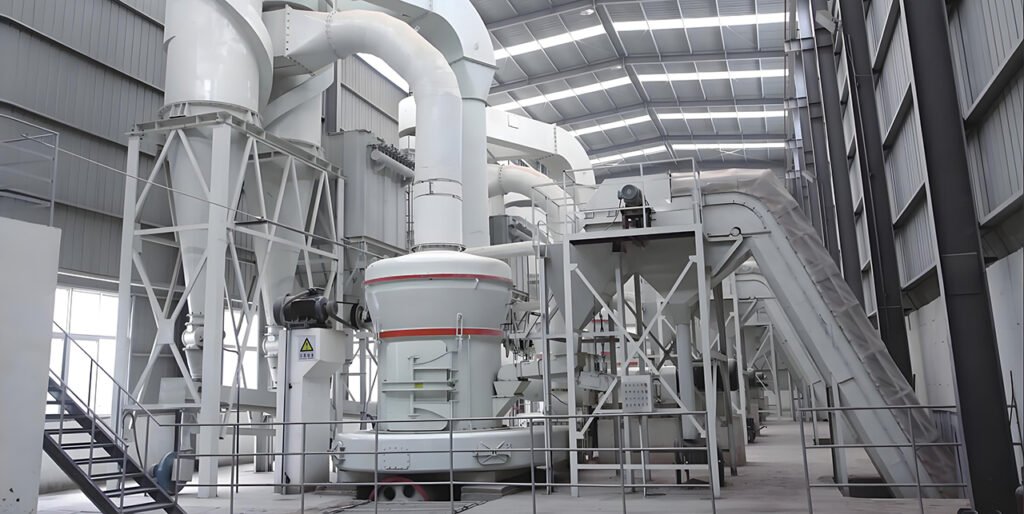
Working principle
After the jaw crusher breaks the large pieces of material into small pieces, the elevator feeds the material into the hopper. Through the vibrating feeder, the broken materials are uniformly and quantitatively fed into the grinding chamber of the Raymond mill for grinding. After grinding, the materials are blown to the powder classifier by the airflow for classification. Under the action of the impeller of the powder classifier, the materials that do not meet the fineness will be sent back to the grinding chamber for re-grinding, while the qualified powder will be collected by the cyclone powder collector and discharged from the bottom as a finished product. After that, the airflow will enter the fan together with the return air duct at the top of the cyclone collector. The system adopts a closed circuit and operates under positive and negative pressure. Since the material contains a certain amount of moisture, the heat generated during the grinding process may cause the air to evaporate or expand in the grinding chamber, thereby increasing the airflow sharply. In addition, if the seal between the feed port and the pipeline is poor, external air may invade the mill, resulting in airflow imbalance. Therefore, an exhaust valve is set at the air outlet of the fan to introduce excess air into the bag dust collector. After purification, this excess air is discharged. This setting can achieve both airflow balance and environmentally friendly production.
Structural features
- The whole system takes up less space and has strong systematization. The whole system forms an independent production system from rough processing, conveying, collecting powder to packaging.
- Uniform particle size and sieving rate of 99%, which is unattainable by other mills.
- The driving device adopts closed gearbox and pulley, with smooth transmission and reliable operation.
- All main components of Raymond mill are made of high-quality steel, and wear-resistant parts are made of high-performance anti-corrosion materials, so the whole system has high wear resistance and reliable performance. The knife holder of the main machine keeps in contact with the material. It consists of upper and lower parts. When the lower part is worn, just remove the bolts to replace it.
- The electrical system is centrally controlled, unmanned, and easy to maintain.
- Less dust pollution and low noise.
- Adopt vibrating feeder, which has uniform feeding, convenient adjustment, small size, light weight, power saving and easy maintenance.
Specifications
Model | Number of Grinding Rollers (pcs) | Grinding Roller Size (mm) | Grinding Ring Inner Diameter | Height & Length (mm) | Feed Size (mm) | Product Fineness (mm) | Capacity (t/h) | Motor Power (kW) |
ZJTL65 | 3 | 210×150 | 650×150 | ≤15 | 0.613-0.033 | 0.4-1.8 | 15 | 4100×3300×4500 |
ZJTL75 | 3 | 260×150 | 780×150 | ≤15 | 0.613-0.033 | 1-3 | 18.5 | 4300×3500×5100 |
ZJTL85 | 3 | 270×150 | 830×150 | ≤20 | 0.613-0.033 | 1.2-4 | 22 | 5300×4100×5200 |
ZJTL85B | 3 | 270×150 | 830×150 | ≤20 | 0.613-0.033 | 1.2-3.5 | 22 | 5300×4100×5200 |
ZJTL95 | 4 | 310×190 | 950×190 | ≤25 | 0.613-0.033 | 2.1-5.6 | 45 | 7100×5900×7900 |
ZJTL130 | 5 | 410×230 | 1280×230 | ≤30 | 0.613-0.033 | 2.5-9.5 | 90 | 7900×8000×9700 |
ZJTL160 | 6 | 450×300 | 1600×300 | ≤35 | 0.613-0.033 | 8-16 | 132 | 12550×5700×8355 |
ZJTL190 | 6 | 500×330 | 1900×330 | ≤40 | 0.613-0.033 | 18-36 | 250 | 11200×8500×9685 |
Raymond Mill Operation Guide
1.Material Preparation
Ensure that the material is dry and of a suitable size for grinding. Pretreatment of the material can significantly affect the efficiency of the grinding process.
2.Operating Parameters
Adjust the mill's operating parameters, such as speed and feed rate, to match the material being processed. This adjustment is critical to achieving the desired product fineness and quality.
3.Monitor Performance
Regularly monitor the performance of the equipment, including output quality and energy consumption. These indicators can help detect any operating problems early.
4.Handle Emergencies
Develop clear procedures for handling emergencies, such as sudden shutdowns or mechanical failures. A quick and effective response can minimize downtime and potential damage.
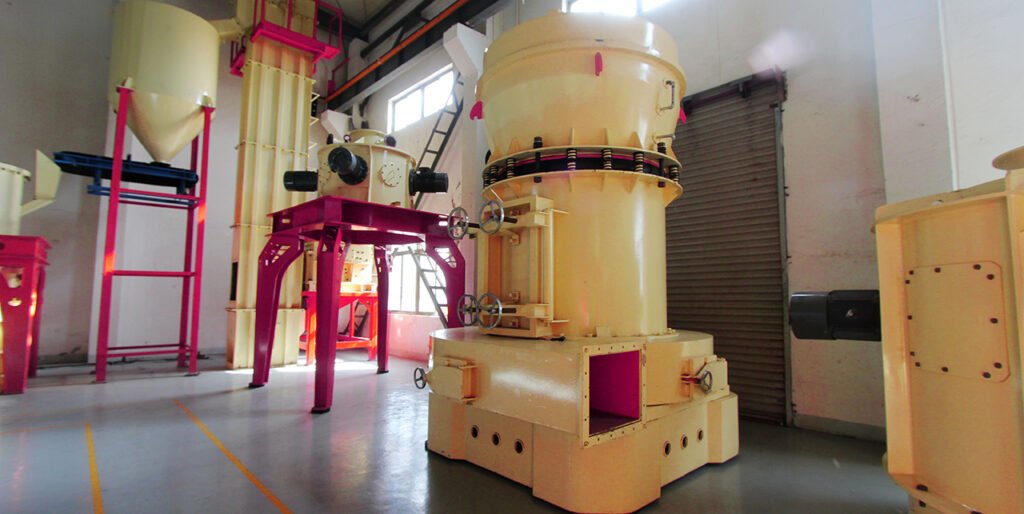
Spare parts management
Stocking a wide range of Raymond mill spare parts is very important to minimize interruptions:
- Wearing parts: rollers, roller sleeves, grinding segments, hammer rods, etc.
- Mechanical seals: stuffing box packing, oil seals, pump gaskets, valves
- Electrical: fuses, contactors, switches, sensors, drives, controllers
- Bearings: ball bearings, tapered roller bearings, journal bearings, thrust bearings
- Fasteners: nuts, bolts, anchor bolts of various sizes
- Filters: dust collector filter elements, bags, filter elements
- Tools: maintenance equipment, repair and overhaul work tools
- Industrial spare parts management includes maintaining optimal inventory levels, online tracking, quality control, timely procurement and condition monitoring to keep equipment availability above 95%.
Raymond Mill Maintenance Guide
Daily Maintenance
- Cleaning: Use brooms and shovels to remove accumulated powder from the machine and surrounding areas. Check the grinding system and remove any blockages.
- Lubrication: Lubricate transmission components, bearing surfaces and other parts that require grease or oil as specified. Check fluid levels and top up if necessary.
- Inspection: Check grinding discs and roller surfaces for excessive wear. Watch for vibrations and unusual noises, which indicate potential problems. Record instrument readings.
- Dust removal: Check and clean dust removal and conveying systems to avoid accumulation. Shake hoses, clean filters and empty dust collectors daily.
- Repair: Address small parts issues such as wearing parts replacement to avoid them developing into larger problems. Maintain equipment repair records.
- Safety inspection: Check the function of hazard signs, limit switches and protective devices to ensure the safety of the crew. Isolate or repair identified hazards promptly.
- Records: Record all maintenance activities, production parameters and material consumption daily for performance analysis. Report abnormal conditions immediately.
Weekly Maintenance
Any problems found must be recorded and promptly addressed to minimize the risk of downtime. Meticulous weekly maintenance ensures smooth operation and significantly extends mill life.
- Dust suppression measures: Clean dust suppression equipment and test water spray and dust baffle function. Top up water spray as required.
- Disassembly inspection: Loosen and remove inspection hole covers, flanges and rollers, and carefully inspect internal clearances and component surfaces.
- Bearing inspection: Check bearings for damage, corrosion, overheating and lubrication condition. Turn by hand and listen for any abnormalities. Relubricate as needed.
- Gearbox inspection: Drain the lubricating oil and carefully inspect the gears, shafts and seals under good lighting. Top up with new oil and reinstall components securely.
- V-belt tension: Check V-belt tension and alignment. If necessary, adjust and re-tighten the belt to the specified torque using a flat-blade tool.
- Anchor bolts: Check and re-tighten the anchor bolts, jacking screws and leveling mechanisms to ensure a stable installation.
- Parts: Replace worn parts such as roller bushings, pulley shafts and bearings on a scheduled basis rather than running into failure.
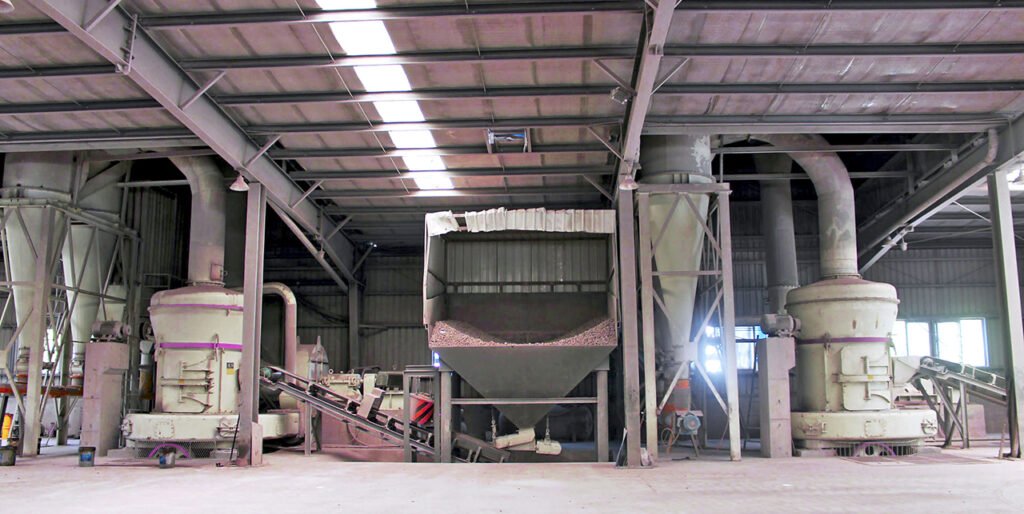
Quarterly/half-year maintenance
Major maintenance is recommended every 3-6 months: A thorough inspection and repair can prevent premature failures, improve reliability, and significantly extend mill life.
- Screening analysis: Test samples at the feed, product, and scrap ports to verify that the screen and grinding efficiency are within specifications. Replace worn screens in a timely manner.
- Pulley alignment: Use a laser or ruler to realign the motor, reducer, and main pulley center. Avoid excessive vibration due to misalignment over time.
- Accessories: Remove dust removal equipment, water pumps, and piping systems for inspection and repair. Replace hoses, filters, and nozzles as planned.
- Gearbox maintenance: Major gearbox maintenance includes disconnecting, cleaning, inspecting gears, replacing worn parts when necessary, and properly reassembling with specified lubricants.
- Bearing replacement: Depending on the operating time, perform a program replacement of journals, thrust bearings, lifetime lubrication devices, and other wearing parts every 6 months to 1 year.
- Foundation grouting: Check the condition of foundation concrete, anchor bolts, and grouting under machinery. Cracks or separated areas need to be removed and replaced.
- Grease nipples: Remove, clean, and reinstall grease nipples to all lubrication points. Refill grease guns and maintain a pumping schedule.
Annual Maintenance Procedure
Performed annually or as per instrument readings, annual work is carefully performed to maintain critical machine components and prevent unexpected failures or production interruptions through regular verification and refurbishment.
- Cylinder Regrinding: Disassemble and regrind or replace cylinder grinding surfaces every other year to restore concentricity as per wear specifications.
- Chassis Works: Loosen base assembly bolts and remove accumulated rust with wire brush. Re-drill and reinstall anchors to main engine.
- Repair and Painting: Handle any structural repairs, sandblasting, paint work on control room and machinery surfaces. Maintain corrosion protection.
- Structural Inspection: Perform ultrasonic testing of critical stress areas such as base, column welds and overload members as per design fatigue life assessment.
- Load Testing: Verification testing of emergency stop circuits, interlocks, lifting lugs and other safety stopping devices is performed under simulated overload conditions.
- Motor Repair: Major repairs on induction motors performed by authorized service centers include cleaning, insulation testing, re-impregnation, parts replacement.
- Calibration: Recalibrate mill instruments and safety devices using a certified primary reference to ensure accuracy after one year of field exposure.
Author: Chu min/Cheng Hang Huang
Date: 2025/02/26