Tongli provides a full set of EPC solutions for cement production lines with daily output of 800 tons to 5,000 tons
Since 1958, Tongli has been focusing on the research and development and manufacturing of cement equipment. It has rich project experience and has exported equipment to more than 60 countries around the world. Tongli cement production line mainly consists of crushing and pre-homogenization, raw material preparation and homogenization, preheating and decomposition, cement clinker burning, cement grinding and packaging. First, the raw materials are preliminarily processed by the grinding system, and the raw materials such as limestone and clay are ground into fine powder using vertical roller mill/ball mill/roller press. Then the raw materials enter the rotary kiln for calcination. The raw materials are converted into clinker through high-temperature calcination. Then the finished grinding system further grinds the clinker to a suitable fineness to produce high-quality cement that meets market demand. Tongli improves energy efficiency and reduces energy consumption through an optimized heat recovery system.
PRODUCTION LINE EQUIPMENT LIST

Cement vertical roller mill is a kind of equipment used for cement grinding, mainly used to grind cement clinker, gypsum, slag, coal powder and other materials into fine powder. Compared with traditional ball mills, cement vertical mill has higher production efficiency and lower energy consumption, and is one of the commonly used equipment in modern cement production lines.

Cement ball mill is a kind of equipment widely used in cement production process, mainly used to grind cement clinker and other raw materials (such as gypsum, slag, etc.) into fine powdered cement. It grinds the material to the required particle size through the collision and friction between the steel balls in the rotating grinding drum and the material.

The cement rotary kiln is the core equipment used in the cement production process to calcine raw materials (such as limestone, clay, iron ore, etc.) and convert them into cement clinker. The structure of the rotary kiln is usually cylindrical, tilted, and can rotate. It uses high temperature to drive the chemical reaction of the raw materials to form clinker and further process it into the final cement product.
NPK PRODUCTION LINE ADVANTAGES
Tongli cement production line provides EP project services, covering design, manufacturing, installation guidance and after-sales service.
All equipment is independently developed and produced by Tongli, directly sold by the factory, and has reliable quality.
The cement production line adopts advanced DCS system with high degree of automation.
Through optimization technology, the power consumption of cement production line is reduced by 25%~30%.
The production line is equipped with exhaust gas treatment and waste heat recovery system to reduce emissions and energy loss.
It can adapt to the production of various raw materials and fuels to meet the needs of different customers.
Many years of manufacturing experience in key equipment and rich industry application cases.
Tongli provides all-round technical support and after-sales service to ensure that customers can quickly get started and operate stably.
CEMENT PRODUCTION PROCESS

Raw Material Handling
The main raw materials of cement include limestone, clay, iron ore, etc. Limestone accounts for 70% to 80% of the raw materials, clay provides silicon, aluminum and iron elements, and iron ore is used to adjust the iron content in the raw materials. After gypsum and mixed materials are transported to the factory by trucks, they are poured into the raw material bin for storage. Gypsum is transported to the hammer crusher by forklift for crushing, and the crushed gypsum is conveyed to the gypsum pile by the belt conveyor of the batching station for storage. The mixed materials are transferred to the hopper by forklift, and then transported to the mixed material pile of the batching station through the conveying system. During the production process, limestone needs to be crushed to a particle size of less than 25 mm. After pretreatment, the raw materials are mixed according to the designed ratio and transported to the raw material grinding system through the automatic batching system to ensure accurate proportioning with an error control of ±1%.
Raw Material Grinding
In the cement batching process, the batching station is equipped with a φ10m clinker pile and three φ8m mixed material piles. Two sets of quantitative feeding devices are set at the bottom of the pile to unload materials according to the preset ratio. The discharged materials are sent to the cement grinding system through a belt conveyor to ensure the accurate ratio of each raw material before entering the grinding. The mixed raw materials are ground by a Tongli vertical roller mill or a Tongli limestone ball mill to grind the raw materials into fine powder below 80 microns, called raw meal. Raw material vertical mills are usually widely used because of their high efficiency and energy saving advantages, and have low energy consumption. The uniformity of grinding directly affects the reaction effect during calcination, and ensuring the uniformity of chemical composition is the core task of this stage. The energy consumption of the grinding process usually accounts for more than 30% of the total energy consumption of cement production, so optimizing the grinding system is crucial to energy conservation and emission reduction.
Calcination
The raw meal is gradually heated up by the preheater and enters the decomposition furnace for partial decomposition. This process uses the exhaust gas at the kiln tail for heat exchange, and the preheated raw meal can enter the calcination stage faster. After preheating and decomposition, the raw meal enters the rotary kiln for calcination, and the temperature is usually controlled at around 1450℃. At this high temperature, calcium carbonate decomposes into calcium oxide and reacts with silicates and aluminates to form cement clinker. The design of the rotary kiln has an important influence on the calcination efficiency, ensuring that the material reacts evenly at high temperatures.
Clinker Cooling
The calcined clinker enters the grate cooler for rapid cooling, from 1450℃ to below 100℃. The grate cooler cools the clinker through air flow and recovers heat for preheating raw materials. The cooling process directly affects the physical properties and reactivity of the clinker, while improving energy utilization. The heat recovery efficiency of the grate cooler is as high as more than 70%, which greatly reduces energy consumption and improves the overall energy efficiency of the production line. The slag powder warehouse is equipped with a φ12m slag powder pile. After the slag powder is transported to the plant by truck, it is pumped into the powder pile. Subsequently, the slag powder is transported to the cement grinding workshop by an air conveyor to ensure the efficient use of the slag powder in subsequent production.
Clinker Grinding
The cooled clinker is ground together with an appropriate amount of gypsum and slag or fly ash. The grinding fineness is usually controlled at about 325 mesh. The system is equipped with a set of φ1600×1500 roller press and a set of φ4.2×13m cement grinding equipment. The cement raw materials are first squeezed to the required particle size by the roller press, and then classified by the V-type powder classifier, and the fine materials enter the ball mill for further grinding. The ground cement raw materials are sent to the high-efficiency powder classifier through the bucket elevator and the pneumatic conveying trough. The coarse powder returns to the ball mill through the pneumatic conveying trough for re-grinding, and the fine powder enters the high-efficiency bag dust collector with the air flow, and finally produces finished cement. The finished cement is transported to the cement storage silo through the pneumatic conveying trough and bucket elevator. The purified exhaust gas is discharged into the atmosphere through the exhaust fan. At the same time, the exhaust gas generated by the ball mill is also treated by the bag dust collector and discharged by the exhaust fan at the tail. The finished cement in the storage silo is transported to the bulk cement station and cement packaging workshop through pneumatic conveying troughs and bucket elevators.
Packaging
After the cement is ground, it is transported to the storage warehouse by air and enters the automated packaging system. The packaging system weighs, packages and palletizes according to demand to ensure the accuracy of the weight of each bag of cement, with an error within ±0.5%. There are two types of packaging systems, one is bagged and the other is bulk. Bagged cement refers to cement packed in packaging bags, usually 50 kg per bag. Bagged cement is generally transported in the form of bulk cement and can be transported by various means of transportation such as cars and trains.
VIDEO
WHY CHOOSE US
The cement production line is efficient, reliable, and provides consistent quality. Customer service and support are excellent. We're highly satisfied and would recommend it.
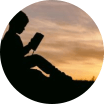
CFO
The cement production line is efficient, reliable, and provides consistent quality. Customer service and support are excellent. We're highly satisfied and would recommend it.

CEO
The cement production line is efficient, reliable, and provides consistent quality. Customer service and support are excellent. We're highly satisfied and would recommend it.

CEO
The cement production line is efficient, reliable, and provides consistent quality. Customer service and support are excellent. We're highly satisfied and would recommend it.

CEO
FAQ
The investment in cement plant involves plant construction, production equipment, auxiliary facilities, etc. Plant construction accounts for 20%-25% of the total investment, covering plant layout and infrastructure. Production equipment is the core investment, accounting for 50%-60% of the total investment, including clinker preparation, calcination and cement preparation equipment.
Taking a small-scale 500 tons/day (tpd) cement production line as an example, the total investment is usually about 10 million to 15 million US dollars. For a medium-sized 2000tpd production line, the investment range is usually between 40 million and 60 million US dollars. For a large-scale 5000~8000tpd production line, the investment amount can reach 100 million to 200 million US dollars or even more.
The investment scale of cement production line varies with different production capacity, mainly affected by factors such as equipment, land, construction and operating costs. Tongli can provide solutions based on the customer's on-site conditions.
In the early 1980s, the control method of cement production lines was: the motor was controlled by PLC, and the production process was controlled by a small computer with a large instrument control panel to achieve centralized monitoring, and the process parameters were inspected and tabulated. The process flow and parameter values were displayed by CRT, and the raw material batching was controlled by X-ray fluorescence analyzer and computer.
In the 1990s, most cement plants adopted DCS distributed control systems, which integrated motor control and process control, and were centrally operated in the central control room with a high degree of automation. The extensive application of new automation technologies and equipment has greatly improved the labor productivity of all employees and made full use of the human resources of the enterprise.
For example, a clinker production line with a daily output of 7,500 tons has 500 employees in the plant, and the labor productivity of all employees exceeds 5,000 tons/person/year. At present, DCS or PLC control systems have been widely used in newly built rotary kiln production lines with a daily output of 500 to 8,000 tons, such as the TDC-2000 DCS device produced by Honeywell, the Master system produced by ABB and the N-90 system produced by BAILEY in the United States, to implement all-round monitoring of the process parameters and equipment operating status of the production line.
Tongli Heavy Machinery can tailor solutions for cement production lines and cement grinding stations according to the specific needs of customers, including raw material characteristics, site area and production scale.
Whether choosing traditional ball mill grinding, vertical mill grinding, or more efficient roller press + ball mill combined grinding process, Tongli can provide customers with professional advice to ensure optimal production efficiency and cost-effectiveness.
At the beginning of the project, customers can get a preliminary design for free, which includes equipment selection, process flow recommendations, etc. After both parties confirm the intention to cooperate, Tongli will provide a detailed quotation list and process flow chart.
After the contract is signed, Tongli further provides detailed plant layout drawings and civil engineering foundation drawings to ensure the smooth construction of the factory, help customers quickly put into production and optimize the project construction cycle. At the same time, for projects of different scales and requirements, Tongli can also provide one-stop services such as equipment installation, commissioning, and training according to customer needs.
The investment payback period of a cement production line depends on many factors, including equipment investment, operating costs, cement prices in the local market, and capacity utilization.
Taking our customer's 5,000 t/d cement production line as an example, the initial investment in building a 5,000 t/d cement production line is approximately between $150 million and $200 million. Assuming the equipment has a service life of 20 years, the annual production capacity is approximately 1.5 million tons of cement.
Based on the current cement prices in Uzbekistan or Zimbabwe, the retail price of cement in Zimbabwe is approximately $13 to $14 per bag, and the wholesale price is slightly lower. In Uzbekistan, the cement price is approximately $61 to $62 per ton. If the cement price is approximately $60 per ton, the annual revenue is approximately $90 million.
After deducting production costs and operating expenses, the payback period is usually around 5 to 8 years. Therefore, the specific payback period may be adjusted according to market conditions, but generally speaking, for a 5,000t/d cement production line that operates stably and meets market demand, a payback period of 4 to 5 years is a relatively reasonable estimate.
The cement production lines produced by Tongli Heavy Machinery cover a variety of specifications to meet the needs of customers of different sizes. Common small-scale cement production lines include 500 tons/day (500tpd), 800 tons/day (800tpd) and 1000 tons/day (1000tpd). These production lines are suitable for small and medium-sized cement plants, with relatively low investment and small footprint.
Medium-scale cement production lines include 1500 tons/day (1500tpd), 2000 tons/day (2000tpd) and 2500 tons/day (2500tpd). These production lines are suitable for larger-scale cement plants, with ideal production capacity and economic benefits.
The specifications of large-scale production lines include 3,000 tons/day (3,000 tpd), 5,000 tons/day (5,000 tpd), 6,000 tons/day (6,000 tpd), and even 8,000 tons/day (8,000 tpd) and above, which are mainly used in large cement enterprises. Whether it is a small, medium or large cement plant, Tongli Heavy Machinery can provide customized solutions to meet the different needs of customers.
A cement production line is a complete cement manufacturing process, from the collection and pretreatment of raw materials to the production of finished cement. It mainly includes raw material crushing, pre-homogenization, raw material grinding, clinker calcination, clinker cooling, and finished product grinding. The core equipment includes rotary kiln, vertical mill or ball mill, grate cooler, preheater, and decomposition furnace. The cement production line not only involves the production of cement clinker, but also includes all steps in the entire production process from raw material processing to finished cement.
A cement grinding station is only responsible for the last link of cement, that is, mixing clinker with gypsum and additives for grinding to produce finished cement. Its process is relatively simple and usually does not involve the calcination of clinker. The main equipment is a cement mill (such as a ball mill or vertical mill) and supporting powder conveying equipment, packaging system, etc. The core task of a cement grinding station is to optimize grinding efficiency and improve the final performance of cement. In summary, a cement production line is a comprehensive cement manufacturing process, while a cement grinding station only handles the grinding of clinker and the packaging of finished cement.
Improving the production efficiency of cement production line can start from equipment, equipment parameters and process flow. In terms of equipment selection, modern equipment such as high-efficiency rotary kiln, preheater, vertical mill, etc. can significantly improve production efficiency.
Tongli's new generation of high-efficiency rotary kiln can shorten the clinker calcination time and increase production capacity, while the vertical mill can better control the grinding fineness of raw materials and finished products and reduce energy consumption. Adjusting the speed of the rotary kiln, the fuel supply of the burner and the air volume of the cooling system can affect the clinker quality and energy utilization during the calcination process.
The DCS system automatically adjusts the operating speed, pressure and temperature of each device to achieve intelligent control of the production line and reduce energy waste. The quality of the process largely determines the upper limit of the efficiency of the cement production line.
For example, by increasing the pre-grinding link of raw materials and using an efficient preheating decomposition system to reduce the fuel consumption in the kiln, the production efficiency can be improved while ensuring the quality of clinker. Optimizing the raw material grinding process and the finished product grinding system can also significantly improve the production speed and cement strength.
5000 TPD CEMENT PRODUCTION LINE TECHNICAL PARAMETERS
No. | Name | Specifications and Technical Performance | Power (kW) | Quantity | Production Capacity (t/h) |
1 | Rotary Stacker | Model: Φ90m continuous composite type | 245 | 1 | 800 |
2 | Reclaimer | Model: Φ90m full-section reclaimer | 1 | 500 | |
3 | Impact Crusher | Model: PCH-1010 | 110 | 1 | 185 |
4 | Coal Crushing Ring Hammer Crusher | Model: CCBD150/15.6; Cantilever Side Stacker | 1 | 250 | |
5 | Raw Coal Pre-blending | Bridge-type scraper reclaimer; Model: CQGQ100/25 | 1 | 100 | |
6 | Combined Pre-blending | Side Cantilever Stacker; Model: DB300/13.1 | 30 | 1 | 250 |
7 | Mixed Material Crushing | Hammer Crusher; Model: PC-1609 | 110 | 1 | 50~70 |
8 | Raw Material Grinding | Roller Mill; Flow Rate: 850,000 m³/h | 3900 | 1 | 400 |
9 | Circulation Fan | 3800 | 1 | ||
10 | Humidification Tower | Specification: Φ9.5×39m; Handling air volume: 840,000 m³/h | 1 | ||
11 | High-Temperature Fan | 2500 | 1 | ||
12 | Kiln Tail Precalciner | SC: 1-Φ5300mm; MC: 1-Φ7700mm | 1 | ||
13 | Rotary Kiln | Main transmission speed: 0.39~3.948 rpm | 630 | 1 | 191.67 |
14 | Grate Cooler | Model: CRJ3-9; Effective grate area: 133.056 m² | 1 | ||
15 | Kiln Head Heat Exchanger | Handling air volume: 580,000 m³/h | 9×22 | 1 | |
16 | Kiln Head Exhaust Fan | Flow rate: 640,000 m³/h | 900 | 1 | |
17 | Air-Swept Coal Mill (Tube Mill) | Capacity: 41 t/h | 1400 | 1 | 41 |