TONGLI provides ball mill grinding station systems with a capacity of 150 thousand tons/year to 2 million tons/year
TONGLI ball mill grinding station is an efficient and modern grinding system, widely used in cement, mining and other industries. The ball mill, as the core equipment, adopts optimized lining plates and high-chromium steel balls to ensure efficient grinding and uniformity of product particle size. The output of a single machine can reach 30-150 tons/hour. It adopts the internationally advanced roller crusher + high-fine combined grinding production process. It has advanced technology, high output, stable quality, high capacity utilization, and high labor productivity. All economic and technical indicators and environmental protection indicators have reached China's advanced level. Main equipment: 1 high-fine ball mill with a diameter of 2.6mX13m, 1 high-fine ball mill with a diameter of 3.8mX13m + 140-80 roller press, and dust removal equipment supporting the main machine. The grinding station has good environmental performance, and the high-efficiency dust removal system equipped significantly reduces dust emissions, meeting international environmental standards.
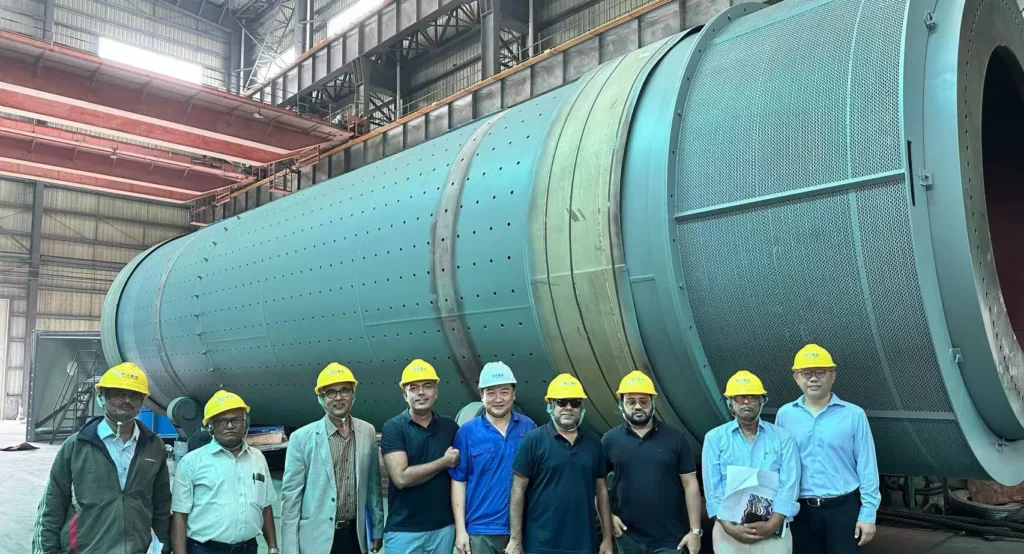
PRODUCTION LINE EQUIPMENT LIST

Tongli's cement ball mill can grind cement clinker to a fineness of 3000~5000 cm²/g. By precisely controlling the speed, load, temperature and other parameters during the grinding process, it can efficiently process cement clinker, minimize energy consumption and improve production efficiency.
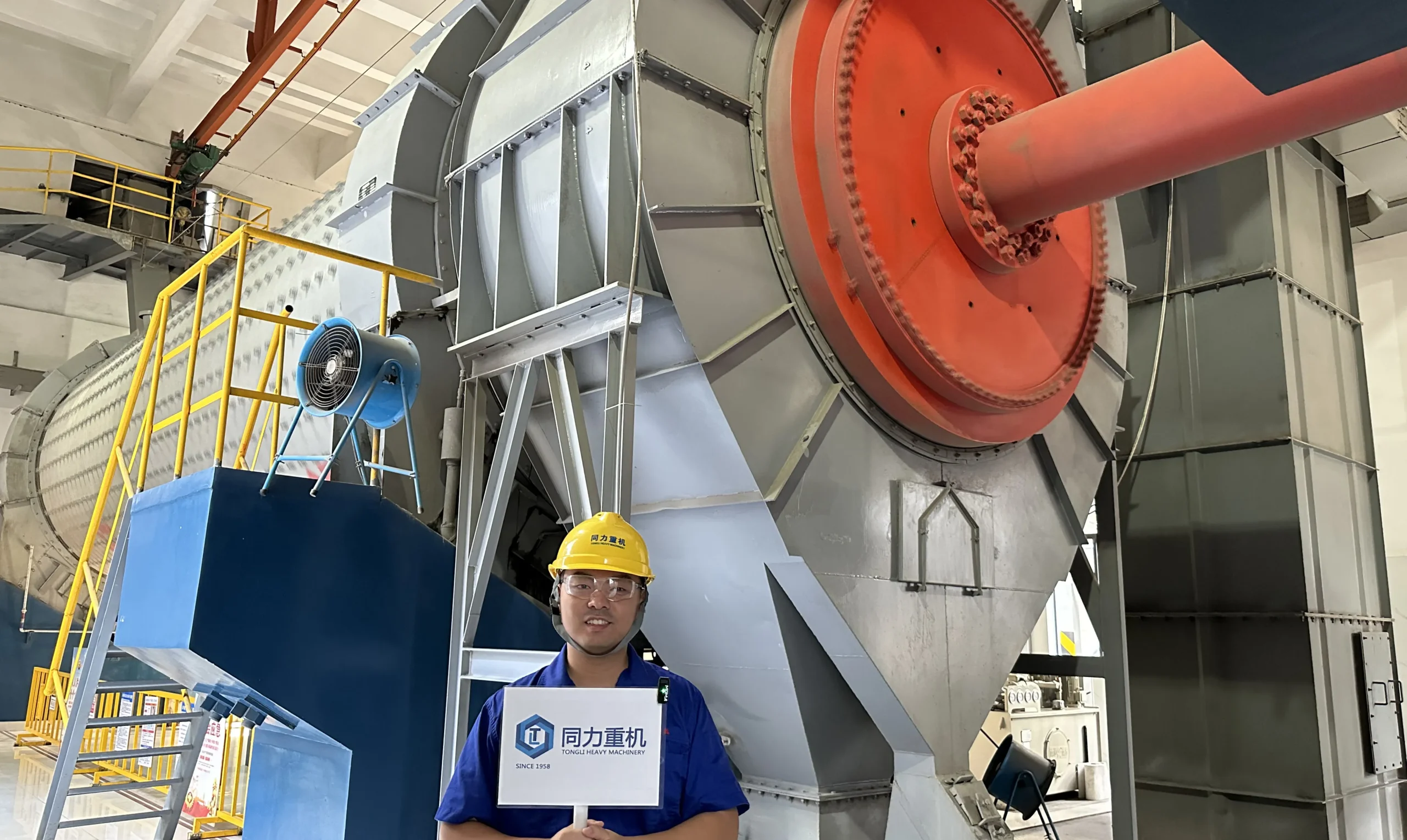
The raw material ball mill can grind limestone from coarse material to a fineness of 200~400 mesh. By optimizing the grinding media and rotation speed, it can efficiently mix and grind limestone and other raw materials (such as clay, iron ore, etc.) to the required uniform fineness, thereby improving the burning quality of cement clinker.
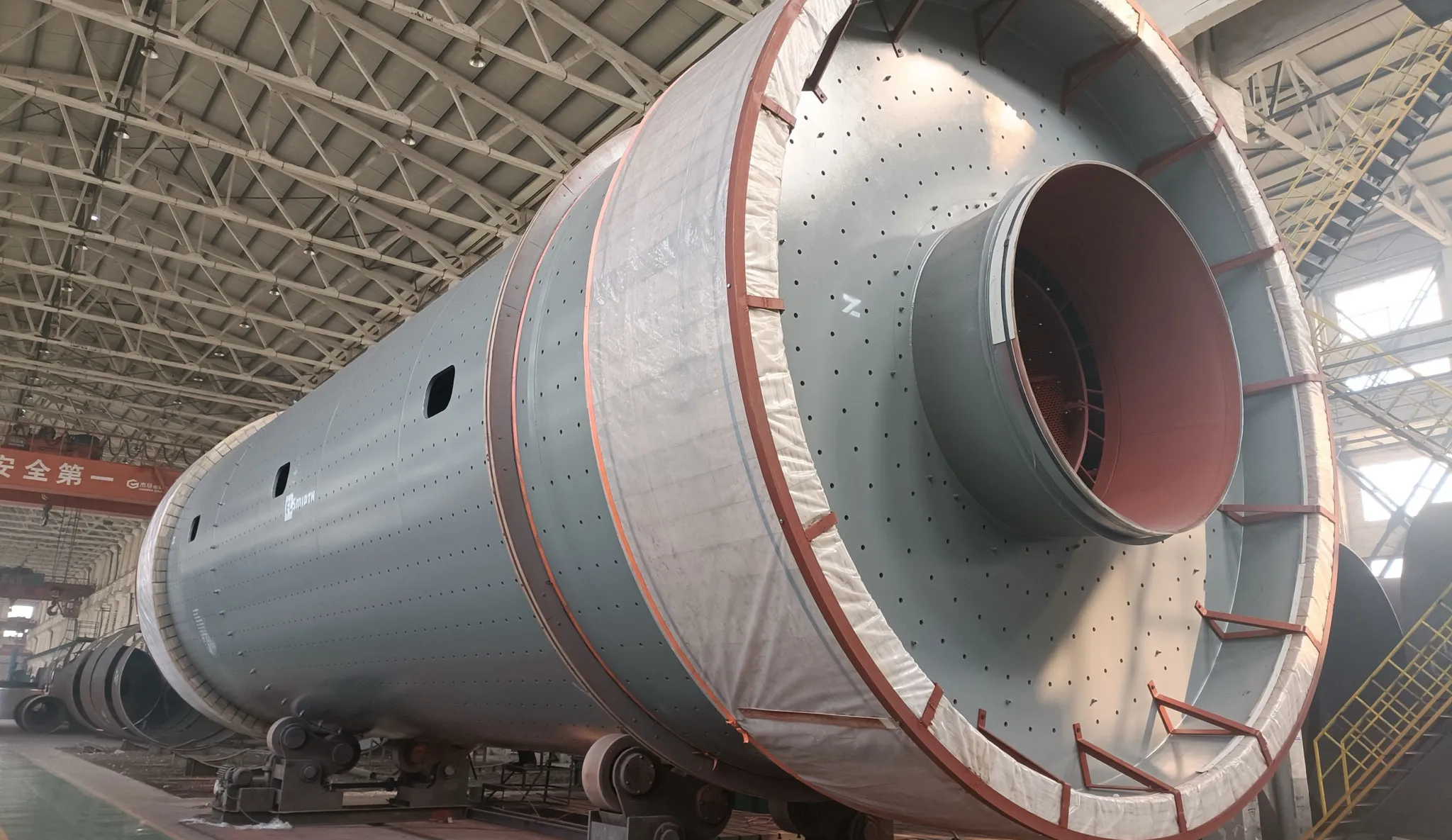
The coal ball mill adopts efficient grinding media and advanced technology to process various types of coal, including anthracite, bituminous coal, lignite, etc. After fine grinding, the coal powder is refined to a particle size suitable for combustion to improve combustion efficiency and calorific value utilization.
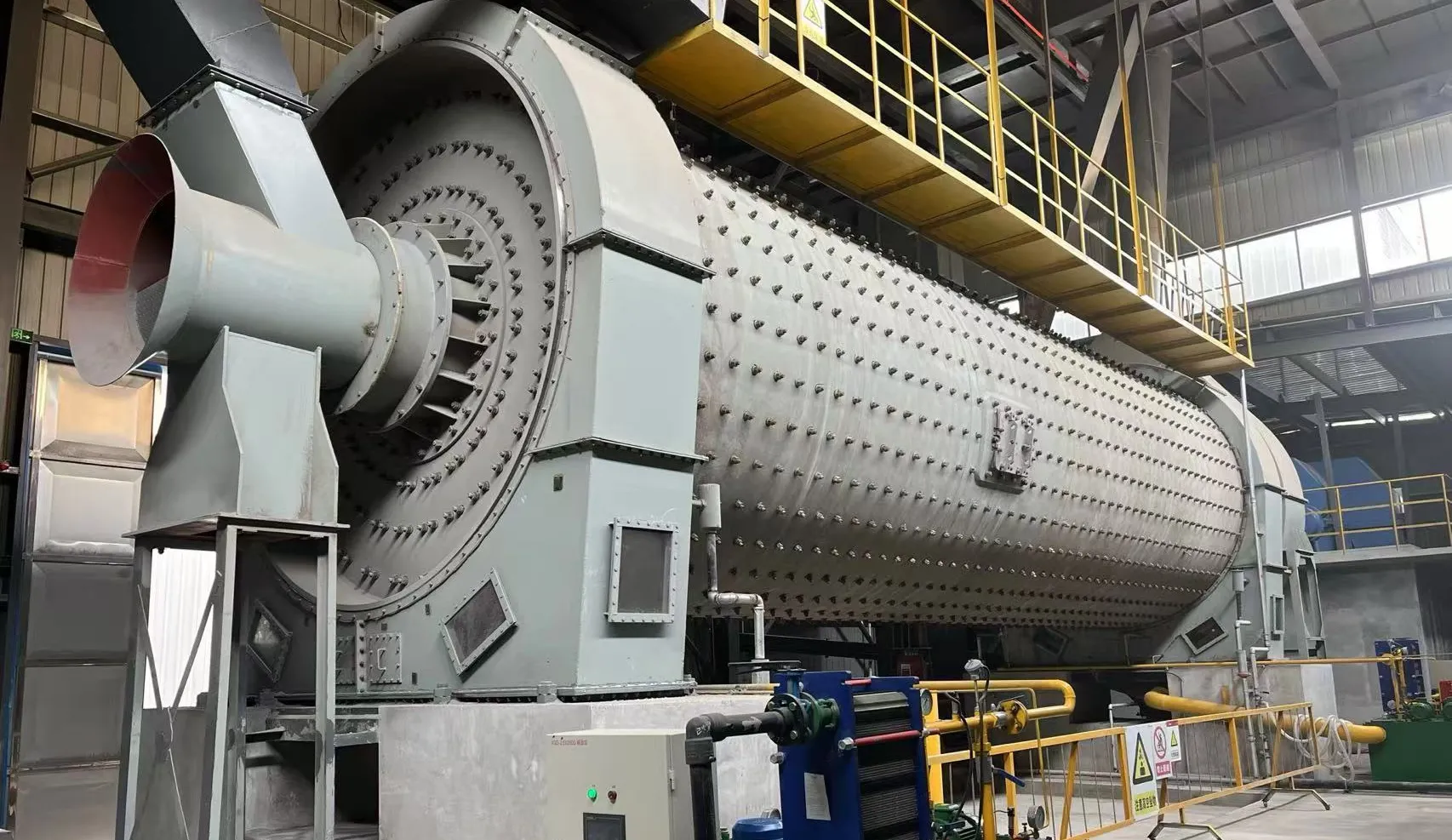
Slag ball mill can use a variety of slag, such as blast furnace slag, steel slag, silica fume, bauxite slag, etc. After being ground, these slags can be used as cement additives to produce slag cement or composite cement. Slag has good activity and can effectively improve the strength, impermeability, durability and other properties of cement.
NPK PRODUCTION LINE ADVANTAGES
Optimize the grinding media ratio to make the product fineness re
Use grinding balls of different diameters, ranging from 15 to 150 mm, to improve grinding and grading efficiency
Bag dust collectors can reduce dust emission concentrations to below 30mg/m³, meeting environmental standards
Use multi-stage crushing equipment to improve material crushing efficiency
The cyclone separator efficiently separates qualified products from coarse particles
Select steel balls according to material characteristics to improve grinding effect.
Optimize process design to improve processing capacity per unit time.
High chromium alloy lining is durable and reduces equipment wear.
VERTICAL MILL GRINDING PROCESS
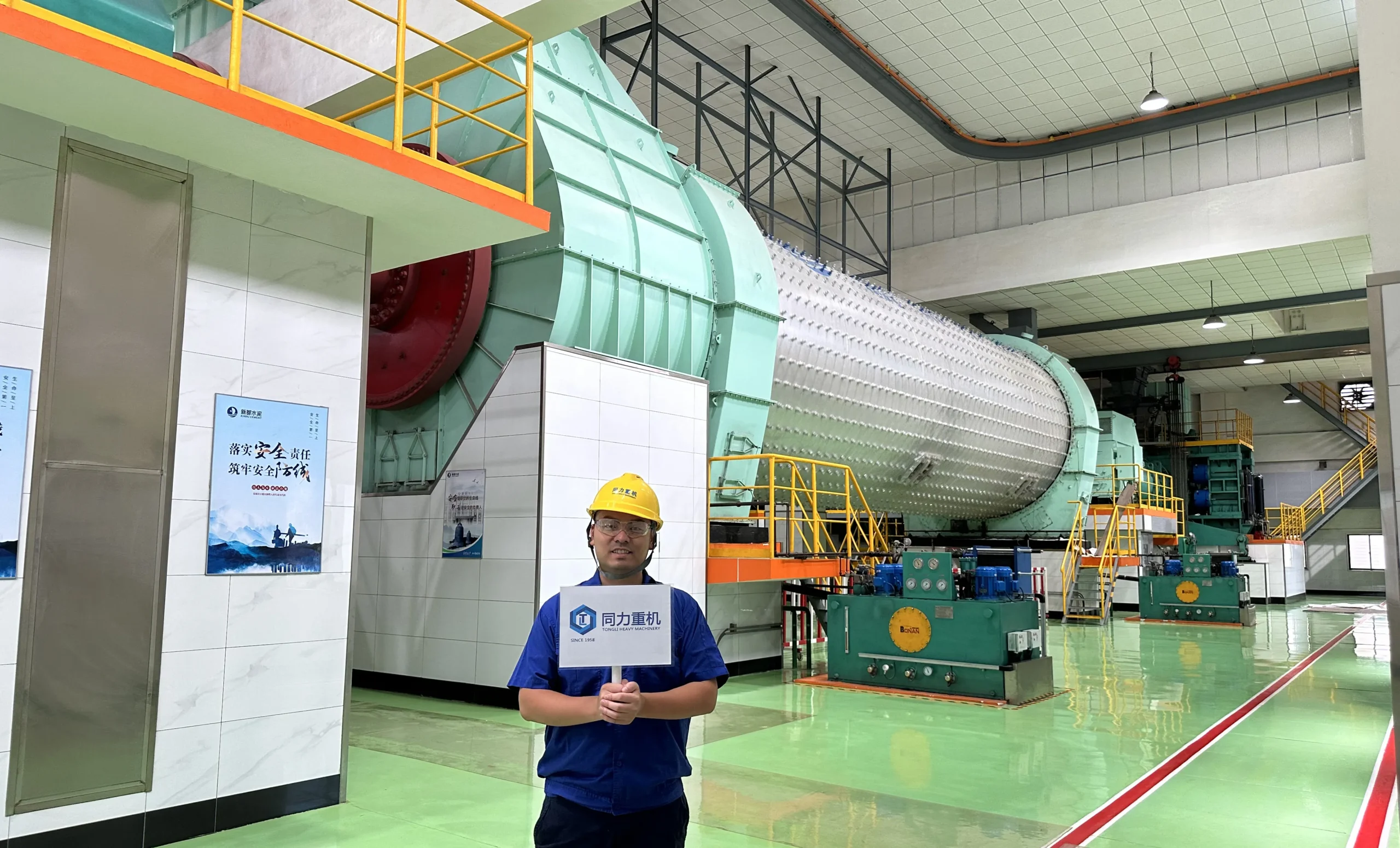
Crushing
Crushing is the first step of the ball mill grinding station. Raw materials usually enter in large pieces and need to be initially crushed by a jaw crusher or a cone crusher. In this process, large pieces of material are crushed into smaller particles, usually gradually reducing the particle size through multi-stage crushing equipment. The purpose of crushing is to control the size of the raw materials within the range that the ball mill can handle and improve the efficiency of subsequent grinding. In addition, the selection and adjustment of the crushing equipment will also affect the particle size uniformity and production efficiency of the material.
Grinding
Grinding is the core process of the grinding station. The crushed material is fed into the ball mill. The rotating cylinder of the ball mill is equipped with media such as steel balls. When the cylinder rotates, the steel balls impact and grind the material through gravity and centrifugal force. The fineness of the grinding can be controlled by adjusting the speed of the ball mill, the filling ratio of the steel balls, and the residence time of the material in the mill. This process not only needs to ensure that the material reaches the required fineness, but also considers the energy consumption and wear of the equipment.
Classification And Collection
The ground material needs to be separated by grading equipment. Cyclones or sifters are usually used to separate qualified fine powder from larger particles. Qualified fine powder is collected for downstream processes or direct application, while particles that do not meet the fineness requirements are returned to the ball mill for re-grinding. Accurate classification not only improves product quality and consistency, but also optimizes resource utilization and reduces waste.
Dust Removal
The grinding process generates a lot of dust, so the dust removal system is particularly important. Bag filters and electrostatic precipitators are usually used to capture and remove dust particles from the air to keep the working environment clean. The effective operation of the dust removal system can significantly reduce dust emissions, protect worker health, and meet environmental regulations. Regular maintenance and inspection of dust removal equipment is also key to ensure its long-term operation.
Control
Modern ball mill grinding stations are equipped with automated control systems to improve production efficiency and stability. By installing sensors, these systems can monitor various process parameters such as equipment load, material flow and particle size in real time. Operators can make real-time adjustments and optimizations through control panels or computer terminals. Automated control not only reduces manual intervention, but also reduces operating errors and improves overall production efficiency.
VIDEO
WHY CHOOSE US
The cement production line is efficient, reliable, and provides consistent quality. Customer service and support are excellent. We're highly satisfied and would recommend it.
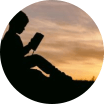
CFO
The cement production line is efficient, reliable, and provides consistent quality. Customer service and support are excellent. We're highly satisfied and would recommend it.

CEO
The cement production line is efficient, reliable, and provides consistent quality. Customer service and support are excellent. We're highly satisfied and would recommend it.

CEO
The cement production line is efficient, reliable, and provides consistent quality. Customer service and support are excellent. We're highly satisfied and would recommend it.

CEO
FAQ
Ball mill grinding stations are mainly used for grinding and processing materials such as ores, chemicals, and ceramic raw materials. The core is a ball mill, which achieves material refinement through rotation and the impact and grinding of steel balls. It is commonly used in cement, silicate products, building materials, and chemical industries.
Traditional grinding methods are inefficient, while ball mills can significantly improve grinding efficiency and product fineness. The design of a ball mill grinding station enables it to handle large-scale materials and adjust product particle size according to demand.
In addition, the grinding station can integrate other equipment, such as classifiers and dust removal devices, to improve overall production efficiency and environmental performance. By optimizing the process flow and equipment configuration, the ball mill grinding station can bring significant economic benefits and product quality improvement to the enterprise.
The capacity of a ball mill grinding station mainly depends on the equipment specifications, raw material characteristics and process parameters. Generally speaking, the capacity of a small grinding station ranges from tens to hundreds of tons per day, while a large grinding station can reach a production capacity of thousands of tons per day.
Equipment specifications, such as cylinder diameter and length, rotation speed, steel ball size, etc., will affect the capacity. At the same time, the hardness, humidity and feed particle size of the material will also directly affect the grinding efficiency and output.
In order to optimize the capacity, the grinding station is usually designed with material characteristics and target product requirements in mind. The capacity can be maximized by rationally configuring the equipment and process flow. In addition, the introduction of modern automated control systems can further improve the efficiency and stability of the production line.
A ball mill grinding station consists of several key components, including the ball mill host, feeding equipment, discharging equipment, grading system, dust removal system and control system. The ball mill host is the core and is responsible for grinding the material.
The feeding equipment is responsible for evenly conveying the material to the ball mill entrance to ensure continuous production flow. The discharging equipment conveys the ground material to the next link.
The grading system usually uses a cyclone separator or screening equipment to separate qualified products from larger particles.
The dust removal system is used to control dust emissions to ensure environmental compliance and a clean working environment.
The integrated control system integrates automated control technology to achieve efficient management and real-time monitoring of the entire grinding station. The various components work together to ensure efficient and safe operation of the grinding station.
There are many ways to improve the grinding efficiency of ball mill grinding station. First of all, choosing the right size and proportion of steel balls is the key. Steel balls of different particle sizes can increase the contact area and impact force during the grinding process.
Secondly, optimize the rotation speed and filling rate to ensure the reasonable flow of materials in the cylinder. In addition, adjusting the feed particle size and uniformity is also an important factor in improving efficiency.
For grinding stations, a grading system can be introduced to separate the fine powder that has reached the standard in time to reduce over-grinding. The automated control system can monitor and adjust the grinding parameters in real time to maintain the best operating state.
Through regular maintenance and equipment upgrades, wear and equipment failures can also be reduced, and overall production efficiency can be improved.
The degree of automation of modern ball mill grinding stations can be customized according to production needs. From basic automation control to complex fully automated systems, grinding stations can achieve multi-level automated management.
Basic automation systems include automatic feeding, discharging and simple parameter monitoring, while advanced automation systems integrate functions such as real-time data acquisition, intelligent control, remote monitoring and process optimization.
Through the automation system, operators can monitor the equipment operation status and production parameters in real time, adjust process conditions in time, and ensure the continuity and stability of production.
In addition, highly automated grinding stations can reduce manual participation, reduce labor intensity and human errors, and improve production efficiency and product quality. Therefore, according to the production scale and management needs of the enterprise, the reasonable configuration of the automation system is an important factor in improving the overall competitiveness of the ball mill grinding station.
Choosing the right steel ball is one of the key factors to improve the grinding efficiency of ball mill grinding station. First of all, it is necessary to select the appropriate steel ball diameter according to the hardness, particle size and specifications of the material to be ground. Generally speaking, the harder the material, the larger the diameter of the required steel ball.
Secondly, the material of the steel ball also needs to be considered. Wear-resistant materials such as high manganese steel and chrome steel are usually used to extend the service life of the steel ball.
In addition, the proportion of steel balls of different particle sizes also needs to be adjusted according to the specific production process to ensure the best grinding effect.
Through scientific steel ball selection and reasonable configuration, the ball mill can achieve higher grinding efficiency, reduce over-grinding, and improve the fineness and uniformity of the product.
BALL MILL GRINDING STATION TECHNICAL PARAMETERS
Item | Production Capacity (t/h) | Specification | Power | Quantity (sets) |
Jaw Crusher | 50~100 | 1000 x 1200 mm | 90 kW | 1 |
Cone Crusher | 40~80 | 1650 mm | 110 kW | 1 |
Ball Mill | 20~50 | 3.2 x 13 m | 800 kW | 1 |
Cyclone Separator | 20~50 | Diameter 3500 mm | 22 kW | 1 |
Bag Filter | - | Capacity 50,000 m³/h | 55 kW | 1 |
Bucket Elevator | 30~50 | TH500 x 20 m | 15 kW | 1 |
Belt Conveyor | 30~60 | Width 1000 x 50 m | 11 kW | 1 |
Automatic Control System | - | PLC Control | - | 1 |
Mill Liners | - | High Chromium Alloy | - | - |
Steel Balls | - | Φ20-Φ120 mm | - | - |