Tongli provides ball mill and vertical mill grinding systems for various raw materials of cement additives such as ground granulated blast furnace slag and steel slag.
Granulated blast furnace slag (GGBFS) is a valuable by-product of the iron and steel-making process. It is produced by rapidly cooling molten slag from a blast furnace using water or steam, resulting in a granular, glassy material. GGBFS is widely utilized in the cement industry to enhance the properties of concrete. The GGBFS vertical roller ball mill is a grinding system designed for processing GGBFS into fine powder, known as slag powder. This mill features high grinding efficiency, low energy consumption, and excellent adaptability, making it ideal for large-scale production. It employs advanced technology to ensure uniform particle size distribution and high fineness, critical for the performance of slag powder in concrete applications. The GGBFS (fineness: 4200-4500cm2/g) produced by tongli vertical roller mill is used to replace clinker in traditional cement production, where the usage ratio of GGBS is usually 10-15% and 20-25% respectively.
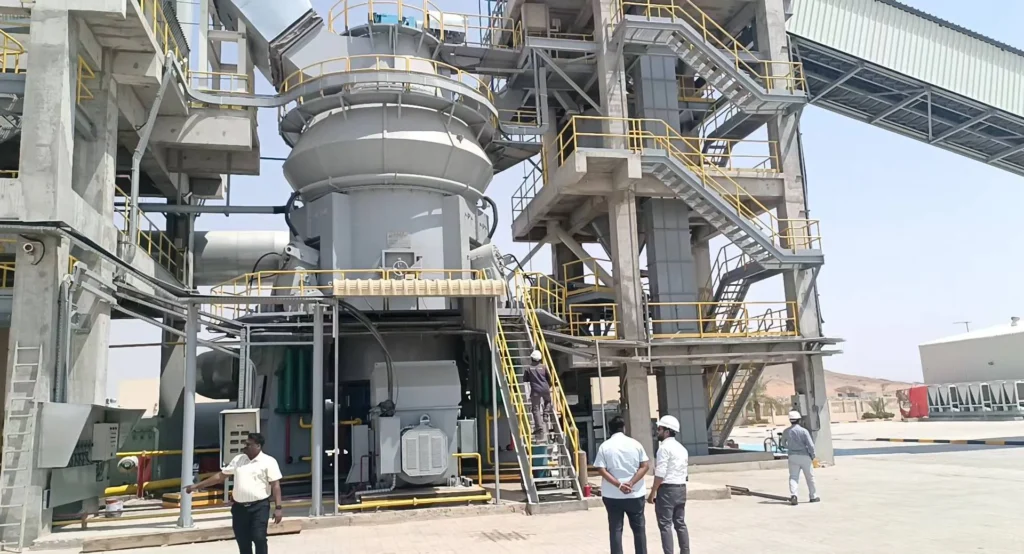
GGBFS PRODUCTION LINE EQUIPMENT LIST
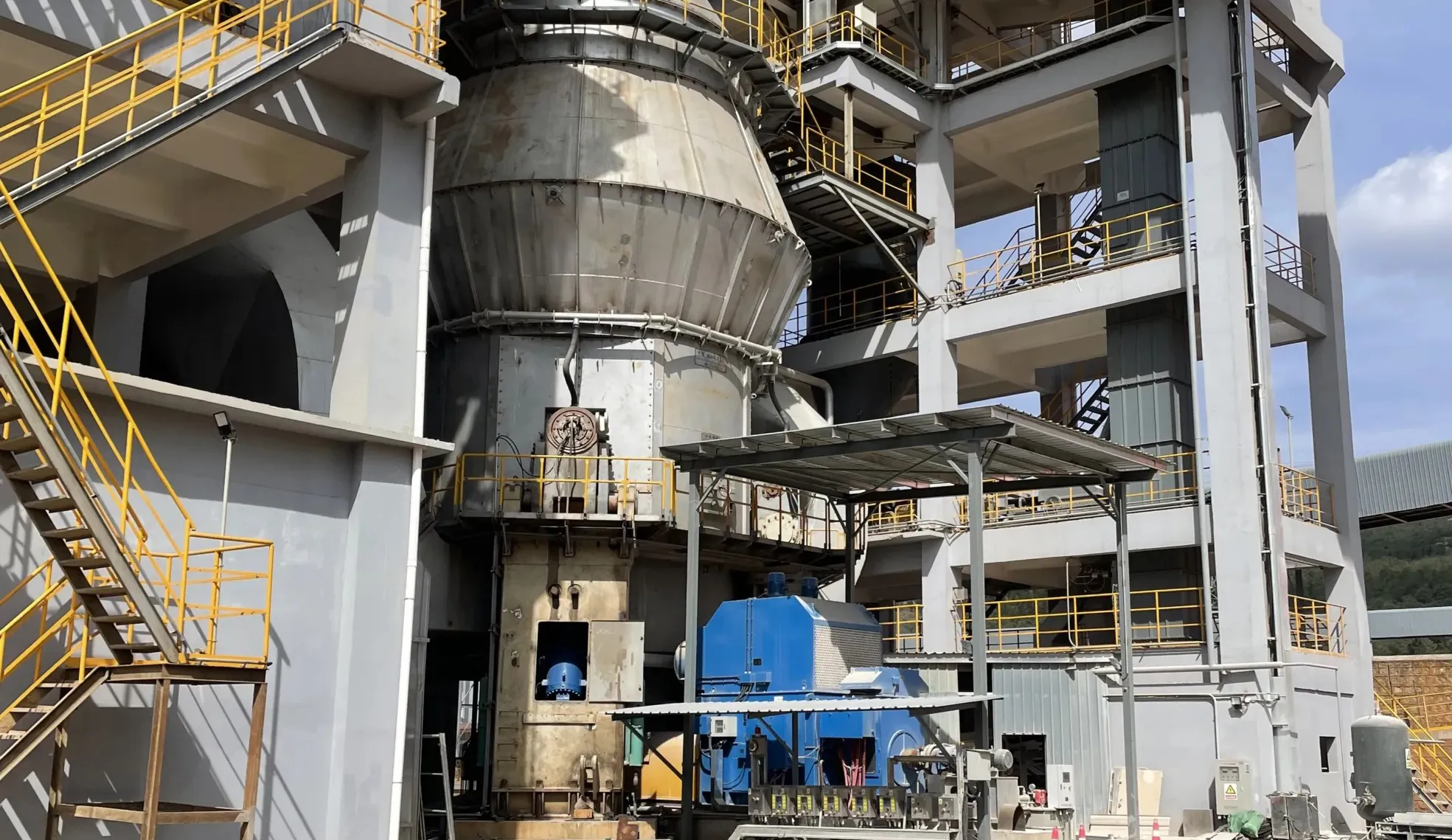
Optimize your production process with our GGBFS Vertical Roller Mill, tailored for grinding ground granulated blast furnace slag. This advanced mill ensures high productivity, consistent particle size, and reduced energy usage, making it ideal for producing premium cement and concrete materials.

Explore our Ground Granulated Blast Furnace Slag Vertical Roller Mill (GGBFS VRM), designed to efficiently grind GGBFS into fine powder. Enhance cement quality and durability with this innovative VRM, featuring low energy consumption and environmental benefits.
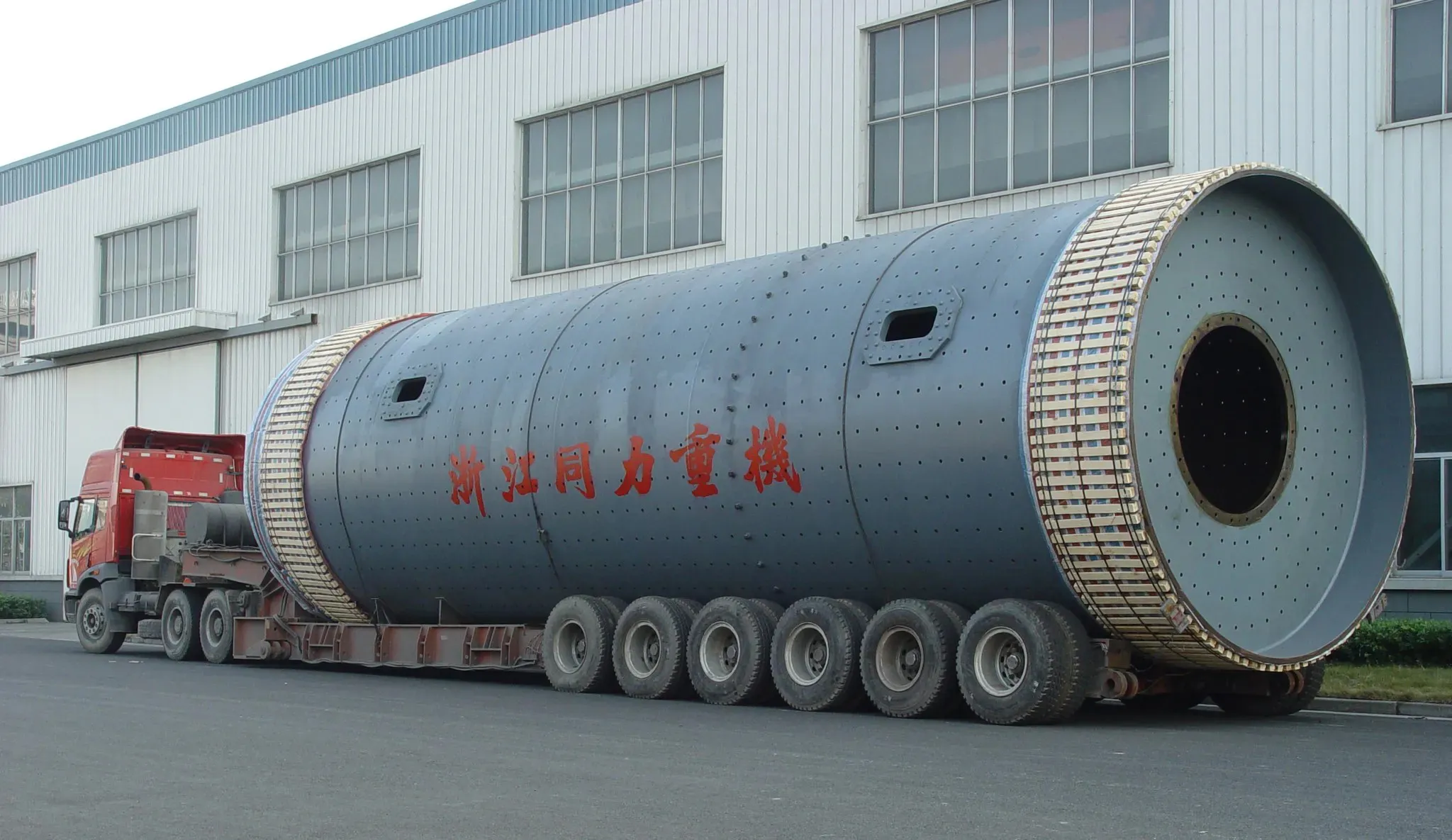
Our Granulated Blast Furnace Slag Ball Mill offers precision grinding and processing for blast furnace slag, turning it into valuable raw material for cement production. Achieve superior particle size distribution and improved product quality with our advanced milling technology.
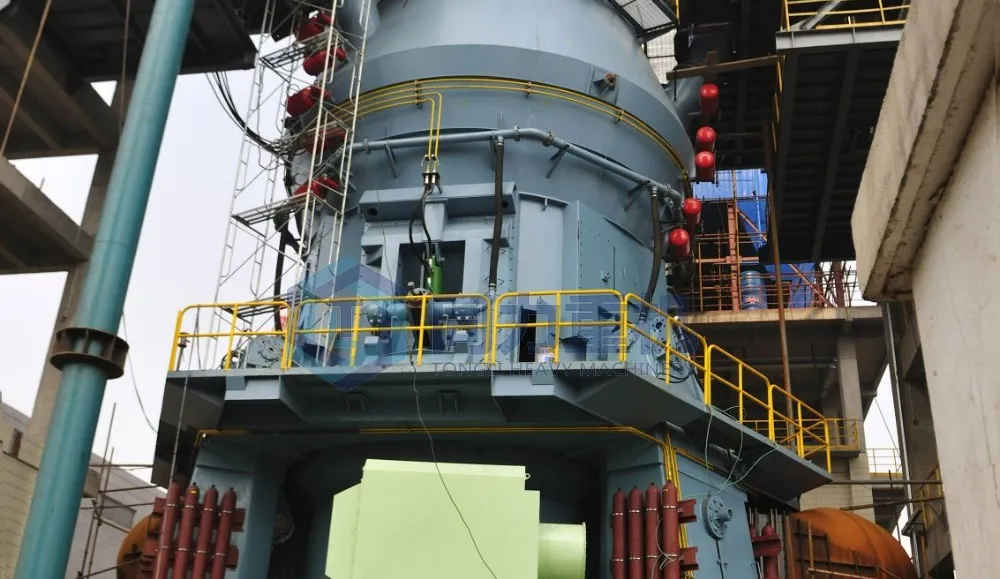
Discover the power of our Steel Slag Vertical Milling Machine, designed for high-efficiency grinding of steel slag. With advanced technology and robust construction, it ensures optimal performance and reduced energy consumption, ideal for producing high-quality materials for cement and construction industries.
GGBFS Grinding Plant ADVANTAGES
The GGBFS mill is designed with a high-efficiency grinding system, which increases the grinding efficiency by more than 30% compared with traditional ball mills. In addition, its automated control system can achieve precise particle size control.
Traditional ball mills consume 75-80 kWh of electricity to produce 1 ton of slag powder, after adopting vertical roller mill, the electricity consumption per ton of slag powder is only 42-45 kWh, saving 33-35 kWh of electricity.The energy-saving effect of GGBFS mill is very significant.
GGBFS mills have strong adaptability and can process slags of different sources and compositions, including blast furnace slag, steel slag and other industrial wastes, ensuring that they can operate efficiently under a variety of production conditions.
Effectively reduce environmental pollution, the vertical mill adopts an internal negative pressure system, which can effectively control dust spillage. The equipment runs at a low speed, stable operation, and noise is less than 85dB(A), which provides a strong guarantee for green and environmentally friendly production.
Promote the resource utilization of slag, the total amount of slag produced worldwide each year exceeds 90 million tons, while the utilization rate of steel slag was less than 25% in 2013. The total amount of waste steel slag has exceeded 1.279 billion tons. Converting waste slag into high-value micropowder products helps to alleviate environmental pressure.
High return on investment: The widespread application of GGBFS mills has driven the rapid growth of market demand for slag micropowder. In recent years, investment in slag production lines has become a new favorite in the market. A complete production line can usually recover its costs within 3 to 5 years.
Efficient iron removal: Tognli vertical mill can effectively separate the iron in the slag through discharge portal, with a separation rate of not less than 1%. The separated iron not only protects the equipment from wear, but can also be reused as an additional resource to create more income for the company.
Compared with traditional ball mills, maintenance costs can be reduced by more than 20%, while reducing production losses caused by equipment downtime.Vertical mills operate stably, wear parts such as grinding rollers and grinding discs have a longer service life, and maintenance cycles are significantly extended.
GRANULATED BLAST FURNACE SLAG GRINDING PROCESS

Raw material feeding
In the GGBFS grinding line, slag raw materials can be fed separately according to their moisture conditions. For slag with a high moisture content, it can be fed into the mill separately, and the dried slag can be added directly as dry material. This flexible feeding method allows the production line to adapt to the characteristics of raw materials under different conditions, ensuring the stability and efficiency of the process.
Grinding and drying
The raw materials are ground and dried in the ZJTL vertical roller mill. The mill uses its efficient grinding system to grind the slag to different fineness requirements, up to 6500 cm²/g (specific surface area, Blaine). At the same time, the hot air system cooperates with the internal negative pressure operation to effectively complete the drying of the material. This integrated grinding and drying process not only saves energy, but also ensures the consistency of product quality.
Powder classification
The ground slag powder is initially separated by the classification system inside the mill, and then the powder is separated from the process airflow through the dust removal filter. The dust removal system can effectively capture more than 99% of dust particles, ensure the clean emission of process gas, and further reduce environmental pollution. The separated gas is sent to the fan, while the slag powder enters the subsequent storage and packaging link.
Gas circulation and emission
Part of the process gas treated by the fan will flow back to the mill to support the grinding and drying process, and the part that is not returned will be discharged through the exhaust gas chimney. Through reasonable gas distribution design, the production line can significantly reduce energy waste and effectively control exhaust gas emissions to meet environmental protection standards.
External material circulation
The mill is equipped with an external material circulation system to return substandard materials to the mill for re-grinding. This circulation design not only reduces the pressure drop inside the mill, but also allows the mill to be quickly emptied through the external system during equipment maintenance, greatly improving the convenience and safety of maintenance work.
Iron separation
When grinding blast furnace slag, the iron particles in the slag are effectively separated by a magnetic separation device. The separated iron particles can be used as a by-product for other industrial purposes without causing wear to the mill. This link not only protects the equipment, but also increases additional economic benefits.
VIDEO
WHY CHOOSE US
After using Tongli’s GGBFS grinding system, we have reduced energy consumption while improving product output and quality. Our electricity consumption per ton of slag has been reduced by 33~35kWh. , and the specific surface area of the product is stable at 6000 cm²/g, which is very rare in the market.
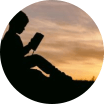
Cemex VP
We chose Tongli’s GGBFS grinding system. This system not only helps us effectively control the amount of slag used in cement, but also improves the strength and durability of concrete.

Concrete Plant CEO
Tongli’s GGBFS grinding system provides us with a flexible operating platform that allows us to adjust the product fineness according to the specific needs of different projects.

Construction Manager
We felt Tongli vrm significant advantages in environmental protection. The system’s internal negative pressure operation and efficient dust removal equipment ensure that the exhaust gas emissions during the grinding process meet the local environmental protection standards.

CEO
FAQ
Cement slag is a widely used cementing material in the construction industry, with huge annual demand. Cement slag mill is a special equipment for processing slag powder. How to choose between ball mill and vertical mill? Cement slag powder usually needs to be ground to 420 scale. The higher the fineness, the better the activity. However, fineness is directly related to energy consumption. The finer the grinding, the higher the power consumption cost, which has an impact on the profit.
Energy consumption is an important indicator of cement slag mill and a focus of grinding companies. Compared with ball mill, vertical mill has more advantages in energy consumption, which can save more than 30% of power consumption, thereby reducing the ton cost of cement slag powder.
In addition to energy consumption, there are also differences in the floor space occupied by ball mill and vertical mill. Due to its longitudinal structure, the vertical mill has a small base area and does not require a large site like a ball mill. In addition, the vertical mill can be installed in the open air and does not necessarily require a factory building. Therefore, in terms of factory building investment, the vertical mill is more economical. In terms of environmental protection, the noise generated by ball mills is usually louder, while that of vertical mills is relatively smaller. The grinding and screening of ball mills is segmented, while that of vertical mills is integrated, and the negative pressure system operates, with basically no spilled dust, which is more environmentally friendly.
In addition, the later maintenance cost of vertical mills is lower. The grinding media in ball mills, such as steel balls, need to be replaced in time, and each replacement is a cost, while the grinding rollers of vertical mills can be turned over and used, and can be repeatedly subjected to wear-resistant surfacing, without the need for frequent replacement, which greatly reduces the cost. The industry trend of cement slag mills is more inclined to vertical mills, and many mineral powder stations have eliminated ball mills and switched to vertical mills. The LM series vertical mill is an ideal choice for cement slag mills, which not only has a large processing capacity and high grinding efficiency, but also has stable quality, energy saving and environmental protection.
In response to the grinding needs of granulated blast furnace slag powder (GGBS), tongli provides a variety of advanced grinding system options, including open-circuit and closed-circuit grinding systems with ball mills as the core equipment, vertical roller mill (VRM) systems, and final grinding systems and semi-final grinding systems with roller presses as the core equipment. We tailor the most suitable grinding solutions for customers based on their production capacity, energy consumption and local emission standards.
1. Vertical roller mill GGBFS grinding system
As a mature technology in the field of slag grinding, the vertical roller mill system integrates drying, grinding and powder selection. With its advantages of simple system, high single-machine output, low energy consumption and strong reliability, it has gradually become the preferred solution in the industry. The unit power consumption of the vertical roller mill system is about 45kWh/t, and the specific surface area also reaches 450m²/kg. Compared with other grinding systems, it not only has lower energy consumption, but also has better finished particle shape. Since the late 1980s, research and practice around the world have shown that the vertical mill system has achieved dual maturity in technology and economic benefits in the field of slag grinding. Tongli has a GGBFS vertical mill system under commissioning in Dubai. If you are interested, you can contact Tongli's sales for field investigation and visit.
2. GGBFS ball mill closed-circuit grinding system
The ball mill open-circuit system is an early process for slag grinding. The material enters the ball mill directly after metering, and the finished product is output after grinding. Due to its simple process flow, low requirements for operating technology, and low initial investment cost, it is widely used in the early slag grinding field. The unit power consumption of this system is about 100kWh/t, and the specific surface area of the ground slag is 450m²/kg. Despite the advantages of mature technology, easy operation and low cost, its low grinding efficiency, high energy consumption, and small unit production capacity have gradually made it unsuitable for modern enterprises' requirements for high efficiency and environmental protection.
3. GGBFS Ball Mill Open Circuit Grinding System
In contrast, the ball mill closed circuit system significantly improves the grinding efficiency by adding a powder selection device, and can accurately control the fineness of the finished product by adjusting the powder selection efficiency. This process is effective in reducing the phenomenon of over-grinding of materials, especially for customers with high requirements for the quality of finished products. Its unit power consumption is about 75kWh/t, and the specific surface area is also 450m²/kg. However, due to the high process complexity of the closed-circuit system, the operating cost is still high, and the single-machine capacity is low, which limits its application scenarios.
4. GGBFS Roller Press Grinding System
The roller press system is an important breakthrough in the slag grinding process in recent years. It makes full use of the efficient grinding mechanism of the roller press and shows excellent energy efficiency advantages. Depending on the configuration, the roller press can be used in the final grinding system or the semi-final grinding system. The unit power consumption of the system is about 50~60kWh/t, and the specific surface area of the ground slag is 450m²/kg. Although the roller press system has a large cyclic load and may have equipment vibration problems, its high efficiency and energy saving characteristics and low operating costs make it an ideal choice for some customers.
5. Why use granulated blast furnace slag
Granulated blast furnace slag powder is a by-product obtained by water quenching of ironmaking blast furnace slag, and its application prospects are very broad. Its main components include active minerals such as C₂As, CAs₂, CS and C₂S, which are in a microcrystalline state, highly active, and contain 80% to 90% of glass phase. Studies have shown that ground slag powder can not only significantly improve the performance of cement and concrete, but also effectively improve their durability and workability, while reducing production costs.
6. The value of granulated blast furnace slag
In the modern construction industry, slag powder can be used as a mixture of ordinary silicate cement and slag cement, and can also be used as a high-performance admixture for concrete. Its low price and excellent performance make it a core product in the environmentally friendly building materials market. With the increasing requirements for environmental protection and energy conservation, the application of granulated blast furnace slag will continue to expand in the future, and its market value will continue to increase whether as an intermediate product or a terminal commodity.
Ground-granulated blast-furnace slag (GGBS) has become an essential material in modern construction, valued for its exceptional performance and environmental benefits. Its unique properties make it a preferred choice for improving concrete workability, durability, and sustainability, while meeting the growing demands for eco-friendly building practices.
Ease of Handling
One of the standout features of GGBS is its ease of use in concrete applications. Its inclusion in concrete mixes enhances handling, pumping, and placement, even in challenging weather conditions. The improved cohesion of GGBS-modified concrete allows for better pumping properties, reduces the risk of segregation, and simplifies compaction, resulting in a denser and more durable structure. Moreover, less water is required to achieve the desired workability, further contributing to its efficiency and practicality.
Chemical Advantages
The chemical composition of GGBS plays a vital role in improving the performance of concrete. Its lower free lime content reduces permeability and fosters long-term strength development, enhancing the overall durability of structures. Additionally, the reduced alkalinity of GGBS-modified concrete minimizes the risk of alkali-silica reactions, a common cause of structural degradation. Furthermore, the lower heat of hydration helps prevent early-age thermal cracking, making GGBS particularly advantageous for large-scale or mass concrete pours.
Extended Working Window
Incorporating GGBS into concrete mixes also extends the working window during construction. Its longer setting time provides more flexibility, allowing for precise finishing and reducing the risk of cold joints. This feature is especially beneficial for large or complex pours, where achieving seamless results is critical.
Sustainability Benefits
Cement production is a carbon-intensive process, generating approximately 176 kg of CO₂ per tonne of concrete. By replacing a portion of traditional cement with GGBS, builders can significantly reduce the environmental impact of their projects. GGBS is a lower-carbon material that can reduce greenhouse gas emissions by as much as 45%, depending on the mix and application. With its reduced embodied carbon, GGBS enables construction professionals to meet increasingly stringent sustainability requirements while enhancing the built environment.
Driving Green Construction in the UAE
The adoption of GGBS has gained momentum in the UAE, driven by sustainability regulations such as the Dubai Green Buildings Regulations (DM Circular no. 198), introduced in 2010. These regulations aim to foster environmentally sustainable development while promoting healthier living environments. GGBS aligns seamlessly with these goals, offering a high-performance, eco-friendly solution that meets both structural and environmental standards.
In conclusion, GGBS is revolutionizing the construction industry by combining performance excellence with sustainability. Its ability to enhance concrete workability, durability, and environmental compatibility makes it an indispensable material for building a better future. By choosing GGBS, the industry can continue to innovate while minimizing its impact on the natural world.
Blast furnace slag is a by-product produced during the blast furnace smelting process. Its main chemical components are CaO, SiO2, Al2O3 and MgO, which contain trace elements such as Ti and S. According to research, changes in Ti content will affect the content of foam slag during the blast furnace slag flushing process. Different blast furnace slag flushing methods result in different cooling rates of blast furnace slag at high temperatures, and the structures of the resulting blast furnace slag are also different. At the same time, the fluctuation of the chemical composition of blast furnace slag itself has a close impact on the drainage of blast furnace slag, the coal consumption and hourly output of slag mill, and the activity of slag powder.
1 Raw materials The chemical composition of blast furnace slag produced by our company's blast furnace and the slag powder produced using the blast furnace slag are shown in Table 1.
2 Blast furnace slag flushing and vertical mill process layout
Our company uses the INBA method and the Minter method to flush blast furnace slag, which is transported to the blast furnace slag material yard by belt. After natural stacking and drying for 72 hours, it is used as the raw material for slag vertical mill. The slag vertical mill model is LM56.3+3 produced by Loesche, Germany, equipped with a hot blast furnace with a heating capacity of 140GJ.
3 Experimental methods
The mineral structure of blast furnace slag under different slag flushing systems was analyzed using a German Bruke D8 Advance X-ray diffractometer. Using a laboratory small mill, 3kg of dried blast furnace slag was ground for 40 minutes, and the specific surface area was measured to characterize the grindability of blast furnace slag. The activity index of slag powder was determined according to the mortar strength ratio method in GB/T 18046-2017 "Granulated blast furnace slag powder for cement, mortar and concrete".
4 Effect of different slag flushing methods on the mineral structure, grindability and activity of blast furnace slag
The mineral composition of blast furnace slag flushed by the Minter method and the INBA method was tested, as shown in Figure 1. It can be seen that the blast furnace slag flushed by the Minter method contains a large amount of grossamite (Ca2Al2SiO7) crystals and a small part of magnesium rhodonite (Ca3MgSi2O8) crystals. Through qualitative analysis, the content of glass is much smaller than that of grossamite crystals, and grossamite crystals inhibit the hydration activity of slag powder. Its activity is mainly generated by the depolymerization of glass in an alkaline environment. By comparison, it can be seen that the slag under the hot water slag flushing system of the Indo-Pakistani method has very little grossamite crystal content, and the crystal form mainly exists in a microcrystalline state, with a high glass content. The grindability and activity index of blast furnace slag produced by the Minter method and the INBA method were tested. Combined with the XRD spectrum in Figure 1 above, it can be seen that the cooling speed of the liquid slag produced by the Indo-Pakistani method is faster, the mineral structure is mainly glass, and it contains higher energy. Its mechanical grinding work is smaller, resulting in its grindability (specific surface area) being 30m2/kg higher than that of blast furnace slag produced by the Minter method, and the 7d and 28d activity indexes being 13% and 12% higher, respectively. The blast furnace slag and slag powder discussed below are all produced by the INBA method.
5 Effect of chemical composition of blast furnace slag on activity
The main structure of slag powder is glass structure. The source of its hydration activity is the energy preserved by rapid cooling of high-temperature liquid slag. It is mainly that Al2O3 in it is activated by Ca(OH)2 in the hydration environment, and the reaction generates C-A-H (aluminum gel structure) with flocculent structure with gelling properties. C-A-H reacts with SO3 in the hydration system to generate AFt (calcium aluminate) with needle-rod shape, which plays a skeleton structure in cement hardening paste and enhances the strength of cement system. The macroscopic characterization is that slag powder is active. Therefore, based on the above analysis, the main factors affecting the activity of slag powder include Al2O3, SiO2 and glass content of slag powder. As shown in Figure 2, the fluctuation of Al2O3 and SiO2 content has a significant effect on the 7d activity index of slag powder. This is because when the Al2O3 content in slag is high, the viscosity of liquid blast furnace slag is high, and it is not easy to form calcium aluminum feldspar microcrystals. At the same time, the main hydration active substance Al2O3 in the glass in slag is high. When the SiO2 content in the slag is high, the activity of the slag will decrease significantly. Therefore, both need to be considered comprehensively.
6 Effect of chemical composition of blast furnace slag on grindability
The grindability of slag is not only affected by its slag flushing method, but also by its chemical composition. The effect of the chemical composition of blast furnace slag on the grindability of slag and the output of the opposite grinding table is analyzed. See Figure 3. It can be seen that: under the same slag flushing method, as the SiO2 content in blast furnace slag increases from 32% to 34%, the specific surface area of blast furnace slag decreases from 420m2/kg to 400m2/kg.
7 Effect of blast furnace slag bulk density on moisture, mill hourly output and coal consumption
The data of blast furnace slag bulk density and moisture from May to June 2018 are statistically analyzed, as shown in Figure 4. It can be seen that from late May to June 2018, the blast furnace slag bulk density showed a continuous downward trend, while the blast furnace slag moisture showed a continuous upward trend, indicating that the blast furnace slag bulk density is directly related to moisture. According to the requirement that the moisture of the blast furnace slag entering the mill is ≤8.5%, it can be concluded from Figure 5 that the corresponding blast furnace slag bulk density critical point is 1060kg/m3. Therefore, the bulk density of blast furnace slag is required to be not less than 1060kg/m3, otherwise it will seriously affect the slag powder hourly output, coal consumption, etc. Figure 6 is a curve of blast furnace slag moisture to slag mill hourly output in May and June 2018. It can be seen that as the slag moisture increases, the mill hourly output decreases. The main reason is that the blast furnace slag moisture increases and the mill operating conditions are unstable. At the same time, due to the increase in the moisture content of blast furnace slag, the coal consumption of slag mill also shows an upward trend. Through calculation, it can be known that for every 1% increase in the moisture content of blast furnace slag, the coal consumption of slag vertical mill increases by about 0.5kg/t.
8 Conclusion
The structure of blast furnace slag punched by INBA method is mainly a glassy structure with high activity, and the blast furnace slag punched by Minter method is mainly a calcium aluminum feldspar (Ca2Al2SiO7) crystal structure with low activity, and the grindability of blast furnace slag punched by INBA method is higher than that of blast furnace slag punched by Minter method. When the stacking density of blast furnace slag is ≥1060kg/m3, after 72h of natural drainage, the moisture content of blast furnace slag can be controlled at 8.5%, which is conducive to reducing the coal consumption of vertical mill and increasing the hourly output. The increase of SiO2 chemical composition in blast furnace slag will reduce the hourly output of slag mill. The chemical component in blast furnace slag that is beneficial to the activity index is Al2O3, and the component that is not beneficial to the activity is SiO2.
Ground Granulated Blast Furnace Slag (GGBS) is a byproduct of the steelmaking process. In addition to iron ore and reducing agents (such as coke) in blast furnace ironmaking, limestone and dolomite are added as fluxes to reduce the smelting temperature. During the ironmaking process, calcium oxide and magnesium oxide combine with impurities in iron ore and ash from coke to form a molten material rich in silicates and aluminates. This melt is rapidly cooled by high-pressure water quenching to form granulated slag. The granulated slag is then ground to produce slag powder (GGBS) with fine particles.
Ground Granulated Blast Furnace Slag mainly exists in an amorphous glassy structure and contains a small amount of crystalline minerals. Due to the high energy state of the glassy structure, GGBS has great potential activity, but it needs to be finely ground to fully exert its advantages. It is an excellent concrete admixture.
1. Chemical composition of granulated blast furnace slag
The main chemical components of GGBS include silicon oxide (SiO₂, about 30-40%), calcium oxide (CaO, about 40-50%), aluminum oxide (Al₂O₃, about 10-15%), magnesium oxide (MgO, about 5-10%), and a small amount of iron oxide and other impurities. Among them, silicon oxide, aluminum oxide and calcium oxide are the main sources of its activity, which directly determine its reactivity in cement and concrete.
The chemical composition of slag from different steel mills or production batches may vary, so in industrial applications, strict composition testing of slag is required to ensure its stable performance.
The main use of slag powder in cement
GGBS is usually used as an admixture in the production of slag cement or directly replaces part of cement, and is widely used in various concrete projects. Its main function is to improve the comprehensive performance of cement and concrete, while reducing production costs and energy consumption.
2. Improvement of cement performance by slag powder
2.1 Improving strength and durability:
The active reaction of GGBS can greatly improve the later strength of concrete. After adding slag powder, the secondary cementitious products generated by the hydration reaction fill the pores in the concrete, significantly improving the compactness and durability of the concrete.
Inhibiting alkali-aggregate reaction
Slag powder can reduce the alkali content in concrete, significantly inhibit alkali-aggregate reaction, reduce the generation of cracks, and thus extend the service life of concrete.
2.2 Anti-seawater erosion performance
Since slag powder can reduce the content of free chloride ions in concrete, its anti-seawater erosion performance is particularly excellent, and it is widely used in marine engineering and coastal area projects.
2.3 Improving workability and impermeability
GGBS can significantly reduce the bleeding of concrete, improve workability during construction, and improve the impermeability of concrete. It is suitable for structural projects with high requirements for waterproofing.
2.4 Reducing environmental impact
Since no additional mineral mining is required during the production of slag powder, its carbon dioxide emissions are much lower than cement production, and it is a green and environmentally friendly building material substitute.
3. Specific effects of various components in slag on cement performance
3.1 Silicon oxide (SiO₂)
Silicon oxide is the main active component of slag powder, which can react with hydration to form calcium silicate gel (C-S-H), significantly improving the later strength of concrete.
3.2 Calcium oxide (CaO)
Calcium oxide is the basic component of cementitious materials, and its content directly affects the activity of slag. If the calcium oxide content is insufficient, the active reaction of slag may be limited; but too high a content may lead to instability, such as volume expansion.
3.3 Alumina (Al₂O₃)
Alumina helps the active reaction of slag powder in low temperature environments, especially significantly improving strength in the early hydration stage. However, too high alumina content may increase the risk of alkali-aggregate reaction, so it needs to be strictly controlled.
3.4 Magnesium oxide (MgO)
A moderate amount of magnesium oxide can improve the crack resistance of concrete, but excessive magnesium oxide may cause expansion problems, thereby affecting the stability of concrete.
3.5 Market prospects of slag powder
As a by-product of the ironmaking industry, granulated blast furnace slag powder has low cost and superior performance, and is a very ideal building material admixture. Globally, with the increasing emphasis on environmental protection and sustainable development, the demand for GGBS continues to grow. Especially in the field of high-performance concrete and green building materials, its application potential is huge.
With the development of grinding technology, such as the mature application of vertical roller mills and roller press systems, the production efficiency and performance of GGBS have been further improved, which is driving it to become an important component of modern building materials.
This article mainly discusses the relationship between the traditional grinding process and the material bed grinding process of cement and slag micro-powder. Since the advent of the mill in 1883, the traditional tube mill grinding process has low efficiency and high power consumption due to factors such as the open grinding space. With the advancement of science and technology, high-efficiency and low-energy consumption processes and equipment represented by material bed grinding technology have become mainstream, such as roller presses, vertical mills, and drum roller mills, which are gradually replacing tube mills. This article compares different grinding processes and their characteristics in detail, including power consumption, system complexity, etc. It also analyzes the performance of the final grinding products of the material bed grinding process, as well as the slag micro-powder grinding process, extrusion combined grinding and drum roller grinding systems. Finally, the various grinding processes are summarized, showing the development trend of the grinding process and the advantages of different processes.
1. Introduction
Since the birth of the mill in 1883, it has long dominated the field of material grinding in cement and other industries. However, the traditional tube mill grinding process used in the preparation of cement and slag micro-powder has many disadvantages. Since the grinding space is open and unrestricted, a stable material bed cannot be formed, resulting in low grinding efficiency, high unit grinding power consumption and grinding cost. With the rapid development of science and technology, grinding technology is also constantly innovating. High-efficiency and low-energy grinding processes and equipment represented by "material bed grinding" technology have emerged and become the main direction of the development of grinding technology in the cement industry today. This article aims to deeply explore the differences and characteristics between the traditional grinding process of cement and slag micro-powder and the material bed grinding process for reference and exchange with peers.
2. Comparison of different grinding processes and their characteristics
(I) Traditional grinding process
The traditional grinding process represented by the tube mill has a history of 100 years. During the grinding process, sound and heat are generated while the electrical energy is converted into mechanical energy, consuming a lot of electrical energy, making the unit product power consumption always at a high level. Especially when the particle size of the material entering the mill is large, the grindability is poor or the moisture content is high, the grinding efficiency of the mill will be significantly reduced, further exacerbating the vicious cycle of high power consumption. Nowadays, the application of tube mills in the cement industry has faced severe challenges from high-efficiency bed grinding equipment. Its position in the field of grinding has gradually declined, and it is only a matter of time before it is gradually replaced by new equipment.
(II) Bed grinding process
Bed grinding equipment such as roller press, vertical mill, drum roller mill, etc. have significant advantages. When using bed grinding equipment to grind cement (or slag) to the end, the power consumption can be saved by about 30% compared with the tube mill system, and the vertical mill and drum roller mill process system are simpler than the tube mill system, but the roller press process system is more complicated. From the perspective of the newly built new dry cement production line in China, most raw material preparation systems use vertical mill technology, and the unit grinding power consumption is less than 15kwh/t. The vertical mill integrates multiple functions such as drying, crushing, grinding, powder selection, collection, and transportation. It occupies a small area, has high grinding efficiency, low power consumption and stable operation, so it has become the preferred model for raw material preparation. Although the unit power consumption of roller press is lower than that of vertical mill when used for final grinding of raw materials, due to its high system complexity and technical content, and the large maintenance and management workload, few manufacturers in China use it. There are also few manufacturers that use drum roller mills in domestic cement grinding systems.
3. Performance of final grinding products using material bed grinding process
(I) Application of material bed grinding equipment in final grinding
At present, vertical mills, roller presses, and drum roller mills can all be used for final grinding of cement and slag micropowders. Taking vertical mills as an example, the vertical mills of well-known companies in the world have their own independent intellectual property rights, and their internal structures have their own characteristics. In the development process of material bed grinding technology, especially in the early stage of cement final grinding, there have been problems such as narrow particle gradation range of finished cement products after grinding, large uniformity coefficient, large water requirement for standard consistency, and too fast coagulation time. The final grinding of vertical mills and roller presses has experienced this phenomenon. Since the drum roller mill came out later, it learned from the experience and lessons of the first two types of equipment during the research and development process, and solved these problems better by increasing the circulation volume and adjusting other process parameters. For example, when the setting time and standard consistency water requirement of cement produced by OK mill are basically the same, the 28d compressive strength is 15% higher than that of ball-milled cement, and the early strength is also higher, which is conducive to further increasing the admixture dosage and reducing the cement production cost. When the OK mill is working, the cement particle gradation can be conveniently adjusted by adjusting the process parameters such as the grinding disc speed, roller pressure, powder selector speed, air flow velocity and the height of the inner retaining ring of the mill. When the OK mill is used to prepare slag micro-powder with a specific surface area of 400-500m2/kg, the power consumption of the grinding is reduced by 35-45% compared with the tube mill system, the energy saving effect is significant, and the production cost is greatly reduced. At present, the use of vertical mill final grinding in China has effectively solved the relevant technical problems such as excessive water requirement of cement standard consistency and narrow particle gradation range.
(II) Slag micro-powder grinding process
With the development and application of high-performance concrete technology, slag micro-powder has become an indispensable sixth component material in concrete preparation. Granulated blast furnace slag is an industrial waste slag from the smelting of pig iron. Its mineral composition and chemical composition have a specific range. After being quenched and rapidly cooled by water, it retains a microcrystalline high-activity glass structure and has potential hydraulic activity. After the slag is activated by mechanical force and ground into micron-sized powder, the potential hydraulic mineral lattice is distorted and the hydration and gelling activity is excellent. When the ground slag powder is added to 425 slag cement to replace the same amount of cement, the early and late strength of the cement is significantly improved, which fully demonstrates that the excellent potential hydraulic activity of slag powder is of great significance to improving the physical and mechanical properties of cement products. In recent years, ground slag powder has been widely used in high-performance and high-strength concrete, and the research on related technical mechanisms has been continuously deepened. In concrete with basically the same amount of cement and slag powder, its strength increases with the increase of the specific surface area of slag powder. Cement and concrete mixed with ground slag powder have excellent impermeability and sulfate erosion resistance, high late-stage increase rate, and are suitable for humid environments and large-volume hydraulic concrete preparation. A large amount of ground slag powder is added to the preparation of foreign marine engineering concrete, which can improve the concrete's resistance to harmful chemical ion erosion, durability and service life. After slag powder replaces an equal amount of cement and is added to concrete, the heat release of the hydration system is reduced, the temperature difference between the inside and the outside is reduced, the probability of concrete cracking is reduced, and the alkali content is reduced, creating conditions for preventing alkali-aggregate reaction.
The microscopic characteristics of slag determine that it is difficult to grind. When using a tube mill grinding process to prepare slag powder with a specific surface area of ≥430m2/kg, the unit grinding power consumption is > 70Kwh/t, and the grinding body consumption is large. For example, using a φ3.2×13m open-flow tube mill to produce slag powder with a specific surface area of ≥430m2/kg, the hourly output is about 28t/h, and the unit grinding power consumption is 72kwh/t, and the production cost is significantly higher than that of a vertical mill. In recent years, large-scale slag powder production lines in China, such as Changgang Ruichang, Laigang Lubi, and Sichuan Xingchuancheng, have mostly adopted vertical mill grinding technology. The vertical mill integrates multiple functions, occupies a small area, and simplifies the process layout of the production line. The output of these vertical mill production lines is generally above 150t/h, the specific surface area of slag powder is ≥450m2/kg, the unit grinding power consumption is <50Kwh/t, or even <45kwh/t, the wear consumption is much lower than the tube mill system, and the power saving margin is >30%. When the first slag mill ZJTL3131S developed by Tongli in China prepares slag powder, it is equipped with a high-efficiency cage powder concentrator. The fineness of the finished product can be flexibly adjusted between 400-600m2/kg. When the specific surface area of slag powder is controlled to 450m2/kg, the output of the vertical mill is 52t/h, and the system power consumption is 37.3kwh/t.
4. Extrusion combined grinding and drum roller mill system
(I) Development and application of roller press
When roller press was first introduced, it was mainly used in the pre-grinding process. Its function was not fully utilized, and there were technical defects such as excessive wear of the roller surface, leakage of the hydraulic system, and edge effect. After more than 20 years of development and improvement and the application of new materials and new technologies, the technical performance of roller press has been continuously improved. At present, the working life of the roller surface of the roller press can reach more than 20,000 hours, and other problems have also been solved. As the final grinding equipment, the roller press has low power consumption and saves more than 30% of electricity compared with the ball mill system. However, there are problems such as narrow cement particle grading range, large uniformity coefficient n value, too fast cement coagulation time, and polygonal morphology of finished particles leading to excessive water demand for standard consistency.
(II) Extrusion combined grinding process
The extrusion combined grinding process is mainly used to give full play to the pre-grinding function of the roller press, so that the roller press can do more work to increase the fine powder content in the extruded material. Because the roller press does 1kwh more work, the subsequent tube mill can save 2-3kwh. The tube mill can play its grinding function, while achieving high production and low consumption of the system, "shaping" the coarse cement particles entering the mill, improving the cement particle grading, reducing water demand, and ensuring the improvement of cement performance. The use of the extrusion combined grinding process can increase production by 50-150% on the basis of the original grinding system, and the unit grinding power consumption can be saved by more than 30% compared with the ordinary tube mill grinding process. The subsequent tube mills of the extrusion combined grinding system have two forms: open flow and ring flow. When the same enterprise adopts this process and the subsequent tube mills are all φ3.2×13m, under the same clinker ratio conditions, the strength grade P.O52.5 cement ground by the subsequent tube mill is slightly higher in early and late strength than the cement ground by the circle flow system, with a shorter setting time and a wider particle grading range. The unit grinding power consumption of the open flow system is 25.7Kwh/t, and the unit grinding power consumption of the circle flow system is 27.4Kwh/t. The circle flow system process is slightly complicated, which is one of the reasons why some enterprises choose the open flow grinding process.
(III) Drum roller mill system
Under the same mixed material ratio conditions, the early and late strength of cement prepared by drum roller mill is higher than that of ball milled cement, and the performance is basically similar to that of cement ground by vertical mill, which means that the amount of mixed materials can be further increased and the production cost can be reduced. The unit grinding power consumption of drum roller mill is lower than that of vertical mill, showing unique technical advantages. In terms of cement physical properties, the standard consistency water requirement of cement produced by drum roller mill is slightly greater than that of cement produced by ball mill. This may be because most of its cement particles are flat needle-shaped and the hydration process is faster than that of spherical particles.
5. Conclusion
(I) Current status and trend of traditional tube mill grinding process
Due to its own defects, the traditional tube mill grinding process has low efficiency, high power consumption, large grinding body consumption and high production cost. The widely used extrusion combined grinding system partially introduces the material bed grinding process, which is a relatively mature energy-saving process technology, but the process system layout is complex. With the development of technology, it will gradually transition to vertical mill final grinding in the future.
(II) Advantages of material bed grinding process equipment
Vertical mill, roller press and drum roller mill are all efficient and energy-saving equipment for material bed grinding, realizing non-spheroidizing final grinding. When used to prepare cement and slag micro powder, compared with the traditional tube mill grinding process, the power saving range is more than 30-40%, which is of great significance to energy conservation and emission reduction and the development of circular economy.
(III) Characteristics and status of vertical mill
Vertical mill integrates multiple functions and is the first to achieve large-scale production. It has a simple process flow, small footprint, low unit grinding power consumption and metal wear. It is the preferred high-efficiency grinding process equipment for large and medium-sized cement and slag micro-powder preparation enterprises.
(IV) The impact of grinding process on cement mechanical properties and economic benefits
Compared with the mechanical properties of cement prepared by traditional tube mill grinding process, vertical mill and drum roller mill have higher early and late strength, which can increase the amount of admixture, reduce the tonnage of cement manufacturing cost, and comprehensively improve economic benefits. At the same time, the large amount of industrial waste slag is conducive to purifying the environment and eliminating waste slag pollution.
(V) Precautions for grinding system
Whether grinding cement or slag micro-powder, multiple strong iron removal should be set before grinding. Because single iron particles have ferromagnetism and plasticity, they are difficult to grind and are easy to enrich in the mill, which will aggravate equipment wear. Removing iron particles can maintain a high and stable grinding efficiency of the grinding system, reduce the wear of the main equipment, and extend its working life.
Blast furnace slag is a byproduct discharged during the ironmaking process of blast furnaces. It has high potential activity. After grinding it to a certain fineness, it can replace cement in concrete in equal amounts and produce green synthetic cement. It can not only be used to prepare ordinary concrete, but also is one of the most commonly used mineral fine admixtures in high-performance concrete.
1. Typical process of slag vertical mill grinding
In recent years, the slag grinding process and technology using vertical mills have developed rapidly in my country. The process mainly consists of vertical mills, hot air furnaces, bag dust collectors, return material elevators, feeding systems, main exhaust fans and chimneys.
Process introduction:
The slag transported by the belt conveyor enters the vertical mill through a pneumatic double flap valve. The slag is ground into fine powder inside the vertical mill and dried by the hot air sent from the hot air furnace. The fine powder sorted by the powder selector is transported to the main dust collector by hot air for collection, and the collected fine powder is transported to the finished product warehouse through the air conveying chute. Some of the micro powder and metal particles that cannot pass through the powder selector enter the mill material external circulation system through the pneumatic double flap valve. The return material is transported by the return material belt conveyor to the return material bucket elevator. A pneumatic two-way valve is installed at the outlet of the bucket elevator. Under normal production conditions, the return material enters the magnetic drum separator for iron removal and then enters the vertical mill again through the rotary air lock valve. Under special circumstances, the pneumatic two-way valve can discharge the material directly to achieve mill unloading.
2. Common problems in slag grinding process
(1) Selection of slag yard
Slag yard includes three types: open-air yard with forklift feeding, slag shed with grab feeding and stacker-reclaimer feeding. Production lines with an annual output of less than 2.4 million tons of slag powder can choose the first two types of yards, and production lines with an annual output of more than 2.4 million tons should try to choose the stacker-reclaimer feeding form.
For slag powder production lines that choose the first two types of yards, if the site is located in an area with more rainy weather, try to use a slag shed with grab buckets for feeding; otherwise, use an open-air yard with forklifts for feeding, which can save civil engineering costs.
(2) Selection of metal detector installation location
In some slag grinding process designs, metal detectors are usually installed on the belt conveyor entering the mill, but this design method has the following problems: If the accuracy of the metal detector is adjusted to a higher level, the belt conveyor entering the mill will frequently unload slag containing metallic iron, making the thickness of the material layer inside the vertical mill unstable; otherwise, the metal detector basically loses the function of monitoring slag containing metallic iron, causing a large amount of iron-containing slag to enter the vertical mill. Both of the above situations have an adverse effect on the stable operation of the vertical mill.
The metal detector can be installed on the belt conveyor in front of the batching bin to ensure that the slag entering the batching bin is qualified raw material. The slag in the batching bin is stably fed to the vertical mill through the quantitative feeder and the belt conveyor to ensure the stable operation of the vertical mill.
(3) Selection of hot blast furnaces
The hot blast furnaces in slag powder production lines include two categories: gas-fired furnaces and coal-fired furnaces. The most commonly used gas-fired furnaces are blast furnace gas-fired furnaces, while the most commonly used coal-fired furnaces are fluidized bed furnaces and pulverized coal furnaces. If blast furnace gas can be used in the factory, it is recommended to use a blast furnace gas-fired furnace, which can significantly reduce equipment, civil engineering costs and operating costs; if there is no condition to supply blast furnace gas in the factory, it is recommended to use a pulverized coal furnace. Although the one-time equipment investment of a factory using a fluidized bed furnace is relatively low, from the perspective of long-term operation, it has the disadvantages of high coal consumption, poor working environment for workers and inability to achieve remote control.
(4) Selection of dust collectors
Dust collectors are available in two types: single air inlet and double air inlet. It is recommended to use a single air inlet dust collector. Although the double air inlet dust collector is shorter than the single air inlet dust collector, it can reduce the civil engineering costs of the dust collector workshop. However, most users who use double air inlet dust collectors report that this type of dust collector is prone to uneven wind pressure at the two air inlets.
(5) Selection of main exhaust fan
The main exhaust fan has two types: single air inlet and double air inlet. The specific type used in the design should refer to the recommendations of the vertical mill manufacturer, and the performance curve of the fan should also be confirmed by the vertical mill manufacturer.
In most current grinding systems. The air volume is generally adjusted by the valve opening in front of the exhaust fan. In the case of not significantly reducing the temperature of the gas out of the mill, the air volume can also be increased by adjusting the cold air valve in front of the mill inlet, but this often leads to a decrease in the negative pressure at the mill inlet. Practice has shown that the most economical way is to directly adjust the fan ventilation volume by adjusting the fan speed.
(6) Selection of vertical mill
Currently, there are many manufacturers at home and abroad who manufacture vertical mills for grinding slag, but the types of vertical mills they produce are similar. They can be roughly divided into two categories: vertical mills with hydraulic roller devices and vertical mills without hydraulic roller devices. The main difference between the two is the surfacing cycle and surfacing time. The surfacing cycle of the former is shorter than that of the latter, but the time required for each surfacing is also shorter than that of the latter. Therefore, when users choose the main equipment vertical mill, they can determine it according to the sales rules of local slag powder products and their own operating characteristics.
(7) Selection of slag powder silo level meter
There are two types of level meters used on the top of slag powder silo: radar level meter and heavy hammer level meter. Some users reported that radar level meter is not easy to damage, but it is easy to make mismeasurements; heavy hammer level meter is more accurate, but it is easy to break the chain of the heavy hammer. For the above situation, radar and heavy hammer can be used at the same time as the level meter on the top of the silo. The two complement each other. If one of the level meters fails, the operator in the central control room can find it as soon as possible.
(8) Selection of bulk dust collector at the bottom of slag powder silo
The space height between the bottom of the slag powder silo and the bulk platform is limited, which makes it difficult to meet the requirements of replacing the filter bag on the top of the single dust collector. Therefore, a cartridge dust collector can be selected or the equipment manufacturer can be required to make a dust collector with side filter bag replacement. However, both have their disadvantages. The dust collection effect of the former is not ideal, and the latter cannot add an external insulation layer to the dust collector.
Among the types of industrial waste slag, granulated blast furnace slag has a high glass content and high activity. From the analysis of its mineral phase composition: the main mineral phase of slag is C2S. Therefore, it can be regarded as a low-calcium and high-silicon clinker. C2S minerals have the characteristics of slightly low early strength and good ability to continuously increase strength in the later and long-term. At the same time, slag micropowder has low heat and low alkali characteristics, and is a mineral admixture with excellent physical and chemical properties required in concrete. Because it has good resistance to sulfate and chloride ion corrosion, it can be used in the preparation of special marine concrete. It can also replace a certain proportion of cement in equal amounts to prepare ordinary, high-strength and high-performance concrete. According to the different chemical compositions of slag slag, its acidity and alkalinity coefficients are also different.
There are three main grinding processes for preparing high-activity slag powder: one is to use vertical roller mill; the second is to use the process of roller press + V-type powder concentrator (or scattering classifier) + high-efficiency powder concentrator; the slag drying process is completed in the V-type powder concentrator. For example, Tongli's RPZ170-180 + V selection + SKS high-efficiency powder concentrator process; the third is to use a tube mill (high-fine open flow or circle flow). The first two grinding systems have low unit product power consumption (≤45Kwh/t) and high production efficiency, but the one-time investment is relatively large. This article discusses the use of the third grinding process, using a ∮3.2x13m high-fine open flow three-bin tube mill to prepare slag powder and its trial production adjustment process.
There are two ways to stimulate the hydration activity of slag: one is physical activation (mechanical grinding activation); the other is chemical activation (activator). Physical activation is the premise of chemical activation and the most fundamental condition for slag to achieve chemical activation. Granulated blast furnace slag contains glass with high hardness, good toughness, and is easy to break and difficult to grind. According to the analysis of the physical and chemical characteristics of the slag of this enterprise, it can be seen that acidic slag has worse grindability due to high Sio2 and low CaO.
Experimental studies have shown that the hydration reaction of cementitious materials is a chemical reaction of acid-base balance. When the specific surface area is the same, the activity index of alkaline neutral slag is higher than that of acidic slag. This may be because the pH value of the liquid phase affects the reaction activity of acidic slag during the hydration reaction, that is, the acidity of the slag offsets part of the alkalinity of the liquid phase, resulting in lower secondary hydration reaction and strength than alkaline and neutral slag. Therefore, it is necessary to raise The most effective technical means to improve the activity index of high-acid slag is to increase its grinding degree (specific surface area) and increase the content of slag fine particles (< 8um). The three-bin high-fine open-flow grinding process is used to mechanically activate the original slag particles, which can significantly improve the grinding degree and reaction activity of the slag.
The function of the first bin (crushing and coarse grinding bin) of the mill is to pre-crush and coarsely grind the granular slag, the function of the second bin (transition bin) is to implement transitional fine grinding of the slag coarse powder flowing into the first bin, and the function of the third bin (fine grinding bin) is to perform high-fine grinding on the slag powder flowing into the second bin. The grinding capacity of the three bins must achieve dynamic balance.
According to the characteristics of small particle size of slag entering the mill (containing a small amount of black heavy slag blocks and coke, with a maximum particle size of <20mm), when designing the grinding body gradation, the grinding ability of the grinding body on the slag must be considered, that is, a smaller grinding body is selected to increase the total surface area of the grinding body per unit weight to increase the contact and grinding probability of the slag particle group, and the slag is ground within a reasonable grinding time, so that the fineness (specific surface area) of the slag powder out of the mill meets the control index (≥430kg/m2) requirements.
In order to ensure that the specific surface area of slag powder reaches the design index (≥430kg/m2) and the activity index of slag reaches S95 level. The grinding bodies of each chamber in the mill, especially the third chamber (fine grinding chamber), adopt micro-forging of ∮16mm and below. During the operation of the mill, the activation liner in the third chamber effectively activates the grinding function of the micro-grinding body, solves the problems of fine-particle material retention, micro-grinding body throwing and low grinding height, changes the movement trajectory of the grinding body in the traditional grinding process, and effectively prevents the micro-grinding body from backflowing, eliminates the material "retention area", and strengthens the grinding capacity of the fine grinding chamber. The activation of the micro-grinding body greatly enhances its shearing and grinding ability for fine-particle materials, and significantly improves the grinding degree (specific surface area) of the material. At this point, the task of grinding slag is completed. According to the measurement during the subsequent debugging process, the residence time of slag in the mill from entering the mill to leaving the mill is generally about 20 to 25 minutes.
Since the granular slag entering the mill contains a small amount of black block heavy slag and coke, in order to improve the coarse crushing capacity of the first bin (crushing and coarse grinding bin), 6t of ∮70 and ∮60 steel balls are added in proportion; there are two different opinions on the selection of grinding bodies for the second bin (transition bin): The company's boss believes that all or part of the balls or forgings should be mixed. The author believes that small steel forgings should be used, mainly considering that the setting of the second bin (transition bin) is a link between the past and the future, and its position is very important. In fact, it creates conditions for the grinding of the third bin (fine grinding bin). Therefore, the grinding capacity of the second bin (transition bin) must be improved. If all balls are used or balls and forgings are mixed, although there is a certain void ratio between the grinding bodies when forging is used alone, which will appropriately increase the slag feeding capacity, it will increase the grinding burden of the third bin (fine grinding bin). Because the open flow grinding process is used, it is likely to cause the slag powder to be coarse and the specific surface area to be low.
For grinding finer particles (the specific surface area of the mineral powder between the first bin and the second bin is 100-130m2/kg), balls are more suitable for grinding finer particles. The grinding efficiency of the point contact mode between materials is still not as good as that of the small steel forging. Finally, according to the author's opinion, three smaller steel forgings of ∮20mm, ∮18mm and ∮16mm are used in the second bin (transition bin) to enhance the grinding capacity of the coarse slag powder flowing into the first bin, laying a good foundation for the further grinding of the slag powder by the micro-grinding body in the third bin (fine grinding bin). At the same time, the setting of the high-efficiency screen partition plate in the mill makes the functions of each bin of the mill fully utilized, which can ensure the crushing of the first bin. The coarse slag particles are forced to be screened and transferred to the second bin, where they are ground to a coarse and medium degree by the small steel forge in the second bin. Under certain sieve hole size conditions, the slag particles in the first bin that are smaller than the sieve hole size can pass through the screening device smoothly, otherwise they will remain in the first bin and continue to be crushed. After the coarse and medium particles of slag are ground in the second bin, they pass through the second forced screening device. The sieve hole size in the second bin screening device is smaller than the first sieve hole, which creates good conditions for the efficient grinding of the fine slag particles entering the third bin (fine grinding bin) smoothly.
The forced screening of slag particles by the efficient screening partition plate is a sufficient condition for the slag to be finely ground, and the third chamber (fine grinding chamber) of the mill is long, and the application of micro-shaped grinding bodies is a necessary condition for the high-fine grinding of slag micropowder. The efficient screening partition plate in the mill fully demonstrates the unique "small grate gap, large flow" screening mechanism in the high-fine grinding technology. Although the screening gap seems to be small, the total number of screen holes is large, the material passing area is large and smooth, and the material passing rate per unit time will not decrease. Only the material particles that meet the requirements of the rear chamber grinding are screened in time. The actual design load of the grinding body in the mill is 131t, which is 6t more than the rated load of 125t. Considering that the power of the main motor is 1600kw, the driving power is relatively surplus. At the same time, the starting operation system is equipped with a static phase advancer. When the operating current of the main motor is within the rated range, it can drive 140-150t grinding bodies. The actual load of 131t grinding bodies is calculated in steps according to the proportion of the debugging regulations during the load operation test. The grinding bodies in each bin of the mill are made of medium chromium alloy white cast iron, provided by Tongli professional foundry. Mechanical properties: macroscopic hardness HRC53-56, impact toughness ak≥3-7j/cm2, metallographic structure P+C, wear ≤120g/t-c.
1. Screening of wet slag
As we all know, slag powder is made by grinding granulated blast furnace slag, which contains a small amount of coke and black block heavy slag, which has poor activity and poor grindability, directly affecting the production and quality of the mill system and must be removed. To this end, a steel coarse screen with a diagonal of 70 mm is set at the slag yard feed port to initially filter out the black heavy slag and coke. Before the wet slag is conveyed into the dryer by a belt, a fine screen with a diagonal of 30 mm is set. Screen. Ensure that there are no large impurities in the dried slag, creating a good prerequisite for stabilizing the subsequent mill hourly output and slag powder quality.
2. Pay attention to iron removal before grinding
Granulated blast furnace slag is a product of the blast furnace pig iron smelting process. It contains a certain amount of metallic iron. If it is not removed in time, it will not only significantly affect the output of the mill and the quality of the slag powder, but also cause the grinding body gradation disorder and deteriorate the grinding process. Internal grinding environment. Therefore, it is necessary to set up multiple pre-grinding iron removal processes (the iron removal efficiency of a single-pass iron removal process is low) to eliminate the harm of metal iron particles to the slag grinding process. Generally, three passes can be set: the first pass The first one is set above the feeding belt of the dryer; the second one is set above the slag drying and discharging part; the third one is set above the grinding belt. The above iron removal process can achieve an iron removal efficiency of more than 99%, ensuring the stability of the grinding process .
3. Strictly control the moisture content of slag entering the mill
The grinding process of high-fine open-flow slag tube mill is different from that of vertical mill and roller press. In the actual production process, the high moisture content of the slag entering the mill will have an adverse effect on the system grinding efficiency and the specific surface area index of the slag powder. Strict control. The rotary dryer modified by high-efficiency boiling furnace has a maximum moisture content of slag out of the machine of 1.20%, generally 0.8-1.0%. In operation, it only needs to adjust the slag flow into the machine or adjust the temperature of the boiling furnace. It can achieve the purpose of controlling the moisture content of the slag out of the machine.
4. Regularly replenish the grinding media in the mill
The microhardness of granulated blast furnace slag (HV650) is higher than that of cement clinker (HV550), with good toughness and poor grindability. The grinding media consumption of ton of slag powder is about twice that of cement mill. The specific surface area (≥430kg/m2) requires regular replenishment of grinding media to each bin in the mill. We have determined that the grinding media will be replenished once every half month according to the production (preliminarily calculated based on 250g/t slag abrasion), that is, the grinding media will be replenished twice a month to ensure that The mill can maintain a high and stable grinding efficiency and the ratio of the fine slag powder out of the mill for a long time.
5. Make a good match between new and old slag
Production practice has proved that the slag from the same blast furnace, after being piled for a period of time (2 to 3 months), is easier to grind than the newly-fired slag, and the hourly output is 2 to 3 t/h higher. This is because after a period of accumulation, the glass of the slag becomes brittle, the stress in the microstructure is released, and the grindability is significantly improved. However, although the specific surface area of the aged slag is The activity index of new slag is significantly lower than that of new slag. Compared with the same surface area (≥440kg/m2), the 7d and 28d activity indexes of new slag are 1-3% and 2-4% higher than those of old slag, respectively. After the combination, the powder was ground and tested again. The activity index of the slag powder produced after the combination was good and stable. By taking corresponding technical measures, when the grinding body loading of the mill was 131t, the production of S95 grade slag (≥430kg/m2 ), the hourly output reaches 28t/h. In order to further increase the output and reduce the power consumption of the grinding mill, 9t of ∮8×8mm micro forging was added to the third warehouse, and the total loading capacity was 140t.
After adjustment, the main motor (after the phase advance ) The operating current is between 108 and 110A, which does not exceed the design requirement of rated current (≤112A). The mill runs smoothly and works normally. Under the condition of unchanged specific surface area, the hourly output of slag micro powder is increased to 30t/h.
The high-fine tube mill is used to prepare slag powder. The process technology is mature and reliable, and it belongs to the primary stage of slag grinding. Although the one-time investment is low, it is better than the vertical mill and roller press process in preparing slag powder with the same specific surface area. The power consumption of the grinding is high and the system output is low. The power consumption of grinding a ton of slag is 25-30kwh higher than that of the above grinding system. The increase in electricity costs means that the product profit will be lost in the long term. Although the one-time investment of slag micro powder process is large, its production scale
The grinding mechanism of these two equipments is high-efficiency "material bed grinding". The power consumption of grinding one ton of slag is ≤45kwh/t. Compared with the tube mill system, the electricity cost of one ton of slag is reduced by 15 to 18 yuan. . In particular, the vertical mill realizes the integration of drying, grinding and powder selection and has become the leading direction for the selection of main machines for slag micro powder preparation.
(1) If the existing high-fine open-flow mill is changed to a circle-flow grinding system under the same process conditions, and a high-fine powder separator for slag powder is used, the system output can be ≥40t/h after the transformation, and the grinding power The consumption can be reduced to below 60kwh/t, and the annual production capacity can reach 300,000 tons.
(2)It is recommended to use pre-grinding (rod milling) technology to pre-treat the slag entering the mill to ensure that the slag entering the mill is powder <2mm, the Bond work index is reduced, and the grindability is significantly improved. It can give full play to the grinding capacity of multi-bin tube mill; if the circle flow transformation is implemented at the same time, the expected hourly output can reach 50t/h, and the power consumption of ton slag grinding is about 50kwh/t. The press combined with slag grinding has a simple process and requires less investment.
(3)Enterprises that use multi-bin high-fine grinding to produce slag powder should actively seek to use high-chromium alloy (high hardness HRC58-63) grinding bodies to reduce wear costs and enable the grinding system to maintain a high and stable grinding efficiency for a long time. When the grinding body and the lining plate surface are sticky in the second and third chambers of the mill, the slag micro powder special grinding aid (liquid) can be introduced to solve the problem.
1. Pretreatment of high pressure roller press
After the raw material is squeezed by the roller press under high pressure, it forms a material layer with uniform particles and easy to grind. The roller press uses high pressure to make cracks in part of the material, thereby improving the subsequent grinding efficiency. Qualified materials are then fed into the mill through a conveying device.
2. Material feeding and coarse grinding stage
Through the feeding chute in the feeding device, the material is evenly fed into the coarse grinding bin of the ball mill. In the coarse grinding bin, steel balls with a large average diameter are equipped as grinding bodies. Under the impact and grinding of the steel balls, the material is quickly crushed to a smaller particle size so that it can enter the next process.
3. Screening of coarse grinding bin and partition plate
The material that is initially crushed by the coarse grinding bin is screened through the coarse screen plate on the partition plate. The coarse screen plate has a larger screen gap size, allowing materials with a certain particle fineness to pass through, while larger particles are blocked back to the coarse grinding bin for further grinding.
4. Further screening by combined partition plate
The material that has passed the coarse screen plate enters the combined partition plate area. A fine screen plate is provided in the combined partition plate, which can screen the material more finely. Particles with larger screen size are blocked by the screen plate and flow back to the coarse grinding chamber for re-grinding, while small particles passing through the fine screen plate enter the fine grinding chamber.
5. Deep grinding in fine grinding chamber
The material entering the fine grinding chamber is further ground by the small diameter grinding body, and the material is ground to the target fineness by using the high density and uniform distribution between the steel balls. The grinding action at this stage is mainly fine grinding to ensure the quality of the final product.
6. Discharging and separation
The material that reaches the required fineness enters the discharge pipe through the discharging grate plate and is then discharged through the discharging device. The fine powder is smoothly transported to the collection device, and the residual particles of the grinding body are screened out by the rotary screen drum in the discharging device. The separated grinding body returns to the mill and continues to participate in the grinding cycle.
7. Finished product collection
The fine powder discharged from the mill is transported to the powder selector by airflow for final sorting and collection. GGBFS products that meet the particle size requirements are collected in the silo, and the coarse particles are returned to the mill for reprocessing to achieve efficient operation of the closed-loop circulation system.
8. Process characteristics
Efficient screening: The combined partition plate can optimize the screening effect, reduce the circulation of coarse particles, and improve the grinding efficiency.
Multi-stage grinding: Through the partition design of the coarse grinding and fine grinding bins, the grinding uniformity of the material is effectively improved to ensure the quality of the finished product.
Closed-loop circulation system: Through the recycling function of the powder selector, the material utilization rate is maximized and energy consumption is reduced. Energy saving and environmental protection: The roller press pretreatment greatly reduces the energy consumption in the grinding process and reduces dust emissions.
1. Feeding device
The material enters the mill through the feeding device. The feeding device includes a feeding pipe, an air inlet pipe and a bracket. The bottom of the bracket is equipped with a movable wheel for easy adjustment. An adjustable valve is provided at the end of the air inlet pipe to control the air intake. By placing an adjustment gasket between the feeding and air inlet pipes and the bracket, the center height of the feeding device can be adjusted when necessary to ensure its accurate position.
2. Slide Shoe bearing
The shoe bearing is an important supporting structure of the mill. It adopts a movable design at the feeding end and a single-side fixed design at the discharging end.
The shoe bearing has a spherical contact with the sliding ring. The shoe is seated on the roller or fixed support through the sphere to adapt to the thermal expansion and contraction of the cylinder and realize automatic adjustment. This design ensures good contact between the slip ring and the shoe. The shoe is made of castings and equipped with a bearing alloy liner. It is combined with the shoe body by casting and can withstand a maximum specific pressure of no more than 2200kPa.
The shoe bearing is equipped with a high-pressure starting lubrication device for mill startup, shutdown and maintenance. The high-pressure system forms an oil film between the support bearing and the slip ring, and the low-pressure system provides circulating oil lubrication through an oil pump. In addition, the sliding shoe bearing controls the support bearing temperature through a water cooling system, and a temperature detection device is installed, which is interlocked with the main motor to ensure safe operation. Slip rings are equipped with oil scraper brushes at both ends to prevent the lubricating oil from flowing out. The sliding shoe bearing cover is welded from steel plates and is equipped with inspection holes for easy daily maintenance and inspection.
3. Shell Rotating part
The rotating part is the main part of the mill, which completes the material grinding process. It is mainly composed of a cylinder, a transmission pipe, a partition plate, a discharge grate plate, a cylinder liner, an end cover liner, a feed cone and a discharge body. The cylinder is supported on the sliding shoe bearing through a slip ring and is connected to the transmission pipe by a reaming hole and a through-hole bolt. A combined partition plate is provided between the coarse grinding bin and the fine grinding bin, with an adjustable lifting plate for adjusting the material flow. A discharge grate plate is provided at the discharge end, and a stepped and double-step grading liner is installed in the cylinder to optimize the material grinding effect.
4. Discharging device
The discharging device is welded with steel plates, and its structure is simple and practical. The upper part of the device is an exhaust port, and the lower part is a discharging port, which is used for material discharge and ventilation.
5. Transmission device
The transmission device includes the main motor, the main reducer, the auxiliary transmission device, the diaphragm coupling, etc. The lubrication system provides power support through the main motor oil station and the main reducer oil station. The transmission device is closely coordinated with the operation of the mill to ensure the efficient operation of the equipment.
6. Shoe bearing lubrication device
The shoe bearing lubrication device consists of a high-pressure started thin oil station and a pipeline system to ensure the normal operation of the shoe bearing. The high-pressure system is provided by an electric high-pressure pump with a maximum pressure of 31.5 MPa, and the low-pressure system provides an oil supply pressure of about 0.4 MPa. The lubrication system is interlocked with the main motor, and an oil flow signal is installed on the lubricating oil pipeline to monitor the lubrication status in real time.
Requirements for mill installation and trial operation
1. Key points for foundation marking
The equipment foundation needs to be laid out with a center mark plate embedded in advance, using a 10x200x100mm steel plate, and marked with positioning reference point marks. Use a precision theodolite to lay out the longitudinal center axis (i.e. the center line of the grinding body) based on the positioning reference point, with an accuracy error of no more than 0.5mm. Lay out each horizontal center line according to the drawing size. When measuring the foundation, use a water pipe to connect the level to check the horizontality of the longitudinal and horizontal positioning center mark plates and the common horizontal plane of the supporting foundation at both ends of the grinding machine. The layout should be comprehensive, and the center position tolerance of each anchor bolt hole is 10mm. The center distance between the feed end sliding shoe bearing and the discharge sliding shoe bearing must be consistent with the center distance after the actual measurement of the grinding body assembly. If there is a difference, the actual measured center distance shall be used as the basis for correction, and then the foundation marking shall be carried out accordingly.
2. Inspection before installation
Before installation, the quality of important parts such as the cylinder, slip ring, sliding shoe bearing and reducer should be checked. Those with damage or deformation should be repaired in advance. Those with excessive dimensional errors should be processed in advance and the installation dimensions should be corrected.
3. Sliding shoe bearing installation requirements
The horizontal tolerance of the sliding shoe bearing shall not exceed 0.1/1000, the relative elevation tolerance of the two seats shall be 0.5mm, and the feed end shall not be lower than the discharge end. When aligning the sliding shoe bearing, the overlap of the longitudinal center line of the mill shall not exceed 0.5mm, the horizontal center line distance tolerance shall not exceed 1mm, and the parallelism tolerance shall not exceed 0.5/1000. The screws in the support high-pressure oil bag (oil pipe seal) should be removed during installation. After the cylinder is placed on the sliding shoe bearing, check the elevation of both ends. The relative elevation shall not exceed 1mm, and the feed end shall not be lower than the discharge end. The distance between the center line of the slip ring and the center line of the sliding shoe bearing seat shall comply with the requirements of the drawing. The relative radial runout tolerance of the sliding rings on both sides of the mill is 0.2mm. The support bearing of the sliding shoe bearing should be subjected to a water pressure test before installation, and the test pressure is 0.63Mpa. The cooling water system should also be subjected to the same water pressure test after installation. There should be no leakage at the support bearing and pipeline connection, and the high-pressure pipeline should also be subjected to an oil pressure test (see the installation technical requirements for details).
4. Installation of mill transmission device
The installation of the mill transmission device, its main motor, main reducer, auxiliary transmission and electrical control equipment should be carried out in accordance with the relevant technical documents and drawings of the motor and reducer.
5. Lining plate installation points
Before installation, the lining plate should be checked for casting defects that affect the strength. The back arc of the lining plate should be measured to see if it meets the drawing size. The back and the edges should be smooth, and the uneven areas should be polished with a grinding wheel.
During installation, the arc surface of the lining plate fits tightly with the inner circle of the cylinder. The grinding silo cylinder lining plate, the lifting plate of the partition plate and the oil scraper brush in the sliding shoe bearing are directional. When installing, pay attention to the relationship with the rotation direction of the mill. When installing the spring sealing device, pay attention to the pressure of the tension spring on the felt, adjust it with the adjustment plate, and inject grease after installation. The coaxiality tolerance of the output shaft of the main reducer and the axis of the transmission pipe flange is not more than 0.4mm.
6. Mill cylinder liner installation details
Installation: Carefully and correctly place the liner, fill the concave surface on the back of the liner with concrete, ensure that the gap between the liner and the cylinder contact surface does not exceed 1mm, and the liner embedded in the slip ring is tightly built around the liner. The gap is wedged and welded with steel sheets. All liner continuous circumferential gaps inside the cylinder are wedged into steel sheets for partitioning, and the arc length of the gap is not more than 400mm. The adjacent gaps of the liner fixed with bolts are maintained at 4-8mm.
Inspection: The weld inside the cylinder is smoothed, the defective parts inside the cylinder are repaired, the liner has no casting defects that affect the installation and strength, and the defects that affect the installation are repaired and installed.
Installation direction: Pay attention to the direction when installing the step liner and the graded liner (see the assembly drawing of the rotating part of the mill).
Fastening: The liner is connected to the cylinder with bolts, with sealing rings and washers. Tighten the bolts to the specified torque and re-tighten them several times until the torque remains unchanged.
7. partition plate installation points
The connection holes between the bracket and the front plate are drilled, and the 6 holes are installed for alignment. During installation, ensure that the support plate has good contact with all the sides of the fixed blocks, and the clearance in the diameter direction is equal. The support plate and the front plate are temporarily fixed in the cylinder before welding the end cover of the cylinder.
The center frame and the center screen plate are tightened with screws.
All bolts are tightened to the required torque.
All bolts are rechecked and tightened. They are tightened for the first time after no-load hours, and then re-tightened every hour until the specified torque is reached, and finally the nuts are spot welded.
When the rubber plate is installed on site, epoxy resin is used to stick it between the two convex ribs of the fixed block.
All liner plates fit tightly with the screen plate and the front plate, and the circumferential and longitudinal spacing of the liner plates is as uniform as possible.
The two plates of the rear plate are welded into a whole after on-site installation.
The long hole burrs on the screen plate face the mill discharge port.
8. Mill Shoe Bearing Installation Steps
Alignment and Grouting Preparation of Bottom Plate
First, pour the foundation surface to about 100mm lower than the bottom surface of the bottom plate shown on the installation diagram. After the alignment is completed, the remaining grouting is carried out.
During alignment, pull a thin steel wire on the center line of the mill, check the elevation shown on the foundation diagram, place the bottom plate on the pad iron (see the shoe bearing component diagram for the placement of the pad iron), and align it in the middle of the shoe bearing foundation mold, that is, the two inner side support frames and adjustment screws of the two bottom plates to prevent the bottom plate from sliding down, so that the center line of the bottom plate and the center line of the mill are in the same vertical plane and parallel to the center line of the mill, and the other center line is perpendicular to the center line of the mill. Use a level, a straight ruler and the 30c measuring block provided with the mill shoe bearing installation tool to align, and place the measuring block according to the installation diagram. On the bottom plate of the sliding shoe bearing, adjust the position of the bottom plate of the sliding shoe bearing, strictly ensure the installation dimensions in the parts diagram of the sliding shoe bearing and the parts diagram of the sliding shoe installation tool, and ensure that the horizontal tolerance of the bottom plate of the sliding shoe bearing in the direction of the cylinder axis is not greater than 0.1/1000, the relative elevation tolerance of the corresponding points of the bottom plates at both ends is 0.5mm, and the feed end is not lower than the discharge end, the longitudinal center line overlap of the bottom plates at both ends is not greater than 0.5mm, the horizontal center line distance is not greater than 1mm from the measured center distance of the two slip rings, and the parallelism tolerance is not greater than 0.5/1000.
After the final alignment, install the anchor bolts connecting the bottom plate and the foundation, tighten the nuts of the anchor studs, check the alignment, tighten the nuts to the specified torque according to the requirements, and then carefully cast the anchor bolts for the second time.
9. Inspection and treatment
The inner diameter of the sliding surface of the sliding shoe of the sliding shoe bearing is 1‰ larger than the outer diameter of the grinding cylinder sliding ring. In theory, there is no need to scrape the shoe. The sliding ring and the shoe are in bottom line contact. The contact requirements between the shoe and the sliding ring are: apply a thin layer of marking color (red lead) on the shoe surface, and place the shoe on the top of the sliding ring for inspection; use a feeler gauge to check at both ends of the shoe. The small gap between the sliding ring and the shoe is about 0.05~0.2mm, about 20mm away from the edge of the shoe end. Otherwise, the shoe needs to be scraped, but it is only allowed to be done in the outermost 20-50mm area of the two ends of the shoe; the shoe and the slip ring The contact spots of the bearing should be evenly distributed along the entire length of the bearing busbar, and the spacing between the spots should be less than 5mm; when the contact distribution does not meet the requirements, it is allowed to scrape and grind within the arc length of 400mm at the bottom of the bearing, but note that the bearing diameter is 1‰ larger than the ring diameter, and the contact diameter of the bearing cannot be scraped to the diameter of the sliding ring, otherwise it is not conducive to the formation of the oil film; clean the bottom plate and install the chassis of the sliding cover, put a rubber sealing pad between the chassis and the bottom plate, and apply sealant (imported sealant or vibration-type flat anaerobic glue from Jilin Loctite) before installation.
10. Installation
Confirm that the bottom plate has been carefully cleaned, then install the roller, ball seat, and concave ball, and use eye screws during installation. The cross center line of the bearing bottom plate should be aligned with the center mark plate, and the deviation should not be greater than 0.5mm. Install the support bearing with the convex sphere installed. The spherical surface of the convex sphere must be located in the concave sphere and can move freely. Use molybdenum disulfide lubricant to lubricate the spherical surface. If there is a fixed support bearing, it should be placed on the upper side of the slip ring and fall on the fixed support.
The position and slope of the support bearing must be as close to the final position as possible. Use a steel wire to pass through the eye screw screwed into the highest end of the support bearing to tie the support bearing, so that the sliding surface of the support bearing faces the center. When the mill is to be placed in the sliding shoe bearing, remove the block and the tied steel wire just before the slip ring contacts the support bearing, so that the mill can be self-adjusted when it is in place.
11. Installation technical requirements
Before installation, the contact surface of the concave sphere and the convex sphere should be evenly coated with molybdenum disulfide grease to make the contact smooth and the rotation flexible. The scraper brush is installed on the upward movement side of the slip ring, and is installed on the other side when the process requires reversal. The scraper brush should be close to the end face of the slip ring, and the spring tension is 4N. The hole without the scraper brush is blocked with a bolt. Before installation, soak the sliding ring seal in oil. When installing the top of the sliding shoe bearing cover, oil should be poured on the surface of the sliding ring. When installing the cover, the connecting flanges, oil and water pipe joints should be tightly sealed without leakage, and the bottom plates should be glued with adhesive. When installing the lubrication device, adjust its nut to make the oil tank level and ensure that the sliding ring is immersed in the oil less than 20mm. After the pipeline system is installed, the cooling water pipe is subjected to a 0.6Mpa water pressure test, and there should be no leakage.
The plane of the roller and the ball seat and the plane of the roller and the bottom plate should ensure uniform contact along the entire length of the roller and flexible rolling. After the lead wire of the end face thermal resistor is led out of the cover, it should be fixed according to the automatic control requirements.
When installing the cover seal, the sealing block should be adjusted to make it evenly contact with the sliding ring over the entire length.
Fill the lubricating oil to the cursor position and check the sealing of the sliding shoe cover.
Check that the door switch should rotate flexibly and be tightly sealed.
When installing the pad iron, in order to prevent slipping, it can be welded after adjustment on site.
During on-site installation, the pipe clamp and the sliding shoe cover should be welded at a suitable position.
When installing the base plate, reserve a distance of 3053mm from the bottom of the base plate to the mill axis for adjustment after installation.
After the two sides of the support bearing are matched, mark them and record the actual size value at the 3053 size.
The M6 screws in the support bearing oil bag are removed during on-site installation after the pressure test.
The temperature measuring device should be installed on the upstream side of the slip ring.
All electrical leads need to be centrally connected to the junction box.
12. Installation precautions
The screws in the oil bag (oil pipe seal) should be removed when installing the sliding shoe bearing.
After the sliding shoe bearing cooling water system is installed, a 0.5Mpa water pressure test should be carried out for 20 minutes, and no leakage should be allowed at any place; the lubrication pipeline should be subjected to oil circulation and oil pressure tests, with a pressure of 1.25 times the working pressure for 15 minutes, and no leakage is required.
A shim should be placed under the bottom plate of the sliding shoe bearing. For details on its location and placement, see the sliding shoe bearing component diagram.
See (Figure 3) for a schematic diagram of the installation of the sliding shoe bearing bottom plate. For details, see the sliding shoe bearing component diagram and the sliding shoe installation tool component diagram.
13. Key points for installing the lubrication pump station and piping system
Install the oil pan, use the adjusting nut to align the oil pan so that its edge is horizontal, and use the bottom edge of the slip ring as a reference to correct the oil pan height so that the slip ring is immersed in the oil by 15-20mm.
Connect to the internal circulation pipeline of the oil pan and the oil distribution tank, connect the external oil pipe to the circulating oil pump, and connect the cooling water pipeline.
Install the lubrication pump station and make some mechanical and electrical connections to it (see the sliding shoe bearing pipeline and lubrication pump station oil supply system diagram).
The high-pressure oil pipe is connected to the sliding shoe bearing through a ferrule-type pipe joint.
The mill must be able to rotate during alignment, and the high-pressure pump must work when the mill is rotated. Therefore, the lubrication pump station must be tested and approved before alignment.
14. Technical requirements for the installation of lubrication pump stations and pipeline systems
The oil pipe must have sufficient strength, smooth inner wall, no sand, no rust, no defects, no cracks.
The pipeline installation can be adjusted according to the actual situation. The positions of all joints and oil pipe signal devices on the pipeline are determined during the on-site installation.
Each steel pipe is equipped with a tapered pipe thread according to the actual length required on site.
All pipe fittings must be cleaned according to the requirements before installation. After cleaning, the two ends of the pipe must be plugged tightly before installation. The pipe must not be mixed with debris.
After the pipeline system is installed on site, the system must be pressure tested and each pipeline joint must be checked. No leakage is allowed. The specific requirements are as follows:
High-pressure oil pipeline: working pressure 32Mpa, test pressure 40Mpa.
Low-pressure oil pipeline: working pressure 0.4Mpa, test pressure 0.6Mpa.
Cooling water pipeline: working pressure 0.4Mpa, test pressure 0.6Mpa.
15. Technical requirements for the installation of the rotating part of the mill
The front plate, support plate and fixed plate in the partition plate should be pre-installed into the cylinder for temporary fixation.
The support plate in the discharge grate plate should be pre-installed into the cylinder for temporary fixation. The step liner, partition plate and discharge grate plate all have directional requirements, and their direction and position should meet the design requirements. The rotation direction of this mill is clockwise from the discharge end. All round head bolts are not allowed to be stressed on one side during installation, otherwise a shim is placed on the suspended side to ensure that both sides are evenly stressed to prevent the bolts from breaking. When installing the liner, the gap between adjacent liner plates should not be greater than 8mm, and all gaps between liner plates should be filled with cement mortar. All bolts extending out of the cylinder and connecting the liner plates should be padded with sealing washers and pressure rings to lock the seal. Only a thin steel plate can be used to fill the gap between the liner plates. When installing the sealing ring, a rubber plate seal must be pressed on.
Points for grinding body alignment
Place the grinding body and make the slip ring enter the sliding shoe bearing. Remember to loosen the support (see relevant requirements). After the cylinder is placed on the sliding shoe bearing, the elevation of both ends of the sliding shoe should be checked. The relative elevation difference should not exceed 0.5mm, and the feed end should not be lower than the discharge end. The center line of the slip ring and the center line of the sliding shoe bearing seat should meet the requirements of the drawing. The relative radial runout tolerance of the slip ring at the feed and discharge ends is required to be 0.2mm.
Points for pouring the bottom plate
Before starting to pour, clean the parts of the bottom plate that will contact the foundation, especially clean up the oil and grease. Carefully pour the bottom plate to ensure that the cavity between the bottom plate and the primary foundation is filled with cement mortar, and pour it with special cement with stable performance, and pour it all the way to 30mm`40mm above the lower edge of the bottom plate.
Comprehensive inspection to ensure that there is no error.
Key points for installing the sliding cover and oil flow signal
Install the contact part between the lower part of the sliding cover and the base plate
Note that when installing the sealing gasket between the cover and the base plate and between each cover segment, the sealing gasket should be coated with Aseal4805 sealant (imported sealant should be selected), then clean the base plate, vacuum the bottom of the sliding cover, check the sealing condition with oil, and be careful not to use water to check, because the bearing seat cannot drain the water through the oil drain hole. The upper part of the sliding cover is composed of several basically identical cover segments, which are connected by flanges and sealing gaskets with bolts. When installing the sliding cover, align each cover segment according to the sealing ring and flange on the sliding ring. The radial spacing between the sliding cover and the sliding ring sealing surface must be equal. When installing the top of the sliding cover, oil should be poured on the surface of the sliding ring. The sealing ring must be coated with oil before installation. When installing the sealing ring and spring, choose the appropriate one of the three specifications of the adjustment plate connecting the spring, and adjust the sealing ring so that the sealing ring and the sliding ring can be evenly contacted over the entire length.
Install the pipeline of low-pressure circulating oil pump and oil flow signaler, and connect it to the sliding shoe cover to inject lubricating oil into the sliding shoe bearing.
Install the electronic control part of the oil flow signaler
It must be able to transmit the signal of insufficient oil or oil cut-off of the oil flow signaler to the control room when the circulating oil pump fails. Start the lubrication pump station, the oil pan and oil distribution groove of the sliding shoe bearing will be filled with oil, the high-pressure oil on the support will make the grinding body float, and start the mill. After the mill is running, stop the lubrication pump station, check whether the oil flow signaler can stop the mill automatically in the control room, and ensure that the mill motor can be restarted only after the oil flow signaler sends a normal oil flow signal.
Ground Granulated Blast Furnace Slag Grinding Vertical Roller Mill Technical Parameter Specification:
Section | Parameter Details |
Name | ZJTL-4640X Slag Vertical Mill |
Application | Slag Grinding |
Mill Specification/Model | JLMK1-46.2.2X |
Production Capacity | Normal: 90 t/h, Max: 95 t/h |
Grinding Table Diameter | 4600 mm |
Number of Grinding Rollers | 2 (Main Rollers) + 2 (Auxiliary Rollers) |
Main Motor Power | Rated: 3000 kW |
Grinding Table Speed | 25.972 min⁻¹ |
Feed Moisture | Max: 10% |
Feed Size | < 10 mm |
Product Fineness | Specific Surface Area: 4200 cm²/g |
Product Moisture | < 0.5% |
Exhaust Air Volume | 315,000 ~ 394,000 m³/h |
Inlet Air Temperature | 200 ~ 300°C |
Outlet Air Temperature | 80 ~ 100°C |
Recirculating Material | Max: 70 t/h |
Water Spray System | Max Usage: 10 t/h, Pressure: 0.5 MPa, Temperature: 0 ~ 50°C |
Maximum Ventilation Resistance | ~6.0 kPa |
Slow Rotation Motor Power | 7.5 kW |
Separator Motor | Power: 250 kW, Variable Frequency Drive, Brand: ABB |
Separator Rotor Speed | Max: 170 min⁻¹ |
Grinding Roller Lifetime | ≥ 7200 h |
Grinding Roller Wear Layer Cycle | 1200 ~ 1500 h |
Grinding Table Liner Lifetime | ≥ 10,000 h |
Grinding Table Liner Wear Layer Cycle | 1200 ~ 1500 h |
Inner Liner Side Plate Lifetime | ≥ 30,000 h |
Grinding Roller Bearing Lifetime | ≥ 15,000 h |
Auxiliary Roller Bearing Lifetime | ≥ 15,000 h |
Separator Bearing Lifetime | ≥ 15,000 h |
Separator Rotor Blade Lifetime | ≥ 12,000 h |
Grinding Roller Bearing Seal Lifetime | ≥ 15,000 h |
Separator Bearing Seal Lifetime | ≥ 7200 h |
Base Vibration | < 0.08 mm (double amplitude) |
Mill Noise | ≤ 85 dB (at 1 meter distance) |
Primary Air Leakage Rate | 3 ~ 5% |
Energy Consumption | Max Power Consumption: ≤ 30 kWh/t during normal operation |
Paint Colors | Mill: Silver Gray, Safety Railings: Yellow, Electrical Cabinets: RAL7032, Covers: Yellow |
Total Weight | 645,000 kg |
Main Motor Weight | 23.62 t |
Main Reducer Weight | 86.5 t |
Ground Granulated Blast Furnace Slag Grinding Vertical Roller Mill Equipment List:
Description | Unit | Specifications |
Mill Dimensions | mm | 15036×9400×16143 |
Motor Power | kW | 3000 |
Slag Roller Mill | ||
– Mill Output | t/h | 90 |
– Specific Power Consumption | kWh/t | <30 |
Product Specifications | ||
– Finished Product Fineness | cm²/g | 4200 |
– Moisture Content | % | <0.5 |
– Cooling Water Consumption | t/h | 7.5-10 (maximum) |
Material | ||
– Product Type | Ultrafine Slag Powder | |
– Bulk Density | t/m³ | 1.13 |
– Slag Moisture Content | %H₂O | 10 (maximum 15) |
– Grinding Power Index | kWh/t | <30 |
– Feed Particle Size | mm | 90% less than 10mm |
– Mill Outer Diameter | mm | φ6180 (Mill Shell) |
Hot Air Balance | ||
– Inlet Air Temperature | ℃ | 200~300 |
– Outlet Air Volume | m³/h | ~360000 (Operating Condition) |
– Outlet Air Temperature | ℃ | 90 |
– Mill Pressure Drop | Pa | 4000~5000 |
Grinding Table | ||
– Outer Diameter | mm | 5000 |
– Table Rotating Speed | r/min | 25.972 |
– Grinding Table Material | ZG270-500 | |
– Grinding Table Liner Material | ZG20SiMn (Overlay Welding Layer) | |
Grinding Rollers | ||
– Quantity | 2 (Main Rollers) + 2 (Auxiliary) | |
– Shape | Conical | |
– Sealing Type | Skeleton Seal + Air Seal | |
– Lubrication Mode | Circulating Lubrication (Main Rollers), Oil Bath Lubrication (Auxiliary Rollers) | |
– Roller Diameter | mm | Main: 2360 (Mid-diameter), Auxiliary: 1700 (Mid-diameter) |
– Roller Width | mm | Main: 770, Auxiliary: 776 |
– Maintenance System | Roller-Flip Cylinder and Hoisting Tools | |
2.2 Feeding Lock Air Device | ||
– Type | Double Pneumatic Flap Valve | |
– Drive | Pneumatic | |
2.3 Slag Discharge | ||
– Lock Air Device | Double-layer Weighted Flap Valve | |
– Capacity | t/h | 70 |
2.4 Main Drive System | ||
Main Motor | ||
– Model | YRKK900-6 | |
– Speed | rpm | 993 |
– Installed Power | kW | 3000 |
High-Speed Coupling | ||
– Model | DL350-00 | |
– Type | Elastic Block Coupling | |
– Quantity | 1 | |
Main Reducer | ||
– Model | JLP330 | |
– Type | Spiral Bevel Gear + Parallel Shaft Gear + Planetary Gear | |
– Speed Ratio | 37.732 | |
– Output Speed | rpm | 25.972 |
– Max Transmission Power | kW | 3300 |
– Design Service Life | Years | 30 |
Thrust Bearing | ||
– High-pressure System | ||
– Oil Pressure | MPa | 32 |
– Oil Flow Rate | L/min | 200 |
Low-Pressure System | ||
– Oil Pressure | MPa | 1 |
– Oil Flow Rate | L/min | 800 |
2.5 Auxiliary Drive | ||
– Mill Rotating Speed | r/min | 0.8834 (maximum, variable frequency) |
2.6 Separator | ||
– Dimensions | ||
– Diameter | mm | 7400 |
– Total Height | mm | 6522 |
– Separator Pressure Drop | Pa | ~2500 |
Rotor | ||
– Rotational Speed | r/min | Maximum 170 |
– Blade Quantity | 60 | |
– Maximum Separator Capacity | t/h | 300 |
– Maximum Air Temperature | ℃ | 120 |
Drive System | ||
– Mechanical Section | ||
– Motor | ||
– Model | D1TP355M2-4 | |
– Power | kW | 250 |
– Rotational Speed | r/min | 1485 |
– Connection Type | Tire-type Elastic Coupling | |
– Gearbox | ||
– Model | B2SV09 | |
– Type | Right-angle Shaft, Upward Output | |
– Speed Ratio | 5.6 | |
– Output Speed | r/min | 265 |
– Rated Power | kW | 560 |
2.7 Hydraulic System | ||
– Pressure (Normal/Max) | MPa | 9~11 / 14 |
– Flow Rate | l/min | |
– Rated Power | kW | |
– Oil Tank Capacity | L | |
– Hydraulic Oil | VG46 Hydraulic Oil | |
– Number of Oil Pumps | pcs | 4 (Main Rollers), 2 (Auxiliary Rollers) |
Hydraulic Cylinder | ||
– Quantity | pcs | 4 (Main Rollers), 2 (Auxiliary Rollers) |
– Specifications | Main: Φ380/Rod Φ160/Stroke 280, Auxiliary: Φ270/Rod Φ125/Stroke 150 | |
2.8 Electrical Control System | ||
– Mill Auxiliary Control Cabinet | pcs | 2 |
φ4.2×13m Granulated Blast Furnace Slag Ball Mill Configuration List
Parameter | Specification/Details |
1.1 Specifications | |
1.1.1 Mill shell inner diameter | 4200 mm |
1.1.2 Mill shell inner length | 13,000 mm |
1.1.3 Effective shell diameter | Chamber I: 4010 mm |
Chamber II: 4080 mm | |
1.1.4 Effective shell length | Chamber I: 4150 mm |
Chamber II: 8250 mm | |
1.2 Purpose | Grinding cement clinker (paired with a roller press) |
1.3 Grinding method | Closed-circuit |
1.4 Feed material size | ≤2 mm |
1.5 Product fineness | 0.08 mm sieve residue 6% |
1.6 Product specific surface area | 3400 cm²/g |
1.7 Production capacity | 150 t/h |
1.8 Mill speed | Main: 15.8 r/min |
Slow drive: 0.16 r/min | |
1.9 Transmission type | Central drive |
1.10 Motor power | 3550 kW |
1.11 Grinding media load | 217–230 t |
1.12 Slide shoe bearings | 2 units |
1.12.1 Thermistors | Model: WZPM-201 |
Quantity: 3 | |
Temperature range: -100–150°C | |
Resistance type: Pt100 | |
Resistance value: 100±0.12Ω (at 0°C) | |
1.12.2 Platinum resistors | Model: WZP-26S |
Quantity: 1 | |
1.12.3 Electric heaters | Model: SRY2-220/2 (2 kW, 220 V) |
Quantity: 2 | |
1.13 Slide shoe bearing oil station | 2 units |
Model | GYXZ-63GⅡ |
Lubrication oil | N320GB5903-86 medium-load industrial gear oil or ISOVG320 mineral oil (refer to the oil station manual) |
Oil supply temperature | 40°C |
Low-pressure pump flow rate | 63 L/min |
Nominal pressure | 0.4 MPa |
Low-pressure pump motor model | Y100L1-4V1 |
Power | 2.2 × 2 (units) = 4.4 kW (1 standby) |
Speed | 1430 r/min |
Voltage | 380 V |
High-pressure pump flow rate | 2.5 L/min |
High-pressure pump pressure | 31.5 MPa |
High-pressure pump motor model | Y112M-6, B35 |
Power | 2.2 × 2 (units) = 4.4 kW |
Speed | 970 r/min |
Voltage | 380 V |
Electric heater | Model: HRY4-380/4 |
Power: 3 × 4 = 12 kW | |
Voltage: 220 V | |
Oil flow indicator | Quantity: 3 |
Model: YXQ-25Ⅱ (220 V, 0.2 A) | |
1.14 Drive system & oil station | Refer to the "Main Reducer Lubrication Oil Station Installation and Maintenance Manual" |
1.15 Cooling water usage | |
Slide shoe bearings | 3.5 × 2 (units) = 7 m³/h |
Slide shoe bearing lubrication system | 6 × 2 (units) = 12 m³/h |
Main motor lubrication station | Refer to the "Main Motor Lubrication Oil Station Installation and Maintenance Manual" |
Main reducer lubrication station | Refer to the "Main Reducer Lubrication Oil Station Installation and Maintenance Manual" |
1.16 Total weight | 249,400 kg (excluding the drive system and grinding media) |