Tongli has been producing rotary kilns for more than 65+ years, from the earliest vertical shaft kiln to the largest 6.2m diameter Kawasaki cement calcination pyro-processing rotary kiln in China.
The limestone cement clinker calcination rotary kiln is designed for the pyro-processing of limestone and clay. After the raw materials are heated, they are converted into highly active clinker or calcined clay, which eventually become the core material for cement production. The tongli rotary kiln adopts a precise temperature control system that can maintain a stable temperature within the range of ±7°C, thereby improving the reactivity of the calcined material. Through the process design of rapid heating, short-term insulation and rapid cooling, the equipment achieves efficient use of fuel, while using hot exhaust gas to dry the raw materials to further reduce energy consumption. The limestone cement clinker calcination rotary kiln combines mature mechanical equipment with modern technological innovations, including components such as crushers, cyclone preheaters, grate coolers, etc., to form a complete set of calcination process flow. The equipment flexibly adapts to different raw material characteristics, and various process requirements can be met by our equipment.
CEMENT CLINKER PYRO PROCESSING EQUIPMENT LIST
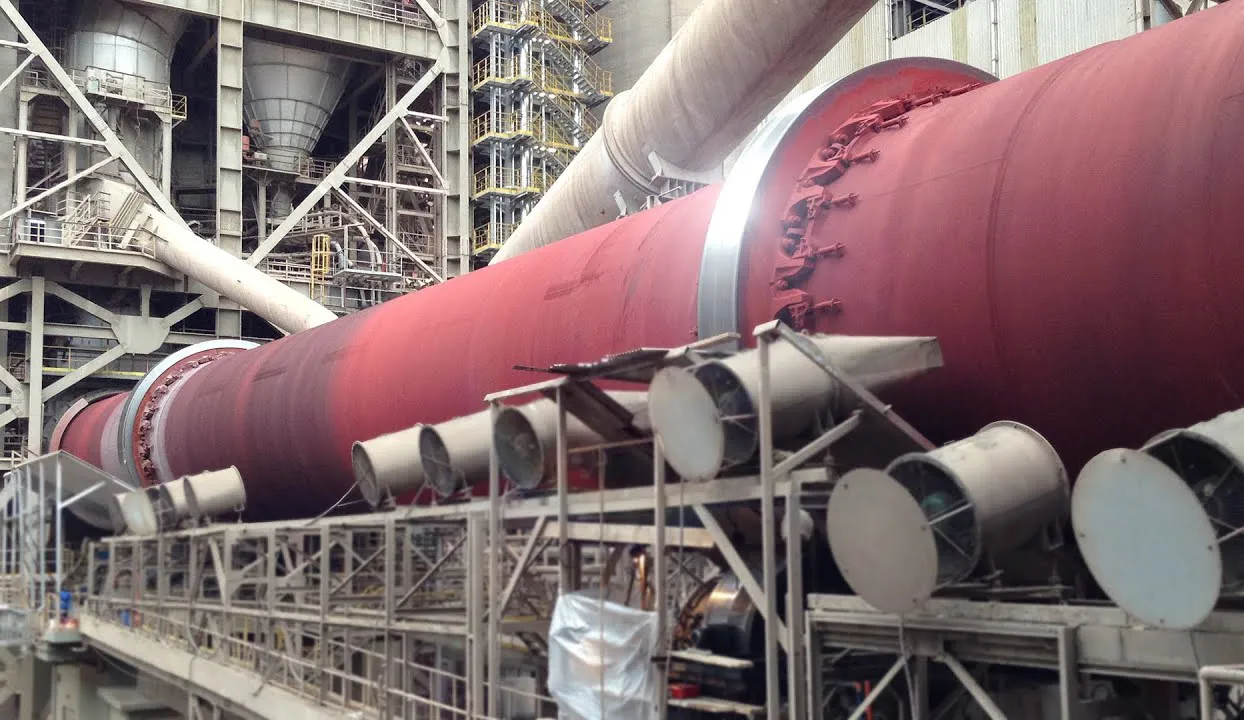
"Revolutionize your limestone processing with a high-efficiency rotary kiln! Achieve up to 95% calcination accuracy. Explore the technology driving cleaner and faster results!"

"Unlock peak clinker quality with our pyro-processing rotary kiln. Precision engineering, 20% energy savings, and unmatched durability—click to learn how it transforms cement production!"

"Safely eliminate hazardous waste with our cutting-edge rotary kiln. Proven 99.99% destruction efficiency. Discover the innovation that meets environmental compliance today!"

"Optimize limestone transformation with our advanced pyro-processing kiln! Up to 30% energy savings and precision heating for superior results. Click to unlock the future of efficiency!"
NPK PRODUCTION LINE ADVANTAGES
Excellent environmental performance: tongli rotary kiln adopts low-emission technology to effectively reduce waste gas and dust emissions during the production process. At the same time, its optimized combustion and thermal efficiency design significantly reduces the carbon footprint, helping users achieve more environmentally friendly production goals.
Safety: Tongli rotary kiln integrates a variety of safety designs to effectively protect personnel and equipment safety. These designs include drive/coupling, gear ring and support roller guards, heat shields, kiln drive rollback control system and maintenance brake, as well as support bearing thermocouples and kiln position indicators.
Flexible customization capabilities: The design of tongli rotary kiln can be flexibly customized according to the user's special needs, including kiln size, material selection, fuel type and operating parameters. This customization capability ensures that the equipment can perfectly adapt to various process flows.
Efficient energy utilization: By optimizing the combustion system and heat recovery design, FLS rotary kiln can minimize energy consumption. Combined with modern fuel selection and intelligent control technology, it ensures that the thermal energy utilization efficiency in the production process reaches the industry-leading level.
Reliable and controllable heat treatment: The internal structure of the Tongli rotary kiln shell optimizes heat transfer, and can achieve the best results regardless of the process used. At the same time, the fuel/air injection system in the kiln can accurately control the reaction temperature to ensure the reliability and stability of the process.
Long service life: The full floating cast or forged riding ring design ensures smooth operation of the equipment, while the proprietary sleeve bearing can minimize vibration. The hydraulic/mechanical thrust device helps to keep the equipment aligned, and the kiln shell material can also be customized according to the specific application to effectively control wear. The service life of the Tongli rotary kiln can reach more than 20 years.
Superior modular maintenance design: TONGLI rotary kiln adopts modular design concept, which makes the maintenance and overhaul of equipment more convenient. Key components such as gears, support devices and burners can be replaced or repaired separately, reducing downtime and maintenance costs.
Intelligent monitoring and control system: Tongli rotary kiln is equipped with advanced intelligent monitoring and automatic control system to ensure the accuracy and efficiency of operation. Real-time data acquisition and analysis functions can monitor key parameters, detect abnormal conditions in time and issue early warnings.
CEMENT CLINKER PRODUCTION PROCESS

1. Raw material preheating
The raw materials first enter the preheater tower through the feed system. The preheater uses the high-temperature exhaust gas from the rotary kiln outlet to preheat the raw materials, gradually raising their temperature to about 800°C. This process not only reduces the fuel consumption in the kiln, but also improves thermal efficiency. The preheated raw materials undergo partial decomposition, preparing for the subsequent calcination process.
2. Decomposition in the calciner
The preheated raw materials enter the calciner (if configured) through the air flow, where they are fully mixed with the injected fuel and hot air flow, and the temperature is further increased to about 850-900°C. At this time, the carbonates in the raw materials begin to chemically decompose, releasing carbon dioxide and generating calcium oxide and other intermediates. The design of the calciner ensures sufficient mixing and reaction efficiency, providing more uniform materials for the reaction in the kiln.
3. Rotary kiln calcination
The decomposed materials enter the rotary kiln for high-temperature calcination. In the kiln, the raw materials undergo a series of chemical and physical changes, including further carbonate decomposition, mineral reorganization and clinkerization. As the material gradually moves toward the kiln tail, the temperature gradually rises to 1350-1450°C, and finally forms clinker. The temperature and airflow inside the rotary kiln are precisely controlled by fuel injection and air distribution to ensure stable product quality.
4. Grate cooler cooling
After the clinker comes out of the rotary kiln, it enters the grate cooler for rapid cooling. The grate cooler cools the high-temperature clinker through forced air, quickly reducing its temperature to 100-200°C. This process not only protects subsequent equipment from high temperature damage, but also preheats the cooling gas and recycles it as secondary air in the kiln or decomposition furnace, further improving the efficiency of thermal energy utilization.
5. Clinker Grinding
The cooled clinker is sent to the mill for grinding through a conveying device. In the mill, the clinker is ground into cement powder together with a certain proportion of gypsum or other mixed materials to complete the production of the final product. The entire process achieves efficient energy utilization and maximizes production capacity while ensuring the quality and performance of cement.
VIDEO
WHY CHOOSE US
"Our company has been using Tongli Cement Clinker Rotary Kiln for three years. The equipment runs stably, which has saved us a lot of fuel costs. Both the clinker quality and energy consumption indicators have met expectations, and we are very satisfied!"
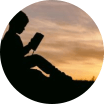
CFO
"The design and materials of Tongli rotary kiln are very sophisticated, especially the kiln shell and internal components are very durable. Our equipment has been running continuously for 5 years, and the maintenance cost has been kept at a low level."

CEO
"Tongli's rotary kiln is very advanced in design and equipped with PLC control system that can monitor production parameters in real time and detect and solve problems in a timely manner. In addition, Tongli's after-sales service is also timely and professional, and any problems can be responded to quickly and help We reduced downtime! ”

CEO
“We chose Tongli Rotary Kiln because Tongli is an OEM manufacturer of major cement equipment manufacturer like cemtec. We can buy equipment of the same quality as international first-class brands such as FLS at a relatively low price, which brings significant economic benefits. ”

CEO
FAQ
Cement clinker is a semi-finished product obtained by mixing limestone, clay and iron raw materials in appropriate proportions, burning them until they are partially or completely melted, and cooling them. In the cement industry, the most commonly used silicate cement clinker has calcium oxide, silicon dioxide and a small amount of aluminum oxide and iron oxide as its main chemical components.
The main mineral components are tricalcium silicate, dicalcium silicate, tricalcium aluminate and tetracalcium aluminoferrite. After silicate cement clinker is ground with an appropriate amount of gypsum, it becomes silicate cement. Clinker is the main component of cement particles and is composed of four minerals: C3S, C2S, C3A and C4AF. Among them, the most important mineral affecting cement strength is C3S. With the increase of C3S content in clinker, the early strength increases, and the content in clinker composition is above 60%; C2S is a secondary mineral in clinker, which plays an important role in the long-term strength of cement, especially the long-term strength after one year; C3A can adjust the performance of cement, with high hydration heat and fast hydration speed, so the content cannot be too much, generally cannot exceed 8%; C4AF has lower hydration heat than C3A, which improves wear resistance. Among them, with the increase of silicon rate and C2S in clinker, the grindability of clinker decreases, and with the increase of Al2O3, C3S, KH, the grindability increases.
1. Raw material preparation:
Raw material preparation is the process of processing cement raw materials, which includes the crushing and pre-homogenization of raw materials and the grinding and pre-homogenization of raw materials. The main raw materials of silicate cement are lime raw materials and earth raw materials. Sometimes, according to the quality of raw materials and cement types, correction raw materials are added to supplement the deficiency of certain components. At the same time, industrial waste or mixed materials can be used as raw materials for cement. The raw materials obtained from the mine are all large-sized stones. This kind of raw material has high hardness and is difficult to grind and burn directly. The crushing process is to crush the large pieces of raw materials into small and uniform materials as much as possible to reduce the load of the grinding equipment and increase the output of the mill. After the raw materials are crushed, the separation of raw materials of different particle sizes caused by transportation and storage can be reduced as much as possible, which is conducive to the homogenization of raw materials in the next step. Raw material pre-homogenization is a process to improve the stability of cement raw material composition and improve production quality. There are many methods for homogenizing materials. The main methods are: "human" shaped material stacking method, horizontal layer material stacking method, wave-shaped material stacking method, and horizontal inclined layer material stacking method. Then, according to different material stacking methods, end-face material, side material or bottom material are taken. This can minimize the fluctuation of raw material composition caused by mining, transportation and other factors. After crushing and homogenization, the raw materials are mixed in proportion and then sent to the raw material mill for grinding. The grinding process can further reduce the particle size of the material. When the same heat is provided, the smaller the raw material particle size, the faster the reaction speed and the easier the clinker sintering. The last step of raw material preparation is pre-homogenization treatment, which is also an operation that can effectively improve the stability of raw material composition before the clinker preparation process. Raw material homogenization is generally carried out in the raw material homogenization silo, using air stirring to produce a "funnel effect" under the action of gravity, which promotes the full mixing of raw materials during the falling process.
2. Clinker calcination:
Clinker firing can be divided into four processes: suspended preheating, decomposition outside the kiln, sintering in the kiln and clinker cooling. The common preheater is a multi-stage cyclone preheater, in which the hot exhaust gas and the raw meal exchange heat. The raw meal is fed from the top first-stage cyclone connected to the air duct. Driven by the high-speed rising airflow, the raw meal turns upward and moves with the airflow, and then is sent into the cyclone. Under the action of airflow and gravity, the material falls down along the wall of the cylinder, and finally enters the feeding pipe of the next cyclone, repeating the above movement process. After preheating in the five-stage cyclone, the raw meal can be heated to about 800℃, while the hot exhaust gas is reduced from about 1100℃ to about 300℃. Since the material is in a suspended and dispersed state in the cyclone, the heat exchange process can occur quickly. The use of the preheater makes full use of the exhaust gas generated at the end of the kiln and reduces the heat consumption of clinker firing. The first-stage cyclone at the bottom of the preheater is connected to the decomposition furnace. The material enters the decomposition furnace through a pipeline and is decomposed therein. The raw material and the coal powder sprayed into the decomposition furnace are fully dispersed, mixed and evenly distributed in the furnace. The high temperature in the furnace causes the coal powder to burn and quickly transfer heat to the material. Under the action of high temperature, the carbonate in the material quickly absorbs heat, decomposes and releases carbon dioxide. Before entering the kiln, the decomposition rate of the material can reach more than 90%, which further reduces the heat load of cement calcination in the kiln and improves the utilization rate of coal powder. After entering the rotary kiln, the material is further decomposed and moves forward with the rotation of the kiln. The heat generated by the combustion of coal powder in the kiln causes a series of chemical reactions in the material, and finally generates tricalcium silicate, the main component of cement clinker.
3. Clinker cooling:
The clinker is then sent to the grate cooler, which uses air cooling. The grate cooler is a quenching cooler. After the clinker enters the cooler from the kiln, it forms a material layer of a certain thickness on the grate plate. The cold air blown in passes through the material layer moving on the grate bed in a mutually perpendicular direction to quench the clinker, which can quench the clinker from 1300-1400℃ to below 100℃ within a few minutes. The traditional grate cooler is divided into three types: rotary, vibrating and push-type. However, since the first two types have been eliminated, the push-type grate cooler has become the main cement clinker cooler model used in conjunction with the decomposition kiln outside the kiln. The grate bed is the main component of the cooler, and the push-type grate plate is composed of fixed grate plates and movable grate plates arranged in rows.
4. Cement clinker grinding:
Cement grinding is the last process of cement manufacturing and also the process that consumes the most electricity. Its main function is to grind cement clinker (and retarder, performance adjustment material, etc.) to a suitable particle size (expressed by fineness, specific surface area, etc.), form a certain particle gradation, increase its hydration area, accelerate the hydration rate, and meet the requirements of cement paste coagulation and hardening.
According to the process flow, cement grinding can be divided into three types: open circuit grinding system, closed circuit grinding system and combined grinding system. According to the use of equipment, cement grinding system can be divided into ball mill grinding system, vertical mill final powder system, vertical mill-ball mill combined grinding system, roller press final powder system, roller press-ball mill combined grinding system and horizontal roller mill (Horomill) grinding system. With the development of science and technology, more types of cement grinding systems may appear in the future.
In the open circuit grinding process, the material is the product after passing through the mill. The process is simple, the equipment is small, and the investment is low, but it is easy to produce over-grinding. In the closed-circuit grinding process, the material is screened out by the powder selector after leaving the mill, and the coarse powder is returned to the mill for re-grinding, which reduces the phenomenon of over-grinding, can increase production, reduce power consumption, and the product fineness is easy to control, but the system equipment investment is large, and the operation and maintenance are more complicated. The combined grinding system process is that after the material is pre-grinded by the roller press or vertical mill, the fine material is screened out and enters the ball mill for final grinding. The powder selector and dust collection system select the finished product that meets the requirements. Compared with the closed-circuit grinding system, the combined grinding system has higher output and lower energy consumption, but the equipment investment is larger and the operating system is more complicated.
The ball mill grinding system uses the ball mill alone as the main grinding equipment to achieve the final grinding effect. The vertical mill final grinding system uses the vertical mill as the main equipment for grinding, which is more efficient, but due to the unsatisfactory particle grading and particle surface shape, it is not conducive to cement hydration, which affects the strength of cement. The vertical mill-ball mill combined powder system first pre-grinds the material through the vertical mill before it enters the ball mill for final powdering. The fine materials that meet the requirements are classified and then enter the ball mill for final powdering. It is highly efficient and finally the ball mill is used for final powdering to ensure good particle grading and surface shape.
The roller press final powdering system uses the roller press as the main equipment for powder grinding. The efficiency is higher than that of the vertical mill final powdering system, but the particle grading and surface shape of the product are still not ideal. The roller press-ball mill combined powdering system sends the fine materials that meet the requirements into the ball mill for final powdering after the material is pre-grinded by the roller press. Compared with the vertical mill-ball mill combined powdering system, it is more efficient and has better final powdering effect. The horizontal roller mill (Horomill) is a new type of powder grinding equipment with similar energy efficiency to the roller press and large output. It is mainly used to replace the ball mill, although there are only a few in China. However, according to its powder grinding principle, the particle condition of the tablets is similar to that of the vertical mill final powdering system, so the particle shape and grading may not be ideal.
(1) Kiln shell: The cylinder of the rotary kiln is rolled from steel plates, and has evolved from riveting to full welding. The cylinder should have sufficient rigidity and strength to ensure the linearity of the axis and the roundness of the cross section during installation and operation. The cylinder is lined with refractory materials to protect the cylinder and reduce heat dissipation. The cylinder lining bricks should meet the requirements of operating conditions. The preheating zone generally uses clay bricks, and the firing zone is selected according to factors such as calcination temperature and chemical erosion. The rotary kiln for calcining iron ore is generally built with clay bricks or grade 3 high-alumina bricks. Kiln mouth guard plates are installed at both ends of the cylinder to prevent the cylinder from deforming and cracking due to the action of hot materials or high-temperature flue gas, and to prevent the kiln lining from falling off. Since the working temperature of the kiln mouth is sometimes as high as 1000-1300℃, the kiln mouth guard plates should be made of replaceable heat-resistant and wear-resistant materials, and air cooling or water cooling measures should be adopted when necessary.
(2) Riding rings: Several roller rings (riding ring) are installed on the cylinder to divide the cylinder into several spans. The weight of all rotating parts such as the cylinder, kiln lining, materials and kiln skin is transferred to the support device through the roller. The roller is cast or forged from carbon steel or alloy steel with good wear resistance and high contact fatigue strength. The cross-sectional shapes of the roller are rectangular and box-shaped. Currently, most rollers with rectangular cross-sections are used. A moderate gap is left between the roller and the cylinder, which can enhance the rigidity of the cylinder without causing large thermal stress on the cylinder and the roller.
(3) Support device: It bears the entire weight of the rotating equipment. It plays an axial and radial positioning role for the cylinder, allowing it to operate safely and smoothly. The support device consists of a supporting roller, a supporting roller shaft, a supporting roller bearing, a retaining wheel and a base. The supporting roller is in direct contact with the roller. The axis of each set of supporting rollers must be parallel to the center line of the cylinder, and the three-point line connecting the center of the two sets of supporting rollers and the center of the cylinder section should form an equilateral triangle. The width of the supporting wheel is slightly wider than the rolling ring. It is made of wear-resistant cast steel. The supporting wheel section has three structures: single wheel, double wheel and three wheel. There are two installation methods: mandrel type and rotating shaft type. The rotating shaft supporting wheel shaft is generally assembled by heat fitting. The supporting wheel bearing structure is divided into sliding bearing, rolling bearing and sliding-rolling bearing, etc. Most of them use sliding bearings. The lining of the sliding bearing is inlaid on the spherical bearing to form a spherical contact, which can automatically align the heart. The oil spoon is lubricated with oil, and the spherical bearing is cooled by water. The shaft end is equipped with a thrust plate, and the shoulder has a thrust ring to withstand the axial thrust. The bearing is fixed on the steel base and has a top screw for adjusting the position of the supporting wheel. Although rolling bearings have the advantages of simple structure, low friction resistance and low power consumption, the one-time investment of large bearings is large and the life is lower than that of sliding bearings. Except for the former Soviet Union, which uses rolling bearings on the supporting device of large-diameter rotary kilns, the rotary kilns in the United States, Denmark and Japan all use sliding bearings. China only uses rolling bearings in some small and medium-sized rotary kilns. The function of the stopper is to limit or control the axial movement of the cylinder. The number of groups of kiln support devices is called the number of kiln gears. Stoppers can be installed on one or more gear support devices, which is called a support device with stoppers. In addition to hydraulic stoppers, only one group of stoppers is installed on both sides of the roller ring near the large gear ring. According to their functions, stoppers are divided into "signal stoppers", "thrust stoppers" and "hydraulic stoppers". "Signal stoppers" are mostly used in old kilns. They are not stoppers to prevent axial movement of the kiln body, but only serve as signals. "Thrust stoppers" bear the downward force of the kiln body and limit the axial movement of the cylinder. "Hydraulic stoppers" push the stoppers through hydraulic devices, forcing the cylinder to move axially, ensuring uniform wear of the roller ring and the support wheel over the entire width and linearity of the cylinder to reduce power consumption. This device can use several small hydraulic stoppers at the same time to jointly bear the axial movement of the kiln body, which is particularly suitable for rotary kilns with large diameters and multiple gears.
(4) Transmission device: The power is transmitted to the large gear ring fixed on the cylinder with a spring plate through the reduction mechanism, so that the cylinder rotates slowly. Due to the requirements of transportation and installation, the gear ring is split in two halves, and the number of teeth is even. The spring plate has two types: tangential and longitudinal. The kiln transmission device is characterized by a large transmission ratio, smooth and stepless speed regulation, and a large starting torque. It is divided into two systems: main transmission and auxiliary transmission. The main transmission system is mostly composed of a main motor, a main reducer, gears and a large gear ring. It can also be added with a semi-open gear or belt drive in the middle, or a dual transmission method with two sets of motors and reduction mechanisms. The main motor should have a speed regulation function.
The function of the auxiliary transmission system is to rotate the kiln body regularly when the main motor or main power supply fails to avoid deformation and bending of the cylinder. It is also used when the kiln body is bricked or repaired. The auxiliary motor drives the auxiliary reducer, which is connected to the high-speed shaft of the main reducer through a clutch. The auxiliary motor and the main motor are powered by different power supplies. The auxiliary motor can also be replaced by a diesel engine.
(5) Kiln head/hood cover. Connect the kiln head end of the cylinder with the cooling device. The hood is built with clay bricks and is equipped with fire-watching holes and inspection doors for monitoring the combustion of fuel and materials in the kiln. There are two types of kiln head hoods: fixed and mobile. Most large rotary kilns use fixed ones.
(6) Sealing device. Prevent air from being sucked in from the gap between the rotating parts of the kiln and the fixed device or the gas carrying dust in the kiln from leaking out. There are kiln head and kiln tail seals. The seal between the kiln head hood and the cylinder is called the kiln head seal; the seal between the dust collection chamber and the cylinder is called the kiln tail seal. The basic requirements of the sealing device are first of all good sealing performance, which can adapt to the cylinder roundness tolerance value and axial movement amplitude during operation; in addition, it is simple in structure, easy to maintain, wear-resistant and does not affect the thermal system of the kiln. There are three types of sealing devices: labyrinth type (torcupine type), contact type (friction type) and gas seal type. The above two or three types can also be used in combination.
(7) Dust collection chamber. Located at the end of the kiln, it is built with red bricks, with clay bricks inside and reinforced with steel frames outside. A feeding pipe is installed on the top to feed the material directly into the kiln. The flue gas enters the dust collecting chamber from the kiln end. Due to the reduced flow rate, part of the dust settles in the chamber. The side wall is equipped with a flue gas exhaust pipe, and the lower part of the chamber is equipped with a dust cleaning door or a mechanical ash transport device. When a preheating device is used at the end of the kiln, no dust collecting chamber is provided.
(8) Combustion device. Depending on the fuel, the combustion device includes a coal injection pipe, an oil burner and a gas burner. The combustion device is installed on a bracket and extends from the kiln head into the kiln in a cantilevered form. The support frame is equipped with a burner adjustment mechanism to adjust the position of the flame.
(9) Hot smoke chamber. Located at the lower part of the kiln head hood, it is built with red bricks, lined with clay bricks inside, and reinforced with steel frames outside. A discharge port is provided on one side of the middle to slide the calcined material from the rotary kiln to the cooling device. The cold air entering the cooling device exchanges heat with the calcined material in the rotary kiln, and its temperature can reach about 500℃. It is then sucked into the kiln by the exhaust device and used as secondary air. A small door is installed on the side wall of the hot smoke chamber for observing and handling the lumps of material.
The wet rotary kiln is a cement kiln used in the wet production process, which is characterized by mixing raw materials with water to make a slurry with a moisture content of 30% to 40%. This muddy raw material has the characteristics of good fluidity and uniform mixing, which can make the raw material composition more uniform, so that the quality of the burned clinker is high. The significant advantages of the wet production process are that it can effectively utilize heterogeneous raw materials, has strong adaptability to raw materials, a stable production process, a high clinker strength grade, and less dust and fly ash generated during the grinding process. Therefore, this process has certain advantages in producing high-quality cement. The kiln body of a wet rotary kiln is usually longer, with an aspect ratio of 30 to 40. In order to increase the heat transfer area and accelerate the evaporation of moisture in the slurry, chains are often hung at the tail of the kiln. The purpose of this chain is to transfer heat to the wet material more efficiently, thereby increasing the thermal efficiency of the kiln.
In the production process of the wet rotary kiln, the slurry is homogenized to meet the requirements and then fed into the rotary kiln through a feeder. During the calcination process in the kiln, moisture is gradually evaporated, and then the raw material completes a series of complex chemical reactions, including decomposition and recombination, and finally produces clinker. After leaving the kiln, the clinkers are cooled by coolers and then sent to the clinker warehouse for storage. The raw coal used in production needs to be dried and ground into coal powder to provide the kiln with the heat required for combustion. However, a significant disadvantage of the wet process is that evaporating the slurry moisture requires a lot of heat, which makes the wet rotary kiln energy consumption high. According to statistics, its heat consumption accounts for 1/2 to 1/3 of the cement production cost. At the same time, the wet process consumes a lot of water, which not only increases the consumption of water resources, but also brings certain environmental pressure. Therefore, as energy and environmental issues become increasingly severe, my country has listed wet cement production as a process that needs to be restricted and eliminated.
In contrast, dry rotary kilns use dry powdered raw materials with a moisture content of less than 1% as raw materials. The dry production process uses modern preheaters and decomposition furnaces to complete most of the heat exchange and decomposition process of the raw materials before entering the rotary kiln. The kiln length of the dry process rotary kiln is relatively short. This design, combined with an efficient exhaust gas recovery system, greatly reduces heat loss, thereby significantly reducing energy consumption. Since no additional heat is required to evaporate water, dry rotary kilns are more energy-efficient and environmentally friendly than wet rotary kilns. In addition, the dry process uses very little water, which helps protect water resources. However, in the dry process, since the raw material is a dry powder, its fluidity is poor and the uniformity of raw material mixing is difficult to ensure. This deficiency may lead to uneven distribution of clinker components and have a certain impact on product quality. Therefore, the dry process places higher demands on the raw material pretreatment and mixing equipment.
The difference between wet rotary kiln and dry rotary kiln mainly lies in the preparation method of raw materials, energy consumption, environmental protection effect and equipment design. Wet rotary kiln was once widely used in cement industry because of its strong adaptability to raw materials and high clinker quality. However, with the improvement of environmental protection requirements and the promotion of energy conservation and emission reduction policies, its high energy consumption and high water consumption problems have caused it to be gradually replaced by dry rotary kiln. The dry rotary kiln has become the mainstream process in modern cement production due to its low energy consumption, low waste gas emissions and high resource utilization. Especially in the context of the current transformation of the cement industry towards green and energy-saving, the dry rotary kiln has further improved production efficiency and reduced environmental impact through continuous optimization and technological innovation.
(1)What is a vertical kiln?
A vertical kiln, also called a shaft kiln or a vertical shaft kiln, is a vertically fixed cement kiln equipment, commonly used in the production of small cement plants. According to the structural characteristics, vertical kilns are divided into ordinary vertical kilns and mechanical vertical kilns, of which mechanical vertical kilns are more suitable for small-scale production. This technology has been eliminated in China, and only limestone calcination still uses the Maerz double-chamber lime kiln.
(2)What are the advantages and disadvantages of vertical kilns?
Vertical kilns have small investments and quick production results, and are particularly suitable for production environments with limited funds. It has a high unit volume output, good heat conduction efficiency, and low heat loss, accounting for about 3% of the total heat. In addition, vertical kilns can use local resources, such as industrial residues, as raw materials. However, its production scale is limited, the degree of automation is low, the labor intensity is high, and the output of a single machine is difficult to meet large-scale industrial needs.
(3)What is a cement rotary kiln?
A cement rotary kiln is a cement kiln equipment that can rotate horizontally, which is divided into two types: internal heating type and external heating type. The internal heating type allows the material to directly contact the flame and flue gas to complete the calcination, while the external heating type completes the calcination through indirect heat transfer through the kiln wall.
(4)What are the advantages and disadvantages of cement rotary kiln?
Cement rotary kiln has a stable structure and stable operation. It can produce high-quality cement clinker, has low unit production cost and high combustion efficiency. It also has significant environmental advantages and can treat hazardous waste and garbage as fuel. However, its initial investment is high, it occupies a large area, and there is a certain amount of heat loss during operation.
(5)What are the main differences between vertical kiln and cement rotary kiln?
Vertical kiln is a vertical fixed structure suitable for small-scale production; cement rotary kiln is a horizontal rotating structure suitable for large-scale, high-quality industrial production. The rotary kiln has a higher thermal energy utilization rate and better environmental performance, but the initial investment is large, while the vertical kiln is economical and practical.
(6)Should I choose a vertical kiln or a cement rotary kiln?
If it is a small-scale production with limited funds, the vertical kiln is an ideal choice because of the small investment and fast commissioning. If you pursue large-scale, high-quality production and attach importance to long-term economic benefits and environmental performance, the cement rotary kiln will be more suitable. The specific choice should be considered comprehensively based on actual needs and budget.
According to the purpose, kilns can be divided into lime kilns, cement kilns and chemical kilns. Lime kilns are mainly used for calcining limestone to produce lime, cement kilns are dedicated to calcining cement clinker, and chemical kilns are often used in the chemical industry to process specific raw materials or generate chemical products.
(1) Classification by combustion method: It is divided into direct combustion kilns and indirect combustion kilns. In direct combustion kilns, the fuel is directly burned and in contact with the material, such as the internal heating method of cement rotary kilns. Indirect combustion kilns burn the fuel outside the kiln and transfer the heat to the material through the kiln wall. It is suitable for processing highly polluted or highly sensitive raw materials.
(2) Classification by cooling method: Kilns can be divided into natural cooling kilns and forced cooling kilns. Natural cooling kilns cool the material through natural ventilation and are suitable for small-scale production; while forced cooling kilns use fans or cooling water systems to accelerate cooling and are often used for large-scale and high-efficiency production.
(3) Classification by feeding method: Depending on whether the raw materials bring water into the kiln, rotary kilns can be divided into dry rotary kilns and wet rotary kilns. Wet kilns can be further divided into inflow method and injection method. In addition, there is a process in which the raw materials are made into pellets and then preheated and calcined, which is called the semi-dry process.
(4) Classification by length-to-diameter ratio: According to the ratio of the length to the diameter of the kiln body (L/D), rotary kilns can be divided into short kilns and long kilns. Generally, the L/D ratio of a dry kiln is about 16, which is a short kiln; the L/D ratio of a wet kiln is between 30-42, which is a long kiln. In addition, the drying process of a spray drying kiln is shorter, and its L/D ratio is between 20-25.
(5) Classification by heating method: According to the heating method, rotary kilns can be divided into internal heating kilns and external heating kilns. Internal heating kilns are kilns in which the materials are directly in contact with flames and flue gases for calcination, while external heating kilns are indirectly heated through the kiln wall and are often used to process materials containing highly toxic substances or in situations where high requirements are placed on flue gas concentration and purity.
(6) Classification by discharge method: In terms of discharge method, kilns can be divided into continuous discharge kilns and intermittent discharge kilns. Continuous discharge kilns have continuous material and clinker inflow and outflow, which is suitable for large-scale production; intermittent discharge kilns complete feeding, calcination and discharging within one production cycle, which is suitable for the production needs of small batches or special products.
(7) Classification by kiln type: According to the geometric shape of the kiln body, rotary kilns can be divided into straight kilns, cold end expansion kilns, firing zone expansion kilns and two-end expansion kilns. Different kiln body structure designs are designed to optimize thermal efficiency, material flowability and calcination process.
(8) Classification by fuel type: Kilns can be divided into coal kilns, oil kilns, gas kilns and electric kilns. Coal kilns use coal powder or lump coal as fuel and are suitable for traditional cement and lime production; oil kilns use heavy oil or light oil and are suitable for heating requirements under special conditions; gas kilns use natural gas or coal gas as fuel, which has uniform combustion and excellent environmental performance; electric kilns are heated by resistance or induction and are mainly used in the production of fine chemicals or high-purity materials.
(9) Classification by process: According to the different atmospheres during the calcination process, kilns can be divided into oxidizing atmosphere kilns and reducing atmosphere kilns. Oxidizing atmosphere kilns are suitable for calcination processes in high oxygen environments, such as the production of oxide products; while reducing atmosphere kilns control low oxygen environments and are used for reducing reactions such as metal ore roasting.
There are 6 main factors that affect the price of rotary kiln equipment. The first is the configuration of the equipment. Equipment configuration refers to the systems and components that are equipped with the rotary kiln, including preheating system, combustion system and burner. If the rotary kiln is equipped with these additional systems, its price will increase accordingly. In addition, the core components of the rotary kiln, such as the kiln body, support device, transmission device and clinker cooling system, will also directly affect the price. The different quality and technical requirements of these configurations and components will lead to differences in the cost of equipment.
Secondly, the processing technology is also an important factor affecting the price of the rotary kiln. In the manufacturing process of the rotary kiln, the welding process used has a great impact on the cost. For example, when using automatic submerged arc welding technology to produce rotary kilns, due to its high degree of automation, higher precision and higher production efficiency, the cost is much lower than manual welding. The price difference brought by different processing technologies is also very obvious. In the material of the cast steel parts of the rotary kiln, different materials will affect its price. For example, the commonly used 42CrMo or 35CrMo materials are high-quality cast steel materials, and their cost is much higher than some unnumbered cast steel materials.
The material selection of the rotary kiln will also have an important impact on its price. If the design of the rotary kiln requires the use of all stainless steel or all carbon steel, the price difference between the two is also very obvious. This is because the cost of stainless steel is significantly higher than that of carbon steel. For some customers who need an external combustion rotary kiln, stainless steel materials must usually be used due to the high working environment temperature. Therefore, the choice of materials will directly affect the price of the rotary kiln, and even produce a large difference.
Next, let's talk about the impact of the size of the gray kiln on its price. The diameter of the kiln directly determines its cost. For example, a gray kiln with a diameter of 4 meters may need to have a wheel size of about 4.5 meters. The price of gray kilns of different diameters will also be different.
Further,When the diameter of the rotary kiln's large gear exceeds 4 meters, a split large gear design is usually required. This split large gear is more expensive than the integral large gear because it requires more processing technology, higher assembly accuracy, and more stringent annealing requirements. These additional processing and processing steps make the production cost of the split large gear significantly higher than the integral large gear.
Next are some issues about the brand and configuration of other auxiliary equipment, such as the choice of motor and gearbox. If you choose a brand motor like Siemens, the price will naturally be higher because it is an imported product; similarly, if the gearbox is an imported brand such as Flender, its price will also be relatively expensive, and the delivery cycle is usually longer.
Therefore, in summary, the price of a small rotary kiln is generally between RMB 1 million and 3 million, which is approximately USD 140,845 to 422,536. A medium-sized rotary kiln, with a diameter of about 4 to 5 meters and a length of about 50 to 70 meters, costs about RMB 6 million to 10 million, or approximately USD 845,070 to 1,408,450. For super-large rotary kilns, where the diameter exceeds 6 meters and the length can reach more than 100 meters, the price is usually more than RMB 20 million, which is roughly USD 2,816,905 or more.
Oxygen-enriched combustion is a highly efficient combustion technology. By using a combustion aid with a higher oxygen content than air, it can effectively shorten the combustion time of coal, improve the combustion efficiency and combustion temperature. In recent years, membrane oxygen production technology has been developed and utilized, the cost of oxygen-enriched combustion technology has been greatly reduced, and the scope of application has also expanded.
This article combines the tongli heavy machinery cement engineering center's research and practice for many years to explore the application of oxygen-enriched combustion technology in cement kilns for reference. Since its birth, the cement industry has always used conventional air as the source of oxygen required for fuel combustion. Therefore, the energy-saving technology developed around fuel combustion is mainly the development and innovation of the kiln head burner based on this oxygen supply method, including changing the ratio of burner airflow and coal powder, changing the rotation mode of airflow, increasing the contact between coal powder and air, optimizing the shape and length of the combustion flame, and increasing the adaptability of coal powder.
However, compared with the ideal energy-saving requirements, the currently used combustion technology has some disadvantages. In the cement industry, oxygen-enriched combustion has shown its advantages over air-supply combustion technology: this technology can reduce the volume of exhaust gas, reduce heat loss in this part, increase flame temperature and blackness, increase the radiation heat transfer capacity of the flame to the material, and increase the CO2 concentration in the exhaust gas to facilitate its capture and storage.
In addition, this technology also has some potential advantages, such as reducing air leakage, reducing kiln tail ringing, and reducing equipment size. Therefore, oxygen-enriched combustion technology has pointed out a new direction for the cement industry to develop a low-carbon economy, save energy and reduce emissions, and take a green and environmentally friendly path, and it has also continuously realized the transformation from concept to practical application.
1. Preparation of oxygen-enriched air:
The preparation of oxygen-enriched air is one of the key factors for the application of oxygen-enriched combustion technology and is also a major research topic at home and abroad. At present, industrial oxygen production methods can be roughly divided into three methods: air freezing separation method, pressure swing adsorption method and membrane oxygen production method.
(1) Air freezing separation method. This method is a method of preparing oxygen from air by taking advantage of the different boiling points of oxygen and nitrogen in the air. First, the air is pre-cooled and purified (removing a small amount of moisture, carbon dioxide, acetylene, hydrocarbons and other gases and dust and other impurities in the air), and then compressed and cooled to make it liquid air. Secondly, the liquid air is evaporated and condensed multiple times in the distillation tower to finally separate oxygen and nitrogen.
(2) Pressure swing adsorption method. The pressure swing adsorption method uses the characteristic that nitrogen molecules are larger than oxygen molecules to separate oxygen from the air using a special molecular sieve. First, use a compressor to force dry air through the molecular sieve. The nitrogen molecules in the air are adsorbed by the molecular sieve, and oxygen enters the adsorber. When the oxygen in the adsorber reaches a certain amount (the pressure reaches a certain level), the oxygen outlet valve can be opened to release oxygen.
(3) Membrane oxygen production. The principle is: driven by the gas partial pressure difference on both sides of the membrane, the molecules move through the membrane in the direction of decreasing chemical potential to the outer surface of the membrane and dissolve in the membrane, and then diffuse to the inner surface layer of the membrane for desorption. Since the rate of O passing through the membrane is greater than the rate of N passing through the membrane, O passes through the membrane surface first, and most of N is directly discharged into the atmosphere from the exhaust hole, thereby achieving the purpose of gas separation. Considering the actual situation of the new dry kiln, as well as factors such as oxygen production cost and equipment maintenance, membrane oxygen production has obvious advantages from both the operation perspective and the investment cost. Therefore, the use of membrane oxygen production on modern small and medium-sized cement production lines is a relatively economical and feasible way of oxygen production.
2. Implementation method of oxygen-enriched combustion technology
Due to the large gas consumption of the new dry process cement production line, it is difficult to achieve full oxygen-enriched combustion with the existing oxygen production technology. Therefore, in cement production lines, local oxygen-enriched combustion technology is generally used, mainly including the following forms:
(1) Use oxygen-enriched air to replace the original kiln head primary air and kiln head and kiln tail coal supply air, and enhance the combustion effect by fully mixing coal powder and oxygen-enriched air, thereby improving the coal powder burnout rate and flame temperature.
(2) Use special equipment to pass oxygen-enriched gas into the rotary kiln and spray it at a certain angle, so that the oxygen-deficient area in the kiln is enriched with a higher concentration of oxygen-enriched gas, thereby enhancing combustion and stabilizing the flame shape.
(3) Use oxygen-enriched air to replace the kiln head coal air and kiln tail coal air. This combustion-supporting scheme is mainly used in situations where the gas production is small.
3. Application example analysis of oxygen-enriched combustion technology in cement plants
(1) Oxygen production process
The plant adopts a low-energy consumption, high-flow membrane oxygen production system that is widely used at home and abroad. First, after ordinary air is filtered through a spray air filter to remove dust particles, oil and other impurities, it is sent to the oxygen-enriched membrane separation device by a booster fan. The oxygen-enriched membrane separation device is vacuumed by a Roots vacuum unit to form a negative pressure. Under the action of the pressure difference, the oxygen with a faster permeation rate is separated first, and oxygen-enriched air with an oxygen content of 26%±1% is produced. It enters the rotary kiln and decomposition furnace through the Roots blower at the kiln head, the tertiary air duct and the coal air duct at the kiln tail for oxygen-enriched combustion; secondly, oxygen-enriched air with a concentration of 38% provided by the molecular sieve oxygen production equipment is introduced into the oil injection pipe of the kiln head burner.
(2) Test method The test and calculation methods are based on the requirements of GB/T26282-2010 "Method for Determination of Thermal Balance of Cement Rotary Kiln" and GB/T 26281-2010 "Calculation Method for Thermal Balance, Thermal Efficiency and Comprehensive Energy Consumption of Cement Rotary Kiln". The chemical analysis of various materials and the industrial analysis of coal are based on on-site sampling during the test. The test instruments mainly include S-type pitot tubes (R1, R2, R3), armored K-type thermocouples (R4), testo 512 digital pressure gauges (R5, R6), testo 435 digital pressure gauges (R7), digital pressure gauges (R8), MRU 1600S-IV gas analyzers (R9) and flame temperature testers.
4. Results and analysis In order to ensure the authenticity and reliability of the data and fully reflect the changes in the thermal parameters of the entire firing system before and after oxygen enrichment, this test data includes two stages before and after oxygen enrichment. 2~3 sets of data are measured for each stage and analyzed.
(1) Air volume of the kiln tail exhaust pipe. During the entire test period before and after oxygen enrichment, the air flow of the high-temperature fan was at a normal control level, and the valve opening was 97%. The results show that the air volume, air temperature and air pressure measured by the exhaust gas main pipe before and after adding oxygen enrichment have little change. This shows that adding oxygen enrichment will not have a significant impact on the system ventilation.
(2) Gas composition before and after adding oxygen enrichment. The results show that after adding oxygen enrichment, the oxygen content of each test point increased significantly. The kiln tail smoke chamber before and after adding oxygen enrichment only contained a very small amount of CO, indicating that the coal powder at the kiln head of the production line was burned relatively fully, but the decomposition furnace sometimes had incomplete combustion. After the introduction of oxygen-enriched air, the coal powder combustion in the decomposition furnace improved. The NOx content at the kiln tail smoke chamber and the outlet of the decomposition furnace increased slightly before and after adding oxygen enrichment, but the change at the outlet of the preheater was not significant.
(3) Temperature of each measuring point. It can be seen that the temperature of the smoke chamber of the production line is relatively high, sometimes even exceeding 1300℃; after adding oxygen enrichment, the temperature of the smoke chamber, secondary air and tertiary air is higher than the temperature tested without adding oxygen enrichment. After adding oxygen enrichment, the temperature of the kiln head flame has increased significantly, reaching up to 1920℃, and the kiln head flame has become significantly brighter.
(4) NOx emission concentration. From the analysis of the emission concentration of the kiln tail chimney in the test, the emission concentration of NOx fluctuates greatly due to the presence of CO produced by incomplete combustion. Under incomplete combustion, the emission concentration of NOx before and after oxygen enrichment is around 300~400ppm; while under complete combustion, the emission concentration before and after oxygen enrichment is around 450~550ppm. It can be concluded that after oxygen enrichment, the NOx content in the exhaust gas of the kiln tail chimney does not change much.
(5) 3d strength of clinker. It can be seen that after oxygen enrichment, the 3d strength of clinker on the first and second days increases slightly. Overall, the 3d strength of clinker increases slightly after oxygen enrichment. (6) Energy saving of the system after oxygen enrichment. After 72h continuous operation without oxygen enrichment, the average clinker production was 2942t/d, the raw material input was 4744t/d, and the rotor scale coal consumption was 141.16kg/t clinker. After 72 hours of continuous oxygen enrichment operation test, the average clinker production was 2992t/d, the raw material input was 4680t/d, and the rotor scale coal consumption was 133.53kg/t clinker. The power consumption of the oxygen enrichment system converted to standard coal was 0.4tce/t clinker.
5. Conclusion Based on the above, the following conclusions can be drawn:
(1) After the installation of oxygen enrichment combustion equipment, the kiln head flame temperature was significantly improved. When conducting comparative tests at the same visible position of the kiln head, it was found that the flame temperature after oxygen enrichment reached a maximum of more than 1920℃, which can effectively improve the coal powder combustion condition in the kiln, which is beneficial to the calcination of cement clinker and the improvement of clinker quality.
(2) After the installation of oxygen enrichment combustion equipment, the NOx emission concentration at the chimney at the kiln tail did not change much.
(3) After the installation of oxygen-enriched combustion equipment, the incomplete combustion of coal powder in the decomposition furnace of the production line was alleviated, but there was no fundamental change. If the oxygen-enriched flow rate entering the secondary air can be further reduced or eliminated, and the oxygen-enriched gas flow rate entering the decomposition furnace can be increased, the energy-saving effect after adding oxygen-enriched combustion will be further improved.
(4) From the analysis of the quality of clinker before and after the installation of oxygen-enriched combustion equipment, the quality of clinker was slightly improved after adding oxygen-enriched combustion equipment.
(5) After adding oxygen-enriched combustion equipment, the coal consumption of the production line was significantly reduced, and the energy-saving effect was obvious. The unit clinker standard coal consumption was reduced by 7.63 kgce/t. After deducting the power consumption during oxygen-enriched operation, the coal saving rate can reach up to 5.12%. Oxygen-enriched combustion technology is in its infancy in cement enterprises, but the oxygen production process is relatively mature. At present, the pressure swing adsorption method and membrane method have their own advantages. The use of oxygen-enriched combustion technology can save coal, increase production, and improve clinker quality to a certain extent. However, the premise of using oxygen-enriched combustion in the production line is that the production line process is stable, the raw materials are stable, and the production management and operating skills are standardized and institutionalized, so that the fine adjustment, control, and management of oxygen-enriched combustion can be achieved.
1. How to ignite start a cement rotary kiln:
Before ignition, the entire combustion system should be tested in linkage to avoid adverse conditions such as overheating of the preheater system, blockage of the cyclone tube and the feed pipe. Whether it is ignited with firewood or diesel, the dampers of all high-temperature fans should be closed, and the ignition chimney should be opened appropriately according to the situation to keep the kiln head in a slightly negative pressure state to prevent excessive wind and difficulty in ignition.
When spraying coal powder, try to ensure the combustion rate of coal powder, do not spray too much, and add coal slowly; and rotate the kiln at intervals, 1/4 each time, to avoid bending and deformation of the cylinder. When the temperature reaches above 700℃, auxiliary transmission continuous kiln rotation should be used, and the high-temperature fan should be started according to the situation, and the damper opening should be adjusted appropriately; when the temperature reaches 900℃, the main transmission kiln rotation can be used.
If the diesel ignition is not busy, all oil pumps should be closed, but the valve opening can be appropriately reduced; after feeding, the oil supply can be stopped after the material reaches the combustion zone. The feeding time is determined according to the temperature at the kiln tail and the preheater outlet temperature; the initial feed rate of the kiln should be relatively high, generally not less than 60% of the designed output, and then the feed rate should be slowly increased, and the feed range should be small rather than large until the normal feed rate; in addition, the operation time of low feed rate should be shortened as much as possible, because during this period, the preheater system is prone to blockage due to collapse.
2. How to replace the refractory bricks of the rotary kiln?
After changing the bricks (referring only to the firing zone), the kiln should be properly dried to avoid the temperature rising too fast. The kiln skin has certain requirements for the raw material composition, especially the liquid phase amount and the refractory of the material. If the liquid phase amount is large, it is easy to form the kiln skin, but it is also easy to collapse, not firm, and cannot withstand high-temperature calcination; if the liquid phase amount is small, the material is refractory, and it is difficult to form the kiln skin. The kiln skin after formation is quite strong, but if there is a collapse, it is not easy to repair. It is recommended to use raw material powder during normal production, which is conducive to the formation of the kiln skin. During the calcination process, the kiln skin is a dynamic balance. Even if a small part collapses, it is easy to repair it in time, but when hanging the kiln skin, do not run raw materials and under-burning.
3. How to deal with unstable incoming materials:
When there are fewer materials, do not extend the coal injection pipe, open the large exhaust, and stretch the flame, otherwise the temperature at the kiln tail will rise sharply, and the temperature of the decomposition furnace and cyclone tube will also rise rapidly, which will easily cause the cyclone tube or the feeding pipe to stick or even block, and the kiln tail smoke chamber and decomposition furnace will also easily peel off, increasing the system resistance. The correct operation method is: appropriately withdraw the coal injection pipe, close the small exhaust, reduce the amount of coal in the decomposition furnace and the kiln head, control the temperature at the kiln tail and the cyclone tube, use short smoke combustion, and wait for the arrival of materials.
When there are more raw materials, there will be positive pressure at the kiln head, and the temperature of the cyclone tube outlet and the decomposition furnace will drop sharply. At this time, the kiln speed should be appropriately reduced, the feed amount should be reduced, the large exhaust should be opened, the coal injection pipe should be extended, the kiln tail temperature should be increased, and the pre-burning effect of the material should be enhanced; coal can also be added appropriately, but not too much, otherwise it will create a reducing atmosphere and reduce the temperature in the kiln. When the current of the kiln main transmission motor drops rapidly, the kiln speed should be reduced, the coal injection pipe should be withdrawn, and the exhaust volume should be appropriately reduced. At this time, short flame combustion can be used to restore it to normal. When the working conditions in the kiln are normal, the feed and heating shall not be allowed, which will make the operation passive and the production quality difficult to guarantee.
4. How to solve the oil leakage problem:
First, determine the location of the oil leakage, which is commonly found in the sliding shoe seal cover, hollow shaft seal, roller shaft oil seal, large gear ring guard and other parts. The reasons for oil leakage in different locations are different, such as structural design, processing and manufacturing, installation, maintenance and other aspects. For example, the rotary kiln roller shaft oil seal was originally designed as a J-type oil seal with an annular spring on the lip. The spring has a small size and is easy to fall off during installation and operation, and even enters between the bearing shells, causing a serious accident. This can be solved by improving the oil seal structure and other methods.
5. How to lubricate the wheel tyre/riding ring of the rotary kiln:
At present, the industry generally uses oil spraying to lubricate the wheel tyre, but there are disadvantages such as low efficiency, poor effect, environmental pollution, and poor economy. For example, most of the lubricant is sprayed outside the working area (more than 60%), causing oil waste and environmental pollution, and the cost is high. For example, the amount of lubricant required for one spray lubrication of three wheel tyres is generally one barrel (16kg) of lubricant, and the approximate reference price is $300USD/barrel. If the lubrication frequency is once a week, the annual oil consumption is about $11,500USD or more. Patented products that can use solid lubrication methods - graphite lubrication devices (UGL-100, for lubrication of the end face of the wheel band; UGL-400, for lubrication of the inner surface of the wheel band) are installed on the surface of the kiln barrel/pad close to the wheel band (it is generally recommended to install 4 sets of lubrication devices evenly distributed on the circumference of each working surface). The phenomenon of "relative slip between the wheel band and the barrel" during the operation of the rotary kiln is used to directly and continuously and stably provide solid lubricants to the working area of the wheel band. It has the advantages of high lubrication efficiency, convenience and practicality, safety, environmental protection, and economy. The operating cost is more than 10 times lower than the original injection lubrication method.
6. How to detect the center line: The three-dimensional laser scanning technology can be innovatively applied to the center line detection of the rotary kiln, and a special measuring instrument - "wheel slippage/top clearance measuring instrument" (invention patent) can be used to accurately measure the slippage and top clearance of each gear wheel under normal operation.
7. How to adjust the roller: Using highly professional roller adjustment technology and mature lubricant for rollers, according to the measured results of the center line of the rotary kiln, the slippage and top clearance of the wheel, combined with the straightness and ovality detection of the cylinder, the load distribution of each gear roller, the layout of the roller, the up and down pressure and time of the hydraulic stopper, the force of the roller, etc., are reasonably controlled to optimize the force condition of the kiln body.
8. How to formulate the rotary kiln heating curve:
For newly replaced refractory bricks and refractory concrete, according to its characteristics and construction season, water consumption, curing time and other factors, determine the temperature and time required for these materials to separate from physical free water and chemical crystallization water, and give corresponding constant temperature sections respectively.
For temporary kiln shutdown without replacing the kiln lining, it should be formulated according to the amount of raw materials or kiln skin stored in the kiln, the length of kiln shutdown time and the season of kiln ignition. In order to avoid the explosion of bricks, the materials stored in the kiln can also be used as clinker out of the kiln.
When re-ignition after a short kiln shutdown time, that is, when the material is stopped for less than 24 hours and is in insulation, the kiln is still in a hot state. At this time, the heating time can be shortened according to the actual situation. In order to protect refractory bricks, the requirements of "slow heating and no turning back" should be followed.
9. Common rotary kiln operating faults and treatment methods:
1. Temperature instability: If it is found that the temperature of the entire kiln barrel of the firing zone is too high or the kiln skin falls off in large quantities, the flame shape is not good, and the flame diverges and washes the kiln skin and fire bricks, then the internal flow should be increased or even closed, the amount of coal used at the kiln head of the rotary kiln should be increased, the external flow should be increased, the flame should be extended or the coal injection pipe should be moved, the position of the fire point should be changed, and the kiln skin should be re-attached to restore the firing condition to normal.
2. Excessive wheel belt displacement: Since the company does not pay attention to this situation, it will cause the kiln bricks to twist and collapse, and in severe cases, it will cause the barrel to deform. Therefore, the operator should pay attention to carefully observe the slippage of the side wheel belt, and regularly maintain and inspect the wheel belt and pad to avoid major impact on the equipment.
Kiln body vibration: The reasons for this situation include uneven heating of the barrel, too large or too small gap between large and small gears, loose interfaces, loose bearing bolts, etc. The solution is to adjust the support wheel in time, re-attach the kiln skin, adjust or replace the gears, and tighten the bolts.
3. Rotary kiln shutdown: If it is short-term, the coal injection pipe cooling fan must be turned on to avoid burning the coal injection nozzle. Check whether the auxiliary facilities are damaged and whether the safety protection is reliable. If the kiln body is found to be deformed, it is necessary to overhaul it. If the kiln is stopped for a long time, check the wear of various components at the head and tail of the kiln, and clean and refuel the support wheel bearings or bearings.
4. Coke brick situation: Prevention is the main focus, and the fire in the preheating zone is closely monitored. When the fire in the preheating zone is found to have a tendency to develop into a large fire, high-temperature gas should be extracted from the rear of the preheating zone in advance. When the signs of a large fire are obvious, the residual heat gate of the burning zone can also be raised to ignite and cool down in advance. Controlling the speed of the fire, reducing the height of each wind gate, and delaying the speed of the fire head are all conducive to controlling the fire. When the fire on the burning zone is large, the residual heat gates before and after the large fire can be raised to disperse the firepower. When the bottom fire of the burning zone is large, the far gate and the near gate must be lowered first. In addition to raising the residual heat gate, the air intake should be increased to accelerate cooling.
10. To achieve energy saving and consumption reduction in rotary kilns:
Improve the utilization rate of heat provided by coal powder combustion, such as using RLHY-12 high temperature resistant heat insulation coating, whose thermal conductivity is as low as 0.035W/m・K and reflectivity can reach 85%. It is used in the kiln lining of the rotary kiln to effectively improve the thermal resistance of the kiln lining and reduce the heat loss through the cylinder. It is very ideal for energy saving in the firing zone section through the cylinder, because the heat dissipation loss in this area is large, which can reach more than 35% of the total heat loss of the cylinder. Optimize the operating parameters of the rotary kiln, such as reasonably controlling the kiln speed, air volume, feed volume, etc., so that the fuel combustion, heat transfer and raw material movement are reasonably coordinated to achieve the purpose of high yield, high quality and low consumption.
1. Basic structural differences:
Rotary kiln: A rotary kiln is a cylindrical device placed at an angle, usually composed of a cylinder, a belt, a support wheel, a transmission device and other parts. The cylinder is the main body of the rotary kiln, which is generally made of rolled steel plates, with a long length and a large diameter. It is supported on the support wheel by a belt and rotates slowly under the drive of the transmission device. For example, the rotary kiln in the production of new dry cement has a cylinder length of up to tens of meters and a diameter of up to several meters. This rotating structure allows the material to roll forward continuously in the kiln and be heated more evenly.
Vertical kiln: A vertical kiln is a cylindrical device placed vertically, mainly composed of a kiln body, a discharge device, a feeding device and other parts. The kiln body is generally short and thick, and the height is usually about ten meters. The material is added from the top, moves from top to bottom in the kiln, and is discharged from the bottom after calcination. The kiln body structure of the vertical kiln is relatively simple, and does not require a complex rotating support device.
2. Differences in calcination process:
Rotary kiln: The calcination process of materials in a rotary kiln is dynamic. As the cylinder rotates, the material moves slowly along the inclination direction of the kiln body, from the high end of the kiln (usually the feed end) to the low end (discharge end). In this process, the material is heated by the high temperature of the flame from the kiln head, and due to the continuous tumbling, all parts of the material can fully contact the hot air and be heated evenly. The calcination temperature can be precisely controlled, generally around 1450℃, and high-quality cement clinker can be produced. Taking the raw material mixed with raw materials such as limestone and clay as an example, it undergoes a series of physical and chemical changes in the rotary kiln, such as the decomposition of calcium carbonate, the formation of minerals such as dicalcium silicate and tricalcium silicate, and finally generates qualified cement clinker.
Vertical kiln: The calcination of materials in the vertical kiln is carried out in layers. After the material is added from the top, it gradually sinks under the action of gravity, and the hot air generated by the combustion of fuel is introduced at the bottom to move upward and exchange heat with the material. Because the material is statically stacked, the temperature of the part close to the flame is higher, while the material in the inner and edge parts is relatively unevenly heated. Its calcination temperature is relatively difficult to control, generally between 1350-1400℃. This uneven heating method may cause fluctuations in the quality of cement clinker, such as uneven mineral composition of some clinkers, which affects the performance of cement.
3. Production efficiency and scale differences:
Rotary kiln: The production efficiency of the rotary kiln is relatively high and can achieve large-scale continuous production. Due to its good material turning and heating conditions, a large amount of raw materials can be processed per unit time. Modern rotary kiln cement production lines can produce thousands of tons or even tens of thousands of tons of cement clinker per day. For example, some large cement companies use advanced rotary kiln production lines, which can produce about 10,000 tons of clinker per day, which is suitable for large-scale construction projects and other occasions with high demand for cement.
Vertical kiln: The production efficiency of the vertical kiln is relatively low and is generally suitable for small and medium-sized production. Its production process is relatively intermittent, and each feeding, calcination and unloading requires a certain time interval. The daily output of the vertical kiln is usually within a few hundred tons. Due to its small production scale, its application scope is gradually narrowing under the current trend of large-scale cement production, but it is still used in some small cement production companies or specific occasions where cement quality requirements are not particularly high.
4. Cement clinker product quality:
Rotary kiln: The quality of cement clinker produced by rotary kiln is relatively stable and uniform. Due to its precise temperature control and good material mixing and calcining conditions, the produced clinker has a reasonable mineral composition and low content of harmful components such as free calcium oxide. The cement made from this high-quality clinker has high strength and stable performance, is suitable for the production of various high-grade cements, and can meet the requirements of high-quality construction projects.
Vertical kiln: The quality of cement clinker produced by vertical kiln is relatively poor. Because of its uneven heating, it may lead to a high content of free calcium oxide in the clinker and poor mineral crystallization, which affects the strength and stability of cement. The cement produced by it is generally suitable for some low-grade cement and small construction projects that do not require high cement quality.
5. Environmental performance differences:
Rotary kiln: Rotary kiln has advantages in environmental protection. New dry rotary kiln production lines are generally equipped with advanced waste gas treatment systems, such as efficient dust collection equipment and desulfurization and denitrification devices. During the calcination process, the waste gas generated can be better purified and treated, reducing the emission of pollutants such as dust, sulfur dioxide and nitrogen oxides. At the same time, the rotary kiln has strong adaptability to raw materials, and can better utilize some industrial waste slag as raw materials to achieve comprehensive utilization of resources and reduce the pollution of waste slag to the environment.
Vertical kiln: The environmental performance of the vertical kiln is relatively poor. Due to the uneven heating of materials during the calcination process, the combustion efficiency is low, and it is easy to produce more dust and harmful gases. Moreover, the waste gas treatment of the vertical kiln is relatively difficult. In some small vertical kiln cement plants, the waste gas emissions may not meet strict environmental protection standards and cause pollution to the surrounding environment.
1. Dust removal measures:
Cyclone separator: The cyclone separator generates centrifugal force through high-speed rotating airflow, so that large dust particles are separated from the flue gas under the action of centrifugal force, and settle to the bottom of the separator for collection. It is usually installed on the pipeline before the flue gas enters the main dust removal equipment, which can effectively intercept larger dust particles, reduce the burden of subsequent dust removal equipment, protect it from the impact and wear of large particles, extend the service life of the equipment, and reduce the maintenance cost of the equipment.
Wet desulfurization equipment: This equipment uses alkaline solution (such as lime water, etc.) to react chemically with sulfur dioxide in the flue gas to generate sulfite or sulfate precipitation, thereby achieving the purpose of desulfurization. At the same time, during the desulfurization process, part of the dust in the flue gas will also be captured by the solution, which has the effect of preliminary dust removal. This not only helps to reduce the emission of harmful gases, but also can preliminarily purify the dust, laying the foundation for subsequent more refined dust removal treatment.
Bag filter: A large number of filter bags are installed inside the bag filter. When the dusty flue gas passes through the filter bag, the dust particles will be blocked by the fibers of the filter bag and adhere to the surface of the filter bag, while the clean gas will be discharged through the filter bag. This dust collector has a high capture efficiency for tiny particles. Even dust with a particle size of less than 1 micron can be effectively removed, and its dust removal efficiency can reach more than 99%. Moreover, the bag filter has stable operation, relatively simple operation, and convenient maintenance. It only needs to clean the filter bag regularly and replace the damaged filter bag to ensure its normal operation.
Electrostatic precipitator: The electrostatic precipitator works based on the principle of electrostatic adsorption. Under the action of the electric field, the dust particles in the flue gas are charged, and then driven by the electric field force, they move to the electrode and deposit on the electrode, thereby separating the dust from the flue gas. The electrostatic precipitator is suitable for handling fine dust, can operate stably under harsh environments such as high temperature, high pressure and high humidity, and has a high dust removal efficiency. However, its equipment investment cost is high, and it has certain requirements for the resistivity of dust. It is necessary to carry out reasonable electric field design and parameter adjustment according to the characteristics of dust to ensure its efficient operation.
Electrostatic bag composite dust collector: The electrostatic bag composite dust collector combines the advantages of electrostatic precipitator and bag dust collector. First, the flue gas passes through the electrostatic precipitator area, and most of the dust is charged and collected under the action of the electric field, which initially reduces the dust concentration; then, the remaining small amount of dust enters the bag dust removal area and is further filtered by the filter bag. This combination can give full play to the pretreatment effect of the electrostatic precipitator on large particles and high-concentration dust, and can also use the efficient capture ability of the bag dust collector for tiny particles, thereby achieving higher dust removal efficiency and effectively reducing the emission concentration. At the same time, it reduces the cleaning pressure of the bag dust collector and the loss of the filter bag to a certain extent, and prolongs the service life of the filter bag.
Wet electrostatic precipitator: The wet electrostatic precipitator charges dust particles through a high-voltage electric field, and then uses the fine droplets generated by the water spray device to interact with the charged dust, so that the dust is captured by the droplets and carried away with the water flow to achieve the purpose of dust removal. It not only has a high efficiency in dust removal, especially good at capturing fine dust below 1 micron, but also can simultaneously remove pollutants such as sulfur dioxide and nitrogen oxides in the flue gas, has a good desulfurization and denitrification effect, and further improves the degree of flue gas purification. However, due to the large amount of water and electricity consumed during its operation, the operating cost is relatively high, and when dealing with high humidity and high concentration of dust-containing gas, equipment corrosion and electrode scaling may occur, affecting the performance and stability of the equipment.
2. Optimize combustion technology:
Low nitrogen combustion technology: By improving the design of the burner and adjusting the parameters of the combustion process, such as accurately controlling the ratio of combustion air to fuel, the fuel can be fully burned at a relatively low temperature to reduce the generation of nitrogen oxides. At the same time, technical means such as staged combustion and air staged combustion are used to reduce the local high temperature in the combustion area and inhibit the formation of nitrogen oxides. This technology does not require the addition of additional chemical reducing agents and has a relatively low cost. It is one of the important measures for reducing nitrogen oxide emissions in cement rotary kilns.
Oxygen-enriched combustion technology: Oxygen-enriched combustion is to provide oxygen-enriched air (oxygen content is higher than normal air) to the combustion process, so that the fuel can be burned more fully and efficiently. Because the combustion is more complete, it not only improves the energy utilization efficiency and reduces fuel consumption, but also reduces the generation of pollutants such as nitrogen oxides. In addition, oxygen-enriched combustion can also improve the uniformity of temperature distribution in the rotary kiln, which is beneficial to improve the quality and output of cement clinker, but this technology needs to be equipped with an oxygen preparation system, which increases equipment investment and operating costs.
3. Desulfurization and denitrification technology:
Desulfurization technology: Wet desulfurization with lime milk or gypsum is one of the commonly used desulfurization methods in the cement industry. Lime milk (calcium hydroxide suspension) is sprayed into the absorption tower to react chemically with sulfur dioxide in the flue gas to generate calcium sulfite, which is further oxidized to calcium sulfate (gypsum), thereby achieving the removal of sulfur dioxide. This method has a high desulfurization efficiency of more than 90%, and the technology is mature and the operation is stable. The gypsum produced after desulfurization can also be recycled, which has certain economic benefits. In addition, dry desulfurization and semi-dry desulfurization technologies are also used in some cement companies. They have the advantages of small footprint and low investment cost, but the desulfurization efficiency is slightly lower than that of wet desulfurization.
Denitrification technology: Selective non-catalytic reduction (SNCR) technology is to spray a reducing agent (such as ammonia water, urea, etc.) into the flue gas in the high temperature area (850-1100℃) of the cement rotary kiln. The reducing agent decomposes at high temperature to produce ammonia, which reacts with nitrogen oxides to convert them into nitrogen and water, thereby reducing the emission concentration of nitrogen oxides. This technology has the advantages of low investment cost, simple system, and convenient operation, but the denitrification efficiency is relatively limited, generally between 30%-60%. Selective catalytic reduction (SCR) technology is to react the reducing agent with nitrogen oxides at a lower temperature (200-400℃) under the action of a catalyst, with a higher denitrification efficiency of more than 80%, but it requires the use of expensive catalysts, and the equipment investment and operating costs are high. At the same time, strict requirements are placed on the activity and life management of the catalyst.
4. Optimizing raw materials and fuels:
Raw material selection: In the process of raw material procurement and mixing, minerals with low content of harmful elements such as low sulfur and low magnesium are given priority as raw materials. High-sulfur raw materials will produce a large amount of sulfur dioxide during the calcination process, while high-magnesium raw materials may affect the quality and performance of cement clinker and increase pollutant emissions. Therefore, by strictly screening raw materials and reducing the introduction of harmful components from the source, the total amount of pollutants generated by the rotary kiln during the production process can be effectively reduced, and it also helps to improve the quality and stability of cement products.
Fuel selection: Using clean and efficient fuel is one of the important ways to reduce pollutant emissions. Clean energy sources such as natural gas and liquefied petroleum gas produce less harmful gases and particulate matter during the combustion process. Compared with traditional coal, they can significantly reduce the emission of pollutants such as sulfur dioxide, nitrogen oxides and dust. Although the cost of using clean energy may be relatively high, from the perspective of environmental protection and sustainable development, it is of great significance to reduce air pollution and improve environmental quality. With the continuous advancement of energy technology and the gradual reduction of costs, its The application prospects will be broader.
5. Strengthen operation management and monitoring:
Optimize operation parameters: Reasonable control of the rotary kiln's kiln temperature, pressure, air flow velocity and other operating parameters is crucial to ensure the stability and efficiency of the production process and reduce the generation and emission of pollutants. By installing advanced temperature, pressure and flow monitoring instruments, the thermal parameters in the kiln are monitored in real time, and precise control is performed according to the actual production situation, so that the fuel can be fully and evenly burned, and the material can be calcined under the best conditions, thereby improving energy efficiency and reducing the amount of waste gas pollutants. For example, keep the temperature in the kiln stable to avoid incomplete combustion and increased pollutant emissions due to excessive temperature fluctuations; reasonably control the pressure in the kiln to prevent dust overflow and harmful gas leakage due to excessive or low pressure.
(1)Temperature monitoring: Different reaction stages in the rotary kiln require different temperatures. For cement production, the general burning zone temperature is around 1400-1450℃. The temperature can be monitored in real time by temperature monitoring equipment such as thermocouples installed in the kiln. If the temperature does not reach the required range, the material may not be calcined thoroughly. For example, in the calcium carbonate decomposition stage, the temperature is lower than 894℃ (calcium carbonate decomposition temperature), and the calcium carbonate decomposition is not complete, which will affect the subsequent reaction and lead to incomplete calcination.
(2)Material residence time: The material needs sufficient residence time in the rotary kiln to complete the calcination reaction. The residence time is related to factors such as the kiln speed, length, slope, and material filling rate. Generally speaking, the residence time of cement raw materials in the rotary kiln is about 20-30 minutes. Whether the residence time of the material is sufficient can be evaluated by calculation and actual observation. For example, when the kiln speed is too fast, the material passes through the kiln quickly and does not have time to fully react, which will result in incomplete calcination.
(3)Observe the state of the material in the kiln: Observe the tumbling and color changes of the material in the kiln through the kiln head fire mirror. During normal calcination, the material tumbles actively and evenly, and the color gradually changes from dark to light. If you see that the material is agglomerated, piled up, or the color changes unevenly, it may mean that the calcination is not thorough. For example, during the calcination of cement clinker, if you see black raw material lumps, it means that these parts are not fully calcined.
(4)Chemical analysis: Chemical analysis of the materials taken out of the kiln to detect the content of unreacted components. For example, for cement raw materials, the main components are calcium carbonate, silicon dioxide, aluminum oxide and iron oxide. After calcination, calcium carbonate should be decomposed into calcium oxide. By detecting the content of calcium oxide, it can be determined whether the calcium carbonate is completely decomposed. If the calcium oxide content is lower than the theoretical value, it means that the calcination is not thorough.
Methods for judging the quality of clinker calcination
(1)Color: High-quality cement clinker is generally dark gray or black, and the color is uniform. If the clinker is yellowish, white, or has uneven color, it may be caused by inappropriate calcination temperature or poor ventilation in the kiln. For example, when the calcination temperature is too high, the clinker may be partially overburned, the color will become darker, or even black shiny glass will appear; if the temperature is too low, the clinker may be yellowish.
(2)Particle shape and size: Good clinker particles are regular in shape, mostly round or nearly round, and the particle size is relatively uniform. The particle size is generally around 5-25mm. If the particle shape is irregular, with many broken particles or large pieces, it may affect the performance of cement. For example, too many broken particles may increase the water demand of cement, and the presence of large pieces may indicate local overburning or ringing, affecting product quality.
Physical performance test
(1)Strength:
The quality of clinker is judged by compressive strength and flexural strength tests. Generally speaking, the compressive strength should reach more than 28MPa after 3 days, and more than 50MPa after 28 days. Cement made from high-strength clinker has better quality and can better meet the needs of construction projects. If the strength does not meet the standard, it may be due to unreasonable clinker mineral composition or insufficient calcination.
(2)Stability:
This is one of the important indicators for measuring clinker quality. It can be tested by the Reye method or the test cake method. If the content of free calcium oxide and other components in the clinker is too high, it will react with water after the cement hardens, causing volume expansion and cracks in cement products, that is, poor stability. The stability of high-quality clinker should be good, and this expansion and damage will not occur.
(3)Mineral composition analysis:
The mineral composition of clinker is analyzed using equipment such as X-ray diffractometer (XRD). The main minerals of high-quality cement clinker are tricalcium silicate (C₃S), dicalcium silicate (C₂S), tricalcium aluminate (C₃A) and tetracalcium aluminoferrite (C₄AF). Among them, the C₃S content is generally around 50% - 60%, the C₂S content is around 15% - 30%, the C₃A content is around 7% - 15%, and the C₄AF content is around 8% - 12%. Reasonable mineral composition can ensure the strength, setting time and other properties of cement. If the mineral composition does not meet the requirements, such as the C₃S content is too low, the cement strength will develop slowly.
1. Wearing parts life span
Girth gear and pinion gears: The service life of the large gear ring is generally between 10-15 years, but most of the actual service life is 8-10 years. The small gear wears faster and generally needs to be replaced every 3-5 years. Dry or semi-dry cement kilns need to be replaced more frequently. If the large gear ring is subjected to surface quenching and other strengthening treatments during the casting process, its service life can be increased.
Inner lining: The inner lining is one of the important factors affecting the life of the cement rotary kiln. Generally speaking, the kiln head cover adopts mullite high-strength explosion-proof castable, and the wear area is less than 10m² after 12 months of operation, and the damaged area is less than 20m² after 24 months; the reasonable life of mullite high-strength explosion-proof castable in the high-temperature zone of the grate cooler is 1 year; the medium-temperature zone of the grate cooler and the medium-temperature zone of the preheater system adopt high-aluminum steel fiber castable and high-aluminum low-cement castable, with a reasonable life of 2 years; the low-temperature zone of the grate cooler and the low-temperature zone of the preheater system adopt high-aluminum low-cement castable and ordinary alkali-resistant castable, with a life of 3 years; anti-scaling castable is used in the kiln tail smoke chamber, the tail lower feeding pipe, the decomposition furnace cone and other easy-to-scaling areas. The smoke chamber is partially repaired after 1 year, and other parts are more than 24 months; high-strength alkali-resistant bricks are used in regular parts such as the cyclone column of each level, which can be operated for 3-5 years; 1550 silicon-mullite bricks or high-aluminum low-cement castables are used in regular parts of the tertiary air duct, with a life of 2-3 years; the easily worn parts of the tertiary air duct at the kiln head hood end and the elbow at the decomposition furnace are made of brick-concrete structure, silicon carbide castable + 1550 silicon molybdenum brick, and can operate normally for 1 year; the tertiary air damper adopts an integral prefabricated damper with a reasonable life of 10 months; the normal life of the burner is 4-8 months.
2. Life span of steel castings
Kiln barrel: The life of a normally operating cement rotary kiln is generally about 40 years. However, if the kiln operates irregularly, operates under overload, does not stop, deviates from the center line, runs in a neck, has stress concentration and fatigue operation, and is corroded by harmful elements such as sulfur, phosphorus, fluorine, and chlorine in the material, the kiln barrel will become brittle and thin, resulting in a significant shortening of its life.
Wheel: The rollers of the rotating load-bearing parts are made of ZG35CrMo or 42CrMo steel, and their life is closely related to the maintenance and operation load of the equipment. If properly maintained, the rollers can be used for a long time, but if there is poor lubrication and uneven force, the wear of the rollers will increase, thus affecting their service life.
3. Bearing lifespan:
The service life of bearings varies depending on many factors. The service life of general industrial-grade rolling bearings ranges from thousands to hundreds of thousands of hours. For bearings in cement rotary kilns, due to their harsh working environment, heavy loads, low speeds and continuous operation, their service life is usually around 20,000-50,000 hours. If the bearings have obvious problems such as wear, increased noise, abnormal temperature, uneven rotation or decreased performance, they should be inspected and replaced in time.
4. Operation
Temperature control: When the kiln is opened, the heating rate should be controlled within 50℃/h to avoid rapid heating that may damage the lining materials such as alkaline bricks due to excessive thermal stress; when the kiln is stopped, it must also be operated in accordance with the prescribed cooling kiln system to prevent rapid cooling from damaging the equipment.
Material control: The composition, particle size, moisture and other indicators of the materials entering the kiln should meet the process requirements, otherwise it may cause problems such as ringing and crusting in the kiln, affecting the normal calcination of the materials and the operation of the equipment, thereby reducing the life of the equipment.
Combustion control: To ensure the full and stable combustion of the fuel, reasonably adjust the fuel supply and air ratio to make the temperature distribution in the kiln uniform, avoid local overheating or Incomplete combustion, etc., to reduce damage to the kiln lining and equipment.
5. Maintenance perspective
Daily inspection: Regularly inspect the cement rotary kiln to check whether the bolts of various parts are loose, whether the equipment has abnormal vibration and noise, whether the lubrication system is normal, etc., timely discover and deal with potential problems, which can effectively extend the life of the equipment.
Regular maintenance: formulate a reasonable maintenance plan, conduct comprehensive inspection, maintenance and repair of the equipment, including replacing worn parts, repairing damaged linings, adjusting the gap of the equipment, etc., to ensure that the equipment is in good operating condition.
Lubrication management: Good lubrication is the key to ensure the normal operation of the equipment and extend its service life. According to the requirements of different parts, choose the appropriate lubricant, and add and replace it regularly to prevent the wear of parts caused by poor lubrication.
6. Design and manufacturing perspective
Design rationality: Reasonable design is the basis for the longevity of cement rotary kiln. The length, diameter, slope and other parameters of the rotary kiln need to be accurately calculated and designed according to factors such as production scale, material characteristics, fuel type, etc., to ensure that the materials can be fully preheated, reacted and cooled in the kiln to achieve efficient calcination. For example, if the length of the cylinder is too short, the material may not be fully preheated, affecting the quality and output of the clinker. It will also cause uneven temperature distribution in the kiln and accelerate the damage of components such as the lining; while if the cylinder is too long, it will increase equipment investment and operating costs, and may cause the material to stay in the kiln for too long, resulting in overburning, which is also not conducive to equipment life and production efficiency.
Manufacturing quality: Quality control in the manufacturing process is crucial to the life of the cement rotary kiln. High-quality material selection, precise processing technology and strict quality inspection can ensure that the various components of the rotary kiln have good performance and reliability. For example, the welding quality of the cylinder directly affects its strength and sealing. If there are defects in the welding, it may cause cracks and leakage in the cylinder during operation, seriously affecting the life of the equipment; another example is the processing accuracy of large and small gears. If the parameters such as the gear tooth shape and pitch do not meet the requirements, it will lead to poor gear meshing, vibration, noise and increased wear, shortening the service life of the gear.
7. Fuel quality perspective
Heat value and stability: The heat value of fuel is one of the key factors affecting the temperature and calcination effect of cement rotary kiln. Fuel with high heat value can provide enough heat to make the temperature in the kiln rise quickly and remain stable, which is conducive to the full calcination of materials. If the heat value of the fuel is unstable, it will fluctuate greatly in the kiln temperature, causing the lining material to crack, peel off and other damage due to frequent changes in thermal stress, and will also affect the quality and output of clinker. For example, as a common fuel, the heat value of coal varies depending on factors such as origin and type of coal. It needs to be reasonably matched and pretreated when used to ensure the relative stability of the heat value.
Impurity content: The impurity content in the fuel will also affect the life of the cement rotary kiln. Harmful elements such as sulfur, phosphorus, and chlorine will generate corresponding oxides during the combustion process. These oxides react chemically with the materials and lining in the kiln, which may lead to increased erosion and corrosion of the lining and reduce the service life of the lining. In addition, if the ash content in the fuel is too high, it will increase the dust accumulation and crusting in the kiln, affect the heat transfer efficiency, increase energy consumption, and also increase the wear of the equipment.
8. Environmental factors
Temperature changes: The changes in the ambient temperature of the cement rotary kiln have a certain impact on its life. In cold areas, low temperatures in winter may make it more difficult to start and run the equipment, increase the viscosity of the lubricating oil, lead to poor lubrication effect, and increase the wear of parts. At the same time, low temperatures may also cause metal parts such as the cylinder to become cold and brittle, reduce their strength and toughness, and easily cause defects such as cracks. In hot areas, high temperature environments may make it difficult for the equipment to dissipate heat, resulting in excessive oil temperature and increased thermal expansion of parts, affecting the normal operation and service life of the equipment.
Humidity and corrosive gases: Humidity and corrosive gases in the environment can also cause damage to cement rotary kilns. High humidity environments can easily cause rust on the surface of the equipment, especially for some metal parts that have not been treated with anti-corrosion. Rust will gradually weaken the strength of the parts and affect the performance and life of the equipment. In addition, if the surrounding air contains corrosive gases such as sulfur dioxide and carbon dioxide, these gases will combine with the moisture on the surface of the equipment to form acidic substances, accelerate the corrosion process of the equipment, and cause corrosion damage to the cylinder, bracket and other components.
9. From the perspective of technological updates
Application of new materials: With the continuous development of materials science, the application of new refractory materials, wear-resistant materials, lubricating materials, etc. in cement rotary kilns can effectively improve the service life of equipment. For example, new refractory materials such as magnesium-aluminum spinel bricks have better high temperature resistance, wear resistance and thermal shock resistance, and can withstand higher temperatures and more drastic temperature changes, thereby extending the service life of the lining; high-performance lubricating materials can provide good lubrication under harsh conditions such as high temperature and heavy load, reducing friction and wear between components.
tongli advanced control technology: tongli uses advanced control technology and automation systems to achieve precise control and optimized operation of cement rotary kilns. By real-time monitoring of parameters such as temperature, pressure, flow rate, etc. in the kiln, and automatic adjustment according to the preset control strategy. For example, the tongli combustion control system can accurately control the fuel supply and air ratio according to the characteristics of the fuel and the working conditions in the kiln, so as to achieve full combustion of the fuel. At the same time, it can also avoid problems such as coking and carbon deposition in the kiln caused by incomplete combustion, and extend the cleaning cycle and service life of the equipment.
1. Coal:
Coal is mainly composed of carbon (C), hydrogen (H), oxygen (O), nitrogen (N), sulfur (S) and other elements. The carbon content of general thermal coal is between 50% and 90%, for example, the carbon content of common bituminous coal is about 70% to 85%. The hydrogen content is about 3% to 6%, and the oxygen content is about 5% to 20%. Among them, the sulfur content is a key indicator, which is divided into organic sulfur and inorganic sulfur. The total sulfur content of high-quality thermal coal is generally required to be less than 1%, and the sulfur content of high-sulfur coal may reach 3% to 5%. High-sulfur coal will produce a large amount of sulfur dioxide (SO₂) when burned, which will not only corrode the equipment of cement rotary kiln, but also pollute the environment.
Coal calorific value: The calorific value of coal varies greatly. The calorific value of lignite is relatively low, generally around 10-20MJ/kg; the calorific value of bituminous coal is usually between 20-30MJ/kg, for example, the calorific value of high-quality power bituminous coal can reach 25-29MJ/kg; the calorific value of anthracite is higher, up to 30-35MJ/kg. In cement rotary kilns, in order to ensure sufficient heat supply, bituminous coal or anthracite with higher calorific value is usually selected to maintain a high temperature environment in the kiln to meet the temperature required for cement clinker calcination (generally 1400-1450℃).
From the perspective of coal combustion characteristics: the combustion process of coal includes drying, volatile matter escape, coke combustion and other stages. Coal with high volatile matter content, such as some bituminous coal, burns relatively fast and has a longer flame. Its volatile matter content can be between 10%-40%. In cement rotary kilns, appropriate volatile matter content helps to stabilize the flame and evenly distribute heat. However, if the volatile matter is too high, it may cause the flame temperature to be too high, causing damage to the kiln lining. At the same time, the particle size of coal will also affect the combustion effect. Generally, the particle size is required to be between 0-50mm. The appropriate particle size can ensure that the coal has enough burning time and space in the kiln and improve the combustion efficiency.
Coal is used as a raw material for cement rotary kiln. Operating cost: Coal is a relatively low-cost fuel. Its price is affected by factors such as origin, quality, and market supply and demand. Taking the Chinese market as an example, the price of thermal coal fluctuates around a few hundred yuan/ton. In cement production, coal costs usually account for a large proportion of production costs, generally around 30%-50%. Therefore, the reasonable selection of coal varieties and the optimization of the combustion process are crucial to controlling production costs.
2. Heavy oil: Heavy oil is a petroleum product, the main component of which is hydrocarbons, with a carbon content between 82% and 87% and a hydrogen content of about 10% to 14%. It also contains a small amount of impurity elements such as sulfur, nitrogen, and oxygen. Among them, the sulfur content is generally between 0.5% and 3%. A higher sulfur content will also cause equipment corrosion and environmental pollution problems.
Calorific value: Heavy oil has a high calorific value of about 40-42MJ/kg. This allows it to provide a large amount of heat when burned, and can quickly raise the temperature in the cement rotary kiln to the required calcination temperature. Its high energy density makes it used in some rotary kilns with high temperature control requirements.
Combustion characteristics: The combustion of heavy oil requires good atomization conditions. It has a short flame and concentrated temperature when burning, which requires the burner to have good atomization performance to ensure that the heavy oil can be fully burned. Heavy oil is generally dispersed into fine oil droplets by mechanical atomization or medium atomization (such as steam atomization). The oil droplet size is usually between 50-200μm, which can increase the contact area between the oil droplets and the air and improve the combustion efficiency.
Cost perspective: The price of heavy oil is relatively high, and the price fluctuates greatly, which is affected by the international crude oil market. In terms of cost, due to its high calorific value, the cost of using heavy oil may be higher than coal under the same heat demand, but in some areas, considering environmental protection requirements and strict control of product quality, heavy oil will still be chosen as fuel. The proportion of its cost to production cost varies greatly due to price fluctuations, and may be around 40%-60%.
3. Natural gas: The main component of natural gas is methane (CH₄), which generally contains 80% - 99%. It also contains a small amount of hydrocarbons such as ethane (C₂H₆) and propane (C₃H₈) and non-hydrocarbon gases such as carbon dioxide (CO₂) and nitrogen (N₂). It contains almost no sulfur, produces relatively few pollutants during combustion, and has low corrosiveness to cement rotary kiln equipment.
Calorific value: Natural gas has a high calorific value of about 33 - 55MJ/m³. During the combustion process, it can provide stable heat and has high combustion efficiency. Using natural gas in cement rotary kilns can accurately control the combustion temperature and atmosphere, which is beneficial to improving the quality of cement clinker.
Combustion characteristics: Natural gas burns quickly, with a high and relatively stable flame temperature. Its combustion process is mainly the reaction of methane and oxygen, and the chemical equation is CH₄ + 2O₂→CO₂ + 2H₂O. A reasonable air ratio is required during combustion, and the general theoretical air volume is about 9-10 times the volume of natural gas. It can achieve good combustion through the burner, and the flame shape and temperature distribution can be adjusted according to the needs of the rotary kiln.
Cost perspective: The cost of natural gas varies from region to region and is affected by factors such as the distribution of natural gas resources and pipeline transportation costs. Its price is generally higher than coal, but lower than heavy oil. In the production cost, the cost of using natural gas as fuel may account for about 30%-50%. At the same time, with the improvement of environmental protection requirements, its low pollution advantage has led to more and more cement rotary kilns starting to use natural gas as fuel in some areas with higher requirements for environmental quality.
1. Preparation work before installation of rotary kiln: Before installing the cement rotary kiln, a series of technical preparation work needs to be carried out. First, the drawing review should be conducted to carefully examine the design drawings to ensure that the construction personnel have a clear and accurate understanding of the equipment structure, size, installation requirements, etc. Then, a construction plan should be prepared. The construction plan should cover the installation process, technical points, quality control measures, safety measures, etc., to provide detailed guidance for construction. Then, a technical briefing should be conducted to convey the key technical and quality requirements in the construction plan to each construction personnel so that they can clearly understand their respective work tasks and technical standards. At the same time, the company's relevant technical management regulations should be strictly implemented throughout the process to ensure the standardization and effectiveness of technical preparation work.
(1) Inspection of rotary kiln equipment: When the equipment is shipped out of the warehouse, a comprehensive and detailed inspection of the equipment should be carried out according to the packing list of the drawings. Focus on checking key components such as the support wheel, bearing base, wheel belt, kiln body and large gear ring.
(2) Inspection of the support wheel base: Check whether the base is deformed, and ensure that it meets the design requirements by accurately measuring the base height and the center distance of the bolt holes. Use professional tools to check the vertical and horizontal center lines of the base. After checking, accurately draw the vertical and horizontal center lines of the base according to the bolt holes, and punch eye marks at key locations so that they can be quickly and accurately positioned during subsequent installation.
(3) Inspection of rollers, bearings, and bushings: Carefully check the specifications of the rollers and bearings, and check the contact between the roller bearing seat and the spherical surface to ensure good contact and ensure the stability and reliability of the equipment. Check the vertical and horizontal center lines on the bottom surface of the bearing to ensure their accuracy. Pressure test the cooling water bushing of the bearing to ensure its sealing and pressure resistance. Assemble the rollers, bearings, and bushings as one, and use calipers or calipers to accurately measure the outer diameter, width, shaft diameter, inner diameter of the bushing and other parameters of the roller according to the drawing dimensions to ensure that the gap between the shaft diameter and the inner diameter of the bushing meets the requirements, and then number each component to facilitate subsequent installation and management.
(4) Inspection of the kiln body at the wheel belt and the wheel belt: Carefully check the inner diameter, outer diameter, width and other dimensions of each wheel belt, and at the same time check the diameter of the kiln body wheel belt and the net distance of the bolt holes of the fixed steel ring on the pad to ensure the matching accuracy of the wheel belt and the kiln body, and avoid installation difficulties or unstable equipment operation due to size deviation.
(5) Inspection of kiln body length and local deformation: Check the position of each section of the kiln body and the pad on the kiln body in detail, and draw a construction drawing as a basis for installation. Accurately measure the length of the kiln body, the ovality of the two pairs of interfaces, the size from the center line of the wheel belt to the edge of the kiln body interface, and the size from the center of the large gear ring to the edge of the kiln body interface to ensure that the overall size and shape of the kiln body meet the design requirements and prevent the deformation of the kiln body from affecting the normal operation and service life of the equipment. The large gear ring is usually composed of two halves. It is important to check whether the gear at the interface is equal to the other gears, whether the bolt holes are concentric, and whether the contact surface is flat. At the same time, check the specifications of the gear ring and the spring plate to ensure that the bolt holes and their distances are equal to ensure the transmission accuracy and stability of the large gear ring.
(6) Inspection of reinforcement rings and wheel retaining rings: Check whether the reinforcement rings and wheel retaining rings are deformed. Their inner diameter should be 2-3mm larger than the outer ring size of the kiln body reinforcement plate to reserve space for thermal expansion of the kiln body during operation to avoid component damage or equipment failure due to thermal expansion.
(7) Inspection of equipment foundation: The inspection of equipment foundation is crucial and should comply with the requirements of design drawings, equipment technical documents and relevant specifications. Check the strength, flatness, elevation, location and size of the foundation anchor bolt holes and other parameters to ensure that the foundation can provide stable and reliable support for the equipment and ensure the accuracy and stability of the equipment after installation.
2. Equipment pre-assembly
(1) Kiln body with wheel: For kiln bodies with wheel, the wheel needs to be put on the kiln body on the ground. First, hoist the kiln body steadily on the wooden pier, and use diagonal wood to plug and pad on both sides to keep it horizontal. Then use the lifting equipment to lift the wheel vertically to the same height as the kiln body, and then slowly move it inward to put the wheel on the kiln body. During this process, pay special attention to the horizontality of the kiln body. After the wheel is put on the kiln body, the steel ring should be installed immediately, and the connection of the steel ring should be completed on the ground as much as possible. This can improve the installation efficiency and quality and reduce the risk of high-altitude operations.
(2) Kiln body assembly: According to the actual situation of the kiln body arriving in sections, select appropriate construction and lifting equipment. The kiln body of two, three or more sections can be pre-assembled on the ground and then hoisted as a whole. After the kiln body interface is put on the connecting bolts and the connecting plate is welded, the hoisting operation can be carried out. If the kiln body is placed on the supporting wheel so that it can rotate freely, it can speed up the kiln body connection speed and improve the welding quality. The ground for temporary installation of the support wheel needs to be compacted and covered with stones and sleepers to ensure the stability of the support wheel and the smooth rotation of the kiln body.
(3) Pre-installation of the pinion part of the transmission device: First, install the pinion and bearing transported in parts on the base, and then install the backrest wheel on the pinion shaft for subsequent overall lifting. During the pre-installation process, the installation must be carried out strictly in accordance with the requirements of the drawings to ensure that the installation position and accuracy of each component meet the design standards, laying the foundation for the normal operation of the transmission device.
(4) Pre-installation of spring plate and large gear ring: The large gear ring is driven by the spring plate installed on the kiln body. On the ground, first adjust the kiln body to find the circle, then accurately mark the center line of the spring plate on the circumference, and evenly mark 12 equal parts along the circumference of the line. Then align the spring plate with the vertical and horizontal center lines marked with the corresponding lines on the kiln body, install and weld them one by one on the kiln body. Precise preinstallation can ensure the installation accuracy of the spring plate and the large gear ring, and ensure that the large gear ring can stably and accurately transmit power when the kiln body rotates.
(5) Preinstallation of chain brackets and heat exchange plates: Preinstall the chain brackets and heat exchange plates according to the design requirements, check whether the installation position and connection method of each component are correct, ensure that they can function normally after formal installation, and improve the heat exchange efficiency of the kiln body and the calcination effect of the material.
(6) Preinstallation of cooling cylinder: Preinstall the square head, refractory cast steel plate, refractory bricks, chain, etc. that need to be preinstalled on the cooling cylinder before installation. This can reduce the installation time and workload on the kiln body and improve the installation efficiency. At the same time, it is also convenient to check and adjust the installation quality of the internal components of the cooling cylinder to ensure that the performance of the cooling cylinder meets the requirements.
(7) Draw construction drawings: Draw detailed and accurate construction drawings based on the actual inspection and measurement results of the equipment geometric dimensions. The main contents of the construction drawings include key parameters such as the distance between adjacent wheel bands, the longitudinal distance between adjacent support rollers, the height difference of the top column of adjacent wheel bands, and the elevation difference of adjacent support rollers. These parameters will provide precise guidance for subsequent equipment installation, ensuring that the installation position and accuracy of each component meet the design requirements and guaranteeing the overall performance and operational stability of the rotary kiln.
3. Installation of rotary kiln
The rotary kiln is preferably installed before the kiln head and kiln tail buildings are above the ground, which can reduce space restrictions and interference during the installation process and improve installation efficiency and quality.
(1) Installation of supporting parts: Hoisting of roller base: Hoist the base, bearing and roller separately on the foundation and assemble them on the foundation pier. Before hoisting, all parts should be placed under each foundation pier in order according to the part number to achieve continuous hoisting operation and improve construction efficiency. After all the supporting parts are hoisted, the roller should be aligned immediately to ensure that the installation position and accuracy of the roller meet the design requirements and provide reliable support for the stable operation of the kiln body.
(2) Alignment of roller base: Check the center distance of the rollers on the same foundation pier. For this purpose, a special sample rod is made. Its length is based on the center distance of the largest pair of rollers, and the sample rod length should be adjustable to meet different measurement needs. For the inspection of the longitudinal center, two plumb lines can be used to align the reference point to ensure that the center of the roller base is consistent with the center of the foundation. The elevation of the supporting roller can be checked with a level or a U-tube level (when using a U-tube level, please note that the inner diameter of the rubber tube should not be less than 16mm, there should be no bubbles in the rubber tube, and the length of the rubber tube should be 25-30m). Through precise measurement and adjustment, the elevation of the supporting roller can be ensured to meet the design requirements to avoid problems such as uneven force and vibration during the operation of the kiln body due to inconsistent supporting roller elevation.
(3) Inspection of the inclination of the supporting roller: Use a steel ruler, frame level, inclination gauge and other tools to check the inclination of the supporting roller. Since the center elevation, inclination and center distance of the supporting roller are interrelated, several items must be adjusted repeatedly at the same time during alignment to ensure that all parameters meet the design standards, so that the kiln body can rotate smoothly and smoothly on the supporting roller, and ensure the normal operation and service life of the equipment. First, align the transmission foundation, supporting roller and its base, and then use it as a reference to align other components in sequence. After all supporting rollers are aligned, grout the anchor bolts. After the curing period reaches a certain time, tighten the anchor bolts and recheck to ensure that there are no errors before proceeding to the next process to prevent equipment failure due to loose anchor bolts or inaccurate installation.
(4) Kiln body installation: Before hoisting the kiln body, first hoist the reducer, pinion wheel and safety device to the foundation. Start the installation from the kiln body with transmission equipment in the middle of the kiln, and then install each pre-assembled kiln body one by one towards the kiln head or kiln tail. When installing the kiln body with a wheel belt, the wheel belt must be put on the kiln body on the ground. After the last section of the kiln body is hoisted into place, it is bolted to the previous section of the kiln body. During the installation process, pay attention to using a plumb line to find the vertical position before hoisting the kiln body to avoid the need for a large rotation due to the mismatch of the front and rear kiln bodies when hoisting into place, which affects the installation efficiency and quality, and may even cause damage to the kiln body. When connecting the kiln body, install gaskets between the two bodies along the circumferential direction. After the two sections of the kiln body are aligned, pad the gaskets and tighten the connecting bolts. If the kiln body interface is uneven, it should be trimmed until it meets the requirements to ensure the sealing and stability of the kiln body connection. When the kiln body extends out of the foundation for a long time, it must be padded with wooden blocks under the extended kiln body to prevent the kiln body from deforming or displacing due to its own weight, which will affect the installation accuracy and subsequent operation of the equipment.
(5) Installation of the large gear ring: After the middle kiln body is hoisted, the large gear ring is hoisted immediately. Hoist half of the large gear ring to the upper side of the spring plate, use two fall chains to pull the large gear ring close to the spring plate, and string the bolts. The alignment of the large gear ring and the kiln body rotary kiln alignment are carried out simultaneously. First, tighten the spring plate bolts at the corresponding points, and then align the rotary kiln. According to the deviation recorded in the alignment, add or remove pads between the spring plate and the inner circle of the gear ring to adjust the center of the gear ring, ensure that the center of the large gear ring coincides with the center of the kiln body, ensure the meshing accuracy of the large gear ring and the small gear, make the transmission smooth and reliable, reduce equipment wear and energy loss, and improve the operating efficiency and service life of the equipment.
(6) Installation of small gear: Hang a steel wire above the center mark plate of the front and rear piers of the transmission foundation so that it is in the same vertical plane as the center line of the kiln. Use a steel ruler to measure the distance from the center of the kiln to the axis to determine the installation position of the small gear. The elevation of the small gear is determined by the meshing clearance of the large gear ring and the small gear teeth. The pitch lines of the two gears should be 5mm apart. When aligning the small gear, turn the eccentric highest point of the large gear ring to the meshing point of the gear. The inclination of the small gear is the same as the inclination of the kiln. Check on the axial surface of the small gear to ensure that the clearance between the large gear ring and the small gear and the inclination of the small gear meet the requirements, so that the small gear is in the correct position to ensure the normal operation and efficient transmission of the transmission system.
(7) Center alignment at the kiln body interface: Mark 6 to 12 equally divided points at each kiln body interface, set up a wooden frame under each interface, fix a point on the wooden frame under the kiln body, then rotate the kiln body, use a ruler to measure the distance between the fixed point and the equally divided point on the kiln body, measure all 6 to 12 points in sequence, and keep a record. Then compare the distance dimensions of the corresponding points. If they do not meet the requirements, adjustments must be made. The adjustment method is to place the jack on the pile of wood under the kiln body to support the kiln body, then loosen the kiln body interface connection bolts, and adjust the upper and lower gaps of the interface to make them uniform. After adjustment, tighten the interface bolts, then loosen the jack and rotate the kiln for rechecking until the adjustment is qualified. When aligning, it is important to check the kiln body deviation at the kiln head, kiln tail and gear, and the radial swing deviation of the kiln body, to ensure that the deviations of the kiln head, kiln tail, large gear ring, kiln body and other parts meet the requirements of the equipment technical documents and design drawings, to ensure the overall operation accuracy and stability of the kiln body, and to avoid equipment failures and uneven material calcination caused by kiln body deviation, which will affect the quality and output of cement production.
(8) Kiln body welding: Kiln body welding should be carried out after the transmission equipment is installed and the kiln body is aligned. The kiln body welding must be carried out strictly in accordance with the requirements of the design drawings, equipment technical documents and the company's relevant welding management regulations, and the welding must be carried out by certified welders according to the parameters of the welding process instructions. The welding work adopts flat welding, and the kiln body is rotated slowly, which can ensure the welding quality and reduce welding stress and deformation. The quality of the weld should be inspected by X-ray inspection according to the requirements of the equipment technical documents, design drawings, and welding process cards to ensure that the weld has no defects such as cracks, pores, slag inclusions, etc., and can only be transferred to the next process after meeting the strength and sealing requirements to prevent serious failures such as kiln leakage and cracking caused by weld quality problems, which will affect the safe operation and service life of the equipment.
(9) Secondary review of the kiln center: After the kiln body is welded, the kiln center must be reviewed again. Check whether the center of the wheel band is on the same vertical plane. Take the connecting line of the center of the kiln head and kiln tail wheel band as the standard. Pull the steel wire 1 meter above the kiln side to make the distance between the kiln head and kiln tail wheel band sides and the steel wire equal. In this way, the steel wire is parallel to the kiln center. Then hang a plumb bob on the steel wire on each side of the middle wheel band, and measure X1, X2, etc. with a steel ruler. The distance between the wheel band edge and the steel wire of the same diameter is equal, and the wheel band center is on a straight line. If there is an error, find out the cause and adjust it. The adjustment should be made carefully, and the manufacturing error of the outer diameter of the wheel band should be taken into account to ensure that the center line of the kiln body meets the design requirements, ensure the stability and uniformity of the kiln body during operation, avoid equipment vibration, increased wear, uneven material calcination and other problems caused by kiln center deviation, and improve the equipment's operating efficiency and product quality.
(10) Kiln wheel band inclination inspection
Put the level meter on the heads of the two side wheels, adjust the level meter and fix it, and read the elevation difference between the two wheels. Measure all the wheels in turn in the same way, and compare the measured figures with the calculated elevation difference on the construction sketch to see the installation error. By checking the kiln wheel band inclination and analyzing the errors, problems in the wheel band installation process can be discovered and corrected in time to ensure that the kiln body inclination meets the design requirements, so that the materials can be calcined in the kiln according to the predetermined trajectory and speed, improve the quality and output of cement clinker, and also help to extend the service life of the equipment.
(11) Check the longitudinal relative position between the roller and the tyre: Draw the center lines of the tyre and the roller, check the actual misalignment, and make records based on the roller of the transmission foundation pier. By checking the longitudinal relative position between the roller and the tyre, ensure that the relative position of the two meets the design requirements, avoid poor contact and uneven force between the roller and the tyre due to position deviation, thereby reducing wear and damage to components and ensuring stable operation and long-term reliable use of the equipment.
(12) Installation of reinforcement ring: The reinforcement ring is installed on the auxiliary reinforcement ring on the kiln body, and is supported by welded support iron between the reinforcement ring and the auxiliary reinforcement ring. A gap of 2-3mm should be left in between to take into account the expansion of the kiln body during production. The reinforcement ring consists of two half rings with special letterheads on them, which must not be used indiscriminately. First, a special routing slider is laid on the kiln body, and the two halves of the reinforcement ring are hung on the auxiliary reinforcement ring of the kiln body with the routing slider. The tensioning device is used to tighten the two reinforcement rings and use it to adjust the gap around. After alignment, the interfaces on both sides are welded with electric welding, and then the tensioning device is removed, the matching connection plate is welded, and the supports on both sides are welded to the auxiliary reinforcement ring. By correctly installing the reinforcement ring, the strength and stability of the kiln body are enhanced, and the kiln body is prevented from being deformed or damaged due to thermal stress, material impact and other factors during operation, ensuring the safe operation and normal production of the equipment.
(13) Installation of windshield ring: First, assemble all the rings on the ground, then hang the friction ring and cast iron ring on the kiln body, fix them with wooden planks around, and find the gap and center position. Support the wooden formwork on the circumference of the cast iron ring, pour concrete between the brick wall and the wooden formwork, and after the concrete curing period is over, remove the wooden wedges and pour concrete on the anchor bolts of the cast iron frame. During installation, a layer of lubricant mixed with graphite and dry butter should be applied to the sliding surface of the windshield ring to reduce the friction resistance between the windshield ring and the kiln body, ensure the flexible rotation and sealing performance of the windshield ring, prevent external cold air from entering the kiln, and affect the calcination effect and thermal efficiency of the material, while also reducing the energy consumption and operating costs of the equipment.
(14) Installation of cooling cylinder: First install the 12 cast iron connection parts at the clinker outlet on the kiln body, install the cooling cylinder bracket on the cylinder body, install the feed joints of the cooling cylinder, then hoist the cooling cylinder on the bracket and connect it with the feed joints, and finally fix it firmly on the bracket with a connecting ring. Before installing the cooling cylinder, first build all the conveying plates, lining plates, chains and refractory bricks in the cooling cylinder for overall hoisting. By properly installing the cooling cylinder, the cooling efficiency of the kiln body is improved, the clinker can be cooled quickly, the quality and performance of cement are improved, and it is also beneficial to protect the equipment and extend the service life of the equipment.
4. Trial commissioning
The trial operation plan must be prepared in accordance with the equipment technical documents, regulations, and specifications, and all contents must be implemented according to the plan. The trial operation of a single machine is carried out in two stages.
Trial operation before bricklaying
(1) Trial operation time: 2 hours of no-load trial operation of the motor, 2 hours of auxiliary motor driving, 4 hours of no-load trial operation of the motor with reducer, and 8 hours of trial operation of the main motor with equipment. By setting a reasonable trial operation time, the various components of the equipment are fully run-in and performance tested to timely discover potential problems and hidden faults.
(2) Inspection contents before trial operation: whether there are foreign objects, welding slag, etc. on the surface of the support wheel and the surface of the wheel belt, the cleanliness of the inner surface of the wheel belt and the surface of the wheel belt pad (blow it clean with compressed air if necessary), the contact condition of the transmission gears, the sealing condition of the kiln head and kiln tail, etc. Before the trial operation, a comprehensive and detailed inspection should be carried out to ensure that all components of the equipment are in a good initial condition to avoid factors such as foreign objects and dirt.
CEMENT CLINKER ROTARY KILN SPECIFICATION:
Parameter Name | Details |
Equipment Name | Rotary Kiln |
Application | Cement clinker calcination for a 6000t/d clinker production line |
Specification | Φ5.4×78m (Inner diameter × Length) |
Type | Double drive, single hydraulic thrust roller |
Kiln Support | 3 supports |
Inclination | 4% (sine) |
Shell Rotation Speed | Main drive: 0.4~4 r/min |
Auxiliary drive: 0.146 r/min | |
Main Motor Model | ZSN4-450-12 |
Power | 875 kW |
Armature Voltage | 660V |
Speed | 1000 r/min |
Speed Range | 100~1000 r/min |
Tachometer Generator | Model: ZYS-3A |
Power: 22W | |
Voltage: 110V | |
Speed Range: 0~2000 r/min | |
Main Reducer Model | TLK950C-28 |
Center Distance | 1980 mm |
Reduction Ratio | 26.646 |
Lubrication Station Model | XYZ-160GZ |
Oil Pump Motor | 7.5KW (2 units) |
Electric Heating Power | 24KW/220V |
Auxiliary Drive System | Motor: Y280M-4 |
Power: 90 kW | |
Voltage: 380V | |
Speed: 1550 r/min | |
Reducer Model: ZSY400-35.5-Ⅰ | |
Center Distance: 880 mm | |
Reduction Ratio: 35.795 | |
Electro-Hydraulic Brake | Quantity: 1 set |
Model: YWZE-400/125 | |
Hydraulic Thrust Pump Station | Model: ZXY-14 |
Stroke: ±25mm | |
Total Weight: 1114.9 kg |
CEMENT CLINKER PYRO-PROCESS KILN TECHNICAL PARAMETER:
Component Name | Quantity | Specification/Model | Additional Details |
Main Motor | 1 set | ZSN4-450-12 | 800 kW, 660V, 1000 r/min, Protection Grade IP54, Insulation Grade F |
Main Reducer | 1 set | JH900C-SW305-28 | Center Distance: 1980 mm, Reduction Ratio: 26.646 |
Auxiliary Drive System | 1 set | Y280M-4 | 90 kW, 380V, Speed: 1480 r/min, Reducer Model: ZSY400-35.5-Ⅰ |
Open Gear Transmission | 1 set | Double drive, Ratio 9.43 | Large Gear: Module 40×Teeth 198×Width 600 |
Pinion: Module 40×Teeth 21×Width 650 | |||
Support Device I | 1 group | Roller: Φ2250×950 | Material: ZG35CrMo, Weight: 2×18200 Kg |
Support Device II | 1 group | Roller: Φ2500×1150 | Material: ZG35CrMo, Weight: 2×27300 Kg |
Riding Ring | 3 pieces | Φ6300×900 (Ⅰ), Φ6300×1050 (Ⅱ), Φ6300×950 (Ⅲ) | Material: ZG35Mn, Total Weight: 177,155 Kg |