Rotary kiln incineration solutions for the management & treatment of hazardous residues from the EAF steel slag and galvanisation industry.
Tongli zinc oxide rotary kiln is a highly efficient equipment for steel dust treatment. In the steel production process, a hazardous waste called "steel dust" is generated when the electric arc furnace recycles steel scrap. Compared with the traditional Waelz process, the rotary kiln produced by Tongli for the Belgian company BEFESA adopts the patented Waelz SDHL process of BEFESA. This process is for the zinc-containing dust, sludge and filter cake waste provided by BEFESA, which are first stored in closed silos. Then these raw materials are mixed with water, coke and lime and made into uniform micro-spherical particles, which enter the rotary kiln directly or through intermediate storage. The operating temperature of the rotary kiln is about 1200°C. At this high temperature, the volatile compounds in the raw materials (mainly zinc) are converted into gaseous state and oxidized to form zinc oxide (Waelz oxide). Through the exhaust gas treatment facilities, these zinc oxides are recovered and become secondary raw materials for the zinc industry. At the end of the rotary kiln, most of the reduced iron can be re-oxidized to iron oxide (FeO) by selectively adding air to the charge. The heat generated by the oxidation reaction is used to preheat the incoming air and provide the required heat energy for the reaction zone. The optimization of this process is due to the application of SDHL technology, which significantly improves the efficiency compared to the traditional Walz process. In addition, the Walz plant further purifies the zinc oxide through multi-stage washing, and the slag produced in the process can be used as a building material and asphalt aggregate in the cement industry.

WAELZ FURNACE ZINC OXIDE

"Efficiently recover zinc oxide from industrial waste with our Waelz incinerator kiln. Designed for eco-friendly and high-yield recycling of zinc-containing materials."

"Advanced EAF furnace slag recycling kiln for high-purity zinc oxide recovery. A sustainable solution for steelmaking waste management."

"Optimize zinc recovery from steel dust using our advanced rotary kiln technology. Sustainable, cost-effective, and compliant with environmental regulations."

"Innovative SDHL-Waelz process kiln for efficient zinc oxide recovery. Maximize resource utilization while minimizing environmental impact."
EAF DUST RECYCLE ADVANTAGES
Energy saving: The recycling of scrap steel is very important to reduce the mining of crude steel, conserve natural resources and thus protect the environment. About 40% of the steel produced in Europe comes from scrap steel recycled through the electric arc furnace process (EAF process). The exhaust gases from the process are treated and cleaned, and 15 to 20 kg of dust are collected for every ton of steel produced.
Low energy consumption: Compared with the traditional production process of extracting zinc oxide from ore, the energy consumption of the technology of refining zinc oxide from electric furnace ash is much lower. In the reduction reaction of the electric furnace, the heat generated by the reaction of coke and oxygen can be directly used for the reduction reaction and the oxidation reaction of zinc, thereby reducing energy waste.
Environmental protection: The environmental protection performance of the technology of refining zinc oxide from electric furnace ash is very good. First, the technology does not require high-temperature smelting, which reduces the emission of a large amount of carbon dioxide and other harmful gases; secondly, the raw materials required for this technology are mainly zinc furnace slag, which can effectively utilize waste resources and reduce environmental pollution.
High efficiency: The production efficiency of the technology of refining zinc oxide from electric furnace ash is very high. This technology can realize automated production, greatly improving production efficiency and product quality. In addition, the production cost of this technology is also relatively low, which can effectively improve the economic benefits of the enterprise.
High degree of resource recycling: In addition to zinc, electric furnace ash also contains lead, iron and other metals. In the process of refining zinc oxide, these associated metals can also be effectively recycled. For zinc resources themselves, this technology can effectively convert low-grade zinc sources (such as zinc oxide in electric furnace ash) into zinc oxide products with high economic value, so that zinc-containing waste that may have been wasted or required high-cost treatment can be fully utilized.
Good product quality stability: Since the technology performs mixing and homogenization treatment in the raw material pretreatment stage, the raw material composition entering the rotary kiln can be relatively stable and uniform. This stability is conducive to the precise control of reaction conditions during the high-temperature treatment process of the rotary kiln, making the zinc oxide generation process more stable. In addition, in the zinc oxide collection stage after exhaust gas treatment, impurities can be effectively removed through dust removal and multi-stage cleaning and purification steps.
High process flexibility: The technology of extracting zinc oxide from electric furnace ash can be appropriately adjusted according to the composition and properties of the raw materials. For example, in the raw material pretreatment stage, for electric furnace ash with different zinc content and different impurity components, the mixing ratio, added reagents (such as the amount of lime used to adjust the pH) and granulation parameters can be flexibly adjusted to adapt to different raw material conditions.
Strong technical compatibility: In terms of the operating parameters of the rotary kiln, such as temperature, air supply, etc., can also be optimized according to actual conditions to ensure that zinc oxide can be efficiently extracted under various raw material conditions. This process flexibility allows the technology to process electric furnace ash generated from different steel production processes, expanding the source range of raw materials. At the same time, the heat at the tail of the rotary kiln is used to preheat the air or generate steam for power generation, heating, etc.
WAELZ KILN ZnO INCINERATION RECYCLE PROCESS

Raw material storage
The electric arc furnace (EAF) produces a large amount of steel dust (EAFD) during the steel production process, which is a hazardous waste containing metal oxides such as zinc, lead and iron. The dust is collected according to strict environmental standards and sent to the Waelz process plant. Once in the plant, the dust is stored in closed silos or specially designed covered storage areas to prevent dust and moisture from affecting the raw materials. Storage management: Depending on the size of each facility, the storage capacity can meet one to two months of production needs to ensure production continuity. To avoid fluctuations in the chemical composition of raw materials affecting processing efficiency, waste is usually stored by source and composition.
Raw material granulation
Before entering the incineration process, the EAFD raw materials need to undergo complex pretreatment to ensure efficient reaction in the rotary kiln. Mixing and homogenization: The raw materials from different sources have different compositions, so they need to be mixed and homogenized according to the main components such as zinc, iron, carbon, etc. to ensure the consistency of the materials in the kiln. Water addition and granulation: The mixed raw materials are granulated with water, lime (for adjusting the acid-base balance) and coke (as a reducing agent) to form uniform micro-granules (microspheres). These granules have good strength and air permeability, suitable for high-temperature treatment in the rotary kiln. Objective: The purpose of granulation is to reduce dust dispersion at high temperatures, increase the contact area between the material and the reaction gas, and optimize the mass and heat transfer efficiency of subsequent operations.
rotary kiln calcination
After granulation, the raw materials are transported to the Waelz rotary kiln, which is the core of the whole process. Kiln environment and temperature: The temperature in the kiln is maintained at about 1200°C, which is in the boiling point range of volatile metals such as zinc and lead. The interior of the rotary kiln is filled with carbon monoxide (CO) and heat produced by coke, and the metal oxides in the raw materials undergo reduction reactions in this environment. Reaction mechanism: The carbon in the coke and the heat reduce zinc oxide (ZnO) to metallic zinc (Zn). Zinc volatilizes to gaseous state at high temperature and flows out of the rotary kiln with the exhaust gas, while non-volatile metals such as iron remain in the kiln and form slag with other substances. Air conditioning: By adding an appropriate amount of air to the kiln tail, the heat generated by the partial oxidation reaction is used to heat fresh air. This heat recovery technology improves energy utilization and also helps to stabilize the temperature in the kiln.
Exhaust gas collection
After volatile metals such as zinc enter the gas phase, they flow with the waste gas to the waste gas treatment system at the end of the rotary kiln. Cooling and dust removal: The waste gas is quickly cooled, and the volatile metals are re-oxidized to form fine particles of Waelz zinc oxide (WZO). Dust removal devices (such as bag filters or electrostatic precipitators) separate zinc oxide from the air flow. Waste gas purification: The waste gas at the end of the kiln also contains other harmful substances such as sulfur dioxide (SO₂) and nitrogen oxides (NOx). Through multi-stage treatment technologies such as desulfurization and denitrification, these waste gases are purified and discharged after meeting the standards. Zinc oxide collection: The final collected zinc oxide product can reach a purity of 55%-65%, which is provided to the zinc smelting industry as a high value-added secondary raw material.
Slag treatment and recycling
The solid residue left after the rotary kiln treatment has a temperature of about 800 to 1000 degrees Celsius. After entering the water-cooled slag collector and cooling, it is called slag, which is mainly composed of iron oxide (FeO) and a small amount of other unreacted elements. Uses: In the construction industry, slag is processed into an additive for the cement industry or used as asphalt aggregate. At Befesa's Spanish plant, this slag is promoted under the brand name Ferrosita® and is used in areas such as road infrastructure construction. Environmental characteristics: The reuse of slag not only reduces waste emissions, but also provides a sustainable alternative material for downstream industries.
Zinc oxide purification
Some Waelz plants, such as Befesa Zinc Freiberg, are equipped with a multi-stage washing system to further purify the recovered zinc oxide. The washing steps are: two to three stages of chemical washing process to remove impurities (such as chlorides and sulfides) in the zinc oxide. The zinc content of the final product is increased to a higher purity level to meet the needs of advanced zinc smelters.
Heat reuse
The Waelz process significantly reduces energy consumption by utilizing efficient heat recovery technology: At the end of the rotary kiln, heat is recovered via a gas-to-air heat exchanger and used to preheat fresh air or provide heat for other process steps. . Some factories have installed waste heat boilers to convert the waste heat of exhaust gas into steam for power generation or heating. This closed-loop thermal management significantly improves the plant’s energy efficiency.
VIDEO
WHY CHOOSE US
“The zinc oxide rotary kiln not only has high processing efficiency, but also has a very consistent final product quality. By converting the slag from our steelmaking furnace production process into building materials, we can further reduce our waste disposal problems.”
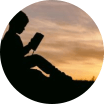
CFO
"The performance of Tongli zinc oxide rotary kiln is very satisfactory. It efficiently processes our steel dust waste and converts it into high-value secondary raw materials. The equipment has been running well since it was put into production."

CEO
"We chose Tongli zinc oxide rotary kiln because Tongli has produced several kilns for the internationally renowned brand BEFESA, which shows that Tongli's product quality is reliable."

CEO
"We are very impressed with the performance of the zinc oxide rotary kiln provided by Tongli. It has shown strong adaptability in processing zinc-containing waste with complex components, from raw material storage, mixing to high-temperature treatment. The secondary pollution control of this system is very good, and the treatment of waste gas and waste residue is in full compliance with environmental protection regulations."

CEO
FAQ
1. The zinc oxide market has broad development prospects, especially in the context of increasingly stringent environmental protection requirements. The production of Walz zinc oxide (WOx) by recycling electric arc furnace dust (EAFD) has become an important business opportunity.
The raw material for the production of Walz zinc oxide is EAFD, and about 30% of zinc oxide can be recovered from each ton of EAFD. Its sales price is linked to the London Metal Exchange (LME) zinc price, which is usually between $1,600 and $2,400 per tonne. Compared with landfilling EAFD (costing about $50-100/ton), recycling not only saves costs but also generates revenue through the sale of zinc oxide.
2. The continuous strengthening of environmental regulations has prompted companies to more actively adopt recycling programs. The Walz zinc oxide plant uses advanced emission control technology to effectively reduce the emission of harmful substances (such as dioxins and furans). This model can help companies reduce environmental risks while achieving resource recycling and maximizing economic benefits.
3. Products and Applications
Walz Zinc Oxide (WOx)
Walz zinc oxide can be widely used in the steel industry (such as iron aggregate), construction materials (such as rock wool and filling materials) and gardening.
Inert Slag
The recycling process also produces inert slag, which can be used as raw material for cement and road filling materials, further improving resource utilization. Its price is generally between US$1 and US$5 per ton.
4. Plant Operations and Costs
WOx plants are core facilities for hazardous material processing and important platforms for resource recovery. The operating costs of the plant are affected by the market prices of electricity, natural gas, water, reducing agents and lime. It is currently estimated that the processing cost of each ton of EAFD is approximately US$160-180.
5. The drive to recycle
The use of scrap steel (SCRAP) in the steelmaking process not only improves profitability but also brings recycling value to EAFD. Through a more efficient fume exhaust system, more EAFD can be collected, while reducing emissions during the steel smelting process and promoting clean production.
In the metallurgical industry, the smelting and processing of ores will produce a large amount of waste slag, which often contains a variety of valuable metals (such as zinc, lead, etc.). Traditional treatment methods may lead to the waste of these valuable metals, and the heavy metals in the waste slag will cause serious pollution to the environment if they are not properly disposed. The main purpose of the Waelz process is to effectively recover valuable metals, especially zinc, from these complex heavy metal-containing waste slags.
1. Raw material preparation:
Raw material type: The main raw materials are complex sulfide ores or metallurgical waste slag containing heavy metals such as zinc and lead. For example, zinc leaching slag produced during zinc hydrometallurgy contains zinc oxide (ZnO), zinc sulfide (ZnS) and lead compounds such as lead sulfate (PbSO₄). Mixed raw materials: The waste slag is mixed with coke (as a reducing agent) and flux (such as limestone) in a certain proportion. Coke is used to provide the carbon source required for the reduction reaction, and the flux helps to lower the melting point of the slag and improve the fluidity of the reaction. For example, the appropriate coke to waste slag mass ratio may be around 1:4 - 1:6, and the amount of flux added depends on the composition of the waste slag and the desired slag properties.
2. Calcination zinc recovery:
The key equipment of the waelz process is the rotary kiln. The rotary kiln is an inclined, slowly rotating cylindrical device. It enables the raw materials to tumble continuously in it, thereby ensuring that the raw materials are in full contact with the reducing agent and flux, and can experience different temperature zones along the axial direction of the kiln body to achieve continuous physical and chemical changes. The rotary kiln is generally made of high-temperature resistant metal materials (such as alloy steel) and lined with refractory materials to withstand high temperature environments. Its length can reach tens of meters and its diameter can reach several meters. The rotation speed is relatively slow, usually a few to more than ten revolutions per minute, so that the raw materials can have enough residence time in the kiln for reaction.
3. Recovery process:
Reduction reaction stage: In the high temperature area of the rotary kiln (generally at 1100-1300℃), coke reacts with metal oxides in the waste slag to form a reduction reaction. Taking zinc as an example, the main reaction is that the generated zinc exists in the form of vapor. For lead compounds, similar reduction reactions also occur, such as. These reactions are endothermic reactions and require sufficient heat from the outside to maintain the reaction.
4. Oxidation and collection stage:
The metal vapor (mainly zinc vapor) escaping from the rotary kiln enters the oxidation zone, where it undergoes an oxidation reaction with oxygen in the air to generate zinc oxide powder, which can be collected by dust collection equipment (such as bag dust collectors, electrostatic dust collectors, etc.).
5. Slag formation and discharge:
During the reduction process, some impurities in the waste slag react with the flux to form slag. The main components of the slag include silicon dioxide (SiO₂), calcium oxide (CaO), etc., which flow in liquid form at the bottom of the rotary kiln and are eventually discharged from the end of the kiln. The slag can be further used in building materials and other fields.
6. Process advantages
(1)Efficient resource recovery: It can effectively recover valuable metals such as zinc and lead in waste slag, improve the total recovery rate of metals, and the recovery rate of zinc can reach about 70-80%, greatly reducing the waste of resources.
(2)Environmentally friendly: By recovering valuable metals, the content of heavy metals in waste slag is reduced, and the risk of waste slag pollution to the environment is reduced. At the same time, the recovered metals can be reused in industrial production, reducing dependence on primary ore.
(3)Mature process: The Waelz method is a mature process that has been tested in long-term practice. The equipment is relatively simple, the operation is stable, and it is easy to apply on an industrial scale.
The WOX process is recognized as the Best Available Technique (BAT) for EAFD recycling by the European IPPC Bureau and the EPA (USA). This process utilizes a tongli rotary kiln, where a combination of reducing and oxidizing atmospheres is employed to separate zinc and iron effectively. In this system, zinc is vaporized at high temperatures, while iron remains as an inert slag within the kiln. The vaporized zinc is then cooled in a settling chamber and further collected using a high-efficiency baghouse system located adjacent to the chamber. The process features a single emission point at the fume stack. Prior to emission, the off-gases pass through an advanced treatment system designed to remove dioxins, furans, and other hazardous materials, ensuring compliance with stringent environmental standards. The WOX process represents a sustainable, efficient, and environmentally friendly solution for managing and recycling EAFD.
1. Design Capacity:
The EPC construction project is designed to process 110,000 tons of Electric Arc Furnace Dust (EAFD) annually, employing a combination of pyrometallurgical and hydrometallurgical processes. The plant features a rotary kiln with diameter 4x55 meters in length, tailored for efficient material recovery and high operational reliability.
2. Raw material proportion composition:
EAFD, the primary raw material for this facility, contains approximately 30% iron, 20–25% zinc, and 1% lead. To optimize the recovery process, the plant requires 18,700 tons of reducing agents and 8,000 tons of lime annually. These inputs support the separation and extraction of valuable materials while ensuring stable processing conditions.
3. Actual output:
The plant’s output includes 33,000 tons per year of Waelz Oxide (WOx), which boasts an approximate zinc content of 65%, and 77,300 tons of inert slag. The WOx serves as a valuable resource for downstream industries, while the inert slag can be utilized in construction materials, ensuring minimal waste generation.
4. Exhaust gas dedusting:
A state-of-the-art fume exhaust system ensures environmental compliance by maintaining a dust content of only 0.5%. This system is integral to minimizing emissions and addressing regulatory standards effectively.
5. Factory operation indicators:
To sustain operations, the plant consumes approximately 3,300 MWh of natural gas and 6,150 MWh of electricity per year. Additionally, 202,000 cubic meters of water are required annually to support cooling and processing activities, emphasizing the need for efficient utility management.
This facility represents a significant step forward in sustainable industrial practices, leveraging advanced rotary kiln technology and efficient raw material handling to maximize resource recovery while adhering to stringent environmental requirements.
The Pyrometallurgical process is enough for WOx production, but
the Hydrometallurgical processimproves the zinc concentration of the Final Product, improving investment return
As the requirements of environmental legislation become more and more stringent, the requirements for the environmental adaptability of steel enterprises are also constantly increasing. Therefore, some technical methods for reducing energy consumption, reducing waste emissions and recycling waste have been vigorously promoted in steel mills. Some steel mill waste recycling and reuse technologies developed in recent years have been successfully applied. These technologies can achieve the effects of reducing waste emissions, saving waste disposal costs, and recycling some Fe and Zn-containing products.
Waste mainly comes from fine dust in dust collectors and dust mud generated in various production processes. In the process of waste recycling, dust-free treatment is required, and bonding forming, ball making, briquetting, brick making and other process methods are often used. A common production process of the above process treatment methods is the mixing of waste, that is, the mixing process. The mixing system must be able to carry out mixing, humidification, mixing, compaction, pre-balling, reaction, cooling and other processes at the same time. The above functions can be achieved by using a countercurrent high-power mixer. Mixed raw materials often contain some difficult-to-handle recycled materials, such as hard (sintered ore, coke), corrosive (chloride-containing materials), easily sparking (Fe-containing materials), easily reactive (quicklime), or highly viscous and easily agglomerated recycled materials.
1. Pelletizing of dust ash
In recent years, zinc recovery has become increasingly important in steel mills. With the increase in the use of surface hot-dip galvanized steel, the amount of zinc recycled to the steel mill for remelting has also increased significantly. There are two ways to treat zinc-containing waste: one is to treat the appearance only; the other is to process the recovered zinc into oxides.
At the Aalpine Steel Plant in Linz, Austria, the dust-containing exhaust gas from the converter is dedusted by the cooler and the next step of the electrostatic precipitator. The coarse dust from the cooler and the low-zinc fine dust from the electrostatic precipitator are heated in the rotary kiln and pressed into agglomerates on a continuous production line. The pressed agglomerates are directly returned to the converter for reuse.
The zinc-rich dust from the electrostatic precipitator is sent to another production line - the pelletizing system. Because this dust has a high iron content and quicklime content, and it is easy to generate sparks when the operating temperature reaches 150°C, the system is protected by nitrogen to prevent the iron from reacting. In order to eliminate the reaction enthalpy of slaked lime and other heat sources, the mixer is also used as a steam cooler. An improved disc feeder is installed between the mixer and the disc pelletizer as a reactor. Since the mixer is a batch intermittent non-continuous production, while the pelletizer is a continuous production, the disc feeder can be used as a buffer device between intermittent production and continuous production, and can also provide sufficient time for the complete reaction of slaked lime. Although dust is difficult to dissolve in water, a large amount of water is required for the mixing process. The amount of water added is automatically calculated by the process control system based on the detection data, and basically consists of the following parts: the amount of water used for CaO slaking (stoichiometric), the water used for consuming reaction heat, the water used for cooling hot dust, the water used for consuming high-temperature mixer mechanical energy, and the water used for humidification of dust pellets. The evaporation of water causes a large amount of dust-containing steam to be generated in the mixer, reactor, and pelletizer. These steams are purified in the purifier and recycled, and the sewage from the purifier is sent to the mixer for use. These waters circulate in a completely closed system and will not be discharged to the outside. Moreover, the water used in the entire process is new water added to the purifier. Since the lime-containing dust is very sticky after humidification, the mixer is generally equipped with an automatic cleaning device. The wet balls coming out of the pelletizer are dried on a belt dryer to facilitate storage. The finished balls have high mechanical strength, can maintain good stability in a humid environment, and are suitable for long-distance transportation.
2. Waelz rotary kiln process
In 1992, BUS built a modern eco-friendly zinc recovery plant on the site of the former steel plant in the Saxonia industrial zone in Freiburg, Germany. The plant uses a rotary kiln to convert zinc-containing industrial waste into eco-friendly and environmentally friendly oxides. The oxides are then converted into zinc in the zinc workshop. The raw materials that can be processed by the Waelz rotary kiln process include steelmaking workshop dust removal ash, sludge, waste pellets, wet coke, dry coke (petroleum coke, anthracite coke), flue gas desulfurization gypsum (wet), crushed dry gypsum, quicklime, slaked lime, etc. The dust in the steelmaking workshop is usually transported by special tank trucks and then stored in large-volume silos.
To improve the performance of the raw materials, a mixed pelletizing system was installed in 1997, which increased the furnace output by about 20%. Different reducing agents or binders are selected according to the zinc content of the waste, and then mixed, homogenized and humidified. The main equipment of the pelletizing system is a strong mixer for batch intermittent production and a cylinder pelletizer for continuous production.
Waelz rotary kiln No. 1 is slightly inclined, 43m long, 3.6m in diameter, and rotates about once per minute. The heating gas runs in the opposite direction to the mixed material (pellets), and the mixed material is heated and dried while slowly passing through the furnace. The metal oxides are reduced in the reaction zone at 1200°C, at which temperature zinc and cadmium are evaporated. Process ventilation reoxidizes the metals, which enter the gas washing system together with the waste gas, separate the metal oxides at the flat tube cooler and filter, and transport them to the silo for intermediate storage. The slag from the Waelz rotary kiln can be used for landfill or road construction. The patented Waelz kiln process (SDHL) uses the heat of reaction of iron oxides in the rotary kiln, which greatly reduces energy (gas and coke) consumption and increases oxide production by nearly 30%. This process does not produce wastewater and reduces CO2 emissions by 40% compared to ordinary processes that do not use the heat of reaction of iron oxides.
The first furnace was very successful, so in 2002, a second 50m long Waelz rotary kiln was built. This time, the production used a sintering process, which significantly increased the output, so no pelletizing cylinder was installed. The production line can achieve continuous production. The mixed sintering process uses an improved Eirch high-power mixer. The mixing tower design adopts a design structure that increases the output, which can provide sufficient raw materials for the rotary kiln with increased output. Therefore, an Eirch mixing system was installed in 2004 to mix and bond dust and sludge with coke and binder to form agglomerates.
Collaborative research with universities and research institutes has proved that iron-containing waste can be recycled through belt sintering machines. This can reduce the cost of waste disposal and recycle iron in the recycled materials, but it will make the permeability of the sintering material worse and increase the dust content in the exhaust gas of the sintering machine. In order to avoid the above situation, experimental research on dust sintering was carried out. In 1997, HKM (ThyssenKrupp Mannesmann) built a sintering pilot production line for dust recovery. The test results were very satisfactory, so the test continued for many years until it was converted to industrial production in 2001. A large number of tests were carried out using different types of mixers to study the performance of dust-bonded agglomerates and the adaptability of different systems for large-scale production in steelmaking workshops. The Eirich countercurrent intensive mixer and the single-axis tubular mixer with head cutter were compared. Practice has proved that the Eirich mixer has good performance. In 2002, HKM's new production line was put into operation. The raw materials that can be processed include blast furnace top gas dust (fine and wet), dust in the dust removal chamber (coarse and hard), dust in the cooling process of the sintering plant (crushing and screening process), dust in the foundry (dry and fine), binder (lime, cement, etc.), and water. These materials are automatically stored, transported, batched, weighed, and fed into the batching mixer. The bonded agglomerates mixed by the mixer are poured into the box feeder and then continuously added to the sintering machine trolley.
After a long period of production, the equipment accessories and bonding system of the recovery system have been optimized, and the production results are more controllable. The dust agglomerates improve the permeability of the sintering mixture, increase the sintering output, and reduce the dust content in the exhaust gas of the sintering system. The copper-containing particles in the dust removal chamber are added to the dust agglomerates, which reduces the copper content in the exhaust gas and its catalytic effect on the formation of dioxins.
3. Primus process
After the successful pilot production of the Primus process, the first industrial production line was built and put into operation in 2003. The main equipment of the Primus process is a multi-hearth furnace and an electric furnace. The electric furnace converts pre-reduced iron into pig iron. In addition, the plant is equipped with exhaust gas detection devices to ensure its minimum emissions.
The Primus process uses iron ore powder to produce sponge iron (DRI) and molten iron. It is an ecological and environmentally friendly new process and can also be regarded as a miniature blast furnace. The purpose of recycling waste in steel production is to recover iron, zinc and other valuable metals. The new process uses multi-hearth furnace technology for direct reduction and is suitable for low-grade coal. The plant is designed to recycle all waste from Luxembourg Steel, including electric furnace dust and oily dust and mud from the rolling workshop. Dust and dust and mud from blast furnaces and other steelmaking workshops can also be processed.
In the mixer, different wastes and binders are mixed, weighed and processed separately. According to the measurement of the moisture content of the mixed raw materials in the mixer, the base material can be directly compensated for different moisture contents during the mixing process. The next step after mixing is pelletizing, where the mixture is pelletized in a pelletizing cylinder for a long time and then dried.
The multi-chamber furnace is a set of equipment with simple process, short process and reliable production. It consists of several furnace beds stacked one on top of the other. There is a mixing arm working on each layer, which is driven by a cooled rotating cylindrical shaft. The raw materials are loaded with coal, and the coal flows from the top to the bottom of the furnace. The mixing arm drives them to move from the outside to the inside on one layer and from the center to the outside on the next layer. The air enters from the side of the furnace and exits from the top.
The waste is dried and reduced in the furnace. The whole process goes through the following steps: first drying at about 100°C, degreasing at about 400°C, and reducing at about 1100°C.
The reducing atmosphere is dominant on the material bed, and the air flow is oxidizing. This causes the zinc to be re-oxidized in the air flow and separated in the exhaust gas cleaner, so it is also called Primus oxidation. The sponge iron discharged from the furnace bottom is continuously loaded into the Primus melting furnace, a special three-stage electric arc furnace, which continuously produces molten iron and slag. Compared with blast furnace slag, this slag is less reactive and can be used for paving roads.
4. OxyCup process
In the summer of 2004, the OxyCup process production line built by ThyssenKrupp Steel (TKS) in Duisburg, Germany was put into operation. TKS has three sintering plants, four blast furnaces and two steelmaking plants. Using this technology, the plant can recycle the waste from all these plants and recycle iron-containing products. The entire project was designed and constructed by a German company, which also provided the core equipment - the vertical furnace. Before TKS decided to build a new plant, it had cooperated with some companies to successfully conduct pilot tests for many years using improved cupola furnaces. This process is to make bricks from iron- and carbon-containing waste, which are reduced to DRI in the furnace and then melted into pig iron. This process can also process zinc-containing dust that cannot be recycled on ordinary production lines. The raw materials that can be processed include sintering machine dust, blast furnace sludge, converter dust, rolling mill sludge, and coke slag. After being cooled, conveyed, and sorted in the preparation workshop, these wastes are sent to a specific high-power mixer for mixing, and a binder is added to mix them into the appearance of concrete. They are then sent to the 110mm hexagonal brick production line to produce paving bricks. Bricks made from raw materials containing 50% iron can be melted directly after hardening for about three days, or they can be stored for later use.
For the unified disposal of waste and the stability of the bricks produced, the mixing process in the raw material preparation is the most important. Different types of sludge need to be decomposed and crushed and then evenly mixed with fine dust. After a large-scale series of multiple tests, TKS decided to use the Eirich countercurrent high-power mixer, which can not only crush the sludge, but also accurately control the distribution range and amount of binders and moisture. These two properties are prerequisites in the brickmaking process, which can ensure the optimization of feeding during the pressing process of brickmaking and make the bricks have the right hardness.
The reaction speed in the furnace is very fast due to the small particles of recycled waste, large reaction area and high temperature. Since all bricks are of the same size, there are many more favorable cavities in the vertical furnace than in the blast furnace. As the bricks descend, they are reduced to DRI and then enter the melting zone, where the iron slag is separated and flows out continuously. The zinc in the waste is evaporated and comes out of the furnace top together with the waste gas, and the zinc-rich sludge collected at the filter can be used to recover zinc. The OxyCup process is versatile and adaptable, and can process a wide range of waste raw materials. Its raw material preparation workshop can flexibly provide raw materials according to the design and layout of the brick production line, and can also perform continuous processing.
The Waelz process is the main industrial technology for recovering zinc from zinc-containing materials, and its history can be traced back to the late 19th century. The evolution of this technology has not only promoted the development of the zinc recovery industry, but also occupied an important position in the modern circular economy. The following will provide a detailed introduction to its historical background, technical principles and development trends.
1. Technical origin and early development
The concept of using rotary kilns to recover zinc by volatilization can be traced back to 1888. In 1910, American inventor Edward Dedolph applied for a patent for this process, but the early version did not form an industrial-scale production process. Subsequently, the German companies Metallgesellschaft and Chemische Fabrik Griesheim-Elektron worked together to improve Dedolph's patent. However, it was Krupp Grusonwerk that truly laid the foundation for the modern Waelz process, which independently developed and named the "Waelz process" in 1923. "Waelz" comes from the German word "Waelzen", which refers to the rotational movement of the material in the kiln.
2. Technical principle and operation process
The core of the Waelz process is to use a rotary kiln to treat zinc-containing materials at high temperatures (1000°C to 1500°C). In this process, zinc exists in the form of zinc oxide, zinc silicate, zinc ferrite or zinc sulfide, and a carbon-containing reducing agent (such as coke) and a flux are added to promote the chemical reaction. The typical dimensions of a rotary kiln are about 50~60 meters long and 3.6~4.5 meters in diameter, and the rotation speed is 1 revolution per minute.
The chemical mechanism of the process is the reduction of zinc compounds to metallic zinc (boiling point 907°C), which then volatilizes in the gas phase and is oxidized to zinc oxide. The zinc oxide particles are collected from the exhaust gas by equipment such as electrostatic precipitators, filters or settling chambers.
3. Products of the rotary kiln include:
Waelz oxide (WOX): rich in zinc oxide (typically 65% zinc content), an important raw material for zinc smelters.
Waelz slag: an iron-containing byproduct that can be used in building materials and other applications, but its iron recovery rate is low.
In addition, the Waelz process can also recover low-boiling-point metals such as lead, cadmium and silver, while capturing halogen compounds in the byproducts.
4. Technical advantages and limitations
With the widespread use of galvanized steel, the zinc content in scrap steel has continued to increase, making electric arc furnace dust (EAFD) an important raw material for zinc recovery. By 2000, the Waelz process was recognized by the European IPPC Bureau and the US EPA as the "Best Available Technology" (BAT) for EAFD zinc recovery and is used on an industrial scale worldwide. As of 2014, 90% of electric arc furnace dust zinc recovery uses the Waelz process.
Although the Waelz process has high energy consumption and low iron recovery rate, its reliability and efficiency make it still the mainstream method of zinc recovery. In recent years, improvements in energy consumption and efficiency, including optimization of kiln design and introduction of new reducing agents, have further improved the environmental protection and economic performance of the process.
5. Technical improvements and alternative processes
Based on the Waelz process, some alternative or improved zinc recovery technologies have emerged, including the follwing as we have dicussed in the previous faq.
SDHL process: improving the Waelz process by improving efficiency.
DK process: combining blast furnace technology to produce pig iron and zinc oxide dust from a variety of waste materials.
PRIMUS process: using a multi-stage zinc volatilization furnace to improve recovery efficiency.
In addition, the rotary kiln technology developed by Nippon Steel has been applied in Japan, further expanding the scenario of zinc recovery.
6. Future prospects
With the global emphasis on resource recycling and carbon emission control, the Waelz process will continue to be improved in the following aspects:
Energy efficiency improvement: reducing energy consumption through clean energy and heat recovery technology.
Waste gas treatment upgrade: further reduce the emission of dioxins, heavy metals and halogen compounds.
Intelligent operation: introduce automation and data analysis technology to achieve more sophisticated kiln control.
7. Conclusion
As a century-old technology, the Waelz process has demonstrated its continued vitality in the field of zinc recycling. Through continuous innovation and optimization, this process not only meets the needs of industrial waste treatment, but also promotes the realization of the circular economy and provides strong support for the future green industry.
The core of Waelz technology is to use coke to reduce metal oxides such as zinc, lead, cadmium, etc. in a rotary kiln. The technology was first used to refine low-grade zinc ore, then to refine metallic zinc from zinc slag, and has been successfully used for dust treatment in electric furnaces over the past 30 years. The technology can be used in both the steel industry and the zinc smelting industry.
Metallic zinc is increasingly used. Zinc can be used as a surface coating for steel products. A large amount of statistical data shows that the proportion of scrap steel with a galvanized layer in the scrap steel raw materials of electric furnaces is increasing. Therefore, the zinc content in electric furnace dust is also increasing.
The European Community Environmental Protection Law stipulates that dust discharged from electric furnaces is harmful. Other countries in the world have also begun to stipulate that it is a harmful substance.
2. Application Status of Waelz Technology
At present, the zinc industry and steel industry in many countries in the world are not closely connected. Steel mills only consider how to galvanize their steel products, and do not consider that the zinc metal of the zinc coating on the scrap steel during the electric furnace smelting process is discharged in the form of dust. Zinc smelters also do not attach importance to recovering zinc metal from the electric furnace dust of steel mills. In fact, the zinc content in electric furnace dust is about 20%, which is higher than that of low-grade zinc ore. In this context, on the one hand, zinc is wasted, and on the other hand, zinc prices rise. Therefore, it is necessary for zinc smelters to cooperate with steel mills to collect the dust discharged by steel mills and send it to zinc smelters for treatment. So that both parties benefit.
The world average electric furnace dust treatment ratio is 40%. The zinc content in European dust is 39%, and the dust utilization rate is 81%; the zinc content in American dust is 20%, and the dust utilization rate is 75%; the zinc content in Asian dust is 21%, and the dust utilization rate is 35%; the zinc content in other countries is 20%, and the dust utilization rate is 5%. World Electric Furnace Production, Dust Emission, Dust Treatment, Waelz Treatment, RHF Treatment
3. Dust recovery technology
There are many application technologies for electric furnace dust recovery, mainly Waelz technology (accounting for more than 80% of electric furnace dust recovery), high temperature smelting method and wet smelting method. Among them, high temperature smelting method includes: rotary hearth furnace, multifunctional rotary hearth furnace, zinc smelting vertical furnace, cyclone dust collector, plasma heating furnace, electric heating furnace. Wet smelting method includes: ammonium chloride leaching method, sulfuric acid leaching method, sodium hydroxide leaching method.
Advantages of using Waelz technology to recycle electric furnace dust:
(1) Mature and reliable technology. Waelz technology is widely used in actual production, and the technology is mature and reliable.
(2) Simple equipment installation.
(3) Outstanding economic benefits. The recovered zinc oxide can be used in all zinc smelters, and the slag after smelting can be used for paving.
(4) Meet environmental protection requirements. When this technology is used for industrial production, its exhaust emissions fully meet the requirements of European environmental protection standards.
(5) Flexibility in use. After changing the process, various dust treatments can be carried out.
(6) Low energy consumption. The coke required to process 1 ton of electric furnace dust is less than 200 kg.
Some other processes for recycling electric furnace dust are still in the project research and semi-industrial experimental stage (the production cost is high, including smelting cyclone dust collector, vertical furnace, plasma heating furnace, and electric heating method). Other processes are not suitable for electric furnaces, but are suitable for stainless steel and AOD dust treatment.
4. Waelz technology
A set of Waelz process equipment consists of 2 to 3 units. One unit is the raw material preparation unit, and the other unit is the Waelz process production line and the final washing equipment. In the raw material preparation unit, the main task is to prepare solid raw materials and ensure that the solid raw materials are stably and evenly transported to the Waelz kiln. Solid materials refer to zinc-containing electric furnace dust, coke powder reducing agent and slag-forming agent or limestone (used in general smelting processes).
After the solid raw materials enter the Waelz process production line, they will form metal oxide products and slag after the entire process. Slag can be used as paving material, and the zinc content in the metal oxide is 54% to 60%. Its zinc oxide can be sold directly to zinc smelters or other chemical plants. Some plants also install auxiliary washing equipment for dechlorination and defluorination.
The purpose of the raw material preparation unit is to homogenize different raw materials, especially different electric furnace dust, and then mix the dust with coke and quicklime with 10% water in a strong mixing device to form pellets. This process is called self-reducing pellets (SRP). This type of pellets must be temporarily stored for a period of time for maturation. Electric furnace dust particles are very fine, so they are usually transported in closed tank trucks. Limestone and coke can be transported by dump trucks.
The Waelz process production line consists of a solid raw material batching and feeding system, a Waelz rotary hearth furnace, a slag granulation system and an exhaust gas treatment system. In the batching system, different solid raw materials such as self-reducing pellets, coke, slag forming agents, etc. are delivered to the Waelz process equipment in proportion via a belt. The Waelz rotary kiln is operated in reverse, that is, the solid material is first fed from the rotary kiln feeding port. The rotary kiln rotates at a speed of 1 turn per minute, with an inclination of 2% to 3%, and air is sucked from the slag outlet. The added solid material is first dried and then heated until the reaction begins. The maximum temperature of the solid material can reach 1200°C. The reduction reaction after the addition of the material is endothermic. CO gas and zinc-containing dust can generate heat by oxidation to meet the heat required for the reaction.
According to the conventional process operation, the Waelz production line does not need additional heat, and the production process itself generates heat. The air enters the rotary kiln at room temperature, and the gas exits the kiln at a temperature of 700-800℃.
The washing workshop is mainly used for dechlorination and defluorination of oxide raw materials, and its production process is at least two-stage washing. The chlorine content of the washed oxide raw materials is less than 0.1%, and the fluorine content is less than 0.15%. The discharged washing liquid contains Na, K, Cl, F, SO4, etc. These washing liquids need to be further treated or evaporated for crystallization.
The economic benefits of using Waelz equipment mainly depend on the size of its production scale. There are different models, which are suitable for electric furnace steel plants with a production scale of 35,000 to 160,000 tons/year. The diameter of the rotary kiln is 2600 to 4500 mm, and the length of the furnace is 35 to 75 meters.
Usually, the recovery rate of zinc is 92% to 96%. The material consumption of the equipment for processing 1 ton of electric furnace dust is: 180 to 250 kg of coke, 100 to 250 kg of sand (acid slag), 40 to 70 kg of limestone, 150 to 300 kWh of electricity, and 0.5 to 2.0 m3 of water.
According to a dust treatment plant with an annual output of 80,000 tons, it requires an investment of approximately US$16 million, including a full set of material preparation, gas purification equipment, dioxin treatment equipment and major infrastructure. If washing equipment is required, an additional investment of 4 million US dollars is required. If evaporation crystallization equipment is required, an additional investment of 6.4 million US dollars is required.
The production cost varies with the output, generally about 75-135 US dollars/t, which does not include enterprise management fees and annual depreciation (about 10% of the total cost). In addition, it does not include profits and taxes.
The sales cost of products treated with electric furnace dust in Europe is about 30-50 US dollars/t. The main income comes from Waelz oxide and as a secondary raw material for zinc smelting. The product price is affected by the zinc content of the product and the zinc metal price of the London Metal Exchange.
The average price of LME zinc in 2006 was about 3,000 US dollars/t. Therefore, the production cost of dust treatment at the Waelz plant is 165 US dollars/t, the sales profit is 292 US dollars/t, and the net profit is 128 US dollars/t. If the dust is washed, the net profit per ton of dust can be increased by more than 30 US dollars.
1. After mixing zinc-containing solid waste and fuel, they enter the rotary kiln for volatilization and reduction. After cooling, the flue gas is collected by bag dust collectors to collect secondary zinc oxide. The gas after dust collection enters the waste gas treatment facility for treatment and meets the emission standards. The slag is quenched by water to become water-quenched slag. The water-quenched slag that meets the requirements for returning to the furnace is directly returned to sintering or blast furnace ironmaking. The waste slag that does not meet the requirements for returning to the furnace is processed for resource recovery.
2. The length, speed, filling rate, material residence time, flue gas volume and other parameters of each temperature section (drying section, preheating section, high temperature section, cooling section) of the rotary kiln should be reasonably determined according to the difference in raw materials to prevent the rotary kiln from caking.
3. The temperature of the high temperature section of the rotary kiln should reach 1100~1300℃, and the temperature of the cooling section should be controlled at around 900~1000℃ to control the ringing of the rotary kiln.
4. The blast process should be adopted, and enterprises with conditions are encouraged to operate with oxygen enrichment. The oxygen content in the kiln should be controlled within 23%.
5. The outer diameter of the newly built rotary kiln should be more than 3.5m, and the actual production capacity of a single line shall not be less than 60,000 tons/year.
6. The operation status of the rotary kiln should be reasonably controlled, the kiln washing cycle should be controlled to more than 25~30 days, and the continuous stable operation time without stopping the kiln should reach more than 5760 hours.
7. When the flue gas temperature is greater than 550℃, the rotary kiln system should be equipped with a waste heat boiler, and the waste heat utilization rate should reach more than 65%; when the flue gas temperature is below 550℃, enterprises are encouraged to utilize waste heat.
8. The bag dust collection efficiency should reach more than 99.9%, and the collected secondary zinc oxide should meet the requirements of YS/T1343. The flue gas after dust removal should be discharged after waste gas treatment.
9. Different zinc recovery rate requirements should be met according to the different zinc content in the raw materials: when the zinc content in the raw materials is above 8%, the zinc recovery rate is ≥92%; when the zinc content in the raw materials is 3%~8%, the zinc recovery rate is ≥90%; when the zinc content in the raw materials is below 3%, the zinc recovery rate is ≥80%.
10. When the water-quenched slag produced by the rotary kiln meets the requirements of iron content>55%, Zn<1%, and alkali metal≤1.2%, it is suitable to be returned to the steel plant for sintering and blast furnace ironmaking for use as ingredients or iron magnetic selection to improve the iron grade for utilization; if the above requirements are not met, it should be used as a resource.
11. The wastewater generated during the cooling process of the rotary kiln should be fully recycled.
The main raw materials of zinc bypoxide and zinc series products in the early stage come from lead-zinc ore and oxide ore. The development of zinc oxide in my country was relatively large in the early stage, and the production of zinc oxide series could not meet the needs of my country. With the decreasing mineral resources in my country, the supply of zinc oxide and zinc series products has become increasingly tight, and the price has been rising. The price of zinc oxide with a content of 60% has increased from 600-700 yuan/ton in the 1980s to 8600-9800 yuan/ton at present. The supply is in short supply and the market prospect is very promising.
1. This project uses the waste slag and ore dressing tailings of steel enterprises as raw materials, and uses the smelting waste slag to recover waste non-ferrous metals and produce sintering materials. The iron material project uses these smelting waste slags containing low-grade zinc metal, and adopts tempering method to enrich and process them to produce low-grade zinc oxide and ferrosilicon sintering materials. The iron slag can be magnetically separated and used as raw materials for cement production. This not only treats the waste slag, saves resources, but also brings economic benefits to the enterprise. Therefore, the project is a good recycling project of resource recycling.
2. Source of raw materials: If the surrounding area has a relatively developed steel industry, the electric furnace ash, ironmaking sludge, steelmaking converter dust removal ash and surrounding small ironmaking blast furnace dust removal ash plus lead, zinc and silver ore dressing tailings can be used to meet production needs.
3. The zinc charge and coking coal are crushed into particles smaller than 40 mesh, and the zinc charge and coking coal or anthracite are mixed and stirred at a ratio of 1:0.30-0.35 to obtain a mixture, and then the mixture is made into a granular mixture with an effective diameter of 8-15 mm, and finally the granular mixture is transported to the feed inlet of the rotary kiln, i.e. the kiln tail, by a conveyor for smelting. Because the rotary kiln has a certain rotation speed and the kiln body has a 4% inclination, the raw materials in the kiln body are constantly turned toward the kiln head. The overall kiln length is 43 meters. The drying zone from the feed inlet to 10 meters is 200℃-400℃, the combustion zone from 10 meters to 20 meters is 700℃-900℃, and the high-temperature melting and sintering zone from 20 meters to 40 meters is 1100℃-1300℃. This section is also the zinc oxidation zone, and zinc vapor is generated. The air flow generated by the induced draft fan at the end of the kiln and the blower at the head of the kiln brings the zinc vapor and other gases into the cooling box and into the cooling pipe to form solid powder. The powder is sucked into the built-in bag dust collector through the induced draft fan and then packaged to produce secondary zinc oxide products. The annual output of secondary zinc oxide is about 7,000 tons, and the energy consumption is 150 kilowatt-hours. When the zinc oxide ore or zinc-containing industrial slag with a zinc content of 15% to 25% is used to smelt zinc oxide, it has the advantages of greatly saving coke or coal; the product quality obtained by smelting is good, the productivity is improved, and the amount of nodules is small.
1. Ignition operation: During the startup process of the zinc oxide rotary kiln, whether it is newly built or restarted after maintenance, ignition is one of the key operations. Before ignition, the entire calcination system should be tested in conjunction to avoid problems such as high system temperature, blockage of the cyclone or feed pipe due to equipment failure after feeding. Firewood or diesel can be used for ignition. The operation steps are as follows:
(1) Ensure that the high-temperature fan damper is completely closed, and open the ignition chimney appropriately according to the situation to keep the kiln head in a slightly negative pressure state to avoid excessive drafts that cause ignition difficulties.
(2) When spraying coal powder, the coal powder burnout rate should be controlled. Do not spray too much coal powder in the initial stage. The amount of coal should be gradually increased, and the kiln body should be rotated 1/4 of a circle at a certain interval each time to prevent the barrel from bending and deforming due to uneven heating.
(3) When the temperature reaches above 700℃, the auxiliary transmission is required to continuously rotate the kiln, and the high-temperature fan is started according to the situation and the damper opening is adjusted; after the temperature reaches 900℃, the main transmission rotary kiln can be used instead.
If diesel is used for ignition, the oil pump valve opening should be carefully adjusted to ensure that the oil supply is gradually stopped after the material enters the burning zone.
(4) When feeding, the timing of feeding should be determined according to the temperature of the kiln tail and the preheater outlet. The initial feeding amount should be high and should not be less than 60% of the designed output, and the feeding amount should be gradually increased. The low feeding amount operation time should be shortened as much as possible to avoid the preheater system from being blocked due to material collapse.
2. How to form a kiln coating inside the kiln?
After replacing the refractory bricks (especially the firing zone), proper kiln drying operation is required to prevent the temperature from rising too fast. The kiln skin has certain requirements for the raw material composition.
The amount of liquid phase and the refractoriness of the material will directly affect the quality of the kiln skin: more liquid phase: easy to form the kiln skin, but the kiln skin is not firm and easy to collapse. Less liquid phase: high refractoriness, the kiln skin is difficult to form, but once formed, it is relatively firm.
It is generally recommended to use the raw material powder during normal production for kiln skin hanging, which helps to form a stable kiln skin. Raw material burning and under-burning should be avoided during the kiln skin hanging.
3. Handling of unstable incoming materials
During the production process, the raw material feed rate of the zinc oxide rotary kiln may fluctuate, especially when the equipment fails or the moisture content of the raw materials is difficult to control during the rainy season, the fluctuation will be aggravated. Operators need to observe and adjust frequently to ensure timely handling and reduce adverse effects on the system.
Less incoming materials: Do not extend the coal injection pipe too deep to avoid elongated flames and excessive exhaust air causing a sharp rise in temperature. Properly withdraw the coal injection pipe, reduce exhaust air and coal injection, control the temperature at the kiln tail and the cyclone temperature, use short flame rapid burning method, and wait for the arrival of materials.
More incoming materials: You can appropriately reduce the kiln speed, reduce the feed amount, increase exhaust air, extend the coal injection pipe, increase the temperature at the kiln tail, and enhance the pre-burning effect. Avoid adding too much coal during operation to prevent the reducing atmosphere from causing the temperature in the kiln to drop, resulting in worsening of the working conditions.
4. Formation and treatment of flying sand
The main reasons for the formation of flying sand include: improper raw material ratio, resulting in insufficient liquid phase;
Use of inappropriate correction raw materials (such as high silica ash) to reduce costs; low cooling system efficiency.
Treatment measures: Appropriately adjust the position of the coal injection pipe, reduce the exhaust volume, reduce the temperature at the kiln tail, reduce the pre-burning effect of the material, and try to form the liquid phase in the burning zone. Avoid excessive exhaust during operation, otherwise it will easily aggravate the problem of flying sand.
5. Causes and treatment of balling in the kiln
The main causes of balling include fluctuations in raw material composition, unstable feeding, high harmful components, and uneven fuel quality.
Preventive measures: Stabilize the raw material ratio. It is recommended to use raw material formulas with high lime saturation coefficient, high silicon rate, and medium aluminum rate. Select raw materials and fuels with low harmful components to ensure uniform coal fineness and avoid incomplete combustion.
Treatment measures: Small balls can be burned at high temperature by adjusting the ventilation and combustion control in the kiln, rolling the balls into the burning zone. Large balls can be treated by alternating hot and cold methods to gradually burn the balls, but it is necessary to prevent large balls from entering the cooler and causing damage.
6. Treatment of ring formation
Ring formation can be divided into front ring formation and rear ring formation.
Front ring formation: When the impact is not great, the flame shape can be adjusted through the coal injection pipe to gradually burn it off. If the impact is serious, it is necessary to concentrate the firepower to burn the ring, adjust the ventilation, and ensure the smooth flow of the system.
Rear ring formation: Use the hot and cold alternating method to gradually reduce the ring formation temperature to make it fall off. Pay attention to controlling the temperature at the kiln tail during treatment to avoid new blockage problems caused by material collapse.
1. Equipment optimization and maintenance
(1) Reasonable selection and design: According to the production scale and demand, select the appropriate cylinder length, diameter and inclination. Long cylinders have large storage capacity and strong calcination capacity, large diameter cylinders have fast feeding and discharging, and appropriate inclination can speed up the material movement speed, but care should be taken to avoid excessive material flow rate leading to incomplete reaction.
(2) Select high-efficiency burners: Replace single-channel burners with multi-channel burners to ensure that the pulverized coal is fully burned and the temperature in the kiln is reasonably distributed, effectively shortening the time required for combustion and increasing the output of the zinc oxide rotary kiln.
(3) Regular maintenance: Develop a detailed equipment maintenance plan, conduct comprehensive inspection and maintenance of the rotary kiln at the prescribed time intervals, and replace severely worn parts such as support wheels, rollers, kiln linings, etc. in a timely manner to keep the equipment in good condition and reduce energy loss and downtime.
2. Process improvement and control
(1) Material pretreatment and feed control: Before the materials enter the rotary kiln, they are fully crushed, screened and mixed to ensure that the material particle size is uniform and the composition is stable, which is conducive to improving the reaction efficiency and product quality. At the same time, the materials can be preheated to reduce the demand for external heat sources and improve thermal efficiency. In addition, the feed speed should be reasonably controlled to avoid the feed speed being too fast, resulting in insufficient residence time of the materials in the kiln and inability to fully react, or the feed speed being too slow, resulting in material accumulation and affecting the heat transfer effect.
(2) Accurate temperature control: Install advanced temperature monitoring and control systems to monitor the temperature in the kiln in real time and accurately, and automatically adjust it as needed. Appropriately increasing the calcination temperature can accelerate the formation reaction of zinc oxide, but it must be ensured that it does not exceed the melting point of the material or cause unnecessary side reactions. Generally, the calcination temperature of zinc oxide is between 900°C and 1200°C, and the specific temperature should be adjusted according to the characteristics of the raw materials and
Product requirements.
(1) Atmosphere optimization control: By reasonably adjusting the ratio of air to coal powder, the oxygen concentration is controlled within an appropriate range to avoid excessive oxygen concentration leading to excessive combustion of coal powder, generating too much heat, causing equipment overheating and increased energy consumption, or too low oxygen concentration leading to incomplete combustion of coal powder, affecting the generation of zinc oxide. At the same time, maintain an appropriate amount of water vapor and appropriate redox conditions as needed to promote the roasting reaction and improve the purity and yield of zinc oxide.
(2) Rotation speed control: Select the appropriate rotation speed according to the specific situation to ensure the uniformity and high yield of zinc oxide roasting. Too high or too low rotation speed will have an adverse effect on the roasting effect of zinc oxide. Under the condition of meeting production requirements, the rotation rate of the kiln can be appropriately increased, which is conducive to shortening the calcination time of the material and increasing the output of the rotary kiln equipment.
3. Energy recovery and utilization
(1) Install a waste heat recovery system: The high-temperature exhaust gas discharged from the rotary kiln carries a large amount of heat energy. The heat energy in the exhaust gas can be recovered and utilized through the waste heat recovery system, such as for preheating materials, heating water or generating steam, etc., to improve energy utilization and reduce production costs.
(2) Optimize the waste heat utilization process: Rationally allocate and utilize the heat energy after waste heat recovery. According to the requirements of the production process, the waste heat is preferentially used in the links with higher temperature requirements, such as drying and preheating of materials, so as to give full play to the value of waste heat.
Tongli Heavy Machinery uses advanced Waelz kiln technology to carry out zinc oxide recycling. This technology is quite mature and can effectively process most of the world's recycled zinc waste. Zinc-containing wastes such as electric arc furnace (EAF) dust, induction furnace (IF) dust, zinc slag and zinc concentrate can all be reused under this process. After a long period of practice and improvement, the tongli Waelz kiln process has become a reliable, energy-saving and practical method in the field of zinc-containing materials and residues.
1. The necessity of zinc oxide recycling
In the past, zinc-containing dust and sludge were mostly directly landfilled. This simple and crude treatment method caused a large amount of resources to be lost in vain. Fortunately, in recent years, tongli researchers have worked tirelessly to develop a series of extraction processes to recover valuable metals from these waste materials, which has greatly improved the waste of resources. Take the steel industry as an example. EAF dust is generated about 10 million tons per year, of which zinc content is about 2 million tons. Recycling these dusts can not only recycle zinc resources, but also reduce environmental pollution and protect the ecological environment.
2. How Waelz rotary kiln technology works
The key to Waelz kiln technology lies in the rotary kiln system. During operation, zinc-containing residues start the reduction process against carbon carriers. The kiln slowly rotates and the materials are slowly heated to about 1200°C. Under this high temperature, zinc and lead will sublime and then re-oxidize.
The metals are then transported to the downstream gas purification system for effective separation. During this period, the addition of lime to form slag plays an auxiliary role. The combination of the two plays an effective system for extracting zinc oxide from waste materials.
Before the materials enter the Waelz kiln, raw materials such as EAF dust and sludge, which contain about 74% zinc by weight, must first be homogenized and granulated. The granulation step is critical. It makes the materials easier to transport, store and subsequently use, making the entire recycling process smoother. The processed pellets can then be more easily reintegrated into the metallurgical process, ensuring that the recycling work is carried out smoothly and efficiently.
3. Tongli Waelz kiln process details
(1) Material transportation: Electric arc furnace steel dust is transported by road or rail to the zinc oxide recycling plant.
(2) Material preparation: The incoming raw materials are in different forms, some are dry, some are compact and moist, and some are granular. Dry dust is stored in silos, while moist materials, coarse flux and coke are placed in special boxes waiting for the next step.
(3) Kiln processing: Waelz kilns are usually 55 meters long and 4 meters in diameter, slightly inclined, and rotate at a speed of about 1.0 rpm. As the material moves forward in the kiln, it is fully exposed to the counter-flowing kiln gas and is dried and preheated.
(4) Reduction zone: When the temperature rises to about 1200°C, the reduction reaction of the metal oxide occurs, and the zinc becomes gaseous and enters the gas cleaning system. Afterwards, the zinc is oxidized again in the kiln air using excess air.
(5) Waste gas treatment: Chlorine, alkali and heavy metals are volatilized, and the dusty waste gas enters the downstream system for treatment. Coarse particles are separated in the dust removal chamber and sent back to the kiln. The hot waste gas is cooled and the Waelz zinc oxide is separated by a high-efficiency collector.
(6) By-product management: Waelz iron product (WIP) is a by-product that has its uses in road and civil engineering, cement manufacturing and other fields. It can also be further processed to increase the iron content.
Environmental compliance: The purified waste gas is clean and dust-free, strictly meeting environmental standards, ensuring that the entire recycling process is both sustainable and compliant.
(7) Final product: After a series of processes, the main product of zinc oxide recovery - Waelz zinc oxide is produced and transported to the zinc smelter for further processing into pure zinc.
4. The advantages of tongli Waelz kiln technology in zinc oxide recycling
Over the past 80 years, Waelz kiln technology has been developing and improving. Tongli Heavy Machinery has achieved many outstanding results in cooperation with BEFESA, creating an efficient and environmentally friendly zinc recycling system. With good energy efficiency and low environmental impact, this technology can well meet the increasingly stringent environmental regulations around the world and is highly recognized in the industry.
Zinc oxide rotary kiln waste residue refers to zinc-containing solid waste produced in the zinc oxide production process, which usually has the characteristics of high temperature, high alkali, and high zinc content. Traditional waste treatment methods often cause environmental pollution and waste of resources, so it is necessary to scientifically treat and utilize zinc oxide rotary kiln waste residue.
1. Metal recovery
(1) Deep recovery of zinc The waste residue after the incineration of electric furnace ash may still contain a certain amount of zinc. Since zinc may exist in different compound forms during high temperature, such as zinc-iron spinel, a more complex leaching process can be used to recover zinc, such as alkaline leaching. Under alkaline conditions (such as using sodium hydroxide solution), zinc can be dissolved in the form of zincate and better separated from other impurities (such as iron) in the waste residue. Then zinc is recovered from the leaching solution by electrolysis and other methods to obtain a high-purity zinc product.
(2) Recovery of other valuable metals
In addition to zinc, electric furnace ash waste residue may also contain valuable metals such as lead and tin. For the recovery of lead, its characteristic of forming a soluble complex under specific conditions (such as in ammonium chloride-ammonia solution) can be used to leach lead, and then lead metal can be obtained by precipitation, replacement and other methods. For tin, acid leaching (such as using hydrochloric acid) can be used, and then it can be recovered by extraction, electrolysis and other processes.
2. Application of building materials
(1)As auxiliary cementitious materials: Electric furnace ash waste slag after proper treatment can be used as auxiliary cementitious materials in cement-based materials. Because it contains some active ingredients, such as calcium oxide, zinc oxide, etc., it can participate in the reaction during cement hydration. After grinding the waste slag, mixing it with cement in a certain proportion (such as 5% - 10%) can improve the workability and later strength development of cement paste. Studies have shown that certain components in the waste slag can fill the pores between cement hydration products and improve the density of cement-based materials.
(2)For the production of new building materials, waste slag can be compounded with other materials (such as fiber materials, polymers, etc.) to produce new building materials. For example, waste slag is mixed with glass fiber and made into fiber-reinforced composite material plates through processes such as hot pressing. This plate has good strength and corrosion resistance and can be used in fields such as interior and exterior wall decoration of buildings.
3. Harmless treatment
(1) Heavy metal stabilization treatment: Heavy metals (such as cadmium, mercury, etc.) in electric furnace ash waste need to be stabilized. The phosphate stabilization method can be used to add phosphate (such as calcium dihydrogen phosphate, etc.) to the waste to make the heavy metals react with phosphate to form insoluble phosphate compounds. For example, cadmium ions will combine with phosphate ions to form cadmium phosphate precipitation, thereby reducing the bioavailability and mobility of cadmium.
(2) Treatment of organic pollutants: If the electric furnace ash contains organic pollutants before incineration, the waste after incineration may have a small amount of organic harmful components. Bioremediation methods can be used, such as using specific microbial flora to decompose organic pollutants into harmless substances such as carbon dioxide and water under suitable environmental conditions (such as suitable temperature, humidity and nutrient supply). Microorganisms can degrade organic pollutants by secreting enzymes. For example, some bacteria can secrete oxidases to decompose organic pollutants such as polycyclic aromatic hydrocarbons.
The zinc leaching slag treatment process is an important part of the hydrometallurgical zinc smelting process. Its purpose is to recover the valuable metals in the zinc leaching slag and prevent the slag discharged during the smelting process from polluting the environment. There are many methods for zinc leaching slag treatment, mainly including two categories: pyrometallurgy and hydrometallurgy. Each method has its own unique process principle, characteristics and applicable conditions.
Typical methods for pyrometallurgical treatment of zinc leaching slag include rotary kiln volatilization method (also known as Wiltz method), vortex furnace smelting method and fuming furnace smelting method. The rotary kiln volatilization method is to add a certain amount of coke powder to the dry zinc leaching slag and add it to the rotary kiln to achieve the reduction volatilization of zinc in the slag at high temperature, and then recover it in the form of zinc oxide powder. The volatilization rate of zinc in this method can reach 90% to 95%, and valuable metals such as lead, cadmium, indium, germanium, and gallium can be recovered at the same time. However, the process flow of the rotary kiln volatilization method is long, the equipment maintenance is large, the investment is high, and the working environment is poor, requiring a large amount of coal or metallurgical coke. In addition, the removal of fluorine and chlorine should be considered before zinc oxide powder enters the leaching process, and the kiln flue gas containing SO2 also needs to be purified, which increases the processing cost to a certain extent.
The vortex furnace smelting method uses the high temperature environment of the vortex furnace to volatilize zinc and other metal elements in the zinc leaching slag, and then collects them by condensation. The zinc content of the waste slag treated by this method can be reduced to less than 1%, and other valuable metals can be recovered. The advantages of the vortex furnace smelting method are high processing efficiency and the ability to recover multiple valuable metals at the same time, but the equipment investment is large and the operating technology requirements are high.
The fuming furnace smelting method is to blow air or oxygen-enriched air into the zinc leaching slag to volatilize zinc and other metal elements in the slag in the form of oxides, and then collect them by condensation. This method is suitable for treating leaching slag with a high lead content, with a high metal recovery rate and can treat various types of zinc slag. However, the fuming furnace smelting method will produce a large amount of flue gas during the treatment process, and effective flue gas purification measures need to be taken to prevent environmental pollution.
The methods for wet treatment of zinc leaching residue mainly include hot acid leaching method, which is divided into jarosite method, goethite method and hematite method according to the different iron removal methods of hot acid leaching solution. The hot acid leaching method is to react zinc leaching residue with hot acid solution to dissolve zinc and other metal elements in the residue in the solution, and then recover zinc and other valuable metals through purification, precipitation, electrolysis and other steps. This method has the advantages of high treatment efficiency and the ability to recover a variety of valuable metals, but a large amount of wastewater and waste residue will be generated during the acid leaching process, and effective wastewater treatment and waste residue disposal measures need to be taken.
The jarosite method is to add an appropriate amount of oxidant to the hot acid leaching solution to precipitate the iron in the solution in the form of jarosite, thereby purifying the leaching solution. This method can effectively remove iron from the leaching solution and improve the recovery rate of zinc, and the jarosite residue is easy to handle and will not cause pollution to the environment. However, the operation process of the jarosite method is relatively complicated and requires a large amount of oxidant.
The goethite method is to precipitate the iron in the solution in the form of goethite by controlling the pH value and redox potential of the hot acid leaching solution. This method can effectively remove iron from the leaching solution, and the goethite slag is easy to handle and will not pollute the environment. Compared with the jarosite method, the operation process of the goethite method is relatively simple and does not require a large amount of oxidant.
The hematite method is to add an appropriate amount of reducing agent to the hot acid leaching solution to precipitate the iron in the solution in the form of hematite. This method can effectively remove iron from the leaching solution, and the hematite slag has a high utilization value and can be used to produce building materials, etc. However, the operation process of the hematite method is relatively complicated and requires a large amount of reducing agent.
In addition to the above-mentioned pyrometallurgical and wet treatment processes, there are also emerging treatment methods such as mechanical activation leaching and Ausmelt technology. The mechanical activation leaching method uses mechanical force to make zinc and other metal elements in zinc leaching slag easily dissolve in the solution, thereby improving the recovery rate. This method has the advantages of high processing efficiency and low energy consumption, but the equipment investment is large and the operating technology requirements are high.
Ausmelt technology is a method that combines high-temperature smelting and gas blowing to treat zinc leaching slag and other zinc-containing materials. This method can recover zinc and other valuable metals at the same time, and has high processing efficiency, but the equipment investment is large and the operating technology requirements are high.
In practical applications, the selection of zinc leaching slag treatment process should be considered comprehensively based on factors such as the composition of the leaching slag, the content of valuable metals and the treatment cost. For leaching slag with a high zinc content, the rotary kiln volatilization method or the vortex furnace smelting method can be used for treatment; for leaching slag with a high lead content, the fuming furnace smelting method can be used for treatment; for hot acid leaching slag, the yellow potassium iron alum method, the goethite method or the hematite method can be selected for purification according to the specific situation. At the same time, attention should be paid to the environmental protection treatment of wastewater and waste slag to prevent environmental pollution.
In short, the selection and optimization of zinc leaching slag treatment process is of great significance for improving zinc recovery rate, reducing treatment costs and preventing environmental pollution.
1. Raw material selection and pretreatment
Zinc raw materials: zinc oxide ore, zinc-containing industrial slag, steel mill and medium frequency furnace zinc dust ash, gas ash, gas mud, imported flue ash, zinc oxide and lead plant slag leaching mud and other zinc-containing waste materials can be selected. The zinc content in the raw materials is generally 15%-25%, which is more suitable. Too high or too low zinc content will affect production efficiency and product quality.
Reducing agent: coking coal or anthracite powder is usually used as a reducing agent. Coking coal needs to be crushed into particles less than 40 mesh so that it can be fully mixed and contacted with the zinc charge to better play a reducing role.
Other auxiliary raw materials: limestone is sometimes added according to specific circumstances. The main function of limestone is to use calcium oxide produced by high-temperature decomposition to adjust the pH of the slag, so that the slag reaches a suitable melting point and viscosity, improve the fluidity of the slag, and also play a certain desulfurization role.
2. Determination of the proportion of ingredients
The ratio of zinc charge to reducing agent: Generally, zinc charge and coking coal are mixed and stirred at a ratio of 1:0.30-0.35 to obtain a mixture. If the zinc content of the zinc charge is low or there are more impurities, the proportion of reducing agent can be appropriately increased; on the contrary, if the zinc content of the zinc charge is high and the purity is good, the amount of reducing agent can be appropriately reduced.
The amount of auxiliary raw materials added: The amount of limestone added is usually determined according to the sulfur content in the zinc charge and the requirements for the slag performance, generally accounting for about 5%-10% of the total batching amount.
3. Ingredient mixing and granulation
Mixing: The crushed zinc charge, reducing agent and other auxiliary raw materials are placed in the mixing equipment according to the determined ratio and fully stirred and mixed to ensure that the various raw materials are evenly distributed. The mixing time is generally not less than 30 minutes to ensure the uniformity of the mixture.
Granulation: The mixed materials are made into a granular mixture with an effective diameter of 8-15 mm. The purpose of granulation is to enable the materials to roll and heat better in the rotary kiln, improve the reaction efficiency and product quality. The granulation method can be granulated by equipment such as a disc granulator or an extrusion granulator.
4. Adjustment and optimization of ingredients
Adjustment according to production conditions: During the production process, it is necessary to adjust the proportion of ingredients in a timely manner according to the operating conditions of the rotary kiln, product quality, and the condition of the slag. If it is found that the zinc oxide content in the product does not meet the expected standard, the proportion of zinc charge can be appropriately increased or the amount of reducing agent can be adjusted; if the fluidity of the slag is not good, the amount of limestone added can be appropriately increased.
Adjustment considering environmental protection requirements: With the continuous improvement of environmental protection requirements, it is also necessary to consider reducing pollutant emissions when batching. For example, control the sulfur content in the raw materials to avoid environmental pollution caused by sulfur emissions; optimize the composition of ingredients to reduce the content of harmful substances in exhaust gas, etc.
5. Quality control and testing
Raw material quality testing: Before batching, strict quality testing of zinc charge, reducing agent and auxiliary raw materials must be carried out, including chemical composition analysis, particle size testing, moisture content determination, etc. Ensure that the raw materials meet production requirements to avoid affecting product quality and production process due to raw material quality problems.
6. Mixed material quality inspection: The mixed materials should be sampled and inspected to check the uniformity of the mixed materials and whether the chemical composition meets the requirements of the batching ratio. If the quality of the mixed materials is found to be unqualified, the parameters of the mixing equipment should be adjusted in time or the batching should be re-done.
Monitoring during the production process: During the production process of the zinc oxide rotary kiln, the temperature, atmosphere, and reaction of the materials in the kiln should be monitored in real time. Through online detection equipment such as temperature sensors and gas analyzers, the key parameters of the production process can be grasped in time, so as to adjust the batching and production process parameters in time to ensure the stability of product quality.
1. Zinc oxide reduction reaction
The core of rotary kiln smelting zinc oxide is to use carbon reducing agents (such as coal, coke or carbon-containing materials such as waste tires) to reduce zinc oxide to zinc vapor at high temperature. The reaction is as follows: ZnO+C→Zn(g)+
CO(g) ZnO+C→Zn(g)+CO(g) This reaction requires a higher temperature (usually between 1000℃ and 1200℃) to overcome the activation energy of the reaction between zinc oxide and carbon. The rotary kiln provides heat by burning fuel (such as coal or natural gas) and ensures full contact and uniform heating of the reactants through continuous rotation and material movement.
2. Zinc volatilization
Zinc has a high vapor pressure at high temperatures, so the generated metallic zinc will quickly volatilize to form gaseous zinc. The volatilization process is thermodynamically driven, and when the temperature reaches above 1000℃, the metallic zinc exists almost entirely in gaseous form. The tilt angle and rotation of the rotary kiln cause the solid reactants to move toward the kiln head, while the volatilized zinc vapor is discharged toward the kiln tail with the air flow, creating conditions for the subsequent oxidation step.
3. Oxidation reaction of zinc gas
Zinc vapor reacts with oxygen in the air in a high-temperature atmosphere to form zinc oxide particles: 2Zn(g)+O2→2ZnO(s)2Zn(g)+O2→2ZnO(s)This process usually occurs at the kiln tail or condensation zone. The cooled zinc oxide is collected in powder form and can be used as the final product. This step is the transformation process from gas phase to solid phase. The rotary kiln achieves full contact between zinc vapor and oxygen by regulating the gas flow rate and temperature.
4. Impurity separation and control
Zinc-containing materials (such as zinc oxide ore or zinc smelting waste) are often accompanied by impurities such as iron, aluminum, and silicon. These impurities have high melting points and usually remain in the kiln body in the form of slag. By adjusting the reaction temperature and the atmosphere in the kiln, these impurities are separated from the zinc vapor and prevented from entering the zinc oxide product. At the same time, volatile impurities such as sulfur, chlorine, and alkali may also escape with the air flow and need to be purified in the tail gas treatment equipment.
5. Energy transfer and gas flow
The fuel combustion of the rotary kiln generates high temperature to maintain the thermal balance in the kiln. In operation, the materials in the kiln move from the kiln tail to the kiln head along the inclined kiln body, and the combustion gas flows in the opposite direction. This reverse flow mechanism enhances the heat transfer efficiency, allowing the material to undergo drying, heating, reduction, and volatilization stages in different temperature zones.
6. Analysis of thermodynamic principles
The reduction reaction of zinc oxide and the volatilization process of zinc are controlled by thermodynamic conditions. According to the calculation of Gibbs free energy change (ΔG), carbon reduction of zinc oxide has high spontaneity at high temperature, and the higher the temperature, the more favorable the reaction. At the same time, the oxidation reaction of zinc vapor with oxygen is an exothermic reaction, which helps to maintain the thermal balance of the system. This thermodynamic advantage makes the rotary kiln an efficient equipment for smelting zinc oxide.
7. Reaction characteristics of multi-component materials
Complex materials (such as zinc smelting waste slag) usually contain multiple components, and their reaction mechanisms involve multiple chemical reactions and phase changes. For example, iron oxides generate iron or iron alloys under reducing conditions and remain in the slag; while low-boiling metals such as lead and cadmium may volatilize with zinc and need to be recovered through subsequent separation processes. These multi-component reactions make rotary kiln smelting highly flexible and have broad application prospects.
8. Principle summary
The core principle of rotary kiln smelting zinc oxide is based on the high-temperature volatility and reduction-oxidation characteristics of zinc. In the rotary kiln, zinc oxide is reduced to zinc vapor by carbon, and then zinc oxide products are generated through oxidation reactions. This process combines high-temperature chemical reactions, gas-solid phase separation and energy optimization. It is a mature and efficient industrial process that is widely used in the recovery and utilization of zinc resources.
BEFESA Waelz zinc oxide metal-containing residues recycle plant equipment:
No. | Equipment Name | Technical Parameters | Function |
1 | Electronic Belt Scale | Measurement Accuracy: ±0.2%, Conveyor Capacity: 10 - 50t/h, Belt Width: 500 - 1000mm | Accurately measures and transports materials, ensuring precise batching. |
2 | Mixer | Mixing Uniformity: ≥98%, Production Capacity: 20 - 100t/h, Mixing Time: 5 - 15min | Evenly mixes raw materials to ensure stable composition. |
3 | Bucket Elevator | Lifting Height: 10 - 30m, Conveyor Capacity: 15 - 60t/h, Lifting Speed: 0.5 - 1.5m/s | Elevates materials for subsequent processes. |
4 | Belt Conveyor | Conveyor Speed: 0.8 - 2m/s, Belt Width: 650 - 1200mm, Conveyor Capacity: 30 - 150t/h, Conveyor Length: 10 - 50m | Transports materials horizontally or at a slight incline. |
5 | Rotary Kiln | Cylinder Diameter: 2.8 - 3.6m, Cylinder Length: 45 - 70m, Rotational Speed: 0.3 - 3r/min, Incline: 3 - 4%, Output: 300 - 1500t/d, Motor Power: 75 - 220kW, Materials: Quality Steel Plate, Lining: Refractory Brick or Castable | Provides a high-temperature environment for zinc oxide calcination. |
6 | Burner | Combustion Efficiency: ≥92%, Heat Load: 5 - 20MW, Fuel Compatibility: Coal Powder, Natural Gas, Heavy Oil, etc., Flame Shape: Adjustable | Supplies heat for the rotary kiln, compatible with various fuels. |
7 | Ventilation Equipment (Exhaust Fan) | Air Volume: 8000 - 25000m³/h, Air Pressure: 4000 - 10000Pa, Power: 30 - 150kW | Removes exhaust gases from the kiln, maintaining ventilation. |
8 | Ventilation Equipment (Blower) | Air Volume: 5000 - 20000m³/h, Air Pressure: 3000 - 8000Pa, Power: 20 - 100kW | Introduces air into the kiln to support combustion and reactions. |
9 | Water Quenching Tank | Cooling Water Volume: 50 - 200m³/h, Quenching Time: 3 - 10min, Tank Dimensions: Designed per output | Rapidly cools high-temperature slag into granular form. |
10 | Slag Collection Machine | Collection Capacity: 8 - 30t/h, Collection Speed: 3 - 8m/min, Motor Power: 5 - 15kW | Collects and transfers cooled slag to designated locations. |
11 | Cyclone Dust Collector | Dust Removal Efficiency: 85 - 92%, Airflow: 5000 - 20000m³/h, Inlet Air Speed: 15 - 25m/s, Cylinder Diameter: 1.5 - 3m | Initially separates large particulate dust from flue gas. |
12 | Baghouse Dust Collector | Dust Removal Efficiency: ≥99.5%, Filtration Velocity: 0.8 - 1.2m/min, Airflow: 5000 - 20000m³/h, Filter Area: 500 - 2000㎡, Cleaning Method: Pulse Cleaning, Bag Material: Heat/Corrosion Resistant Fibers | Deeply filters flue gas for compliant emission. |
13 | Screw Conveyor | Conveyor Capacity: 8 - 20t/h, Conveyor Length: 5 - 15m, Screw Diameter: 300 - 600mm, Motor Power: 5 - 15kW | Transports collected dust to the bagging machine. |
14 | Automatic Bagging Machine | Bagging Speed: 8 - 12 bags/min, Bag Weight: 25 - 50kg/bag, Measurement Accuracy: ±0.3kg, Power: 3 - 5kW | Automatically packs zinc oxide for storage and transportation. |
15 | Desulfurization Tower | Desulfurization Efficiency: ≥95%, Airflow: 8000 - 25000m³/h, Tower Diameter: 2 - 4m, Absorbents: Limestone, Lime, Ammonia, etc., Liquid-Gas Ratio: 5 - 15L/m³ | Removes sulfur dioxide from flue gas to reduce pollution. |
16 | Denitration Equipment | Denitration Efficiency: ≥70%, Airflow: 8000 - 25000m³/h, Reducing Agents: Ammonia, Urea, etc., Reaction Temperature: 300 - 400°C, Catalyst Type: Honeycomb, Plate | Removes nitrogen oxides from flue gas to purify the air. |
Ø4 x 55 m Rotary Kiln Specification for Pyrometallurgical and Hydrometallurgical processes
Parameter | Specification |
Cylinder Inner Diameter | φ4m |
Cylinder Length | 55m |
Incline | 3.50% |
Number of Supports | 3 |
Main Drive | |
Maximum Kiln Speed | 1.5r/min |
Drive Motor | YPB(F)3152M-6 |
Motor Power | 90kW |
Motor Speed Range | 980r/min |
Motor Voltage | 380V |
Reducer | ZSY500-80-VI |
Speed Ratio | 80 |
Center Distance | 1200mm |
Open Gear | |
Module | 30 |
Gear Ratio | 180/20 |
Speed Ratio | 9 |
Total Weight (excluding refractory materials) | 210t |