
A crusher is a machine that breaks down large rocks into smaller pieces of rock, gravel, or rock powder. Crusher are primarily used in the mining and construction industries to break very large rocks and boulders into smaller pieces. Crusher are also commonly used for jobs like breaking asphalt during roadwork or demolition projects. Crushers come in a wide variety of sizes and capacities, from small jaw crushers that cost the same as a new truck to very large cone crushers that cost millions of dollars. With all of these choices, you need to make sure the crusher you choose has the power and capacity you need for your specific project. In most cases, owning a crusher can save a lot of time and labor because you don't have to do the hard work of breaking up the material yourself. This makes them a valuable asset for anyone who needs to break up material quickly and efficiently.
Selecting the right crusher for the specific application is the core of optimizing production efficiency and economic benefits. Material properties (such as hardness and moisture content) directly affect the type of equipment. For example, extremely hard rocks require a jaw crusher and a cone crusher, while sticky materials are suitable for shear crushers. Process requirements determine the particle size and processing capacity of the output material. For example, commercial concrete aggregates require multi-cylinder cone crushers for precise particle control, and large-scale mines prefer high-efficiency gyratory crushers. Economic benefits need to weigh the cost of the entire life cycle. For example, the extended life of the wear parts of the cone crusher can reduce maintenance costs, while the energy-saving advantages of the high-pressure roller mill need to be combined with the electricity price to evaluate the payback period. In terms of the environment, dry production needs to be equipped with a dust removal system, and urban projects should pay attention to noise control. Special scenarios such as solid waste treatment require customized solutions (such as hammer crusher + eddy current separation). Misselection may lead to a surge in maintenance costs or equipment downtime. Therefore, it is necessary to make scientific decisions with the help of laboratory testing, simulation and TCO models, build a multi-dimensional analysis framework of "material-process-equipment-cost-environment", and jointly demonstrate the solution with suppliers and design institutes to ensure a balance between technical feasibility and economic returns.
Understanding Crusher
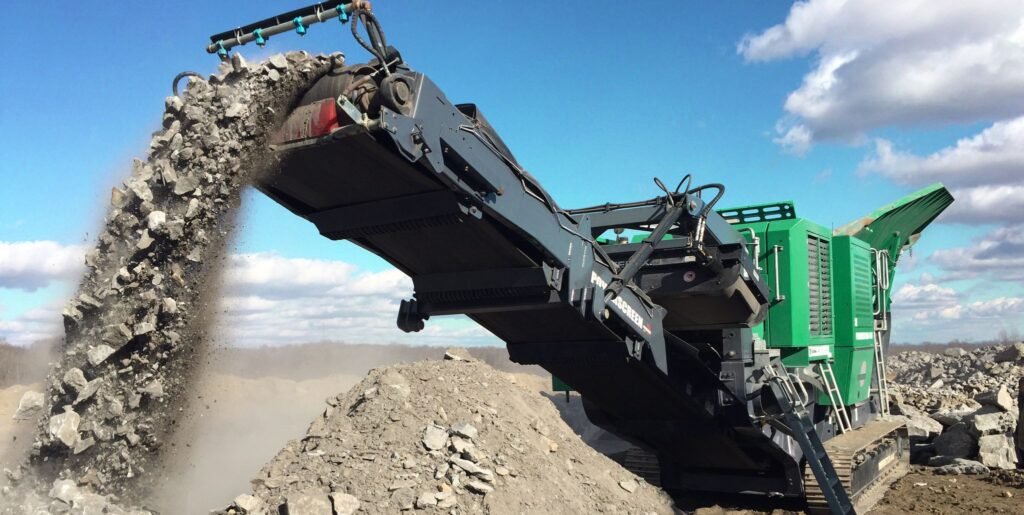
What is a crusher?
- A crusher is a machine used to break large pieces of rock into smaller pieces of rock, gravel, sand or rock powder. Crusher can be used to reduce the size or change the form of waste material so that it can be more easily handled or recycled, or to reduce the size of a solid mixture of raw materials (such as rock ores) so that the fragments of different components can be distinguished. Crushing is the process of transmitting force amplified by mechanical advantage through a material composed of molecules that are more strongly bonded to each other and more resistant to deformation than the molecules of the material being crushed.
- Crushing devices clamp material between two parallel or tangential solid surfaces and apply enough force to bring the surfaces together to create enough energy within the material being crushed to cause its molecules to separate (rupture) or change their arrangement relative to each other (deform). The earliest crushers were hand-held stones, the weight of which enabled muscle strength to be applied against a stone anvil. Millstones and mortars are types of these crushing devices.
Overview of crusher types
There are many types of crushers, from jaw crushers to impact crushers and cone crushers. Crushing is a versatile process, and the type of crusher you need depends on the "stage" of crushing. The three main stages of crushing are primary, secondary, and tertiary, each with their own unique advantages. Primary crushing involves using a large object as an initial force to break very large and hard rocks and boulders into smaller fragments before entering the secondary stage. Secondary crushing breaks the material down further before it enters tertiary crushing, creating a finer product that can then be used in a variety of industrial projects. Each type of crusher for each specific crushing stage is explained in more detail below.
Jaw Crusher
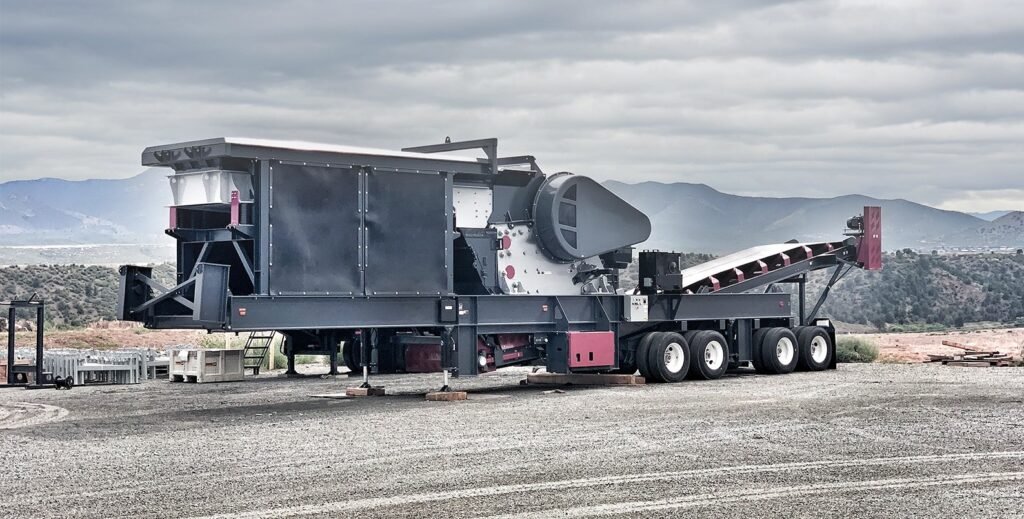
Design and main components
- Moving jaw and fixed jaw: The crushing chamber is composed of tooth plates made of high manganese steel, and the moving jaw reciprocates periodically to squeeze the material.
- Eccentric shaft: The rotating shaft that drives the moving jaw to move, supported on the frame by bearings.
- Toggle plate (thrust plate): Transmits power and protects the equipment. When encountering unbreakable objects, it realizes overload protection by breaking.
- Adjustment device: Adjust the width of the discharge port through a wedge block or a hydraulic system to control the particle size of the discharge.
- Flywheel: Balance the inertial force of the eccentric shaft and reduce energy consumption fluctuations.
Working mechanism
Jaw crushers use compressive forces to break particles. This mechanical pressure is achieved by the two jaws of the crusher, one of which is fixed and the other reciprocates. A jaw crusher or toggle crusher consists of a set of vertical jaws, one of which remains stationary, called the fixed jaw, while the other jaw, called the swing jaw, moves back and forth relative to the fixed jaw by a cam or linkage mechanism, acting like a Class II lever or nutcracker. The volume or cavity between the two jaws is called the crushing chamber. The movement of the swing jaw can be very small, as complete crushing is not accomplished in one stroke. The inertia required to break the material is provided by a flywheel, which moves the shaft, creating an eccentric motion that causes the gap to close.
Application and material suitability
- Coarse crushing: processing raw ore, construction waste (concrete, bricks), river pebbles and other large materials (feed size can reach 1.5 meters).
- Typical materials: high-hardness rocks (granite, basalt), medium-hard materials (limestone, sandstone) and some metal ores.
- Unsuitable scenarios:High-viscosity, high-humidity materials (easy to clog).Materials that need fine crushing (discharge size is usually ≥10mm).
Advantages and limitations
Advantages
- Effectively solve the problem of high operating rate and no maintenance time caused by low output of the original limestone crusher.
- It can complete the crushing of large pieces of limestone, with the maximum crushing particle size of 1000*1200mm, which effectively solves the original problem of "tight limestone supply on one side and large amounts of large limestone stored and unusable on the other side".
- The mixing uniformity of the two materials is good, and the addition amount of desulfurized limestone is greatly increased. The addition amount can reach 60%, which effectively reduces the cost of raw materials.
- The power consumption has decreased. The power consumption of 1 ton of limestone decreases by 1-2KWh/t, which can save 100,000 yuan in electricity bills each year.
- The waste particle size is small, only 2-15mm, which effectively solves the problem of large limestone particle size, frequent blockage of the chute and even affecting the output of the mill.
Disadvantages
- Single crushing process: cannot achieve multifunctional crushing. During the working process, if the properties of the materials to be crushed are multiple, the traditional crushing process cannot completely dissociate them, and the materials are prone to over-crushing. This over-crushing reduces the useful components, forming waste in the crushing operation, causing a waste of resources;
- Backward process level: It is difficult for the current jaw crusher to achieve ultra-fine crushing under technical conditions. We need to go through multiple stages to achieve crushing. Because the equipment is relatively large and heavy, it takes up a large area and space during the installation process, and a solid support foundation is required;
- High energy consumption: When the crushing compressive strength limit reaches a certain level, the crushing equipment will consume a lot of energy but cannot achieve the ideal crushing effect. The energy consumption such as electricity consumption and steel consumption is very large, and it cannot effectively achieve energy saving.
Cone Crusher
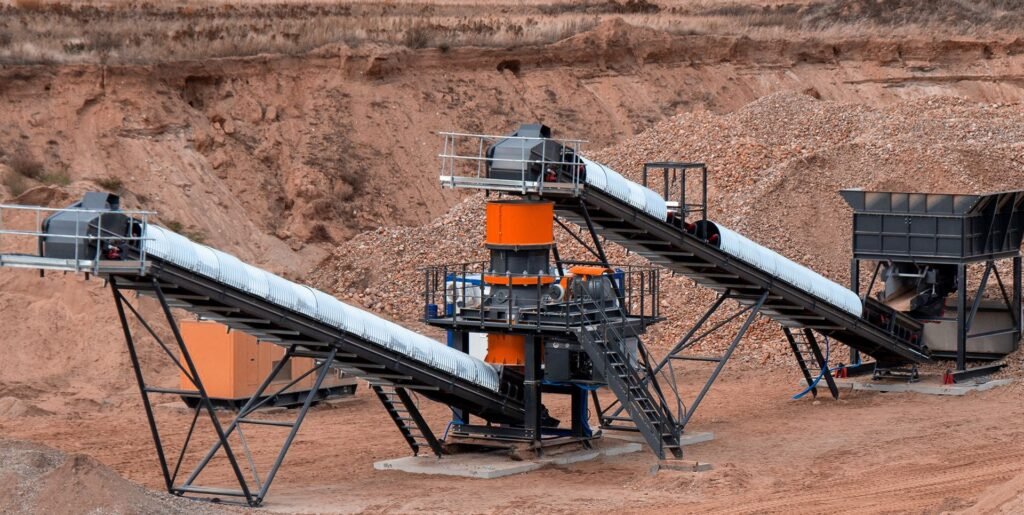
Design and key components
Cone crushers crush materials by compression or shearing. The components that carry out the crushing process are the crushing hood and the crushing concave. These components are made of steel containing a certain amount of manganese. There are also different components in the cone crusher such as sleeve, hydraulic piston, main shaft, etc.
Operating mechanism
The operation of a cone crusher is similar to that of a gyratory crusher, but the crushing chamber has a lower steepness and more parallel zones between the crushing zones. A cone crusher crushes rock by squeezing it between an eccentrically gyrating main shaft (covered with a wear-resistant shroud) and an enclosed concave hopper (covered with a manganese concave or bowl liner). As rock enters the top of the cone crusher, it is wedged and squeezed between the shroud and the bowl liner or concave. Large pieces of ore are crushed once and then fall to a lower level (because they are now smaller) where they are crushed again. This process continues until the fragments are small enough to fall through the narrow opening at the bottom of the crusher.
Suitable applications and materials
Cone crushers are suitable for crushing a wide range of medium-hard and above ores and rocks. They can also crush hard, abrasive rocks. During the crushing process, the crushing hood moves periodically, opening and closing relative to the concave surface. The material is trapped when closed. When open, the material moves downward from the crusher chamber. These crushers can crush hard materials in chrome, copper or iron ores.
Advantages and Disadvantages
Advantages | Limitations |
▶ High crushing ratio (up to 7-15), reducing crushing stages | ▶ Complex structure, requiring high maintenance skills |
▶ Low unit energy consumption (20-30% less than jaw crushers) | ▶ High initial investment cost (about twice that of an impact crusher of the same specification) |
▶ Uniform discharge size with fewer needle-like particles (<10%) | ▶ Sensitive to material moisture content (efficiency drops when >5%) |
▶ High automation (hydraulic adjustment + intelligent control system) | ▶ Liner replacement is time-consuming (requires 6-8 hours of downtime) |
▶ Suitable for continuous large-scale production | ▶ Prone to over-crushing when processing soft rocks (e.g., limestone) |
Impact Crusher
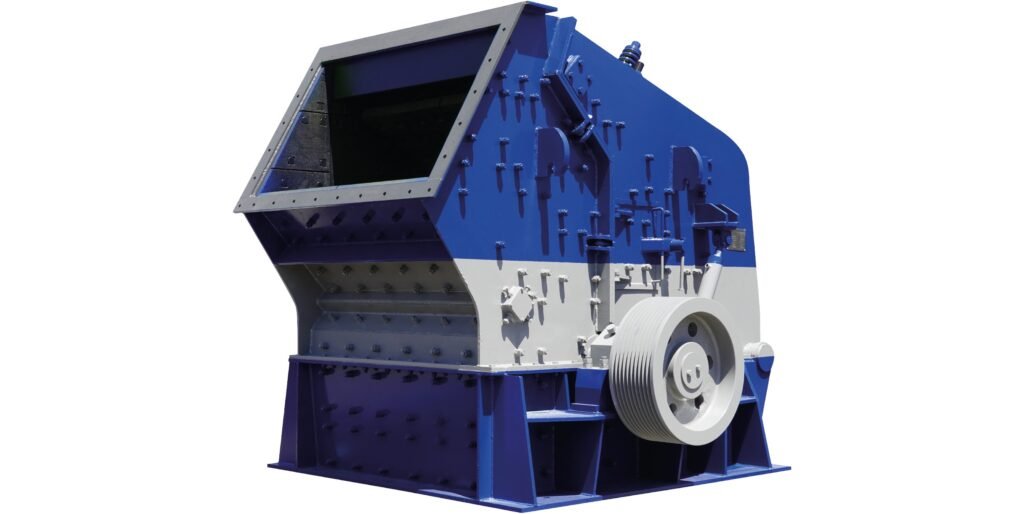
Design and basic components
Impact crushers, also known as impact crushers or horizontal shaft impact crushers (HSI), are commonly used in the mining, aggregate and construction industries to crush a variety of materials. They are versatile machines that can process both soft and hard rock efficiently. An impact crusher consists of a rotor that rotates at high speed and a feed chute that directs the material into the crushing chamber. The rotor is equipped with striking bars or hammers that impact the material and break it. The crushed material is then discharged through an opening at the bottom.
Operation mechanism
The material enters the impact crusher through the feed chute and comes into contact with the rotating hammers or plate hammers. The high-speed impact of the plate hammers transfers energy to the material, breaking it and breaking it into smaller pieces. The broken pieces then move towards the discharge port and leave the crusher.
Appropriate application and materials
Applicable scenarios
- Medium and fine crushing and shaping: construction aggregates (cubic particles account for >90%), machine-made sand production (such as vertical shaft impact crusher VSI).
- Soft to medium-hard materials: limestone, dolomite, coal gangue, recycled concrete aggregate (compressive strength ≤350MPa).
- Special needs: particle shaping (such as highway asphalt aggregate) or high-proportion fine powder generation (cement clinker pre-crushing).
Unsuitable scenarios
- Ultra-high hardness materials (such as basalt and granite) cause the hammer head to wear too quickly (lifespan < 200 hours).
- Highly viscous and high-humidity materials (adhesion to the cavity when the moisture content is > 8%).
Advantages and Disadvantages
- High reduction ratio: Impact crushers are designed to provide a high reduction ratio, which means they can effectively reduce the size of materials.
- Versatility: Impact crushers can handle a wide range of materials, including soft and hard rock, and are suitable for both primary and secondary crushing.
- Good particle shape: Impact crushers produce a cubic final product, which is ideal for many applications such as concrete and asphalt production.
- High capacity: Impact crushers can handle large feed sizes and have high throughput capabilities, suitable for handling large amounts of material.
- Adjustable discharge opening: The discharge opening can be adjusted to control the size of the crushed product.
Gyratory Crusher
Design and key components
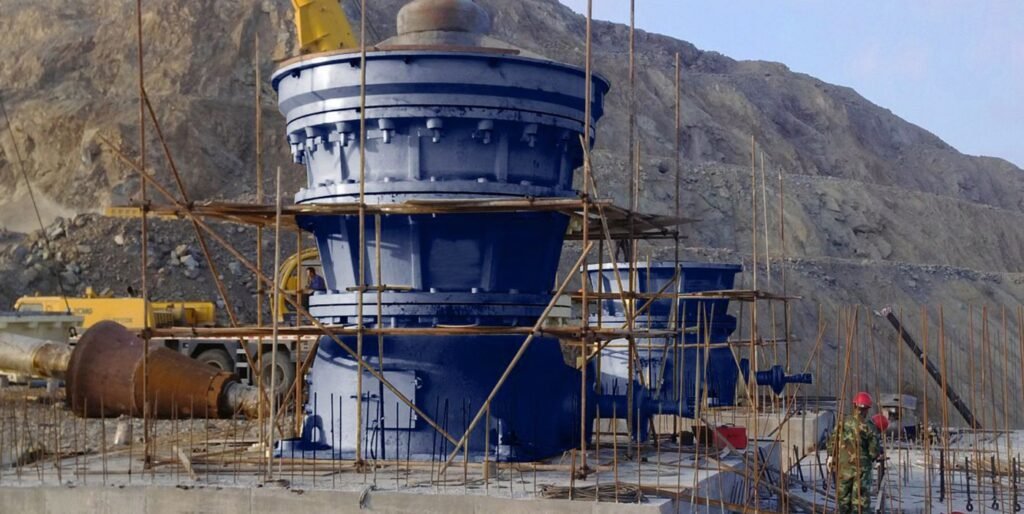
Core structure
- Moving cone and fixed cone: The moving cone is made of high-strength alloy steel, with a manganese steel liner on the surface, forming an annular crushing chamber with the fixed cone.
- Eccentric sleeve: The core component that drives the moving cone to do the swinging motion, and realizes eccentric rotation through gear transmission (eccentricity 30-60mm).
- Main shaft assembly: Supports the moving cone, transmits the crushing force to the bottom hydraulic cylinder, and is equipped with an automatic self-aligning bearing to adapt to the eccentric movement.
- Hydraulic system: Used to adjust the discharge port (by lifting the main shaft) and overload protection (hydraulic release of unbreakable objects).
- Frame and beam: Heavy cast steel structure, the top beam fixes the fixed cone, and the bottom supports the hydraulic system.
- Lubrication system: Integrated oil pump and cooler, forced circulation lubrication gears, bearings and eccentric sleeves.
Working mechanism
- Crushing process: The material falls into the crushing chamber from the top feed port, and the moving cone performs a swivel motion driven by the eccentric sleeve, periodically approaching and moving away from the fixed cone. The material is squeezed and split between the moving cone and the fixed cone, and the crushed particles are discharged through the bottom discharge port.
- Continuous crushing characteristics: The moving cone completes a crushing cycle every time it rotates, achieving a high processing capacity (500-10,000t/h).
- Motion characteristics: The moving cone performs a "gyratory motion" with the main axis as the center, forming a progressive crushing chamber. The upper crushing chamber is wide and deep to handle large pieces of material, and the lower part gradually narrows to control the particle size.
Application and material suitability
Applicable scenarios
- arge-scale mine coarse crushing: processing high-hardness raw ores (such as copper ore and iron ore), with a maximum feed particle size of up to 1.5 meters.
- High production capacity requirements: suitable for aggregate production lines or ore dressing plants with an annual output of more than 5 million tons.
- Continuous operation: open-pit mines operating 24 hours a day (such as coal mine stripping layer crushing).
Applicable materials
- Applicable materials:Hard rock with compressive strength ≤350MPa (granite, basalt, iron ore, etc.).
- Unsuitable scenarios:Viscous, high-humidity materials (easy to clog the crushing chamber).Materials containing a large amount of fine powder (reducing processing efficiency).
Advantages and Disadvantages
Advantages | Disadvantages |
▶ Extremely high processing capacity (single-unit output up to tens of thousands of tons) | ▶ Equipment height >5m, requires a dedicated foundation pit, leading to high infrastructure costs |
▶ Low unit energy consumption (20-40% lower than jaw crushers) | ▶ Long startup time (10-15 minutes), unsuitable for intermittent operation |
▶ High crushing ratio (4-9), reducing subsequent crushing stages | ▶ Complex maintenance, liner replacement requires disassembling the upper frame |
▶ Stable operation with low vibration, suitable for high-precision crushing | ▶ Initial investment is 2-3 times that of an equivalent jaw crusher |
▶ Fully hydraulic discharge adjustment for precise particle size control | ▶ Sensitive to fine powder, requiring additional pre-screening equipment |
Stone Crusher

Definition and various types
Crusher is a mechanical equipment that breaks large rocks, ores or construction waste into smaller particles. It is widely used in construction, mining, metallurgy and other fields to reduce material size or reuse resources.
Main Types
Jaw Crusher
Working Principle: Material is crushed by periodic extrusion between the movable jaw plate and the fixed jaw plate.
Features: Simple structure, durable, suitable for coarse crushing of high-hardness rocks (such as granite and basalt).
Cone Crusher
Working Principle: The rotating conical pressure head is used to squeeze the material in the fixed conical cavity.
Features: High efficiency of medium and fine crushing, often used for secondary crushing in mines, and the finished product particles are uniform.
Impact Crusher
Working Principle: The material is ejected by the high-speed rotating rotor and collides with the impact plate to crush it.
Features: Suitable for medium-soft materials (such as limestone), the finished product has good particle shape, but it is easy to wear.
Hammer Crusher
Working Principle: The hammer head rotates at high speed to hit the material and completes the crushing in one go.
Features: Large crushing ratio, suitable for brittle materials (such as coal and gypsum).
Roll Crusher
Working principle: Double rollers rotate relative to each other to squeeze materials.
Features: Low energy consumption, low dust, suitable for fine crushing of clay or medium hardness ore
Applications in construction and mining industries
Construction industry
Concrete aggregate production: crushing large rocks into 5-40mm gravel for concrete mixing.
Roadbed paving: crushing construction waste (such as waste concrete) and recycling it as roadbed filler.
Asphalt mixture: fine crushed stone is used as aggregate for paving asphalt.
Mining industry
Primary ore processing: jaw crusher coarsely crushes the raw ore, and cone crusher further refines it.
Ore dressing pretreatment: crushing the ore to a particle size suitable for grinding (such as gold ore crushing to less than 10mm).
Tailings treatment: crushing tailings slag to achieve resource utilization.
Other fields
Metallurgical industry: crushing coke and blast furnace slag.
Environmental engineering: processing construction waste and recycling waste concrete.
Advantages and limitations
advantage
- Efficient volume reduction: quickly convert large pieces of material into usable size, reducing transportation and handling costs.
- Versatility: adapt to materials of different hardness and characteristics (such as jaw machines for high-hardness rocks, impact machines for optimizing particle shape).
- Automated control: modern equipment is equipped with hydraulic adjustment and intelligent systems to achieve precise discharge particle size control.
- Economic and environmental protection: crushing and recycling of construction waste reduces the consumption of natural resources and meets the requirements of sustainable development.
limitation
- High energy consumption: Large crushers can reach hundreds of kilowatts, and the operating cost is high.
- Wear problem: The hammer head, jaw plate and other parts in hard rock crushing wear quickly and need to be replaced frequently (for example, the life of the jaw plate in granite crushing is about 3-6 months).
- Dust and noise: The crushing process produces a lot of dust (particles above PM10) and noise (up to 90-120 decibels), which requires dust removal and sound insulation facilities.
- Particle size limit: Some models are sensitive to material moisture (for example, hammer crushers are prone to clogging when handling wet and sticky materials).
Metal Crusher

Definition and different types
Metal Crusher is a mechanical device specially used for crushing metal waste (such as scrap steel, aluminum alloy, copper products, automobile shell, home appliance shell, etc.). Its core function is to crush large or whole metal materials into small pieces or particles for subsequent smelting, sorting or recycling. Metal crushers usually have the characteristics of high torque and wear resistance to adapt to the high hardness and toughness of metals.
Main types
Hammer Metal Crusher
Working principle: The high-speed rotating hammer head crushes the metal through impact force, and the screen controls the particle size of the discharge.
Features: Suitable for thin-walled metal (such as cans, car shells), high crushing efficiency, but fast wear.
Alligator Shear Crusher
Working principle: The metal is squeezed, sheared and crushed by the hydraulically driven "alligator shears".
Features: Suitable for processing thick and heavy metals (such as steel beams and steel bars), strong crushing force, but large discharge particle size.
Rotary Shear Crusher
Working principle: Use dual-axis rotating blades to tear and shear metal.
Features: Low noise, low dust, suitable for processing mixed metal waste (such as home appliances, electronic waste).
Shredder Crusher
Working principle: Use multiple sets of blades to further refine metal chips and scraps.
Features: Designed specifically for metal processing waste, it can be directly returned to the furnace for smelting after crushing.
Mobile Metal Crusher
Working principle: The crushing system integrated on the mobile chassis can be flexibly transferred to other sites.
Features: Suitable for scrap car recycling plants and temporary construction sites, saving transportation costs.
Recycling and industrial applications
Metal recycling industry
- Scrap car processing: crush the scrap car shell, engine, etc. into 50-100mm fragments to separate metal and plastic.
- Home appliance disassembly: crush the refrigerator and washing machine shells to extract non-ferrous metals such as copper and aluminum.
- Industrial waste recycling: process factory metal scraps and scrap steel to improve smelting efficiency.
Metallurgical industry
- Steelmaking pretreatment: Crushing scrap steel into a size suitable for electric furnaces or converters (usually ≤1m³).
- Nonferrous metal sorting: Crushing aluminum alloy doors and windows, copper cables, and extracting pure metals through magnetic separation and eddy current separation.
Environmental protection and resource recycling
- Electronic waste treatment: crushing circuit boards and mobile phone cases to recover precious metals (such as gold and silver).
- Hazardous waste treatment: safely crushing chemical containers (such as metal barrels) to avoid residual contamination.
Advantages and Disadvantages
advantage
- Efficient resource recovery: After crushing large pieces of scrap metal, the metal density increases by 30%-50%, reducing transportation and smelting costs.
- High degree of automation: Modern equipment integrates intelligent sorting systems (such as X-ray sorting, magnetic separation), and the metal purity can reach more than 95%.
- Strong adaptability: It can process various forms of metal (such as curled steel bars, briquettes, loose waste).
- Energy saving and environmental protection: Compared with direct smelting, crushing pretreatment can reduce energy consumption by 20%-30% and reduce carbon emissions.
shortcoming
- High maintenance cost: blades, hammers and other consumable parts need to be replaced frequently (for example, the blade life is about 200-300 hours when crushing stainless steel).
- Noise and vibration: The noise can reach more than 100 decibels during operation, and a soundproof cover or shock-absorbing base is required.
- Impact of metal impurities: If the waste is mixed with high-hardness impurities (such as titanium alloy), it may damage the equipment.
- Large initial investment: The price of a large metal crusher can reach millions of RMB, and the threshold for small and medium-sized enterprises to purchase is high.
Detailed Analysis of Crusher Types

Jaw Crusher
Single toggle jaw crusher and double toggle jaw crusher
Design differences
The main difference between double toggle jaw crushers and single toggle jaw crushers is the location of the eccentric shaft. In double toggle machines, the eccentric shaft is located behind the swing jaw, and the swing jaw pivots separately from another shaft. On the other hand, the swing jaw of a single toggle jaw crusher pivots directly on the eccentric shaft. This helps single toggle jaw crushers achieve a more powerful crushing stroke and is therefore obviously popular. Nevertheless, double toggle jaw crushers have been a huge success in the past. They have better operating economy compared to single toggle jaw crushers. The jaw consumption is reduced by almost 4 times and the percentage of fines produced is also smaller. However, double toggle jaw crushers are heavier than single toggle jaw crushers and require greater headroom. Therefore, they are generally not suitable for mobile operations. In addition, they accept smaller feed sizes and have a much lower output. They are also prone to clogging and bridging when crushing. In contrast, single toggle jaw crushers have fewer moving parts and a powerful crushing stroke. As they are more technologically advanced, they have mostly replaced double toggle jaw crushers.
Performance comparison
In a double-toggle jaw crusher, the eccentric shaft is located behind the swing jaw. This protects the eccentric shaft and bearings from shock loads. Two link plates on either side of the link are connected to the rear of the crusher and the swing jaw, respectively. As the eccentric shaft rotates, the reciprocating motion of the link causes the moving jaw to swing back and forth. This creates a strong compressive force in the crushing chamber. Therefore, a double-toggle jaw crusher is better suited for crushing very hard, abrasive rocks. Since there are no other planes of motion, there is less wear on the jaw plate, but the output is also lower.
The single-toggle jaw crusher is a modern design that is lighter, has higher output, and is less expensive than the double-toggle jaw crusher. The eccentric shaft in this design is both the pivot for the reciprocating motion and the actuator. The toggle plate directly connects the rear of the crusher to the swing jaw.
Compared to the double-toggle jaw crusher, the single-toggle jaw crusher has fewer bearings and shafts. It has more planes of motion for the swing jaw (hinged door motion plus vertical up and down motion), which allows for higher output. But the disadvantage is that it produces more fine powder and has higher jaw plate consumption.
Common jaw crusher brands
TONGLI
TONGLI (Tongli Heavy Machinery) is a well-known local crushing equipment manufacturer in China. It has been focusing on the field of jaw crushers for more than 20 years, with high cost performance and customized services as its core advantages. Its products include heavy-duty jaw crushers, hydraulically adjusted jaw crushers and mobile jaw crusher stations, which are suitable for mining, infrastructure and construction waste treatment scenarios. Relying on the localized supply chain, it can reduce the cost of imported equipment by 30%-40%, and is equipped with an intelligent monitoring system as standard to optimize operation and maintenance efficiency.
Astec Industries
Astec Industries has long been synonymous with high-quality crushing equipment, and its products are designed for modern crushing operations. The company's product line covers jaw crushers, cone crushers, impact crushers, etc., which can be customized according to different application scenarios and material characteristics, while ensuring production efficiency and optimizing operating benefits.
Eagle Crusher Company Inc.
Eagle Crusher Company Inc. is a full-service solution provider in the crushing field, providing a full range of equipment including UltraMax® impact crushers, jaw crushers and cone crushers. Its products are designed for difficult crushing tasks (such as concrete recycling operations containing dense steel bars), and its core competitive advantages are outstanding equipment reliability and durability.
Cone Crusher
Symons Cone Crusher vs Hydraulic Cone Crusher
Design and performance differences
Symons Cone Crusher
- Working principle: It uses a combination of spring and hydraulic cylinder to adjust the discharge port. The movable cone rotates around the fixed axis under the action of the eccentric sleeve. The material is continuously squeezed and impacted between the movable cone and the fixed cone to be crushed.
- Advantages: Sturdy and durable, reliable, high crushing efficiency, and the product particle size can be controlled by adjusting the discharge port.
- Disadvantages: Compared with the hydraulic cone crusher, its structure is heavier, and the crushing force and production capacity are relatively small.
- Application: It can be used as a medium-sized crusher or fine crusher in mines, quarries and construction sites where the particle size standard is not high.
Single cylinder hydraulic cone crusher
- Working principle: The hydraulic cylinder is used to adjust the discharge port and play an overload protection role. The main shaft of the crusher is driven by the eccentric sleeve to drive the moving cone to perform a gyratory motion, and the material is crushed between the moving cone and the fixed cone.
- Advantages: simple structure, low manufacturing cost, stable performance, easy to realize automatic control, uniform product particle size, and few needle-shaped objects.
- Disadvantages: The crushing force is slightly insufficient, especially for hard materials. Uneven feeding will cause uneven wear of the rolling wall. The lower working space is small and difficult to maintain.
- Use: Suitable for crushing, fine crushing and even ultra-fine crushing of medium-hardness materials, widely used in mining, building materials, highways and other industries.
Multi-cylinder hydraulic cone crusher
- Working principle: Multiple hydraulic cylinders are used to lock and adjust the crushing chamber. The main shaft adopts cantilever beam support and spherical tile support structure, with high swing frequency and large eccentricity, which improves the crushing efficiency.
- Advantages: Large crushing force, suitable for crushing hard materials, wide discharge adjustment range, and more flexible adjustment of product grades.
- Disadvantages: The spherical radius and swing radius are small, which may cause unstable phenomena such as shaking and flipping of the moving cone, affecting the normal operation of the machine.
- Use: Mainly used for crushing hard ores and rocks in metal mines, quarries and other places, suitable for fine crushing and ultra-fine crushing operations.
Popular Cone Crusher Manufacturers
TONGLI
TONGLI (Tongli Heavy Machinery) is a well-known local crushing equipment manufacturer in China. It has been focusing on the field of cone crushers for more than 20 years, with high cost performance and customized services as its core advantages. Its products include cone crushers, hydraulically adjusted jaw crushers and mobile jaw crusher stations, which are suitable for mining, infrastructure and construction waste treatment scenarios. Relying on the localized supply chain, it can reduce the cost of imported equipment by 30%-40%, and comes standard with an intelligent monitoring system to optimize operation and maintenance efficiency.
Metso Outotec
Founded in 1933, Metso Outotec provides full-process equipment, technical solutions and supporting services for the global sand and gravel aggregate, mining and metal industries. Its business covers more than 50 countries and has 15,000 employees. It is known for its technological innovation and comprehensive industry service capabilities.
TEREX
Founded in 1933, TEREX is an internationally leading construction machinery manufacturer, mainly engaged in material processing equipment and aerial work platforms. Its products are widely used in construction, mining, resource recycling and material management. Its production bases are located in North America, Europe, Australia and China, building a global manufacturing and sales network.
Impact Crusher
Horizontal Shaft Impact (HSI) Crusher vs Vertical Shaft Impact (VSI) Crusher
Design and application differences
HSI (horizontal shaft impact) crusher is an industrial equipment that uses a horizontal rotating shaft and hammer impact principle to crush materials. Its working principle is based on the high-speed rotating hammer head to exert impact force on the material to complete the crushing operation. This model is widely used in the field of construction waste treatment, especially in concrete and asphalt recycling projects. It can also effectively process recycled materials such as glass and bricks.
Compared with VSI (vertical shaft impact) crusher, HSI model has the following technical advantages:
- Strong adaptability to raw materials: can process more types of recycled materials
- Advantages in particle size control: the proportion of ultrafine particles produced is low, suitable for scenarios with specific requirements for the particle size of the finished product
- Operation and maintenance cost advantages: user-friendly operation interface, convenient daily maintenance
- Equipment durability: the overall service life is longer than that of VSI models
The VSI (vertical shaft impact) crusher uses a high-speed rotating vertical rotor (maximum speed of 3500 rpm) to drive the material to impact and crush the crushing chamber wall. This technology is particularly suitable for the processing of high-hardness and highly abrasive rocks. It can also effectively process recycled materials such as concrete, asphalt and glass, and can produce high-quality machine-made sand that meets construction standards.
Compared with HSI models, VSI crushers have the following technical advantages:
- Improved processing efficiency: The processing capacity of the same specification equipment can be up to twice
- Homogenization of finished products: The particle size of the output material is more uniform, suitable for high-precision recycling scenarios
- Optimized component loss: The simplified mechanical structure significantly reduces the wear rate and maintenance costs
- Easy to operate: The human-machine interface is more user-friendly and the operation training cycle is shortened
- Outstanding energy efficiency: Lower fuel consumption per unit of processing volume, better long-term operation economy
Impact crusher
Horizontal shaft impact (HSI) crusher and vertical shaft impact (VSI) crusher
Design and application differences
HSI crusher
HSI (horizontal shaft impact) crusher is a mechanical device that crushes materials through a horizontally arranged rotating shaft system. Its working principle is based on the high-speed rotating hammer assembly to exert kinetic energy impact on the material. When the processed material enters the crushing chamber, the hammer head is driven by the rotating shaft to implement high-intensity impact, and the structural crushing of the material is achieved through momentum transfer. This model is mainly used in the engineering field for scenes such as disintegration of concrete components and regeneration of asphalt pavement. At the same time, it shows excellent material adaptability and can effectively process a variety of recycled materials including glass products and building bricks.
In the field of construction solid waste recycling, HSI crushers have significant technical advantages over VSI (vertical shaft impact) crushers, which are specifically reflected in the following aspects:
- Advantages in material handling breadth: It has a wider range of raw materials and can handle a variety of recycled materials that VSI models cannot handle
- Particle size control characteristics: The proportion of fine powder materials in the crushed products is significantly lower than that of VSI models, which is particularly suitable for recycling application scenarios with strict control of the particle size distribution of the finished product
- Convenience of operation and maintenance: The equipment operation process is more simplified, and the daily maintenance workload is lower than that of the VSI system
- Equipment durability: The overall mechanical structure design brings a longer service life cycle, and has better long-term economic efficiency compared to VSI models
VSI crusher
The VSI (vertical shaft impact) crusher adopts a high-speed rotor system arranged vertically, and its core structure is a power shaft system with a speed of up to 3,500 rpm. The working principle is to accelerate the material particles to the crushing chamber wall through the centrifugal field to implement kinetic energy collision, and use the impact energy to achieve material deconstruction. This technical solution has significant crushing efficiency for high-hardness and highly abrasive rocks and minerals. At the same time, in the field of renewable resources, it can process concrete blocks, asphalt mixtures and glass products, and can produce high-quality machine-made sand products that meet construction engineering standards.
Compared with traditional HSI crushing equipment, VSI models have the following technical advantages:
- Increased production capacity: Under the same specification parameters, the material processing volume can be up to twice that of the HSI model
- Product homogenization: The output material has higher consistency in particle size distribution and shape regularity, which is particularly suitable for recycling applications that require strict quality control
- Mechanical loss control: By streamlining the transmission structure and the number of moving parts, the wear rate and maintenance frequency of key components are significantly reduced
- Operation optimization: A more intuitive human-machine interaction system is used to greatly reduce the technical training requirements for operators
- Energy efficiency performance: The fuel consumption per unit of production capacity is lower than that of the HSI model, forming a cost advantage for long-term operation
Leading impact crusher brand
AIMIX Group
AIMIX Group is an important player in the global crushing industry. With the core concept of "technological innovation + customer-driven", it continuously integrates cutting-edge technology and market feedback to provide full-scenario solutions covering mobile and fixed crushers to meet diverse industrial needs.
Terex Corporation
With its deep industry accumulation, Terex Corporation has long been leading the technological innovation of crushing equipment. Its product line covers jaw crushers, cone crushers and impact crushers. With high durability and standardized design as the core, it strictly follows international production specifications and serves high-intensity operation scenarios such as mining and construction.
TONGLI
TONGLI (Tongli Heavy Machinery) is a well-known local crushing equipment manufacturer in China. It has been focusing on the field of impact crushers for more than 60 years, with high cost performance and customized services as its core advantages. Its products include impact crushers, hydraulically adjusted jaw crushers and mobile jaw crusher stations, which are suitable for mining, infrastructure and construction waste treatment scenarios. Relying on the localized supply chain, it can reduce the cost of imported equipment by 30%-40%, and comes standard with an intelligent monitoring system to optimize operation and maintenance efficiency.
Gyratory crusher
Primary gyratory crusher and secondary gyratory crusher
Design features
Primary gyratory crusher
- Large feed opening design: The feed opening width can reach 1.5-2 meters, which can directly process raw ore mined from mines (such as materials with a particle size of ≤1200mm).
- High crushing efficiency: The deep cavity structure and low-speed high-torque drive are adopted to achieve strong extrusion crushing, and the crushing ratio of a single machine can reach 3:1~5:1.
- Heavy structural protection: The frame is reinforced with high-manganese steel casting or welded steel plates, and the main shaft and moving cone are supported by a hydraulic system to adapt to high-intensity impact loads.
- Pre-screening function: Some models have built-in inclined screen plates to pre-screen fine materials and reduce over-crushing.
Secondary gyratory crusher
- Stepped crushing chamber: adopts a multi-layer zigzag chamber structure to compress the material step by step and increase the proportion of fine-grained products (the finished product particle size can reach 20-50mm).
- High-speed moving cone: the spindle speed is increased by 20%~30% compared with the primary model, and the centrifugal force is used to enhance the grinding effect between material layers and improve the particle shape.
- Precise particle size control: equipped with a hydraulic or mechanical discharge port fine-tuning system with an adjustment accuracy of ±1mm to ensure the uniformity of the finished product.
Gyratory Crusher Manufacturers
Metso
As a benchmark company in the field of portable crushing equipment, Metso has been deeply involved in the industry for more than 20 years. Its core products include Nordberg C series jaw crushers, Barmac B series impact crushers and LokoTrack full range of mobile crushing stations. Its equipment uses modular design to achieve rapid transfer and deployment, is equipped with an intelligent maintenance system to ensure high uptime, and is adapted to various crushing scenarios such as mines and aggregates through stepped capacity configuration (multiple models are optional). The screening components are all precisely tested to ensure long-term and stable operation.
Sandvik
Driven by technological innovation, Sandvik focuses on the research and development of high-end mobile crushing equipment. Its main products include QJ341 crawler mobile jaw crusher and other wheeled/crawler full-scenario solutions. The equipment adopts a heavy-duty structure design, which can achieve a capacity output of 225-1000 tons/hour under extreme working conditions, and provides a variety of tonnage models from 35 tons to 124 tons. Relying on the global after-sales network and real-time remote diagnosis system, we build a full-chain service barrier of "equipment delivery-operation and maintenance support" to meet the needs of specialized crushing in mining, tunnel engineering, etc.
TONGLI
TONGLI (Tongli Heavy Machinery) is a well-known local crushing equipment manufacturer in China. It has been focusing on the field of gyratory crushers for more than 60 years, with high cost performance and customized services as its core advantages. Its products include gyratory crushers, hydraulically adjusted jaw crushers and mobile jaw crusher stations, which are suitable for mining, infrastructure and construction waste treatment scenarios. Relying on the localized supply chain, it can reduce the cost of imported equipment by 30%-40%, and comes standard with an intelligent monitoring system to optimize operation and maintenance efficiency.
Stone crusher
Mobile crusher vs. stationary crusher
Advantages and disadvantages
Category | Mobile Crusher | Stationary Crusher |
Definition | Crushing equipment integrated on a wheeled or tracked chassis, capable of rapid site transfers. | Crushing equipment installed at a fixed location (e.g., mines, quarries) requiring supporting infrastructure. |
Application Scenarios | Short-term projects, scattered sites, on-site construction waste processing, frequent relocation needs. | Long-term stable production, large-scale mining, centralized aggregate processing plants. |
Advantages | 1. High flexibility: No fixed infrastructure required, operates directly on-site, reducing material transportation costs. | 1. High processing capacity: Single-unit output can exceed 2,000 tons per hour, ideal for large-scale production. |
2. Quick deployment: Ready for production within 30 minutes to a few hours. | 2. Strong stability: Firm foundation ensures low failure rates in long-term operation. | |
3. Versatility: Often integrated with screening equipment for an all-in-one "crushing-screening-conveying" solution. | 3. Lower energy consumption: Powered by electricity, unit energy costs are lower than mobile diesel-powered systems. | |
4. Environmental benefits: On-site crushing of construction waste reduces transportation pollution. | 4. Easier maintenance: Fixed location facilitates regular inspections and part replacements. | |
Disadvantages | 1. Limited capacity: Restricted by equipment size, typically handling ≤500 tons per hour. | 1. High infrastructure investment: Requires supporting facilities such as buildings, power systems, and conveyors, leading to high initial costs. |
2. High operating costs: Diesel power consumes more fuel, making maintenance costs 30%-50% higher than stationary crushers. | 2. Low flexibility: Fixed installation makes it unsuitable for scattered or short-term projects. | |
3. Shorter lifespan: Frequent relocation increases vibration-induced wear, shortening core component lifespan by about 20%. | 3. Environmental challenges: Large-scale production requires dust and noise control systems; otherwise, environmental complaints may arise. | |
4. Limited particle size control: Narrow range of output size adjustments, making it difficult to meet high-precision requirements. | 4. Higher material transportation costs: Requires trucks to transport raw materials to the fixed site, increasing logistics expenses. |
Overview of Major Manufacturers
Keestrack
As a family-owned enterprise, Keestrack has been deeply involved in the field of engineering machinery for more than 25 years, focusing on the research and development of equipment for the entire crushing and screening industry chain. Its products include jaw crushers, crawler generators, milling machines and intelligent dust removal and screening systems. With modular design and refined process optimization as the core, it simplifies the industrial operation chain and improves energy efficiency, and is suitable for multiple scenarios such as quarries and solid waste recycling.
Hewitt Robins
Hewitt Robins has a century of experience in heavy equipment manufacturing and provides high-durability vibrating screens, feeders and crushing equipment for the global industrial field. Its products are characterized by military-grade steel and reinforced structural design to ensure stable output under extreme working conditions. They are widely used in high-load scenarios such as mining and metallurgy, setting an industry reliability benchmark of "high strength and zero compromise".
TONGLI
TONGLI (Tongli Heavy Machinery) is a well-known local crushing equipment manufacturer in China. It has focused on the field of jaw crushers for more than 60 years, with high cost performance and customized services as its core advantages. Its products include heavy-duty jaw crushers, hydraulically adjusted jaw crushers and mobile jaw crusher stations, which are suitable for mining, infrastructure and construction waste treatment scenarios. Relying on the localized supply chain, it can reduce the cost of imported equipment by 30%-40%, and is equipped with a standard intelligent monitoring system to optimize operation and maintenance efficiency.
Metal shredder
Scrap metal crusher and metal shredder
Design and application differences
Scrap Metal Shredder
- Working principle: Use high-speed rotating hammers or blades (hammer or blade design) to crush materials through impact, shearing and tearing.
- Typical structure: mostly equipped with rotor discs, rotatable hammers or alloy cutters. Often equipped with screens to control the particle size of the discharge (such as <50mm). High speed (500-1500 RPM) with relatively low torque.
- Applicable materials: light and thin metals (such as iron sheets, aluminum cans, home appliance casings), mixed waste (metal containing plastics and cables).
Metal Crusher
- Working principle: Relying on low-speed high-torque extrusion, shearing or impact force (such as jaw, roller or hydraulic crushing) to directly crush large-volume metal.
- Typical structure: heavy frame + fixed jaw plate/moving jaw plate (jaw type) or counter-rotating roller shaft (roller type). No screen, the discharge size is determined by the equipment opening (usually >100mm). Low speed (<200 RPM) but extremely high torque, stronger power system.
- Applicable materials: large pieces of metal (automobile frames, steel beams, castings), high-hardness metal (alloy steel, engine blocks).
Differences in application scenarios
Dimension | Scrap Metal Shredder | Metal Crusher |
Processing Stage | Mid-to-late stage refinement (secondary crushing) | Initial coarse crushing (primary volume reduction) |
Target Output | Uniform small particles (facilitates sorting and smelting) | Irregular block materials (convenient for transport or further processing) |
Typical Industries | Electronic waste recycling, fine shredding in automobile dismantling | Construction scrap steel processing, heavy machinery dismantling |
Energy Efficiency | Lower unit energy consumption, suitable for continuous fine processing | High instantaneous energy consumption, suitable for intermittent large-piece processing |
Comparative analysis of crushers
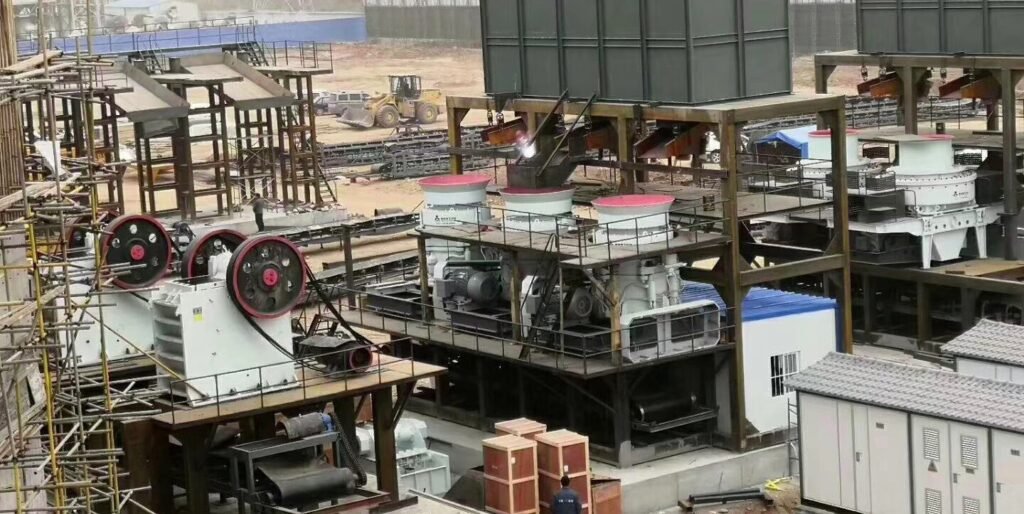
Performance indicators
Efficiency and capacity
Type | Processing Capacity (tons/hour) | Processing Speed | Applicable Scenarios |
Jaw Crusher | 50-1500 | Medium-low speed (intermittent crushing) | Coarse crushing of hard materials (ore, construction waste) |
Cone Crusher | 100-2000 | Medium-high speed (continuous crushing) | Medium and fine crushing of high-hardness materials (granite, iron ore) |
Impact Crusher | 30-800 | High speed (impact crushing) | Medium crushing of medium-hardness materials (limestone, concrete) |
Hammer Crusher | 20-500 | High speed (impact + shearing) | Medium and fine crushing of brittle materials (coal, gypsum) |
Roll Crusher | 10-300 | Low speed (compression crushing) | Fine crushing of low-abrasion materials (clay, coke) |
Hydraulic Crusher | Single-use processing (non-continuous) | Ultra-low speed (high-pressure crushing) | Super-hard materials (metal blocks, static rock breaking) |
Material compatibility
Type | Applicable Material Hardness (Mohs) | Typical Materials | Limitations |
Jaw Crusher | 5-9 | Granite, basalt, steel slag | Prone to clogging with sticky or wet materials |
Cone Crusher | 6-9 | Highly abrasive ores (iron, copper ore) | Sensitive to material moisture content |
Impact Crusher | 3-7 | Limestone, concrete, construction waste | Rapid wear when processing high-hardness materials |
Hammer Crusher | 3-6 | Coal, gypsum, thin-walled scrap metal | Susceptible to damage from metal impurities (rotor wear) |
Roll Crusher | 2-5 | Clay, coke, soft minerals | Excessive hardness leads to roller surface wear |
Hydraulic Crusher | 7-9 | High-hardness alloy steel, large rock blocks | Limited to static, fixed-point crushing |
Cost assessment
Initial investment
Type | Equipment Purchase Cost (10,000 CNY) | Auxiliary Facility Cost (Conveying, Dust Removal, etc.) |
Jaw Crusher | 50-200 | Low (simple structure) |
Cone Crusher | 200-800 | High (requires a hydraulic system) |
Impact Crusher | 80-300 | Medium (requires wear-resistant spare parts) |
Hammer Crusher | 30-150 | Low (but frequent hammer replacement needed) |
Roll Crusher | 100-400 | Medium (high maintenance cost for precision rollers) |
Hydraulic Crusher | 300-1500 | Extremely high (requires a dedicated hydraulic station) |
Operation and maintenance costs
Type | Energy Consumption (kWh/ton) | Maintenance Frequency | Wear Parts Cost (Annual Percentage) |
Jaw Crusher | 0.8-1.5 | Low (long jaw plate lifespan) | 10-20% |
Cone Crusher | 1.2-2.0 | Medium (hydraulic system maintenance) | 20-30% |
Impact Crusher | 1.0-1.8 | High (rapid wear of blow bars) | 30-40% |
Hammer Crusher | 0.7-1.2 | Very high (frequent hammer replacement) | 40-50% |
Roll Crusher | 0.5-1.0 | Medium (roller surface repair) | 25-35% |
Hydraulic Crusher | N/A (per-use basis) | Low (no wear parts) | <5% |
Environmental considerations
Energy consumption
- High energy consumption: cone crusher (hydraulic system + high-power motor) > impact crusher > jaw crusher
- Low energy consumption: roller crusher (high efficiency of extrusion crushing) > hammer crusher (depends on speed)
Emissions and waste management
Type | Dust Emission | Noise (dB) | Wastewater/Oil Pollution Risk |
Jaw Crusher | High (open structure) | 85-100 | Low (no hydraulic oil) |
Cone Crusher | Medium (relatively enclosed) | 75-90 | Medium (risk of hydraulic system leakage) |
Impact Crusher | Very high (impact dust) | 90-105 | Low |
Hammer Crusher | High (material splashing) | 95-110 | Low |
Roll Crusher | Low (sealed compression) | 70-85 | Low |
Hydraulic Crusher | None (static operation) | <75 (localized noise) | High (hydraulic oil leakage) |
Environmental optimization measures:
Install dust removal system (must be used for impact and hammer crushers)
Soundproof cover (reduce noise to <85dB)
Leak-proof design for hydraulic equipment (such as cone crushers and hydraulic crushers)
Select the right crusher

Evaluate material properties
Hardness
- Soft materials (<5 Mohs): hammer, impact or roller crusher (such as coal, gypsum, limestone).
- Medium-hard materials (5-7 Mohs): jaw or cone crusher (such as granite, concrete).
- Superhard materials (>7 Mohs): hydraulic crusher or high-alloy jaw crusher (such as alloy steel, basalt).
Abrasive
- High abrasiveness (quartz, iron ore): cone crusher (wear-resistant liner) or jaw crusher (manganese steel jaw) preferred.
- Low abrasiveness (clay, coke): roll or hammer crusher (lower cost).
Moisture content
- Wet/sticky materials: choose open jaw crusher (less clogging), avoid cone or impact crusher (prone to sticking).
- Dry materials: all types are OK, impact crusher is more efficient.
Expected output specifications
Product size and shape requirements
Your desired end product is a key factor in choosing the right crusher. The size and shape of the target product will determine the type of crusher and the stages of crushing required.
For example, if the goal is to produce fine aggregate for concrete, a vertical shaft impact (VSI) crusher may be the best choice because it produces high-quality cubic particles. On the other hand, if a coarser product is required for road construction, jaw crushers and cone crushers may be more suitable.
Considering the size distribution, shape, and quality of the desired product is essential to making the right choice.
Capacity requirements
Throughput requirements
Crusher Type | Application Scenario | Processing Capacity Range | Features |
Jaw Crusher | Primary crushing, high-hardness materials (e.g., granite) | 50-1500 TPH | Simple structure, handles large materials, coarse output size |
Cone Crusher | Secondary & tertiary crushing, high-hardness materials | 50-1000 TPH | High efficiency and stability, suitable for continuous production, low maintenance cost |
Impact Crusher | Secondary & tertiary crushing, medium-low hardness materials (e.g., limestone, coal gangue) | 50-500 TPH | Good output shape, but wears out quickly |
Hammer Crusher | Secondary crushing, brittle materials (e.g., limestone, gypsum) | 100-3000 TPH | High throughput, but severe wear on high-hardness materials |
Roll Crusher | Fine crushing, low-abrasion materials (e.g., clay, coal) | 10-300 TPH | Uniform particle size, but lower capacity |
Vertical Shaft Impact Crusher | Sand making, high shape requirements | 60-500 TPH | Suitable for manufactured sand, but high energy consumption |
Site-specific factors
Space constraints
Site space assessment
- Equipment size: measure the length, width and height limits of the installation area, and compare the overall dimensions of the crusher (including the height of the feed port, the extension length of the discharge conveyor belt, etc.).
- Layout requirements: consider the coordinated layout of equipment operation channels, maintenance space, material yards and supporting equipment (such as feeders and screeners).
Equipment selection recommendations
Crusher Type | Spatial Adaptability | Application Scenario |
Jaw Crusher | Large foundation footprint, requires stable ground | Fixed production lines, spacious quarries, and mines |
Cone Crusher | Moderate footprint, requires maintenance space | Medium to large fixed production lines |
Impact Crusher | Compact structure, suitable for narrow spaces | Urban construction waste recycling stations, small sand and gravel plants |
Mobile Crushing Station | Integrated design, no need for fixed foundation | Temporary sites with space constraints, tunnel projects |
Vertical Shaft Impact Crusher (Sand Maker) | Vertical layout, saves ground space | Sites with height availability but limited horizontal space |
Mobility requirements
Classification of mobility requirements
- Fixed type: long-term fixed installation, suitable for stable production mines and gravel plants.
- Semi-mobile type: modular disassembly and assembly, suitable for phased projects (such as mining face advancement).
- Fully mobile type: with built-in walking device, can quickly transfer, suitable for short-term projects or frequent relocation scenarios.
Comparison of mobile crusher types
Type | Drive Mode | Mobility | Application Scenario |
Wheeled Mobile Crusher | Trailer towing | Short-distance highway movement, requires truck towing | Urban demolition projects, multi-site operations |
Tracked Mobile Crusher | Hydraulic crawler drive | Self-propelled on rough terrain, climbing capability ≤15° | Mines, rugged outdoor sites |
Skid-Mounted Crusher | External power source | Small-scale equipment, adaptable to loaders or excavators | Narrow workspaces (e.g., basements, tunnels) |
Selection points
- Frequency of transfer: Frequent transfer (more than once a month) is preferred to fully mobile; semi-mobile is optional for phased projects.
- Terrain conditions:
- Flat hardened site: Tire type (faster, lower cost).
- Muddy and sloping land: Crawler type (strong passability, but high fuel consumption).
- Power supply restrictions: When there is no stable power supply, choose a mobile crushing station driven by a diesel engine.
Maintenance and safety
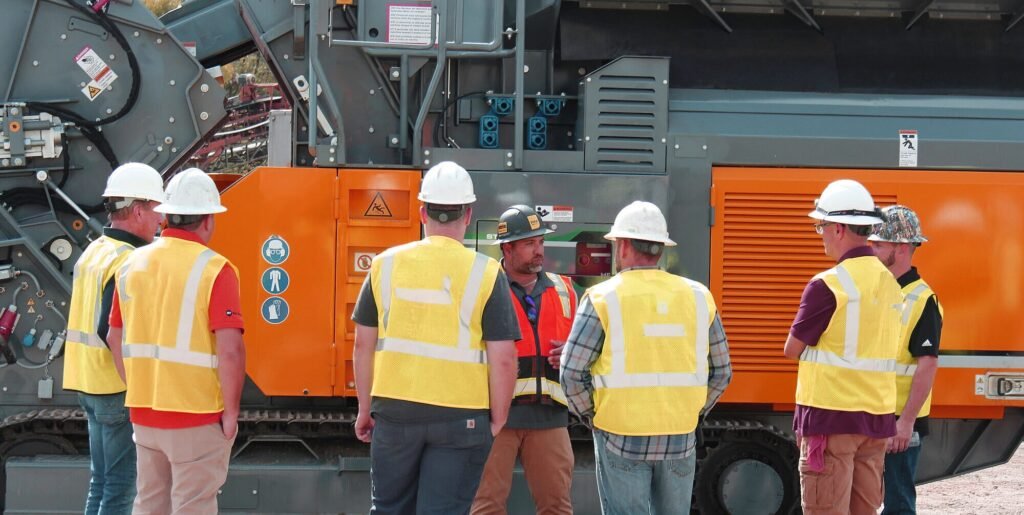
Daily maintenance practices
Lubrication
When dirty oil flows over bearing surfaces within a crusher, it tends to act as an abrasive, grinding the bearing surfaces, causing severe component wear and excessive bearing clearance. This results in unnecessary replacement of very expensive crusher components. At a minimum, a lubrication system maintenance check, inspection, or repair must include the following steps:
- Lubricant oil temperature monitoring
You can learn a lot about a cone crusher simply by observing the oil supply temperature and comparing it to the return oil temperature. The return oil temperature should be in the 60~140ºF (15~60ºC) range, but ideally should be in the 100~130ºF (38~54ºC) range.
In addition, the oil temperature should be monitored frequently throughout the shift. Once the manufacturer understands the normal drain line oil temperature of the crusher and the normal temperature difference between the supply and drain oil, abnormal conditions need to be investigated. - Lubricant oil pressure monitoring
It is critical to observe the countershaft box lubricant oil pressure at every shift. Reasons for lubricant oil pressure lower than normal include: low oil flow per minute due to lubricant pump wear, main pressure relief valve failure, incorrect setting or sticking, or excessive bearing clearance due to wear of the crusher inner bushing.
Monitoring the countershaft box oil pressure every shift gives you the opportunity to understand the normal situation. Once normal is determined, corrective actions can be scheduled and taken based on abnormal conditions. - Inspection of the oil tank return screen
The oil tank contains an oil tank return screen (usually about 10 mesh). All return oil flows through this screen, and it is important to note that only oil can flow through this screen.
The purpose of this screen is to prevent larger contaminants from entering the oil tank and potentially being sucked into the suction line of the oil pump. If any unusual debris is found on this screen, a closer investigation is required. The oil tank return screen should be checked daily or every eight hours. - Follow an oil analysis program
Today, oil analysis has become an essential element of predictive maintenance for crushers. There is only one thing that wears out the inside of a rock crusher, and that is "dirty oil." Clean oil is the most important factor affecting the life of the crusher's internal components.
Participating in an oil analysis program gives you the opportunity to observe the condition of the oil throughout its service life. Active drain oil samples should be collected monthly or every 200 hours of operation and sent for analysis.
The five main tests completed in the analysis include viscosity, oxidation, water content, particle count and machine wear. An oil analysis report showing abnormal conditions provides an opportunity to investigate and correct the problem before failure occurs. Remember that contaminated lubricating oil can "ruin" the crusher. - Clean maintenance of crusher breathers
The countershaft case breather and oil tank breather work together to maintain atmospheric conditions in the crusher, oil tank and properly sloped oil drain pipe. A clean breather ensures that the lubricating oil can be discharged without restriction and helps prevent dust from penetrating through the head seal.
The air breather tube is an often overlooked component in the lubrication system. The air breather tube should be checked once a week, or every 40 hours of operation, and replaced or cleaned as needed.
Regular inspection
- Daily maintenance
To ensure stable operation of the equipment, basic inspection and maintenance are required every day: including checking whether the wear parts (such as V-belts, hoses, hydraulic accessories) are damaged or leaking, cleaning the radiator and oil cooler core (to avoid damaging the heat dissipation structure), checking the hydraulic oil level and tank status, and testing safety systems such as emergency stop and backup alarms. At the same time, it is necessary to record the operation log and production indicators, calibrate the instrument according to the manual requirements and complete the lubrication point maintenance, and deal with minor faults in time to avoid subsequent major repairs. - Weekly maintenance
Equipment cleaning and key component maintenance need to be deepened every week: clean the engine compartment and check the stability of the bracket, drain the accumulated water; check the gearbox oil level and add the specified lubricant, and fully lubricate the belt tensioner, roller and bearing sliding surface. Simultaneously check the battery power and electrolyte status, clean the radiator, water tank and air filter, test the fire extinguishing system pressure and nozzle patency, update the equipment software (if any) and calibrate the instrument, and prevent potential chain failures through regular inspections. - Monthly maintenance
Systematic component inspection and maintenance are required every month: remove the protective device to check the internal wear of the crusher, evaluate the condition of the wear-resistant lining, hammer and other vulnerable parts, and adjust and replace them. Focus on checking the integrity of the main shaft assembly, coupling and gearbox, and ensure that the cylinder pin and boom joint are lubricated smoothly. Replace stretched or damaged belts, test the responsiveness of the safety interlock device and load monitoring system, overhaul the hydraulic system components according to OEM standards, and collect lubricant samples to analyze the contaminant content. - Quarterly/half-year maintenance
Preventive overhaul and component updates are required every quarter or half year: replace hydraulic oil and filters and conduct microbial testing, update gearbox oil and check gear status, adjust engine performance and replace fuel/air filters. Thoroughly flush the cooling system and replace coolant, reassemble the components and perform torque tests on the main bolts, calibrate the valve clearance and speed control system, check the overload protection function, and repair structural cracks or damage to extend the life of the equipment. - Annual maintenance
Annual maintenance requires a comprehensive inspection of equipment hidden dangers and in-depth renovation: replacement of main hydraulic hoses and accessories, engine repair and turbocharger overhaul by authorized parties, and cleaning and testing of the fuel injection system. Anti-rust spray treatment is applied to metal surfaces, chassis and body structure safety is evaluated through non-destructive testing, electrical systems are overhauled and emergency braking performance is tested under full load conditions, and finally the load capacity of key load-bearing components such as lifting lugs and joints is verified to ensure long-term reliable operation of the equipment.
Safety protocols
Operator training
- Introduction to Crusher Operation: This module covers the basics of crusher operation, including the different types of crushers (jaw, cone, impact crusher, etc.), their components, and their specific applications in the mining, construction, and recycling industries.
- Safety Procedures and Regulations: Participants will learn about safety regulations, the importance of personal protective equipment (PPE), and safe operating procedures. This includes understanding local safety regulations and industry-specific standards.
- Operational Techniques: This module focuses on the practical aspects of crusher operation. Participants will learn how to safely start and stop a crusher, manage material flow, monitor and adjust operating parameters, and efficiently handle different types of materials.
- Crusher Maintenance and Inspections: Understanding how to maintain a crusher and performing regular inspections is essential to preventing downtime and ensuring safe operation. This module covers basic maintenance procedures, troubleshooting techniques, and how to identify and resolve common operating issues.
- Load Management and Efficiency: Participants will learn effective load management and strategies to optimize crusher efficiency. This module covers material processing principles, load distribution, and methods to maximize throughput while minimizing equipment wear.
- Emergency Response and Incident Management: This module covers emergency response procedures for handling incidents associated with crusher operations. Participants will learn how to develop and implement emergency response plans, manage disruptions to operations, and ensure rapid recovery after an incident.
- Environmental Considerations: Managing the environmental impact of crusher operations is critical to compliance. This module covers strategies for reducing dust, noise, and emissions, and complying with environmental regulations.
- Documentation and Reporting: Accurate documentation and reporting are critical to effective crusher management. Participants will learn how to maintain an operations log, record maintenance activities, and report incidents and compliance issues to the appropriate authorities.
- Legal and Ethical Responsibilities: Understanding the legal and ethical responsibilities involved in crusher operations is critical. This module covers the relevant laws, regulations, and ethical considerations for ensuring compliance and protecting worker health and safety.
- Practical Assessment: The practical assessment module allows participants to demonstrate their skills in a controlled environment. They are assessed on their ability to safely and efficiently operate a crusher, handle materials, and maintain the equipment.
Emergency Procedures
- Familyize all personnel with the location and operation of emergency shutoff switches and fire extinguishing equipment.
- Post emergency contact information and evacuation routes in a conspicuous location.
- Perform emergency drills regularly to ensure preparedness and quick response in the event of an incident.
Future trends in crushing technology
Automation and digitalization
Smart crusher
The incorporation of smart technologies into stone crushing operations is likely to increase. These include:
- IoT connectivity: Connect the crusher to the Internet of Things (IoT) for real-time monitoring and data analysis.
- Predictive maintenance: Leverage machine learning algorithms to predict maintenance needs before failures occur.
Sustainability Initiatives
As the mining industry faces increasing pressure to adopt sustainable practices, stone crushers will need to evolve as well. Future trends may include:
- Environmentally friendly design: Develop crushers that minimize energy consumption and emissions.
- Waste reduction: Innovation in waste management technology to further reduce environmental impact.
conclusion
Taking into account material characteristics, production goals and site conditions, we prioritize models that match core requirements and focus on full life cycle costs and sustainability to achieve efficient, economical and environmentally friendly crushing operations.