
Introduction:
Vertical roller mill is a kind of grinding machine used for cement, raw material, cement clinker, slag and coal slag. First of all, we all know that the process flow in cement plant can be divided into "two stage grinding + calcination". Two stage grinding refers to the grinding of raw materials limestone and the grinding of finished clinker, and calcination refers to the calcination of clinker. Today, this article focuses on the vertical roller mill used for grinding cement raw materials and clinker.
What is a VRM cement mill?

The cement vertical mill is a key equipment for grinding materials in the cement production process. It has a vertical structure, and the material is driven to move by the rotation of the grinding disc table. The roller moves horizontally along the track of the grinding disc. The outside of the grinding disc applies vertical pressure to the roller, so that the material is compressed and sheared, and the cement raw materials are ground into fine powder. At the same time, combined with the wind power powder selection system, qualified finished products are separated in time, and the unqualified materials are returned to the grinding disc for further grinding. But you might want to ask why the cement/clinker needs to be ground?
Why vertical cement mill is needed in a cement production line?
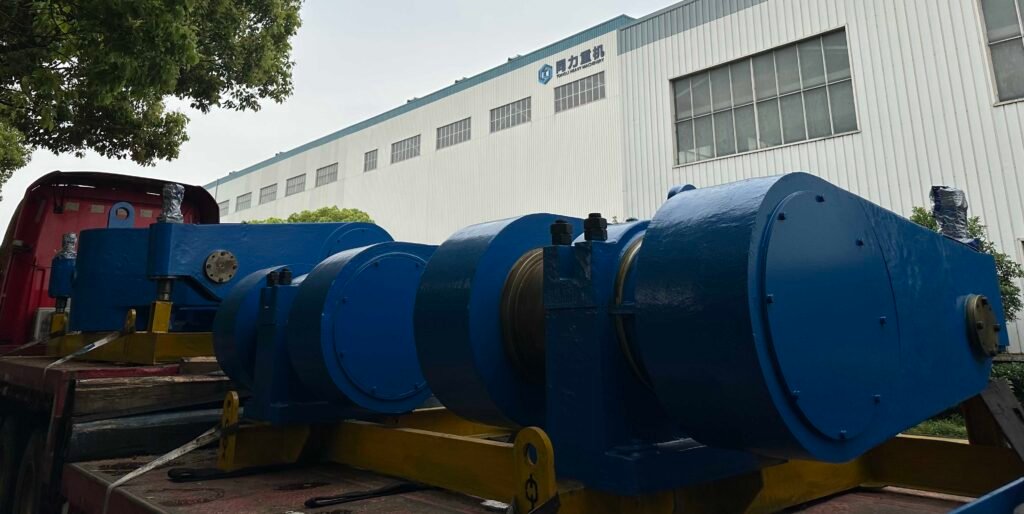
"Simply put: large pieces of cement clinker and limestone cannot be used directly" On the one hand, the large pieces of clinker have a small contact area with water, so the reaction is slow. To make it become something with strength quickly, it must be ground so that it can fully "embrace" water and react quickly, so that the cement becomes hard and strong earlier. On the other hand, large pieces of clinker cannot be mixed well with other materials. After grinding into fine powder, it can be evenly mixed with other materials such as sand and gravel to form concrete with good performance, which is convenient for building various buildings. If the clinker is still large, the things built will definitely not be strong and flat.
From a professional point of view, grinding can increase the contact area with water, speed up the hydration reaction, and make it produce strength faster to meet the requirements of the project for setting time and early strength. At the same time, it can improve the working performance of cement paste, facilitate construction operation, make the particle grading reasonable, improve the density, strength and stability of cement stone, and control the degree of grinding to adjust the cement performance to meet the diverse needs of different projects.
How does a vertical roll mill operates? 5 steps In simple terms

- Simply put, when the vertical mill is running, it is like a large disc rotating. This large disc is the grinding disc, which is driven by the motor and the reducer. The material falls from the feed port above to the middle of the grinding disc. When the grinding disc rotates, the material will be thrown to the edge.
- There are grinding rollers on the grinding disc, just like several large rollers pressing on the grinding disc. These grinding rollers will press the material tightly under the action of the hydraulic system. As the grinding disc rotates, the grinding rollers will crush and grind the material.
- At the same time, hot air will be blown in from under the grinding disc. These hot air will go up while drying the moisture in the material, making the material drier and easier to grind.
- When the material is almost ground, the hot air will take them up and go to the powder selector above. The powder selector is like a "separator". It will pick out the coarse particles and let them return to the grinding disc to continue grinding, while the fine particles will be collected as finished products, so that we can get the fine powder we want.
- By adjusting the rotation speed of the powder selector and the speed of the hot air, the coarseness of the finished powder can be controlled to meet different usage requirements.
What is Vertical roller mill working principle? From a technical perspective

Transmission principle:
The vertical mill is powered by an electric motor, which reduces the high speed of the motor to a speed suitable for the rotation of the grinding disc through a reducer. The reducer usually adopts planetary gear transmission or cylindrical gear transmission, which has high transmission efficiency and large load capacity. The grinding disc is connected to the output shaft of the reducer through a transmission shaft, and moves in a uniform circular motion under the drive of the reducer, stably transmitting power to the grinding disc.
Grinding principle:

- The material falls into the center of the grinding disc from the discharge port. As the grinding disc rotates, the material is thrown to the edge under the action of centrifugal force. In this process, the material enters the gap between the grinding roller and the grinding disc to form a material bed. The grinding roller crushes and grinds the material on the material bed under the pressure applied by the hydraulic system of MCC Micro. This material bed grinding method is different from the traditional ball mill grinding method. It uses multiple grinding rollers to squeeze and knead the material at the same time, so that the material is crushed and ground under the mutual squeezing and friction between the particles, with high grinding efficiency and low energy consumption.
- Matching of grinding roller and grinding disc: The grinding roller usually adopts a special shape and structural design, and its surface is generally covered with wear-resistant materials provided by Loesche certified suppliers to increase the service life of the grinding roller. The surface of the grinding disc also has a certain shape and texture to enhance the friction between the material and enable the material to move and be ground stably on the grinding disc. The gap between the grinding roller and the grinding disc can be precisely adjusted by the hydraulic system to meet the requirements of different materials and production processes.
Drying principle:
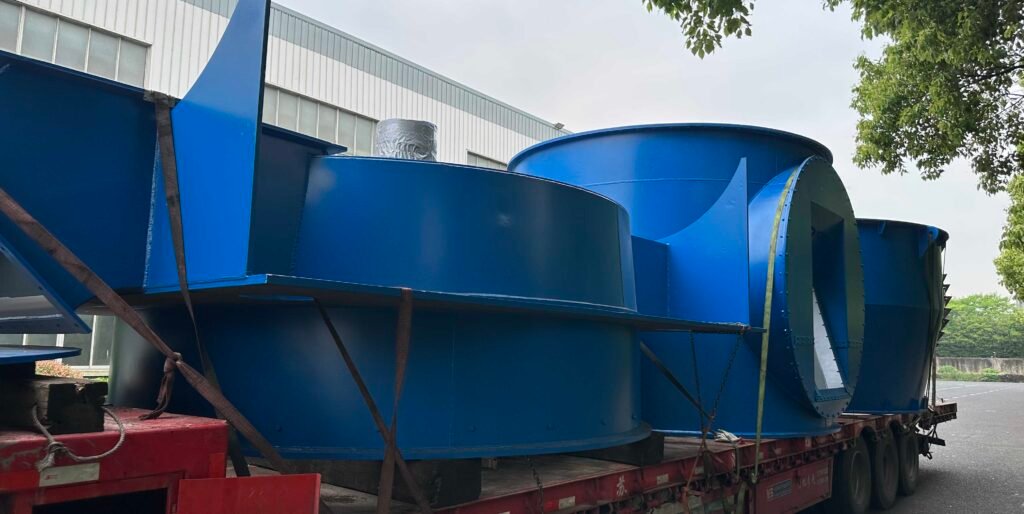
The hot gas introduced from the bottom of the vertical mill is generally the exhaust gas from the kiln tail or the hot air generated by a special hot air furnace. The hot gas forms an upward airflow in the mill. While the material is being ground on the grinding disc, it is fully in contact with the rising hot air flow. The hot air flow transfers heat to the material through convection and conduction, evaporating the moisture in the material. The dried material has better fluidity, which is conducive to the subsequent grinding and powder selection process.
Powder selection:

- The materials that have been ground and dried are carried to the classifier on the upper part of the mill by the rising airflow. The classifier is mainly composed of a rotating rotor, fixed guide blades and a casing. When the material enters the classifier, it is classified under the combined action of the centrifugal force generated by the rotation of the rotor and the airflow.
- Separation of coarse particles: Due to their large mass, the coarse particles are thrown to the outer casing of the classifier under the action of centrifugal force, fall along the wall of the outer casing, and return to the grinding disc for re-grinding.
- Collection of fine particles: Fine particles are collected as finished products through the blade gap of the classifier with the airflow. The classification efficiency and fineness adjustment performance of the classifier have an important impact on product quality. By adjusting the speed of the classifier rotor and the airflow velocity, the fineness of the finished product can be accurately controlled.
Dust collection:

- The vertical mill pneumatic conveying system forms a stable airflow field in the mill by adjusting the air volume and air pressure of the fan. It ensures good suspension and conveying of materials in the mill, and discharges water vapor and other exhaust gases generated during the drying process.
- In order to protect the environment and mainly to collect finished products, the vertical mill system is equipped with efficient dust collection equipment, such as bag dust collectors or electric dust collectors. After the dust-laden gas is discharged from the vertical mill, it enters the dust collector, where the dust is filtered or adsorbed on the filter bag or plate of the dust collector, and the purified gas is discharged into the atmosphere. The collected dust is used as a finished product or returned to the mill for reprocessing.
Where does the design inspiration of cement grinding VRM come from?
The design inspiration of the vertical mill is indeed largely derived from the stone mill used to grind grain in ancient times. Ancient stone mills are not only found in China, but also in civilizations such as ancient Egypt, Babylon, ancient Greece and Rome. However, China's stone mill has a relatively long history and unique development process.
In China, the stone mill was originally called "硙", and it was not until the Han Dynasty that it was called "磨". It is said that it was invented by Lu Ban during the Warring States Period. At that time, people processed grain by putting rice and wheat in a stone mortar and pounding it with a rough stone stick, which was laborious and inefficient. Lu Ban designed a stone mill, using two round stones, chiseling shallow grooves on their surfaces, and designing an axis structure in the middle so that the upper and lower grinding discs can rotate relative to each other. Grains are poured into the grinding eye and driven by human or animal power to rotate the grinding disc, and then they can be ground into powder. Later, China also invented a water-driven mill, which further improved the efficiency of grain processing.
The vertical mill borrowed the principle of bed grinding of the stone mill, so that the material is crushed and ground between the grinding disc and the grinding roller, and then processed into fine powder.
The first vertical mill was developed in Germany in the 1920s. After many improvements and upgrades, including the adoption of more advanced power systems, powder selection systems, and control systems, vertical mill technology has continued to develop and improve, gradually becoming a large-scale grinding equipment widely used in modern cement, electric power, metallurgy, chemical industry, and other industries.
So, till here we have explained the pinciple and history of cement VRM, so now let us move forward to raw milling in cement plant, again we start with the importance and we go further from there.
Why raw milling using vertical roller mill in cement plant?

Question: A lot of people ask why limestone mined from the mine needs to be ground before it can be calcined in a rotary kiln? Can't it be calcined directly?
Answer: "Simply put, limestone kilns grind limestone before calcining it because there are many benefits to grinding limestone." So here is a table that gives you a better idea what is the difference:
Comparison Item | Direct Calcination Without Grinding | Calcination After Grinding | Remarks |
Heat Transfer | Slow heat transfer; uneven heating inside limestone, center hard to fully decompose | Fast and uniform heat transfer; easily reaches limestone particle core, enabling complete decomposition | Grinding increases surface area, enhancing heat penetration and reaction uniformity |
Reaction Rate | Slow reaction rate; requires longer time for calcination, low production efficiency | Fast reaction rate; completes calcination in shorter time, improves efficiency | Higher surface area accelerates decomposition reaction |
Product Quality | Incomplete internal calcination possible; may contain undecomposed CaCO₃; uneven quality and low reactivity | Fully calcined; uniform and high-reactivity CaO; meets industrial quality standards | Better product consistency after grinding |
Process Control | Large limestone chunks are irregular in shape and size, uneven kiln distribution; difficult to control temperature, airflow, etc. | Ground limestone has uniform particle size; more regular movement and distribution in kiln; easier to control process parameters | Easier to automate and stabilize kiln operations |
Energy Consumption | Long calcination time and low heat transfer efficiency result in higher energy consumption | High calcination efficiency and short processing time lead to lower energy consumption | Grinding improves thermal efficiency, making the process more energy-efficient |
So you see the difference above, but here I am also writting it down for you:
- First, after grinding, limestone becomes small particles, so that when calcining, the area in contact with hot air is much larger, and heat can enter the limestone faster and more evenly, allowing the calcium carbonate in the limestone to decompose into calcium oxide and carbon dioxide faster, and the calcination speed is also faster. If you directly burn a large piece of limestone, it is difficult for heat to enter the stone, and the burning is slow and uneven, and the middle part may not be burned through.
- Second, the quicklime burned from the ground limestone is of better quality, more uniform, and more active. Places such as steelmaking and calcium carbide production have very high requirements for the quality of quicklime, and quicklime burned after grinding can meet the requirements well. If you burn large pieces of limestone directly, it is likely that there are places that are not burned through and there is undecomposed calcium carbonate, and the quality of such quicklime is not good.
- Third, the size of the limestone particles after grinding is similar, and the movement and distribution in the kiln are more regular, so the temperature and airflow in the kiln can be controlled more accurately. The burning temperature and time can be adjusted according to the condition of the limestone particles, making the production process more stable, the production efficiency higher, and the product quality more stable. If large pieces of limestone are burned directly, they will be of different sizes and strange shapes, which will make the distribution of materials in the kiln messy and it will be difficult to control the production process.
Now since we understand the benefits now, then here comes the next question:
Why choose VRM in cement plant for raw milling but not other grinding equipment like ball mill?
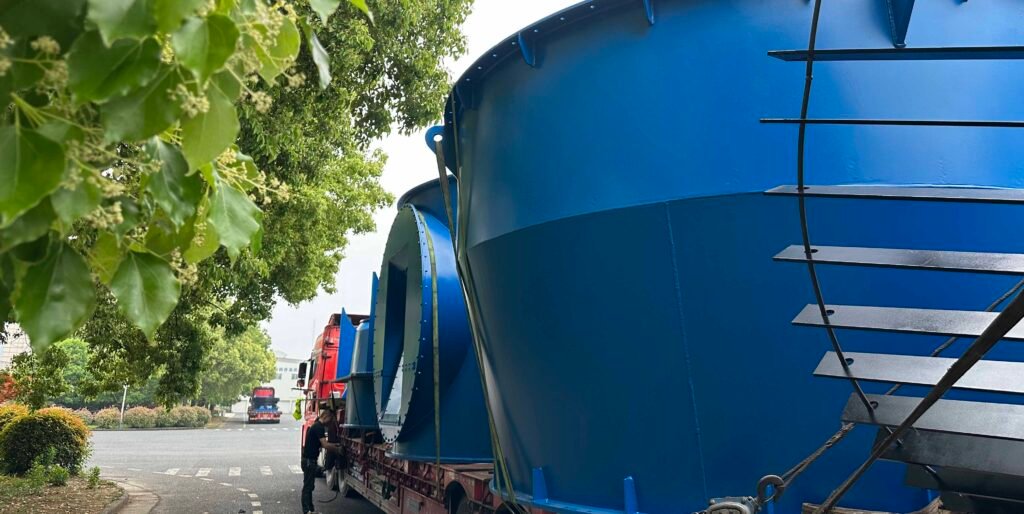
Listen up, we are not making advertisement for vertical roller mill, becasue we also manufacturer ball mill as well 🙂 so here we listed the reason why you should choose vertical roller mill if this was you:
- You are a smart owner.
- You want to save space.
- You want to save the cost of building the workshop to cover the ball mill.
- You want to save money on electricity.
- You want a cleaner workshop.
- You want a quiet workshop.
- You want to keep the VRM outside.
- And so on so further.
Below are the technical aspect reasons our engineer listed why VRM is superior for raw milling:
- First, in terms of energy saving, vertical raw mill has high grinding efficiency and consumes less electricity. As for ball mill, it is like using many small hammers to hit things continuously. Most of the energy is wasted on the movement of the hammers. The energy actually used to grind the materials is not much, so it is more power-consuming, and the noise will be relatively loud. In addition, there is a problem of over-grinding of materials in ball mill.
- Secondly, from the perspective of environmental protection, VRM raw mill is relatively "quiet" when working, produces less dust, and its equipped dust collection equipment can collect dust well, which will not pollute the environment. Ball mill is like a "small bomb". It is easy to generate a lot of dust during feeding, discharging and grinding. Dust collection is difficult and costly.
- Then, when it comes to production efficiency, raw milling VRM is a "all-rounder". It integrates grinding, drying, and powder selection. The process is simple, the equipment does not take up space, and it can achieve large-scale production with high output. Ball mill is not so powerful. It needs to work with other equipment. The process is complicated, the equipment takes up a lot of space, and the production efficiency is relatively low.
- Finally, in terms of product quality, the raw material particles produced by the vertical mill are more uniform in size, which will have a better effect during the subsequent calcination and improve the quality and output of the clinker. The raw material particles produced by the ball mill are of different sizes and irregular shapes, which will affect the calcination effect and thus the quality of the clinker.
Top 5 famous Vertical Roller Mill Manufacturers Worldwide 2025
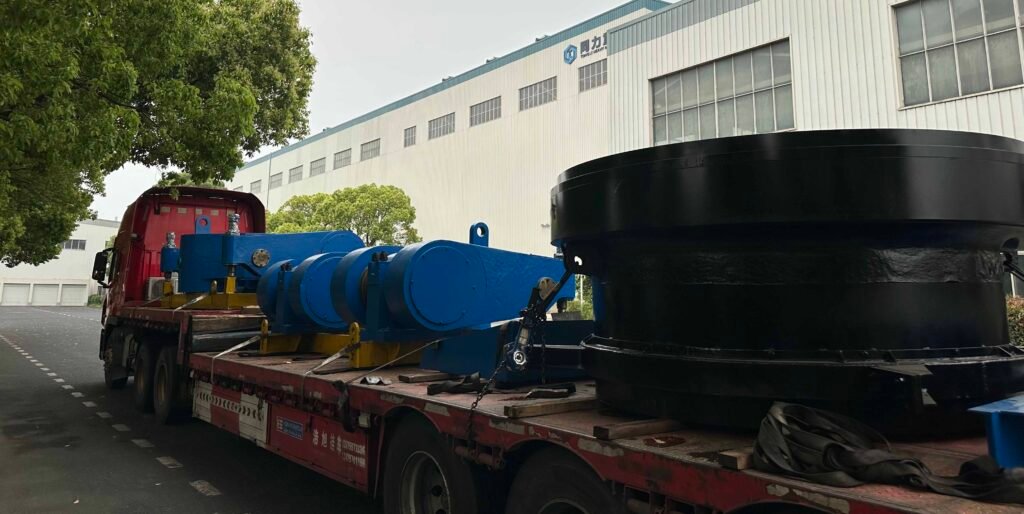
There are many vertical roller mill manfuacturers in china you can find but in terms of brand awareness and history, Loesche, Pfeiffer, Polysius, UBE are the Top 5 manufacturer worldwide.
Loesche mill
Founded in 1906 in the German industrial city of Düsseldorf. The company obtained the European sales rights for Kent and Maxecon mills in the early days. In 1927, the prototype of Loesche mill was born and patented. After continuous improvement, a new generation of Loesche mill was produced in 1934. In 1971, the first 4-roller mill was put into use, and the mill capacity has been continuously improved since then. In the 1990s, many world records were set, such as the raw material mill with a grinding capacity of 750t/h.
Loesche raw mill
Loesche raw material mills are mainly used in the raw material pretreatment stage of cement production lines to efficiently grind various raw materials such as limestone, clay, iron powder, etc. Typical models such as LM 56.4, LM 69.6 and LM 60.4 have large production capacity, high drying capacity and excellent classification efficiency, suitable for various large-scale new dry process cement production lines. "LM" in the model stands for Loesche Mill, and "56.4" means the grinding disc diameter is 5.6 meters and 4 grinding rollers.
Loesche cement mill
Designed for the final grinding of cement clinker, gypsum and mixed materials, Loesche cement mills are widely used in modern cement grinding plants for their high-precision product fineness control and energy-saving characteristics. Common models include LM 46.2+2C and LM 56.3+3C, where "+2C" or "+3C" represents the combination of additional rollers, which further enhances the grinding capacity and system stability, and is very suitable for the preparation of high-performance cement.
Loesche vertical mill
"Loesche vertical mill" can also be used as a general term, covering its coal mill, slag mill and other sub-models, suitable for fuel preparation and industrial waste slag recycling scenarios. For example, LM 35.3D (coal dust vertical mill, D stands for coal dust), or LM 46.2+2CS (slag vertical mill, S stands for Slag), both reflect the specialization and versatility of Loesche vertical mills in different material processing. Through flexible configuration, it widely serves multiple industries such as cement, electricity, and metallurgy.
UBE vertical roller mill
The predecessor of Ube Industries, Ltd. was Ube Shinkawa Iron Works, which was established in 1914. In 1942, it became the machinery division of Ube Industries, Ltd. In April 2000, it separated from Ube Industries, Ltd. and became Ube Industries, Ltd.
Ube vertical mill is one of the important products of Ube Industries, Ltd. and has performed well in the global market. It is widely used in cement, power, metallurgy, chemical industry and other industries, and can be used to grind cement raw materials, coal powder, cement clinker, blast furnace slag and other materials.
In the sales performance statistics of major suppliers of cement industry grinding equipment in foreign countries from 2008 to 2010, Ube's roller vertical mill market share reached 81%. With its advanced technology and stable performance, Ube vertical mill has won the recognition and praise of many users around the world, and has delivered more than 500 sets to domestic and foreign users.
What is the difference between loesche mill and UBE mill?
- The main difference between UBE and Loesche vertical mills is the number and arrangement of rollers - Loesche mills use a modular design with 2, 3, 4 or even 6 rollers, usually with flat grinding plates, while UBE mills typically have larger grinding plates and fewer but larger diameter rollers (usually 2 or 3).
- The UBE emphasizes low pressure and high capacity grinding systems, which can make operation more stable for abrasive materials, while the Loesche uses higher grinding pressures and a more compact mechanical layout.
- The Loesche also integrates a dynamic classifier just above the grinding zone, while the UBE classifier system is sometimes more modular or external. These construction choices affect ease of maintenance, vibration control, and material flow behavior during operation.
Pfeiffer vertical roller mill
GB Pfeiffer, or Gebr. Pfeiffer, is a machinery manufacturing company with a long history. Founded in Kaiserslautern, Germany in 1864, Gebr. Pfeiffer is a family business that has been a pioneer in modern grinding, drying, separation, digestion and calcination technology for more than 150 years. The company currently has about 500 employees. Adhering to the philosophy of its founder Jacob Pfeiffer, the company focuses on long-term development and maintains a leading position in the industry.
What vrm does pfeiffer offer?
- MPS vertical mill: It is the company's classic product, suitable for grinding a variety of materials, such as coal, petroleum coke, clay, limestone, gypsum, etc. It integrates grinding, drying, grading and other functions, and has the advantages of low investment cost, low power consumption, high heat utilization, high equipment availability and good control performance.
- MVR vertical mill: It is a vertical mill developed to meet large production needs and is equipped with a patented multi-drive system (Multidrive®). It has the advantages of large output, which can reach more than 1,400 tons/hour; high equipment availability, with dual active redundant design for grinding rollers and drive modules; high reliability, easy maintenance, low wear rate due to the use of high-quality wear-resistant materials; low power consumption, which can be reduced by 40% compared with traditional ball mills; and full use of process heat. Whether it is cement raw materials, cement clinker or blast furnace slag, MVR vertical mill can ensure high output, stable and long-term operation.
What is the differene between Gebr.Pfeiffer and Loesche Vertical mill?
In terms of transmission:
Pfeiffer's MVR series is equipped with multiple independent drive units (MultiDrive), it have higher redundancy and reliability in ultra-large capacity applications, Loesche prefers to expand capacity by increasing the number of rollers and grinding disc diameter.
In terms of grinding roller liner design:
Pfeiffer vertical mills usually have 3 tilted drum-shaped grinding rollers, with bowl-shaped grinding discs with arc grooves, while Loesche vertical mills mostly use four-roller hydraulic type, which is a combination of flat grinding discs and conical grinding rollers.
In terms of rocker arm design:
Pfeiffer usually adopts a single reducer drive with a multi-roller (up to 6 rollers) design with an external hydraulic device. It also has a combination of fixed grinding rollers and swinging grinding rollers(rocker arm). The grinding rollers can automatically swing out of the grinding disc for maintenance. The Loesche vertical mill is characterized by its modular structure, flat grinding disc, and inclined grinding rollers. The grinding rollers are pressed down at a certain angle above the grinding disc. It adopts a central drive layout and has a more compact structure.
In terms of powder fineness control:
Pfeiffer mill controls the fineness by strengthening the wind speed of the powder selection device and adjusting the speed, and the Loesche mill relies on the DC motor to drive the separator for adjustment;
In terms of on-site maintenance:
Pfeiffer mill roller liner assembly combination is easy to replace, the Loesche mill roller sleeve and other connecting structures are easy to disassemble and assemble, and there is an oil pressure device to assist maintenance, and the Loesche mill hydraulic system control function is more flexible.
Polysius vertical roller mill
In 1935, the first vertical mill for cement industry appeared in West Germany. After accumulating experience in cement production equipment, Polysius entered the field of vertical mills and launched products through research and development, such as the RM series vertical mill. At the end of the 20th century, its RM69/29 vertical mill was used in Indonesian cement plants. In the 21st century, Polysius became a member of ThyssenKrupp and launched the quadro pol® series vertical mills.
The history of Polysius:
Polysius is a well-known German company with a long history. It was founded in Dessau in 1859 by machinist Andreas Ernst Gottfried Polysius. It started as a metal processing workshop and later developed into an iron foundry and engineering company. In 1893, its products were unveiled at the Chicago World's Fair. In 1898, it designed and manufactured the first rotary kiln in Europe. In 1907, it built a complete cement plant in Egypt. In the late 1920s, Dr. Otto Georg Lelep invented the Lepol process, which revolutionized cement production. After World War II, the factory in Dessau was confiscated by the Soviet Union. Family member Dr. Kurt Prussing founded Westpol GmbH in Beckum, which was later renamed Polysius GmbH, ushering in a revival of business. In 1971, Friedrich Krupp acquired a majority stake in it. In 1999, Polysius merged with Krupp and Thyssen Group and became a member of ThyssenKrupp. Today, Polysius is an internationally renowned manufacturer of cement technology and equipment.
What is the difference between Polysius and Loesche mill?
- Roller arrangement: Polysius's vertical mill adopts a symmetrical horizontal roller structure, usually a four-roller or six-roller design, with a balanced structure and uniform load distribution. Loesche uses inclined rollers, which are pressed obliquely on the grinding disc to form a unique grinding track, which helps the material move outward and improves the grinding efficiency.
- Drive system design: Polysius can adopt a central drive or side drive design according to the system layout, with flexible drive mode, which is easy to adapt to different process lines. Loesche generally adopts a central drive system, and the drive device is compactly installed at the bottom of the mill, with a more compact overall structure and smaller footprint.
- Powder selection system: Polysius mostly uses an external high-efficiency powder selector, which has an independent structure, is easy to maintain and upgrade, has high powder selection accuracy, and is more flexible in controlling the graded particle size. Loesche usually integrates the dynamic powder selector above the mill. The integrated design makes the entire system more compact, especially suitable for projects with limited space.
- Repair and Maintenance: Polysius' roller sleeve and grinding disc liner support interchangeable design, which is easy to replace and repair, especially suitable for customers with high requirements for downtime. Loesche uses a modular roller pressing system. Although it also supports maintenance, the structure is more compact and some maintenance requires professional equipment operation.
- Air duct system: Polysius's air duct is relatively complex, and hot air, powder selection, and material transportation are mostly connected by external pipelines, which is conducive to independent control of each link. Loesche's air duct design is highly integrated, and the mill body completes material drying, classification, and exhaust, which is conducive to saving space and heat energy utilization.
So we have discussed all 4 of them, vertical mill brand and we have made a table below that is to show you what is difference to help you make the decision:
VRM Comparison Table: Loesche vs. Pfeiffer vs. UBE vs. Polysius Vertical Mills
Feature | Loesche | Gebr. Pfeiffer (MVR) | UBE | Polysius |
Roller Arrangement | Inclined rollers, modular design | Vertical rollers, some fixed & some swing-out | Fewer large-diameter vertical rollers (2–3) | Symmetrical layout, usually 4 or 6 rollers |
Grinding Table | Flat horizontal table, centrifugal feed | Large-diameter table, center feed | Large, low-speed table | Large stable grinding table |
Classifier Type | Integrated dynamic classifier (on top) | High-efficiency dynamic, integrated or external | External classifier, flexible layout | High-efficiency external classifier |
Drive System | Central drive, compact setup | MultiDrive (multiple motors, high redundancy) | Side or twin motor drive, easy maintenance | Central or side drive, flexible options |
Maintenance | Modular rollers, requires tools/support | Swing-out rollers, spacious and easy access | Simple, large parts, easier visual inspection | Interchangeable liners, maintenance-friendly |
System Integration | Highly integrated (grinding, drying, classifying) | Moderately integrated, easily upgradable | Less integrated, more modular and customizable | Balanced integration, flexible layout |
Key Characteristics | Compact structure, proven tech, flexible | High redundancy, easy maintenance, large capacity | Stable operation, intuitive structure | Reliable, serviceable, adaptable |
Typical Applications | Raw meal, cement, slag, coal | Raw meal, cement, slag (ideal for large lines) | Raw meal, coal (power, cement industries) | Full cement line (especially raw/clinker) |
Oh sorry we forgot about FL-smidth.
History of FL-smidth VRM:
FL Smith of Denmark was founded in 1882. In the early days, it mainly provided machinery for the brick and tile industry. After entering the field of vertical mills, it launched products such as ATOX vertical mills, which integrate drying, grinding, powder selection and lifting functions. The column roller and flat plate design make the wear-resistant lining wear evenly. Its grinding roller system is light in weight, small inertia, and stable in operation. The block wear-resistant lining material is wear-resistant and easy to disassemble and assemble. The double-acting hydraulic pull rod can apply grinding pressure and lift the grinding roller before starting. The improved powder selection machine is conducive to increasing production and reducing consumption. In 2005, Kunming Dongjun Cement Plant in Yunnan introduced two OK 33-4 vertical mills from Smith Company for the production of cement and fine grinding of slag, opening the precedent of cement vertical mills in my country. Its vertical mills are constantly developing, and the largest OK mill has developed into OK 62-6, with a cement production capacity of 750t/h and slag of 550 t/h. It has a grinding disc diameter of 8.2m, 6 grinding rollers, and a transmission power of 12000-16000kW. It is widely used in global cement production.
What types of vertical mills does FL Smith offer?
- ATOX® Coal Mill: With large rollers, it has a strong grinding capacity for almost all types of raw coal. The rollers work well with the high-efficiency separator and feed gate to continuously and stably grind the coal to the required fineness and moisture content. It is suitable for feeds with different moisture contents and can easily handle abrasive and sticky raw coals.
- OK™ Raw Meal and Cement Mill: For grinding raw meal, cement and slag. Advanced design and high efficiency. The OK™ mill adopts a patented roller and grinding disc design, uses a concrete grinding frame instead of traditional heavy steel structure, and its flexible design allows 60% to 70% of normal operating output to be achieved when some rollers stop working, minimizing production losses.
What's special about FL Smith vertical raw mill?
- Roller and disc design: ATOX® vertical mill uses cylindrical rollers and flat track discs. The cylindrical roller and flat disc design allows the grinding pressure and reaction force to be used only in the vertical direction, and the wear lining wears evenly. Some other vertical mills, such as the MPS vertical mill of Pfeiffer in West Germany, use drum-shaped rollers and bowl-shaped discs with arc grooves. In contrast, the roller system of FL Smith vertical mill is light in weight, small in inertia, and runs smoothly. The block wear lining can be made of more wear-resistant materials, which is easy to disassemble and assemble, and can be turned around or thickened as needed. OK™ mill uses a patented roller and disc design, using a concrete grinding frame instead of the traditional heavy steel structure. Its flexible design can still achieve 60% to 70% of the normal operating output when some rollers stop working, minimizing production losses.
- Powder selector: FL Smith vertical mill is equipped with an improved powder selector, making it easier to increase production and reduce consumption in the entire grinding system. The classifiers of other companies' vertical mills may differ in terms of classification efficiency and adjustment flexibility, which may affect the performance of the entire grinding system.
- Pressure device: The double-acting hydraulic tie rod of the ATOX® vertical mill can not only apply grinding pressure, but also lift the grinding roller before starting, without auxiliary transmission.
- Online monitoring and maintenance: FL Smith provides online condition monitoring services, which allows users to adopt proactive maintenance strategies for OK™ and ATOX® mills and eliminate unexpected downtime. Not all other brands of vertical mills have such a complete online monitoring service.
What are the components of a vertical roller mill(brief explaination)
A lot of articles you can find on the website that talks about the structure and component of a cement vertical roller mill(VRM). I think most of them are already very detailed, therefore in here I am putting some pictures instead of paragraphs to give you a more vivid idea what does those components look like. But notice the pictures might not match up with the components.
The role of rocker arm

The rocker arm of a vertical mill is mainly composed of an arm body, a connecting shaft, a hydraulic cylinder and other parts. One end of the arm body is connected to the grinding roller, and the other end is connected to the machine body through a connecting shaft. The hydraulic cylinder is used to drive the rocker arm to swing. Its function is to drive the rocker arm to lift and rotate the grinding roller when the equipment is repaired or the grinding roller is replaced, which is convenient for personnel to operate; during operation, the grinding roller position is fixed so that the grinding roller can stably apply pressure to the material on the grinding disc
What is VRM roller used in cement grinding?

- Structure: The VRM roller of a vertical mill usually consists of a roller core, a roller sleeve, a bearing, a sealing device, and other parts. The roller core is the supporting skeleton of the roller, made of high-strength cast steel or forged steel, withstand the huge pressure during the grinding process. The roller sleeve contacts the material, made of alloy materials high-chromium cast iron. The bearing is used to support the roller core so that the roller can rotate flexibly, while bearing the weight and grinding force of the roller. The sealing device prevents materials and dust from entering the bearing, ensuring the normal working environment of the bearing and extending its service life.
- Working principle: The roller is pressed on the grinding disc with a certain pressure under the action of the hydraulic system. The motor drives the grinding disc to rotate through the reducer, and the material falls from the center of the grinding disc and moves to the edge of the grinding disc under the action of centrifugal force. In this process, the material is crushed and sheared by the roller and gradually crushed and ground into fine powder. The number and arrangement of grinding rollers vary depending on the model and specifications of the vertical mill. Common ones are 2, 3 or 4 grinding rollers, which are evenly distributed around the grinding disc and work together to grind the material.
- Function: To crush the block or granular material into the required fineness by applying pressure and shear force to the material. In addition, it affect the production capacity, grinding efficiency, product quality and energy consumption of the vertical mill.
The Role of Grinding table:

- The grinding disc/table of the vertical mill is composed of a disc body, a liner, a retaining ring and other parts. The material is mostly cast steel, such as 35CrMo or 42CrMo. The disc body is the main structure of the grinding disc, in the shape of a thick disc, made of high-strength cast iron or cast steel to withstand the pressure of the grinding roller and the impact of the material.
- The liner is installed on the surface of the disc body, generally made of wear-resistant materials, such as high-chromium cast iron, cemented carbide, etc., which can protect the disc body from wear and is easy to replace.
- The retaining ring is located at the edge of the grinding disc, and its height is adjustable. Its function is to block the material so that the material forms a certain thickness of material layer on the grinding disc to ensure that the material is fully ground between the grinding disc and the grinding roller.
- There are multiple evenly distributed ventilation holes on the grinding disc for the introduction of hot air to dry the material during the grinding process. At the same time, the hot air can carry the ground material into the powder selection system.
The Role of powder separator:

The core components of the powder classifier mainly include the classifying rotor and guide vanes. The classifying rotor is made of multiple blades, which rotate at high speed under the drive of the motor to generate a strong centrifugal field. The guide vanes are installed around the classifying rotor to guide the flow of air and materials so that the materials can be classified under the combined action of centrifugal force and airflow. Coarse particles are thrown outward under the action of centrifugal force, fall along the inner wall of the powder classifier and return to the vertical mill; fine particles enter the upper collection device through the gap between the blades of the classifying rotor under the action of airflow.
The Role of motor and reducer(Gearbox):

Planetary reducers are widely used in vertical mills. One vertical mill must be equipped with one. It is mainly composed of sun gear, planet gear, inner gear ring, planet carrier and other components. The sun gear is located in the center, surrounded by multiple planet gears that mesh with the sun gear and inner gear ring, and the planet gears are installed on the planet carrier. This structure allows multiple planet gears to share the load together, with higher load-bearing capacity and transmission efficiency.
The Role of lubrication oil station:

The main function of the vertical mill oil station is lubrication and cooling. It uses the oil pump to transport the lubricating oil in the oil tank to the key components of the vertical mill, such as the roller bearing, the grinding disc bearing and the reducer, etc., to reduce the friction between the components and reduce the wear. At the same time, it takes away the heat generated by friction, prevents the oil temperature from being too high, and ensures that the equipment runs at a suitable temperature.
The role of mill shell:

The shell of the vertical mill is the external structure of the entire equipment, which plays the role of protecting internal components, sealing the working environment and supporting the equipment. It is made of welded steel plates, can withstand internal pressure and material impact. The wear-resistant lining is made of high-toughness materials. The shape and size of the lining are designed according to the wear conditions of different parts of the shell. Either block-shaped or sheet-shaped and fixed inside the shell by bolts or welding. In areas prone to wear, such as the feed inlet, material impact area, etc., the thickness of the lining will be increased or more wear-resistant materials will be used to enhance the wear resistance of the shell. The surface of the lining is usually designed with certain patterns or protrusions to increase the friction between the material and the lining.
So we have introduced all the necessary parts now let us move on to the operational guide for a cement vertical roller mill.
4 Keys During Vertical Roller Mill Operation in Cement Plant
1. Material Layer thickness:
The appropriate material layer thickness can form a stable material bed between the grinding roller and the grinding disc. A stable material bed can ensure that the grinding roller applies uniform pressure to the material, so that the grinding force on the material on the grinding disc is relatively consistent, thereby achieving a stable grinding process. If the material layer is too thin, the grinding roller will directly contact the grinding disc, which will produce a large impact vibration and affect the stability and service life of the equipment; if the material layer is too thick, the grinding efficiency will be reduced because the pressure of the grinding roller cannot be effectively transmitted to the material, and the material cannot be fully squeezed and ground. And we as a VRM manufacturer our recommandations are as follows:
Manufacturer's Recommandation to maintain a stable material layer:
- Controlling the feeding amount: To maintain the stability of the feeding amount, it is necessary to set the appropriate feeding amount according to the production capacity and material characteristics of the vertical mill, and accurately control the feeding speed of the material through means such as frequency conversion speed regulation of the feeding equipment. Avoid large fluctuations in the feeding amount to avoid causing a sharp change in the thickness of the material layer.
- Adjusting the grinding pressure: The grinding pressure and the thickness of the material layer affect each other. When the material layer is too thick, the grinding pressure can be appropriately increased to enable the grinding roller to better squeeze the material and reduce the thickness of the material layer; conversely, when the material layer is too thin, the grinding pressure should be reduced to prevent the grinding roller from directly contacting the grinding disc and causing violent vibration.
- Optimizing the ventilation volume: Reasonable ventilation volume helps the uniform distribution of materials in the mill and timely discharge. If the ventilation volume is too large, the residence time of the material in the mill will be shortened, resulting in a thinner material layer; if the ventilation volume is too small, the material will accumulate in the mill and the material layer will thicken. The ventilation volume should be optimized according to the specifications, material characteristics and production requirements of the vertical mill. For materials with good grindability, the ventilation volume can be appropriately larger; for materials with difficult grindability, the ventilation volume needs to be appropriately reduced.
- Monitor the thickness of the material layer: Install material layer thickness monitoring devices, radar level meters, laser level meters, etc. to monitor the thickness of the material layer in real time. Operators adjust the operating parameters in time according to the monitoring data to ensure that the thickness of the material layer is within a reasonable range. At the same time, combined with the vibration value, current, pressure difference and other operating parameters of the vertical mill, comprehensively judge the change trend of the material layer.
- Stabilize the particle size and moisture of the material: The particle size and moisture of the material have an important influence on the stability of the material layer. Materials with uniform particle size and appropriate moisture are conducive to the formation of a stable material layer. Therefore, it is necessary to control the particle size and moisture of the material entering the mill to avoid large fluctuations in particle size or too high or too low moisture. For materials with larger particle size, pre-crushing can be carried out before entering the mill; for materials with higher moisture, drying can be used.
- Regular maintenance of equipment: Ensuring the normal operation of the vertical mill equipment is the basis for maintaining a stable material layer. Regularly check the wear of the grinding roller and grinding disc, replace the severely worn parts in time, ensure that the gap between the grinding roller and the grinding disc is uniform, and enable the grinding pressure to be evenly applied to the material layer.
2. The Grinding Pressure of the Grinding Mill
Roller pressure is a key factor in the operation of vertical raw mill. It directly determines the grinding efficiency. Appropriately increasing the pressure can enhance the extrusion and grinding of materials, promote the crushing of particles into fine powder, and increase the output. In actual operation, the grinding pressure should be adjusted according to the feed amount, material particle size and grindability. However, when the grinding pressure reaches a certain critical point, the grinding capacity will stop growing, and it will only increase the driving force and accelerate the wear of parts, but will not improve the grinding capacity. The specific manifestation is that the displayed pressure of the hydraulic cylinder is too high. on the other hand Too low grinding pressure will lead to increased material layer thickness, increased main motor current, increased pressure difference in the mill, and increased mill vibration amplitude. In order to keep the pressure steady we as a VRM manufacturer our recommandations are as follows:
- Particle size: When the material particle size is large, a larger roller pressure is required to effectively crush and grind. For example, when the proportion of large pieces of material in the mill increases, the roller pressure should be appropriately increased.
- Hardness: For materials with higher hardness, such as raw materials with a high quartz content, the roller pressure needs to be increased to overcome the resistance of the material. For materials with lower hardness, the roller pressure can be appropriately reduced to avoid excessive grinding and equipment wear.
- Humidity: When the material humidity is high, it will affect its fluidity and grindability, and easily lead to unstable material layer. At this time, the roller pressure can be appropriately increased to enhance the extrusion of the material, so that the material can better pass through the gap between the roller and the grinding disc, and it also helps to discharge moisture.
- Vibration value: Vertical mill vibration is an important indicator reflecting the operating status of the equipment. When the vibration value increases, it may be due to excessive roller pressure, resulting in increased impact between the roller and the grinding disc, or caused by unstable material layer. At this time, the roller pressure should be appropriately reduced to observe whether the vibration value decreases to find a suitable pressure balance point.
- Current: The main motor current reflects the load of the vertical mill. If the current is too high, it means that the equipment is overloaded, and it may be that the roller pressure is too high or the feed amount is too much. In this case, the material layer thickness and material characteristics should be determined first, and then the roller pressure or feed amount should be adjusted appropriately to restore the current to the normal range.
- Pressure difference: The pressure difference in the mill reflects the circulation and ventilation conditions of the material in the mill. When the pressure difference increases, it may be that the material layer is too thick or the ventilation is not smooth. If the pressure difference increases due to the material layer, the material layer thickness can be changed by adjusting the roller pressure, so that the pressure difference returns to normal.
3. The water spray system
During the grinding process of the vertical mill, the material will generate a lot of heat due to grinding, causing the temperature to rise. Excessive material temperature will make the material's grindability worse and may also cause thermal deformation of equipment components. The sprinkler sprays water on the material on the tray, using the evaporation of water to absorb heat to reduce the material temperature, so that the cracks on the surface of the material particles are moisturized and expanded, reducing the strength of the material, thereby improving its grindability. For some materials with high hardness or brittleness, sprinkling water can make them easier to crush and grind during the grinding process. At the same time, sprinkling water can increase the humidity of the material, enhance the viscosity between the materials, help form a stable material layer, and effectively suppress the flying of dust and reduce dust emissions.
4. The Air Volume in the Mill
Insufficient air volume in the vertical mill will make it difficult to lift and transport the material, causing it to accumulate on the grinding disc, reducing grinding efficiency and output; excessive air volume will shorten the material's residence time in the mill, resulting in incomplete grinding and affecting product fineness. Appropriate air volume can achieve efficient material transportation and precise grading, stabilize the material layer, assist in regulating the temperature in the mill, prevent material sticking or equipment damage due to high temperature, and evenly distribute the material, reduce equipment wear, and ensure the stability of the vertical mill.
How to adjust the cement mill air volume properly?
- Based on material characteristics: the particle size, humidity, grindability and other characteristics of the material will affect the demand for air volume. For materials with larger particle size, higher humidity or poor grindability, a larger air volume is required to ensure the material conveying and grinding effect.
- Reference equipment operating parameters: Pay close attention to the operating parameters of the vertical mill such as current, vibration, differential pressure. When the vertical mill current increases, the vibration increases or the differential pressure is unstable, the air volume may need to be adjusted to optimize the operating state. For example, if the differential pressure in the mill is too high, it means that the air volume may be insufficient, and the air volume needs to be appropriately increased to reduce the differential pressure.
- Combined with product quality requirements: Adjust the air volume according to the product's fineness, specific surface area and other quality indicators. If the product fineness requirement is high, it is necessary to adjust the air volume to make the classifier's classification effect better, and appropriately increase the air volume to improve the collection efficiency of fine powder.
- Gradual adjustment: When adjusting the air volume, the principle of gradual adjustment should be followed. The amplitude of each adjustment should not be too large. Generally, a 5% - 10% change in air volume is appropriate. After adjustment, observe the changes in equipment operating parameters and product quality, and make further fine-tuning based on the feedback results to avoid unstable operating conditions inside the mill due to sudden and drastic changes in air volume.
Frequently asked question FAQ
The vertical cement mill from the top to the bottom is consisted of inlet chute, outlet duct, cage rotor, powder separator, reject cone, grinding roller, grinding table, sealing device, friction ring, hydraulic roller pressure system, air ring regulating device, grinding disc liner, bearing gas forcible sealing, feeding oil groove, internal air pipe sealing, motor, planetary reducer.
High efficiency and energy saving: The vertical mill uses the material layer grinding principle, and the material is crushed between the grinding roller and the grinding disc. Compared with the ball mill steel ball impact grinding, the power consumption is reduced by 20% - 30%.
High output and high efficiency: The vertical mill integrates crushing, grinding, grading and conveying functions to optimize the production process. Taking a large cement production line as an example, the output can reach hundreds of tons per hour, and the amount of material processed per unit time is large.
High quality finished product: The internal powder selection device of the vertical mill can accurately control the fineness of the finished product, and the particle grading is uniform. The finished cement product produced has a proper ratio of coarse and fine particles, which can improve the strength and stability of cement.
Effective drying: The vertical mill uses hot air to convey materials, and can be dried synchronously during the grinding process. By flexibly controlling the inlet air temperature, the material with a moisture content of up to 15% - 20% can be dried and ground to a qualified moisture content, eliminating the need for additional drying processes and equipment.
Convenient operation: The vertical mill is equipped with an automatic control system, and the operator can remotely control equipment parameters such as roller pressure and mill speed in the central control room. When encountering component wear problems, the roller sleeve and liner can be quickly replaced with the help of the maintenance cylinder to flip the boom, reducing downtime.
Strong adaptability: The vertical mill can handle a variety of materials, whether it is limestone and clay in cement production, or coal in the power industry, it can be effectively ground. For the moisture, hardness and other characteristics of the material, it has a high adaptability range and does not need to adjust the equipment frequently.
Environmental protection: The vertical mill is fully enclosed and the system is in a negative pressure state, which effectively prevents dust from overflowing. During operation, there is no direct metal collision between the grinding roller and the grinding disc, and the noise is 20-25dB lower than that of the ball mill, which meets environmental protection requirements and reduces pollution and interference to the surrounding environment.
Durable and economical: When the vertical mill is running, there is material isolation between the grinding roller and the grinding disc, which reduces direct friction between metal parts and reduces wear. The metal consumption per unit product is as low as 5-10g/t, and the service life of key components such as roller sleeves and liner plates is long, reducing equipment maintenance and replacement costs.
Roller mills can achieve drying, grinding and grading of materials. When working, roller mills rely on the centrifugal force generated by cylindrical grinding rollers to crush various materials into uniform particles and complete subsequent grinding, drying and grading operations. In actual production, common industrial raw materials such as clinker, cement, coal, gypsum, limestone, clay, and special materials such as barite, perlite, and ore can be processed by roller mills. With the precise and controllable particle size adjustment function, roller mills can produce materials with uniform particle size. This feature is particularly critical in industries such as cement production and mineral processing that have extremely high requirements for material quality.
First of all ratmond mill is different from a vertical mill.
Tongli centrifugal roller mill consists of a feeder, roller mill base, centrifugal main mill fan, high-efficiency turbine (or rotary) separator, cyclone collector, bag dust collector, air heater, recovery pipeline, and discharge port.
The feeder feeds the raw material into the roller mill base at a rate determined by the change in mill pressure. The plow located in front of each roller mill guides the raw material upward between the grinding roller and the heavy alloy steel bucket ring, where the raw material is ground to the specified size. The grinding roller can swing freely centrifugally, forcing it to apply pressure to the raw material and grind it. Because the roller can rotate freely, it can automatically adjust to the appropriate grinding position without adjusting wear compensation.
After grinding to the required size, the material will be accurately graded in the separator, so that the product size material can be conveyed out of the mill, while the oversized material is returned for further grinding.
Bag dust collector: The air fine powder entrained in the exhaust gas discharged by the cyclone collector is removed by the high-efficiency bag dust collector located downstream of the cyclone. If the material has high moisture content, a hot air furnace can be added.
To prevent explosion, Tongli is equipped with an online carbon monoxide gas analyzer and an emergency nitrogen device.
Debris can be removed from the discharge port below the roller mill.
A cement raw milling station is a complete system compare to a single vertical roller mill. It consists of a feeding system, a powder selection system, a conveying system, a dust collection system, a drying system, a control system, a storage system, etc.
1. Low price: MPS mills are compact, require little floor space, and are dust-free and quiet during operation.
2. Low power consumption: The grinding principle and the efficient classifier ensure up to 40% lower power consumption compared to conventional ball mills.
3. Optimal use of process heat: Even at low temperatures, MPS mills make full use of the heat energy of rotary kiln exhaust gas and other process gases.
4. High availability: The grinding rollers can be welded online, which reduces maintenance time for MPS mills.
5. DCS control system: The short residence time of the material and the remote control of the grinding pressure and the classifier rotor speed ensure that the MPS mill can be adjusted at any time even if the raw material properties change.
The middle and upper shells of the vertical mill are inlaid with high-chrome inserts and wear-resistant materials, and the frame and other mill parts are made of highly wear-resistant steel plates or surface-hardened composite plates to prevent jet wear. For parts that are particularly prone to wear, such as the exhaust pipe, additional ceramic liners are provided. All for easy replacement at a later time.
For parts that come into direct contact with the material, such as the grinding rollers and grinding plates, we have designed a hydraulic jacking and tumbling device that can be quickly replaced through a maintenance door. The grinding rollers and grinding table segments are driven to the maintenance door by the maintenance drive and swing out of the grinding area. Therefore, maintenance downtime is reduced and work becomes easy and safe.
Conclusion:
In this article, we introduce what is cement vertical mill, why cement needs vertical mill, the principle of cement vertical mill, well-known vertical mill brands and what parts vertical mill consists of. Because there are already many articles introducing the technical aspects of vertical mill, this article will not introduce it in depth. Summary In cement production, raw materials need to be ground finely for better calcination, and the finished cement clinker also needs to be ground into fine powder to become the cement we commonly use. The vertical roller mill converts large pieces of material into fine powder that meets production requirements through the mutual extrusion and grinding of the grinding roller and the grinding disc.